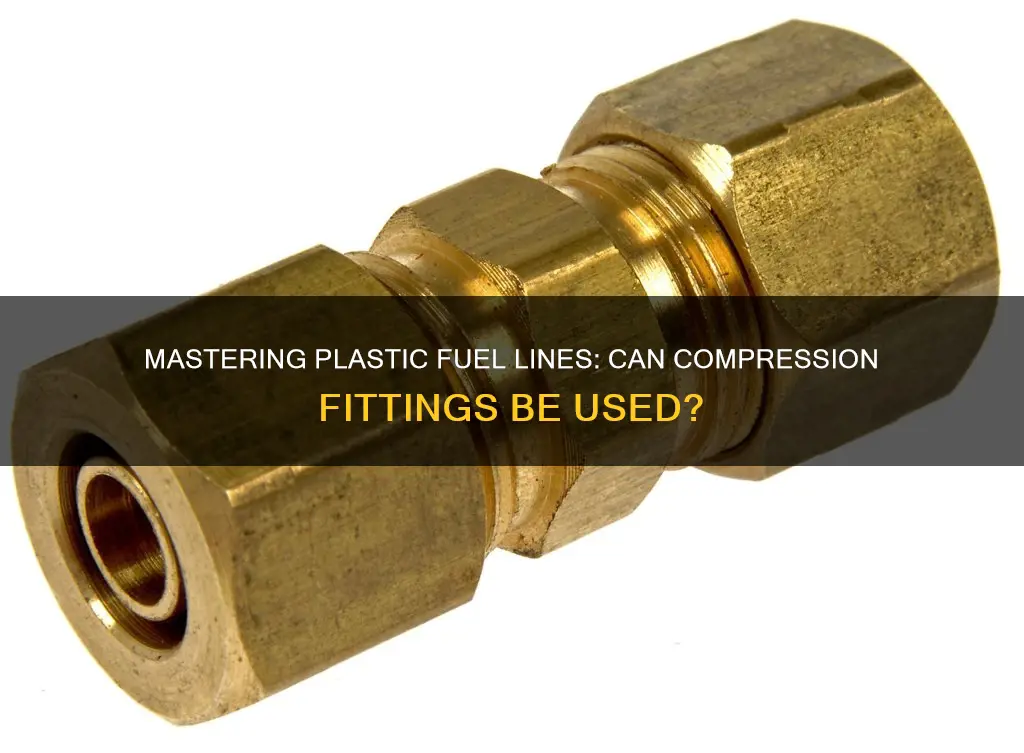
Compression fittings are commonly used for joining metal pipes, but their application to plastic fuel lines is a topic of debate among mechanics and engineers. While compression fittings can provide a secure and leak-free connection, the compatibility with plastic fuel lines is a concern due to the potential for damage to the plastic material. This paragraph aims to explore the feasibility and best practices for using compression fittings on plastic fuel lines, considering the unique properties and requirements of both materials.
Characteristics | Values |
---|---|
Compatibility | Compression fittings can be used on plastic fuel lines, but it's important to choose the right type and size for a secure and leak-free connection. |
Material | Plastic fuel lines are typically made from materials like polyethene (PE) or polypropylene (PP), which are compatible with compression fittings. |
Strength | Compression fittings provide a strong and reliable connection, ensuring the fuel line can withstand pressure and vibrations. |
Flexibility | Plastic fuel lines offer flexibility, allowing for easy routing and installation, which is beneficial when connecting to various engine components. |
Temperature Resistance | The choice of compression fitting material should match the operating temperature range of the fuel line to avoid degradation or failure. |
Ease of Installation | Compression fittings are generally easy to install, requiring only a few simple steps, making them a convenient option for DIY enthusiasts. |
Cost | Compression fittings and plastic fuel lines are often more affordable compared to other connection methods, making them a cost-effective solution. |
Availability | These fittings and fuel lines are widely available in hardware stores and automotive shops, ensuring accessibility for repairs and replacements. |
What You'll Learn
- Compatibility: Check if compression fittings are suitable for specific plastic fuel lines
- Material Strength: Ensure fittings can withstand fuel pressure and temperature changes
- Leaks: Proper installation prevents fuel leaks and ensures a secure connection
- Flexibility: Plastic fuel lines require flexible fittings that can adapt to movement
- Maintenance: Regular inspection and replacement of fittings are essential for fuel system longevity
Compatibility: Check if compression fittings are suitable for specific plastic fuel lines
When considering the use of compression fittings for plastic fuel lines, it is crucial to prioritize compatibility to ensure a secure and reliable connection. Plastic fuel lines are designed to be lightweight and flexible, but they may not always be compatible with standard compression fittings. The key factor to consider is the material of the fuel line and the type of compression fitting being used.
Compression fittings typically consist of a ferrule or sleeve that is crimped onto the fuel line. The ferrule is made of a hard, durable material that creates a tight seal when compressed. However, not all plastics are suitable for this process. Some common plastics used in fuel lines include polyvinyl chloride (PVC), high-density polyethylene (HDPE), and polypropylene. It is essential to check the manufacturer's specifications and guidelines for each type of plastic to determine the appropriate compression fitting.
For example, PVC fuel lines often require special PVC-rated compression fittings, as standard fittings may not provide a secure seal due to the material's properties. Similarly, HDPE and polypropylene fuel lines may need specific fittings designed to accommodate their unique characteristics. Using the wrong type of compression fitting can lead to leaks, reduced performance, or even damage to the fuel line over time.
To ensure compatibility, it is recommended to consult the fuel line manufacturer's documentation or contact their technical support team. They can provide detailed information on the recommended compression fittings and installation procedures for their specific fuel line products. Additionally, some manufacturers may offer custom-made fittings or adapters to accommodate unique fuel line configurations.
In summary, when working with plastic fuel lines, it is imperative to verify compatibility with the chosen compression fittings. By selecting the appropriate fittings for the specific plastic material, you can ensure a secure and reliable connection, maximizing the performance and longevity of the fuel line system. Always refer to the manufacturer's guidelines and seek expert advice when in doubt to avoid potential issues.
Unraveling the Mystery: Why Air Bubbles Form in Furnace Fuel Lines
You may want to see also
Material Strength: Ensure fittings can withstand fuel pressure and temperature changes
When considering the use of compression fittings for plastic fuel lines, it is crucial to prioritize material strength and durability. Plastic fuel lines are designed to handle the unique challenges of fuel transportation, including varying pressure and temperature conditions. The fittings used in this setup must be able to withstand these demands to ensure a reliable and safe system.
The primary concern with plastic fuel lines is their susceptibility to fuel pressure. Fuel, especially in high-performance vehicles, can exert significant force on the lines and fittings. Compression fittings, typically made from materials like brass or bronze, offer a secure connection by compressing the fuel line against the fitting's inner surface. However, the material of the fitting itself must be robust enough to handle this pressure without deforming or failing. Common materials for compression fittings include stainless steel, which provides excellent strength and corrosion resistance, ensuring the fittings can endure the demanding environment of a fuel system.
Temperature changes also play a critical role in material selection. Plastic fuel lines can experience extreme temperature variations, from cold starts in winter to high-temperature operation during extended use. Fittings must remain flexible and resilient across this range to avoid cracking or breaking. Materials like nylon or polypropylene, known for their flexibility and resistance to temperature extremes, are ideal choices for compression fittings in such applications. These materials can accommodate the expansion and contraction of the fuel line without compromising the integrity of the connection.
Additionally, the compatibility of the fitting material with the fuel type is essential. Different fuels, such as gasoline, diesel, or ethanol blends, may have unique chemical properties that can affect the fittings over time. For instance, ethanol-blended fuels can be more corrosive to certain materials. Therefore, choosing fittings made from materials resistant to fuel-related degradation, such as stainless steel or specific polymers, is vital to ensure long-term reliability.
In summary, when using compression fittings on plastic fuel lines, material strength and compatibility are key considerations. The fittings should be constructed from materials that can withstand fuel pressure, temperature fluctuations, and potential fuel-related corrosion. By selecting the right materials, you can ensure a robust and safe fuel system, minimizing the risk of leaks or system failures.
When Fuel Lines Detach: Understanding the Consequences and Solutions
You may want to see also
Leaks: Proper installation prevents fuel leaks and ensures a secure connection
The use of compression fittings on plastic fuel lines is a common practice in automotive repairs, but it requires careful attention to detail to ensure a secure and leak-free connection. Proper installation is crucial to prevent fuel leaks, which can be dangerous and costly. Here's a guide to help you understand the process and ensure a reliable setup.
When connecting fuel lines, it's essential to use the right tools and materials. Compression fittings are designed to create a tight seal between the fitting and the fuel line. These fittings typically consist of a body, a compression ring, and a nut. The body is made of a durable material that can withstand the pressure and temperature changes in the fuel system. The compression ring is a critical component, as it directly contacts the fuel line and creates the seal. It should be made of a compatible material, often a soft metal or a synthetic rubber, to ensure a secure grip without damaging the plastic fuel line.
Installation begins by ensuring the fuel line is clean and free of any debris or contaminants. Start by inserting the fuel line into the compression fitting, ensuring it is centered. Then, tighten the nut securely by hand, creating initial pressure on the fitting. This initial compression is vital to set the stage for a proper seal. Next, use a wrench to tighten the nut further, but be cautious not to over-tighten, as this can damage the fuel line or the fitting itself. The goal is to achieve a firm, even pressure around the entire fitting.
After tightening, inspect the connection for any signs of leakage. You can do this by applying a small amount of fuel line sealant or tape around the fitting and then gently pressing on the fitting to simulate pressure. If no leaks occur, the installation is successful. However, if any fuel escapes, it indicates that the fitting may not be seated correctly, or the compression ring might be damaged. In such cases, carefully remove the fitting, clean the surfaces, and re-install it, ensuring a proper alignment and tightening sequence.
Remember, the key to a successful installation is precision and attention to detail. Always use the correct tools and materials, and take the time to inspect your work. Properly installed compression fittings on plastic fuel lines will provide a reliable and secure connection, minimizing the risk of fuel leaks and ensuring the safety and efficiency of your vehicle's fuel system.
Choosing the Right Fuel Line for Your 2007 Suzuki DR650
You may want to see also
Flexibility: Plastic fuel lines require flexible fittings that can adapt to movement
When it comes to installing fuel lines, especially in automotive applications, the choice of fittings is crucial for both performance and longevity. Plastic fuel lines, in particular, present a unique challenge due to their inherent flexibility and the need for a secure connection. One common question that arises is whether compression fittings can be used with plastic fuel lines. The answer is a cautious yes, but with certain considerations.
Compression fittings are designed to create a tight seal by compressing the pipe or tube material. While they are effective for metal and rigid plastic lines, they may not be the best choice for plastic fuel lines. Plastic fuel lines are typically made from materials like PVC or polyethene, which are flexible and can expand or contract with temperature changes. This flexibility is a benefit in terms of reducing stress on the fuel system, but it also means that traditional compression fittings might not provide the necessary adaptability.
The key to successfully using compression fittings with plastic fuel lines lies in selecting the right type of fitting and ensuring a proper installation. One popular alternative is the use of quick-connect fittings, which are designed to be flexible and adaptable. These fittings often feature a barbed design with an internal O-ring or gasket, providing a secure seal without the need for compression. They are easy to install and can accommodate the movement of the fuel lines, making them a preferred choice for many mechanics.
Another option is the use of flexible compression fittings, which are specifically engineered to work with plastic materials. These fittings typically have a soft, rubberized body that conforms to the shape of the fuel line, creating a tight seal. The flexibility of the fitting allows it to move with the fuel line, ensuring a secure connection without the risk of damage. When using these fittings, it is essential to follow the manufacturer's guidelines for sizing and installation to ensure a reliable bond.
In summary, while compression fittings can be used with plastic fuel lines, it is essential to choose the right type of fitting and consider the flexibility of the fuel lines. Quick-connect fittings and flexible compression fittings are excellent alternatives that provide the necessary adaptability and security for a successful installation. Proper installation techniques and the use of compatible materials will ensure a long-lasting and reliable fuel system.
Fuel Line Fix: A Step-by-Step Guide to Repairing 1.4-Inch Lines
You may want to see also
Maintenance: Regular inspection and replacement of fittings are essential for fuel system longevity
Maintaining a fuel system is crucial to ensure the safe and efficient operation of any vehicle. One critical aspect of this maintenance is the regular inspection and timely replacement of compression fittings used in plastic fuel lines. These fittings play a vital role in connecting the fuel tank to the engine, and their condition directly impacts the overall performance and reliability of the fuel system.
Over time, compression fittings can degrade due to various factors. The primary concern is the potential for these fittings to become brittle and crack, especially when exposed to fuel's corrosive properties and temperature fluctuations. When this happens, the fittings may fail to provide a secure seal, leading to fuel leaks, which can be extremely dangerous. Additionally, the constant pressure and movement within the fuel system can cause the fittings to loosen or become dislodged, further exacerbating the risk of leaks and potential engine damage.
Regular inspections are the first line of defense against these issues. It is recommended that drivers and vehicle owners inspect the compression fittings at least once a year or whenever there are routine maintenance checks. During these inspections, look for any visible signs of damage, such as cracks, brittleness, or discoloration. Also, check for any signs of fuel leakage around the fittings. If any issues are detected, it is imperative to address them promptly.
Replacing the fittings is a straightforward process that can be performed by professionals or experienced DIY enthusiasts. When replacing, ensure that the new fittings are compatible with the type of fuel line used and that they are properly lubricated to facilitate a secure connection. It is also essential to follow the manufacturer's guidelines for torque specifications to ensure a tight, reliable seal. Regular maintenance and timely replacements will significantly contribute to the longevity of the fuel system, preventing costly repairs and ensuring the vehicle's optimal performance.
Dirt Bike Fuel Line: Top Stores for Your Ride
You may want to see also
Frequently asked questions
Yes, compression fittings can be used for plastic fuel lines, but it's important to choose the right type of fitting and ensure a proper installation. Compression fittings are commonly used for joining plastic fuel lines because they provide a secure and leak-tight connection without the need for soldering or welding.
Compression fittings offer several benefits for plastic fuel lines. They are easy to install, requiring only a few simple steps. These fittings create a tight seal by compressing the fuel line material, ensuring a reliable connection. Additionally, they are cost-effective and widely available, making them a popular choice for automotive applications.
When using compression fittings on plastic fuel lines, it's crucial to select the appropriate size and type of fitting for the fuel line diameter. Using the wrong size can lead to poor sealing or even damage to the fuel line. It's also essential to ensure that the fuel line material is compatible with the fitting material to avoid any potential degradation or leaks.
Compression fittings are generally not designed to be reused or repaired once they have failed. If a compression fitting leaks, it is best to replace it entirely. Reusing or attempting to repair a failed fitting may compromise the integrity of the fuel system and could lead to further issues. It's always recommended to replace faulty fittings with new ones to maintain the safety and reliability of the fuel line connection.