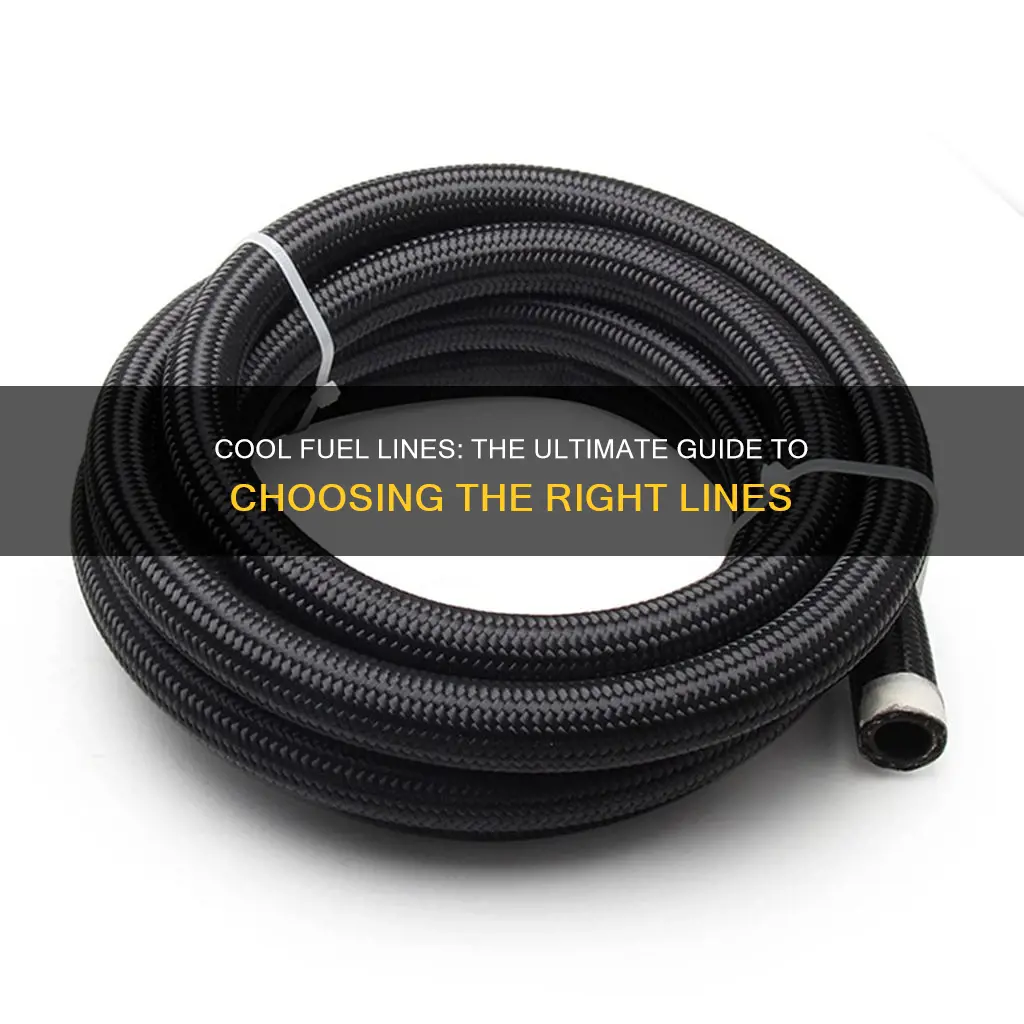
Cooling fuel lines are an essential component of any vehicle's cooling system, and proper maintenance is crucial to ensure optimal performance and longevity. These lines are responsible for transferring coolant from the engine to the radiator, where it dissipates heat and maintains the engine's operating temperature. Over time, fuel lines can degrade due to factors such as age, heat, and chemical exposure, leading to potential issues like coolant leaks, reduced engine performance, and even engine damage. Understanding the types of fuel lines available, their installation process, and the signs of wear and tear is vital for vehicle owners and mechanics alike to ensure the efficient operation of the cooling system and the overall health of the engine.
What You'll Learn
- Engine Cooling Systems: Efficient cooling lines ensure optimal engine performance and longevity
- Coolant Flow: Proper flow rate and circulation maintain engine temperature within safe limits
- Heat Exchange: Effective heat exchangers transfer heat from coolant to radiator for efficient cooling
- Coolant Types: Different coolants have varying properties, affecting engine cooling and corrosion resistance
- Cooling Line Material: Choosing the right material for cooling lines prevents leaks and corrosion
Engine Cooling Systems: Efficient cooling lines ensure optimal engine performance and longevity
Engine cooling systems are an essential component of any vehicle's engine, ensuring optimal performance and longevity. At the heart of this system are the cooling lines, which play a critical role in maintaining the engine's operating temperature within the ideal range. These lines are responsible for transferring heat from the engine to the radiator, allowing for efficient cooling and preventing overheating.
The design and efficiency of cooling lines are crucial for several reasons. Firstly, they help regulate the engine's temperature, ensuring it operates at the optimal level for performance and fuel efficiency. When an engine runs too hot, it can lead to increased wear and tear, reduced power output, and even permanent damage. Conversely, an engine that runs too cold may struggle to start and can experience reduced performance and fuel economy. Therefore, an efficient cooling system is vital for maintaining the engine's health and overall performance.
Cooling lines are typically made of materials that can withstand high temperatures and pressures, such as aluminum or brass. These materials are chosen for their ability to efficiently transfer heat while maintaining structural integrity. The lines are designed with specific diameters and lengths to ensure optimal flow and heat dissipation. Engineers carefully consider factors such as the engine's power output, operating conditions, and the vehicle's overall design when specifying the cooling lines.
In addition to the lines themselves, the overall engine cooling system includes components like the radiator, coolant, and fans. The radiator is designed to dissipate heat from the coolant, which is circulated through the engine block and cooling lines. The coolant acts as a heat transfer medium, absorbing and carrying heat away from the engine. Fans are often used to enhance air circulation around the radiator, further improving cooling efficiency.
Regular maintenance and inspection of the cooling lines are essential to ensure their longevity and optimal performance. Over time, cooling lines can develop leaks, blockages, or damage due to corrosion or impact. These issues can lead to reduced cooling efficiency, engine overheating, and potential engine failure. Therefore, it is crucial to inspect the lines periodically, replace any damaged or worn-out components, and ensure the system is properly flushed and refilled with fresh coolant as recommended by the manufacturer.
Ultimate Guide: Best Fuel Line Material for Maximum Performance
You may want to see also
Coolant Flow: Proper flow rate and circulation maintain engine temperature within safe limits
The efficient management of engine temperature is crucial for optimal performance and longevity. One of the key components in this process is the coolant flow, which involves the proper flow rate and circulation of the coolant through the engine. This system is designed to absorb and transfer heat away from the engine block, ensuring that the engine operates within a safe temperature range.
The flow rate of the coolant is critical as it directly impacts the engine's ability to maintain optimal temperatures. Insufficient flow can lead to overheating, as the coolant may not be able to effectively absorb and dissipate heat. Conversely, excessive flow can result in coolant loss and potential engine damage. Therefore, it is essential to maintain a balanced flow rate that ensures efficient heat transfer without compromising the system's integrity.
Proper circulation is another vital aspect of coolant management. Coolant circulation involves the continuous movement of the coolant through the engine's passages and radiator. This circulation helps to distribute heat evenly and prevents the formation of hot spots. When the coolant circulates effectively, it can efficiently carry heat away from the engine components, allowing for better temperature control.
To ensure optimal coolant flow, it is recommended to regularly check and maintain the coolant system. This includes inspecting the coolant level, checking for any leaks, and verifying the condition of the radiator and hoses. Over time, coolant can degrade and lose its effectiveness, so regular replacement is necessary. Additionally, using a coolant additive can help maintain the coolant's properties and ensure its ability to protect engine components.
In summary, maintaining proper coolant flow is essential for engine health. By ensuring an adequate flow rate and efficient circulation, the engine can operate at its optimal temperature, reducing the risk of overheating and potential damage. Regular maintenance and monitoring of the coolant system are key practices to guarantee the engine's longevity and reliable performance.
Understanding the Car's Fuel Line: A Comprehensive Guide
You may want to see also
Heat Exchange: Effective heat exchangers transfer heat from coolant to radiator for efficient cooling
Heat exchangers are crucial components in any cooling system, especially in engines, where efficient heat transfer is essential to maintain optimal performance and prevent overheating. The primary function of a heat exchanger is to facilitate the transfer of heat from a coolant (often a liquid or a mixture of liquids) to a radiator, which then dissipates the heat into the surrounding environment. This process is vital for cooling fuel systems, ensuring that the fuel remains at an ideal temperature for efficient combustion.
Effective heat exchangers are designed to maximize heat transfer efficiency, which is achieved through several key factors. Firstly, the surface area of the heat exchanger plays a significant role. A larger surface area provides more contact points for heat transfer, allowing for more efficient cooling. This is often achieved by using fins or extended surfaces on the exchanger's tubes or plates, which increase the overall surface area exposed to the coolant.
Secondly, the flow rate of the coolant is critical. A higher flow rate increases the heat transfer coefficient, which is a measure of the heat transfer rate per unit area. By ensuring a steady and consistent flow of coolant through the heat exchanger, the system can effectively remove heat from the fuel, preventing overheating. This is typically controlled by the engine's cooling system, which regulates the coolant's speed and pressure.
The design of the heat exchanger itself is another important aspect. Different designs, such as shell and tube, plate and frame, or spiral wound heat exchangers, offer varying levels of efficiency. For instance, shell and tube exchangers provide excellent heat transfer capabilities due to their large surface area and efficient fluid flow. Plate and frame exchangers, on the other hand, are compact and offer good heat transfer rates, making them suitable for space-constrained applications.
In addition to these design considerations, the material used for the heat exchanger is crucial. Materials like aluminum or copper alloys are often preferred due to their high thermal conductivity, which allows for rapid heat transfer. These materials are also lightweight and corrosion-resistant, ensuring the longevity and reliability of the cooling system. Proper sealing and insulation of the heat exchanger are also essential to prevent coolant leaks and maintain system efficiency.
In summary, effective heat exchangers are the backbone of efficient cooling systems, especially for fuel cooling. By maximizing surface area, controlling coolant flow rates, and utilizing appropriate designs and materials, engineers can ensure that heat is efficiently transferred from the coolant to the radiator. This, in turn, maintains the optimal temperature of the fuel, leading to improved engine performance and longevity. Understanding these principles is key to designing and maintaining reliable cooling systems for various applications.
Echo PB 200 Fuel Line Size: A Comprehensive Guide
You may want to see also
Coolant Types: Different coolants have varying properties, affecting engine cooling and corrosion resistance
Coolant, often referred to as engine coolant, is a liquid mixture that plays a crucial role in maintaining the optimal operating temperature of an engine. It is designed to absorb and transfer heat, ensuring the engine runs at a stable temperature while preventing overheating. The choice of coolant type is essential as different coolants possess unique properties that can significantly impact engine performance and longevity.
One of the primary considerations when selecting a coolant is its ability to facilitate efficient heat exchange. Coolants typically contain a mixture of water and a special additive that enhances their heat transfer capabilities. These additives often include ethylene glycol or propylene glycol, which act as antifreeze agents, preventing the coolant from freezing in cold climates and boiling at high temperatures. The presence of these additives also contributes to the coolant's ability to lubricate the engine's internal components, reducing friction and wear.
The properties of coolants can vary widely, and this variation directly influences their performance in different engine systems. Some coolants are designed to provide excellent engine cooling, especially in high-performance vehicles or those operating in extreme conditions. These coolants often have a higher concentration of additives, ensuring optimal heat dissipation and engine protection. On the other hand, some coolants prioritize corrosion resistance, making them ideal for older vehicles or those with aluminum components, as they help prevent engine block and cylinder head corrosion.
In addition to engine cooling and corrosion prevention, coolants also play a role in maintaining the engine's cleanliness. Modern coolants often contain additives that help disperse and suspend contaminants, such as rust and scale, preventing them from building up inside the engine. This is particularly important in ensuring the longevity and proper functioning of the engine's internal components.
When choosing a coolant, it is essential to consider the specific requirements of your vehicle. Different engines may have unique needs, and using the correct type of coolant is vital for optimal performance. Consulting the vehicle's manual or seeking advice from automotive experts can help in selecting the most suitable coolant type, ensuring your engine remains cool, clean, and well-protected.
Freezing Fuel: The Impact of Water in Fuel Lines
You may want to see also
Cooling Line Material: Choosing the right material for cooling lines prevents leaks and corrosion
When it comes to cooling lines for fuel systems, selecting the appropriate material is crucial to ensure the longevity and reliability of the entire setup. The primary goal is to prevent leaks and corrosion, which can lead to costly repairs and potential safety hazards. Here's an in-depth look at the key considerations for choosing the right material:
Material Compatibility: The first step is to understand the compatibility of materials with the fuel being transported. Different fuels have varying chemical compositions, and some materials may react with the fuel over time, leading to degradation. For instance, certain plastics might not be suitable for fuels with high alcohol content, as they can become brittle and crack. On the other hand, materials like stainless steel or specific alloys are often preferred for their resistance to corrosion and compatibility with a wide range of fuels.
Temperature Resistance: Cooling lines are exposed to varying temperatures, especially in high-performance applications. Materials should be chosen to withstand these temperature fluctuations without compromising their structural integrity. For example, if the cooling lines are used in an engine with a high-temperature exhaust, materials like aluminum alloys or specialized plastics with excellent thermal stability should be considered. These materials can handle extreme temperatures without warping or becoming brittle.
Flexibility and Durability: Cooling lines need to be flexible enough to accommodate engine movement and vibrations without cracking or breaking. Materials like rubber or certain types of flexible plastics can provide the necessary flexibility. However, they should also be durable to withstand the harsh environment inside an engine bay. Reinforcing these flexible materials with braided reinforcement or adding protective layers can enhance their durability.
Leak Prevention: To prevent leaks, the material's ability to form a tight seal is essential. Materials like PTFE (polytetrafluoroethylene) or specialized rubber compounds can create reliable seals. These materials are often used in the form of gaskets or O-rings to ensure a secure connection between components. Additionally, the manufacturing process should be meticulous to avoid any defects that could lead to leaks.
Corrosion Resistance: Corrosion is a significant concern, especially in environments with high humidity or exposure to road salt. Materials like stainless steel, which forms a protective oxide layer, are highly resistant to corrosion. For applications where corrosion is a primary concern, choosing materials with excellent corrosion-resistant properties is imperative. This ensures that the cooling lines remain effective over an extended period without deterioration.
In summary, selecting the right material for cooling lines involves a careful consideration of compatibility, temperature resistance, flexibility, leak prevention, and corrosion resistance. By choosing materials that excel in these areas, engineers can design fuel systems that are not only efficient but also highly reliable, minimizing the risk of leaks and corrosion-related issues.
Understanding Saturn Fuel Line Inner Diameter: A Comprehensive Guide
You may want to see also
Frequently asked questions
Fuel cooling is an essential process in modern vehicles, especially in regions with colder climates. The primary goal is to maintain the optimal temperature of the fuel, ensuring it remains in a liquid state and functions efficiently. This process helps prevent fuel condensation, which can lead to engine performance issues and potential damage.
By keeping the fuel at the right temperature, the engine can operate more efficiently. Cooler fuel has a higher energy content, allowing for better combustion and increased power output. This results in improved engine performance, faster acceleration, and enhanced overall driving experience.
Neglecting fuel cooling can lead to several problems. In colder temperatures, fuel can thicken and become less volatile, making it harder for the engine to ignite. This may result in poor engine performance, reduced power, and even starting difficulties. Additionally, uncooled fuel can lead to increased engine wear and potential long-term damage due to improper combustion.