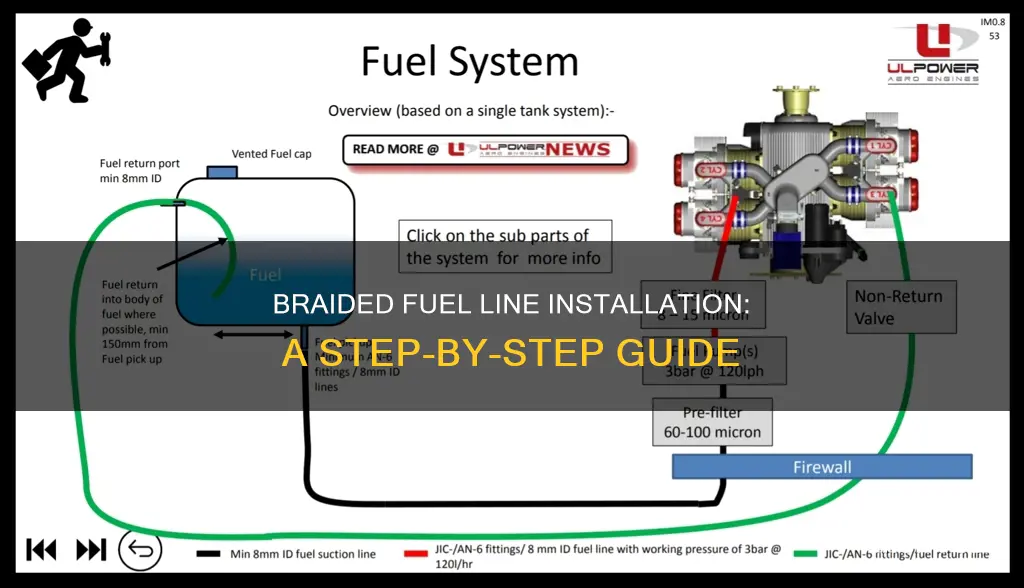
Installing steel braided fuel lines is a great way to improve the performance and reliability of your vehicle's fuel system. These lines are designed to be more durable and flexible than traditional rubber hoses, making them less prone to cracking and leaking over time. In this guide, we'll walk you through the process of installing steel braided fuel lines, ensuring your vehicle receives the fuel it needs efficiently and safely. We'll cover the necessary tools and materials, as well as step-by-step instructions for a successful installation.
What You'll Learn
- Prepare Tools: Gather necessary tools like fuel line cutters, crimping pliers, and fuel line cleaner
- Inspect Fuel System: Check for any leaks or damage before replacing the fuel lines
- Cut and Prepare Lines: Measure and cut the steel braided fuel lines to the correct length
- Crimp Connections: Use crimping pliers to secure connections, ensuring a tight and reliable bond
- Test and Clean: After installation, test for leaks and clean the system to ensure optimal performance
Prepare Tools: Gather necessary tools like fuel line cutters, crimping pliers, and fuel line cleaner
Before you begin the installation process, it's crucial to gather the right tools to ensure a smooth and efficient job. Here's a breakdown of the essential tools you'll need:
Fuel Line Cutters: These specialized cutting tools are designed to precisely trim fuel lines to the desired length. Look for a set that includes different sizes to accommodate various fuel line diameters. Ensure they are sharp and capable of cutting through the steel braided material without damaging it.
Crimping Pliers: Crimping pliers are a must-have for securing the fuel lines. They provide the necessary pressure to create a tight, leak-free connection. Choose a pair with adjustable jaws to accommodate different fuel line sizes. The ability to crimp both ends of the line is essential for a complete installation.
Fuel Line Cleaner: Cleaning is an often-overlooked but critical step. Use a fuel line cleaner to remove any contaminants, old fuel, or debris from the existing fuel lines. This ensures a clean and reliable connection for the new braided fuel lines. Opt for a cleaner that is compatible with the fuel system materials to avoid any adverse reactions.
Additionally, consider having a fuel line inspection mirror, a small torch for lighting tight spaces, and safety gear like gloves and eye protection. These tools will make the installation process safer and more manageable. With the right preparation, you'll be well-equipped to tackle the installation of steel-braided fuel lines.
Mastering the Art of Fuel Line Wrenching: A Comprehensive Guide
You may want to see also
Inspect Fuel System: Check for any leaks or damage before replacing the fuel lines
Before embarking on the task of replacing fuel lines with steel braided options, it is crucial to thoroughly inspect the fuel system to ensure a successful and safe installation. This initial step is often overlooked but is essential to identify potential issues and ensure the new fuel lines are installed correctly.
Start by identifying the fuel lines in your vehicle. These lines are typically made of rubber or plastic and carry fuel from the tank to the engine. Locate the fuel tank and trace the lines to their respective connections at the engine. Inspect each line for any visible signs of damage, such as cracks, punctures, or swelling. Look for any signs of deterioration, especially in areas where the lines are exposed to heat or vibration.
The next step is to check for leaks. This is a critical aspect of the inspection process. You can use a few methods to detect leaks. One common technique is to spray a soapy water solution on the fuel lines and connections. If you notice any bubbles forming, it indicates a leak. Alternatively, you can use a fuel line dye or a specialized leak detection spray to identify leaks more precisely. Apply the dye or spray to the fuel lines and connections, then observe for any discoloration or wet spots, which would signify a leak.
In addition to visual inspections, it's important to check for any signs of fuel contamination. Over time, fuel can accumulate contaminants, such as water or debris, which can cause issues with the engine's performance. Check the fuel filter for any signs of clogging or contamination. If the filter is dirty or shows signs of degradation, it may indicate a problem with the fuel system that requires attention.
By thoroughly inspecting the fuel system before replacing the fuel lines, you can identify and address any existing issues. This ensures that the new steel braided fuel lines are installed in a system that is already in good condition, reducing the risk of future problems and ensuring optimal engine performance. It is a crucial step that should not be skipped to guarantee a successful and safe installation.
Octane Fuel Lines: Unlocking Power or Overkill?
You may want to see also
Cut and Prepare Lines: Measure and cut the steel braided fuel lines to the correct length
When preparing to install steel braided fuel lines, accurate measurements and precise cutting are crucial steps to ensure a successful and safe installation. Here's a detailed guide on how to measure and cut the lines:
Measuring the Required Length: Begin by referring to the vehicle's manual or the manufacturer's specifications to determine the exact length of fuel lines needed. Take into account the existing lines and any additional length required to reach the fuel source and the engine. Measure twice to ensure accuracy, as this step is critical to avoid cutting too much or too little. Use a flexible measuring tape or a ruler to get precise measurements.
Marking the Cutting Points: Once you have the correct length, mark the steel braided fuel lines at the measured points. You can use a permanent marker or a piece of chalk to create clear lines. Ensure that the marks are aligned with the ends of the lines to facilitate a straight cut. It's important to mark both the inner and outer layers of the braided fuel line to ensure an even cut.
Cutting Technique: Utilize a sharp utility knife or a specialized fuel line cutter for clean and precise cuts. Hold the line firmly and cut along the marked lines, being careful not to cut the braided strands. If using a knife, make sure to cut through the outer layer first, then carefully slice through the inner layers. For a cleaner cut, you can also use a pair of scissors designed for fuel lines, ensuring you cut through all layers without damaging the inner fuel-carrying tube.
Safety Precautions: When cutting, work in a well-ventilated area and wear protective gear, such as gloves, to avoid any potential hazards. Keep children and pets away from the work area to prevent accidents. Always be mindful of the cutting process to avoid any accidental cuts or damage to nearby components.
By following these steps, you'll ensure that the steel braided fuel lines are cut to the precise length required, setting the foundation for a successful installation. Remember, accurate measurements and careful cutting are essential to maintaining the integrity of the fuel system and overall vehicle performance.
Understanding B1 Fuel Line: A Comprehensive Guide
You may want to see also
Crimp Connections: Use crimping pliers to secure connections, ensuring a tight and reliable bond
When it comes to installing steel braided fuel lines, ensuring secure and reliable connections is crucial to maintain optimal performance and prevent potential issues. One effective method for achieving this is through crimp connections. This technique involves using crimping pliers to create a tight and secure bond between the fuel line and various components, such as fittings and adapters.
Crimping provides a mechanical connection that offers several advantages. Firstly, it creates a robust and durable bond, ensuring that the fuel lines remain firmly in place even under varying conditions. This is particularly important in high-performance vehicles or those operating in challenging environments where vibrations and temperature fluctuations are common. By using crimping pliers, you can apply precise pressure to the connection points, ensuring a snug fit that prevents fuel leaks and potential system failures.
To begin the crimping process, you'll need to gather the necessary tools and materials. Crimping pliers specifically designed for this purpose are essential, as they provide the required force to create a secure bond. Ensure that the pliers are compatible with the fuel line and fitting sizes you are working with. Additionally, you may need to use crimping dies or inserts, which are often included with the pliers, to guide the process and ensure consistent results.
The crimping technique involves carefully positioning the fuel line and fitting, ensuring proper alignment. Then, using the crimping pliers, apply firm and consistent pressure to the connection point. The goal is to create a visible deformation or 'crimp' on the fuel line, indicating a secure bond. It's important to follow the manufacturer's guidelines for the specific crimping force required to achieve the desired connection strength. Over-crimping can damage the fuel line, while under-crimping may result in a weak connection.
Regularly inspect the crimp connections to ensure their integrity. Check for any signs of looseness or damage, especially in areas prone to vibration or movement. Properly secured crimp connections will contribute to the overall reliability of your fuel system, ensuring efficient fuel delivery and optimal engine performance. Remember, taking the time to master the art of crimp connections will pay off in the long run, providing a solid foundation for a well-maintained fuel system.
Mastering the Art of Fuel Line Removal: A Step-by-Step Guide
You may want to see also
Test and Clean: After installation, test for leaks and clean the system to ensure optimal performance
After completing the installation of steel-braided fuel lines, it is crucial to conduct a thorough test and cleaning process to ensure the system's optimal performance and longevity. This step is often overlooked, but it plays a vital role in maintaining the integrity of your fuel system. Here's a detailed guide on how to approach this task:
Testing for Leaks:
The first and most critical step is to check for any leaks in the newly installed fuel lines. Start by ensuring that the engine is off and the vehicle is in a stable position. Use a soapy water solution, a common and effective method for leak detection. Apply the solution to all connections, joints, and bends in the fuel lines. If a leak is present, you will notice bubbles forming on the surface where the soap has been applied. These bubbles indicate a potential issue that needs immediate attention. If no leaks are found, proceed to the next step.
Pressure Testing:
For a more comprehensive test, consider using a fuel pressure gauge. This method helps identify any potential issues with the fuel pump or restrictions in the line. Start the engine and allow it to idle. Connect the pressure gauge to the fuel rail or line, ensuring a secure connection. Read the gauge and compare the readings to the manufacturer's specifications. If the pressure is significantly lower or higher than the recommended range, it may indicate a problem that requires further investigation.
System Cleaning:
Cleaning the fuel system is essential to remove any contaminants that may have accumulated during installation or transportation. Start by disconnecting the fuel lines from the engine and fuel tank. Use a fuel line cleaner or a suitable solvent to flush out any debris or old fuel. Ensure you follow the instructions provided by the cleaner manufacturer. Rinse the lines thoroughly to remove any residue. For a more thorough clean, consider using a fuel system cleaner that can be injected directly into the engine's fuel supply, following the product's guidelines.
Final Inspection:
After cleaning, perform a final visual inspection of the entire fuel system. Check for any signs of damage, corrosion, or debris buildup. Ensure that all connections are tight and secure. Verify that the fuel lines are properly routed and not rubbing against any moving parts or sharp edges. This inspection will help identify any potential issues that may have been missed during the installation process.
By following these steps, you can ensure that your steel-braided fuel lines are installed correctly and function optimally. Regular maintenance and testing will contribute to the overall reliability and performance of your vehicle's fuel system.
Harley Road King Fuel Line Size: Expert Guide
You may want to see also
Frequently asked questions
Steel braided fuel lines offer several advantages over traditional rubber hoses. They are more durable, flexible, and resistant to heat and fuel degradation. The braided design provides excellent flexibility, allowing for easy installation around tight spaces and engine components. Additionally, these lines are less prone to cracking and leaking, ensuring a reliable fuel supply to the engine.
Before installation, ensure you have the necessary tools and materials, including the new fuel lines, fuel line connectors, and a fuel filter. Clean the engine bay and remove any old fuel lines or hoses. It's crucial to inspect the fuel system for any signs of damage or corrosion, as these issues should be addressed before installation.
While it is possible to install steel braided fuel lines yourself, especially if you have experience with automotive repairs, it is recommended to have some mechanical knowledge and skills. The process involves understanding the fuel system layout, proper routing, and secure connections. If you're unsure or uncomfortable with the task, consulting a professional mechanic is advisable to ensure a safe and correct installation.
Routing the fuel lines is a critical step to ensure optimal performance and longevity. The lines should be routed away from heat sources, such as exhaust manifolds and headers, to prevent damage from heat. Keep the lines as straight as possible to minimize stress on the braided material. Allow enough length for flexibility during engine movement, and secure the lines using appropriate ties or clips to prevent tangling or interference with other components.
Connecting the fuel lines requires careful attention to detail. Start by attaching the fuel pump line to the pump outlet, ensuring a tight connection. Then, route the line to the fuel filter, and finally, to the engine's fuel rail or injectors. Use fuel line connectors to secure the connections and ensure a leak-free seal. It's essential to check for any signs of leakage after installation and tighten connections as needed.