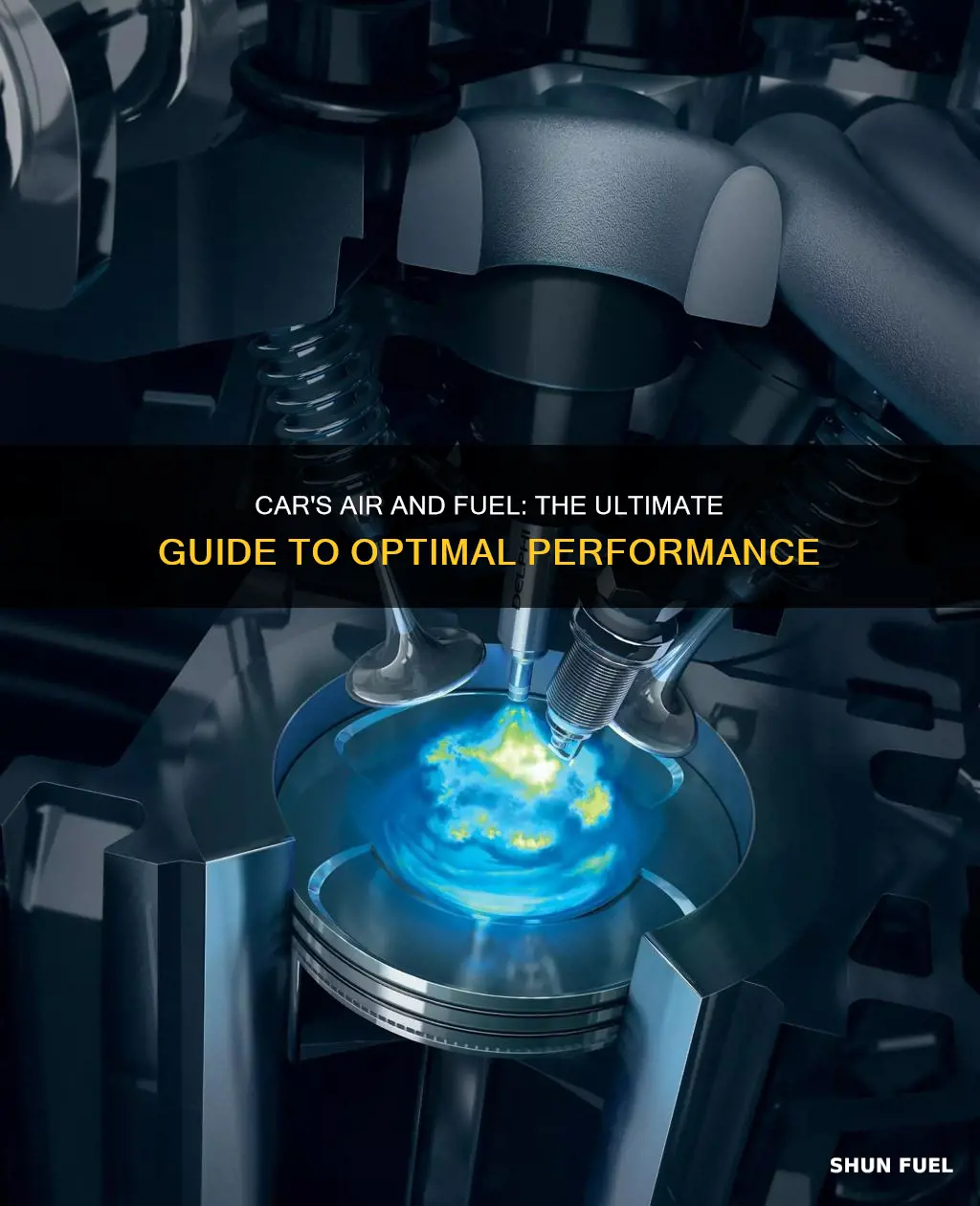
Understanding the air and fuel delivery system in a car is crucial for optimizing performance and fuel efficiency. The engine requires a precise mixture of air and fuel to run efficiently, and any imbalance can lead to poor performance, increased emissions, or even engine damage. This paragraph will explore the various components and processes involved in determining how much air and fuel a car's engine receives, including the role of the air filter, fuel injectors, and the intricate dance between the engine's sensors and computer systems.
What You'll Learn
- Engine Intake: Air filtration and volume control for optimal combustion
- Fuel Injection: Precise fuel delivery for efficient engine performance
- Air-Fuel Ratio: Ideal mixture for combustion, affecting engine power and emissions
- Throttle Body: Regulates air flow, impacting engine response and fuel efficiency
- Evaporation Emission Control: Reduces fuel loss and improves engine operation
Engine Intake: Air filtration and volume control for optimal combustion
The engine intake system plays a critical role in ensuring that the engine receives the right amount of air for optimal combustion. This process begins with the air filter, which is designed to capture and remove contaminants from the incoming air. The air filter is typically located in the engine bay and is often a replaceable element. Its primary function is to prevent dust, dirt, pollen, and other particles from entering the engine, which could otherwise cause damage to internal components. A clean air filter is essential for maintaining engine performance and longevity.
As air passes through the filter, it is directed into the engine's intake manifold or throttle body. The intake manifold is a chamber that distributes the air-fuel mixture to the individual cylinders. It is designed to ensure that the air is evenly distributed, allowing for precise control of the fuel-air ratio. The volume of air entering the engine is carefully managed to achieve optimal combustion. Modern vehicles often employ electronic sensors to monitor the air intake, ensuring that the engine receives the correct amount of air for efficient operation.
Air filtration is a critical aspect of this process. Contaminants in the air can lead to reduced engine performance, increased fuel consumption, and even engine damage. Therefore, the air filter must be regularly inspected and replaced to maintain its efficiency. Over time, the filter can become clogged with dirt and debris, reducing its ability to filter out contaminants. This can result in a restricted airflow, causing the engine to run poorly and potentially leading to performance issues.
In addition to filtration, the engine intake system also controls the volume of air entering the engine. This is achieved through the use of throttle bodies or intake valves, which regulate the airflow based on engine speed and load. When the accelerator is pressed, the throttle opens, allowing more air to enter the engine, which is then mixed with fuel for combustion. The engine's computer system continuously monitors these processes, adjusting the fuel injection and ignition timing to optimize power output and fuel efficiency.
Optimizing the engine intake process is crucial for achieving the best possible performance and fuel economy. It ensures that the engine receives the right amount of air, which, when combined with the appropriate amount of fuel, results in efficient combustion. This, in turn, leads to improved power output, reduced emissions, and better overall engine operation. Understanding and maintaining the engine intake system's components are essential for any vehicle owner to keep their car running smoothly and efficiently.
Air Conditioning's Impact: Fuel Efficiency in Cars
You may want to see also
Fuel Injection: Precise fuel delivery for efficient engine performance
Fuel injection is a critical component of modern engine technology, revolutionizing the way vehicles deliver fuel to their engines. This system ensures precise fuel delivery, optimizing combustion and enhancing overall engine performance. By replacing the traditional carburetor, fuel injection offers a more efficient and controlled method of mixing air and fuel, resulting in improved power, fuel economy, and reduced emissions.
The process begins with the fuel injection system, which consists of an electronic control unit (ECU) and injectors. The ECU receives data from various sensors, including engine speed, temperature, and load, to calculate the exact amount of fuel required for optimal combustion. This microchip-controlled system ensures that the fuel is delivered precisely when and where it is needed. Each injector is responsible for spraying a fine mist of fuel into the engine's intake manifold or directly into the combustion chamber, depending on the engine design.
One of the key advantages of fuel injection is its ability to provide a precise air-fuel mixture. In a conventional engine, the carburetor mixes air and fuel, but this process can be inconsistent, leading to uneven combustion. Fuel injection, however, ensures that the correct ratio of air to fuel is achieved, promoting complete combustion and maximizing power output. This precision also contributes to better fuel efficiency, as the engine can run on a leaner mixture without sacrificing performance.
Modern fuel injection systems are highly advanced, utilizing electronic sensors and actuators to fine-tune the fuel delivery process. These sensors monitor parameters such as engine temperature, pressure, and oxygen levels, allowing the ECU to make real-time adjustments. For instance, if the engine is running too rich (with an excess of fuel), the system can automatically reduce the fuel flow to maintain the optimal air-fuel ratio. This dynamic adjustment ensures that the engine operates efficiently under various conditions, from idling to high-speed cruising.
Furthermore, fuel injection technology has led to the development of direct fuel injection, where fuel is injected directly into the combustion chamber. This approach provides even greater control over the combustion process, as the fuel is injected at a specific point and time, optimizing the air-fuel mixture's quality. Direct fuel injection is commonly found in high-performance engines, where precise fuel delivery is crucial for achieving maximum power and responsiveness while maintaining fuel efficiency.
In summary, fuel injection systems have transformed the way vehicles deliver fuel, offering precise control over the air-fuel mixture. This technology ensures efficient combustion, improved performance, and reduced emissions. With its ability to fine-tune fuel delivery based on real-time data, fuel injection has become an essential component in modern engine design, providing drivers with a more responsive and environmentally friendly driving experience.
The Green Illusion: Are Electric Cars Still Coal-Powered?
You may want to see also
Air-Fuel Ratio: Ideal mixture for combustion, affecting engine power and emissions
The air-fuel ratio is a critical aspect of internal combustion engines, referring to the mass ratio of air to fuel that is supplied to the engine's combustion chamber. This ratio is a fundamental parameter that directly influences engine performance, efficiency, and emissions. Achieving the ideal air-fuel ratio is essential for optimal combustion, ensuring that the fuel burns completely and efficiently, thereby maximizing power output while minimizing harmful pollutants.
In an ideal scenario, the air-fuel ratio should be precisely balanced to provide the perfect mixture for combustion. This ratio is typically expressed as a volume or mass ratio of air to fuel. For gasoline engines, the stoichiometric air-fuel ratio, which is the theoretical ideal ratio, is approximately 14.7:1. This means that for every 14.7 parts of air, one part of fuel is required for complete combustion. This ratio ensures that all the fuel is burned efficiently, producing the maximum amount of power and minimal emissions.
However, in practical terms, engines often operate at leaner or richer mixtures than the stoichiometric ratio. A lean mixture, with a higher air-to-fuel ratio than the stoichiometric value, can result in incomplete combustion, leading to reduced power and increased emissions of nitrogen oxides (NOx). On the other hand, a rich mixture, with a lower air-to-fuel ratio, can cause excessive fuel consumption, increased carbon monoxide (CO) emissions, and reduced engine performance.
The engine's computer or electronic control unit (ECU) plays a vital role in managing the air-fuel ratio. It continuously monitors various parameters, such as engine speed, load, and temperature, to adjust the fuel injection and air intake accordingly. The ECU ensures that the air-fuel ratio is optimized for the specific driving conditions, providing a balance between power, efficiency, and emissions. Modern vehicles often employ sophisticated sensors and control algorithms to maintain the ideal air-fuel ratio, ensuring optimal engine performance and compliance with emissions regulations.
In summary, the air-fuel ratio is a critical factor in engine operation, impacting both performance and environmental impact. Achieving the ideal ratio of air to fuel is essential for efficient combustion, maximizing power output, and minimizing harmful emissions. Through advanced engine management systems, modern vehicles can maintain this optimal ratio, ensuring a well-balanced and environmentally friendly driving experience.
Maximize Your Car's Mileage: 5 Tips to Reduce Fuel Consumption
You may want to see also
Throttle Body: Regulates air flow, impacting engine response and fuel efficiency
The throttle body is a crucial component in the intricate process of air and fuel management within a car's engine. Its primary function is to regulate the airflow into the engine, which directly influences the engine's response and overall fuel efficiency. This component is often overlooked, but its impact on the vehicle's performance is significant.
Located between the air filter and the engine, the throttle body acts as a gatekeeper, controlling the amount of air that enters the engine's combustion chamber. When the driver presses the accelerator pedal, the throttle body opens, allowing a precise amount of air to flow into the engine. This process is a delicate balance, as too much air can lead to inefficient combustion, while too little can result in a lack of power and potential engine damage. The throttle body's design ensures that the air-fuel mixture is optimized for efficient combustion, which is essential for the engine's performance and longevity.
Its mechanism is quite intricate. It consists of a throttle plate, which is a flat, circular component that rotates when the accelerator is pressed. This plate is connected to a throttle position sensor, which sends feedback to the engine control unit (ECU). The ECU then adjusts the fuel injection and ignition timing accordingly. The sensor's role is critical as it provides real-time data on the throttle position, allowing the ECU to make precise adjustments to maintain optimal engine performance.
The impact of the throttle body on engine response is immediate. When the driver demands more power, the throttle body responds by opening wider, allowing a larger volume of air into the engine. This increased airflow results in a more robust combustion process, leading to a quicker and more responsive engine. Conversely, when the driver eases off the accelerator, the throttle body closes, reducing the airflow and allowing the engine to idle smoothly. This dynamic control ensures that the engine operates efficiently across various driving conditions.
Furthermore, the throttle body plays a vital role in fuel efficiency. By precisely regulating airflow, it helps optimize the air-fuel mixture, ensuring that the engine burns fuel efficiently. This efficiency is crucial for improving mileage and reducing fuel consumption. Modern vehicles often employ advanced throttle body designs, incorporating electronic controls to further enhance fuel economy and reduce emissions. These designs allow for more precise control over airflow, contributing to a more environmentally friendly and cost-effective driving experience.
The Environmental Impact of Car Fuel: A Deep Dive
You may want to see also
Evaporation Emission Control: Reduces fuel loss and improves engine operation
Evaporation Emission Control is a crucial system in modern vehicles designed to minimize fuel loss and optimize engine performance. This system plays a vital role in addressing the issue of fuel evaporation, which occurs when volatile hydrocarbons in gasoline vaporize and escape from the fuel tank and carburetor, especially during the refueling process or when the vehicle is stationary. By implementing effective evaporation emission control, cars can significantly reduce harmful emissions and improve overall engine efficiency.
The primary function of this control system is to capture and recycle the evaporated fuel, preventing it from entering the atmosphere. It achieves this through a series of components working together. One key element is the charcoal canister, which is typically located under the vehicle's floor. This canister is filled with activated charcoal, a highly porous material that absorbs and traps the evaporated fuel. As fuel vaporizes, it is drawn into the engine's intake system, where it can be burned, thereby reducing emissions. The charcoal canister continuously absorbs and stores these vapors until the engine is running, ensuring that no harmful emissions are released during periods of inactivity.
Another essential component is the vapor return line, which connects the fuel tank to the charcoal canister. This line allows the system to actively draw the evaporated fuel back into the tank, where it can be reused. When the engine is running, the vacuum created by the intake process pulls the stored fuel vapors from the canister, ensuring a continuous supply of fuel for combustion. This process not only reduces fuel loss but also improves engine performance by providing a steady and controlled fuel-air mixture.
Furthermore, the Evaporation Emission Control system incorporates a purge valve, which is strategically positioned in the intake manifold. This valve opens during engine operation, allowing the stored fuel vapors in the charcoal canister to be drawn into the engine's combustion chamber. By actively introducing these vapors, the system ensures that the engine receives a precise and efficient fuel-air mixture, resulting in improved power output and reduced emissions.
In summary, Evaporation Emission Control is a sophisticated mechanism that actively manages fuel evaporation, a common issue in vehicles. By capturing and recycling evaporated fuel, this system reduces fuel loss, enhances engine operation, and contributes to lower emissions. Through the use of charcoal canisters, vapor return lines, and purge valves, modern cars can effectively control fuel-related emissions, ensuring a more environmentally friendly and efficient driving experience.
Powering the Future: Unlocking the Secrets of Fuel Cell Technology in Cars
You may want to see also
Frequently asked questions
Monitoring your car's performance and fuel efficiency can provide insights. If your car is not getting enough air, you might notice poor acceleration, reduced power, and a decrease in fuel economy. Check for any warning lights on the dashboard, especially the check engine light, which could indicate an issue with the fuel or air intake system.
Insufficient fuel can lead to engine misfires, rough idling, and a lack of power. You may also experience frequent stalling, especially during acceleration or when driving at higher speeds. Keep an eye on your fuel gauge; if it drops rapidly or the 'low fuel' light comes on too quickly, it could be a sign of an issue with the fuel delivery system.
Regularly inspecting and replacing the air filter is crucial. A dirty air filter can restrict airflow, leading to reduced engine performance and increased fuel consumption. Check the air filter housing for any signs of damage or excessive dirt accumulation. It's recommended to replace the air filter at regular intervals or when the check engine light comes on, indicating a potential issue.
Yes, several problems can arise with the fueling system. Clogged fuel injectors or a faulty fuel pump can result in improper fuel delivery, causing engine misfires and reduced performance. Leaks in the fuel lines or a malfunctioning fuel pressure regulator can also lead to fuel-related issues. Regular maintenance and timely repairs are essential to ensure optimal fueling and engine operation.