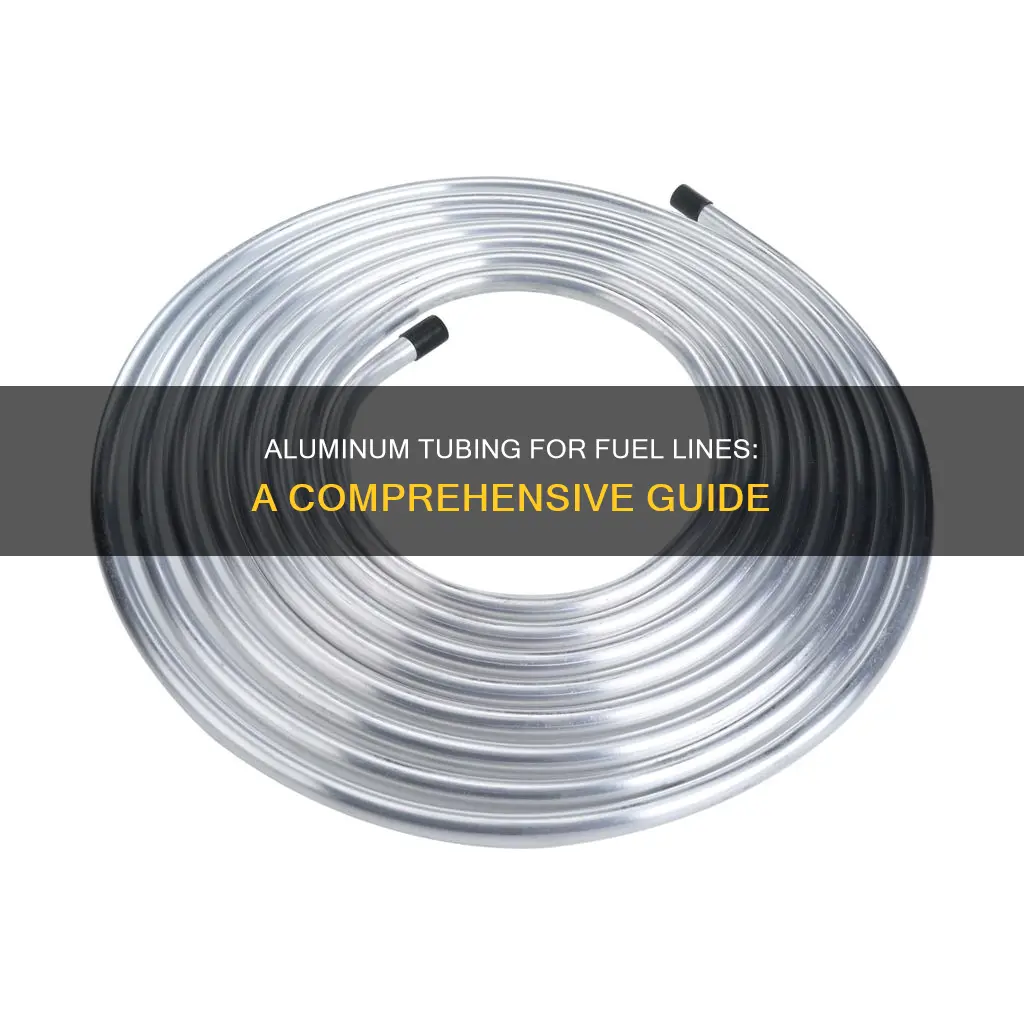
Aluminum tubing is a versatile material that can be used for various applications, including fuel lines. While it may not be the most common choice for fuel lines due to its lower cost and weight compared to other materials, it can be a viable option in certain scenarios. This paragraph will explore the advantages and considerations of using aluminum tubing for fuel lines, including its corrosion resistance, flexibility, and potential challenges.
Characteristics | Values |
---|---|
Corrosion Resistance | Aluminum tubing is highly resistant to corrosion, especially in the presence of fuel, which can help prevent leaks and maintain the integrity of the fuel system over time. |
Flexibility | It offers good flexibility, allowing for easier installation and the ability to accommodate slight movements in the vehicle's structure. |
Lightweight | The material is lightweight, reducing the overall weight of the fuel system and potentially improving vehicle performance. |
Heat Conductivity | Aluminum has good thermal conductivity, which can help dissipate heat away from the fuel lines, especially in high-temperature environments. |
Cost | It is generally more affordable than other materials like stainless steel, making it a cost-effective option for fuel lines. |
Availability | Aluminum tubing is widely available and can be easily sourced from hardware stores or automotive suppliers. |
Weldability | This material can be easily welded, providing a secure and reliable connection for fuel lines. |
Strength | While not as strong as steel, aluminum tubing can still provide adequate strength for fuel lines, especially when used in conjunction with proper fittings and supports. |
Compatibility | It is compatible with most fuels, including gasoline, diesel, and biofuels, making it a versatile choice for various vehicle applications. |
Maintenance | Aluminum fuel lines may require less maintenance due to their corrosion resistance, reducing the need for frequent inspections and replacements. |
What You'll Learn
- Material Compatibility: Aluminum tubing is compatible with most fuels, but not all
- Corrosion Resistance: Aluminum can corrode in certain environments, affecting fuel line durability
- Flexibility: Aluminum tubing offers good flexibility, making it suitable for fuel lines with bends
- Weight: Lighter than steel, aluminum tubing reduces vehicle weight and fuel consumption
- Cost: Aluminum tubing is generally more affordable than other materials, making it a cost-effective option
Material Compatibility: Aluminum tubing is compatible with most fuels, but not all
Aluminum tubing is a popular choice for fuel lines due to its lightweight nature and corrosion resistance, making it an ideal material for various applications. However, it's essential to understand that not all fuels are compatible with aluminum. The compatibility of aluminum tubing with different fuels depends on several factors, including the fuel's chemical properties and the specific requirements of the fuel system.
In general, aluminum is compatible with most conventional fuels, such as gasoline, diesel, and kerosene. These fuels typically have a neutral pH level, which means they do not corrode or react with aluminum. Aluminum tubing can withstand the typical fuel pressures and temperatures found in most vehicles and machinery without any significant degradation. For example, aluminum fuel lines are commonly used in automotive applications, ensuring efficient fuel delivery while maintaining the structural integrity of the vehicle.
However, there are some fuels that may not be suitable for aluminum tubing. One such fuel is ethanol, which has a higher pH level and can corrode aluminum over time. Ethanol-blended fuels, such as E85, require special consideration and may necessitate the use of additional protective coatings or alternative materials to ensure compatibility and prevent fuel leaks. Similarly, fuels with high acidic content, like some racing fuels, can also lead to corrosion and should be avoided when using aluminum tubing.
To ensure the longevity and reliability of the fuel system, it is crucial to consult the manufacturer's guidelines and specifications for the particular fuel being used. Some fuel suppliers provide recommendations or restrictions regarding the use of aluminum tubing, ensuring optimal performance and safety. Additionally, considering the specific environmental conditions and operating temperatures of the application can further guide the selection of the most compatible fuel and tubing material.
In summary, while aluminum tubing is a versatile and widely used material for fuel lines, it is essential to recognize that not all fuels are compatible. Factors such as pH levels, acidic content, and specific fuel requirements should be considered to ensure the proper functioning and longevity of the fuel system. By understanding these compatibility considerations, engineers and enthusiasts can make informed decisions when selecting materials for fuel lines, optimizing performance, and ensuring safety.
Mastering the Art of Fuel Line Clamp Removal: A Step-by-Step Guide
You may want to see also
Corrosion Resistance: Aluminum can corrode in certain environments, affecting fuel line durability
Aluminum tubing has been a popular choice for fuel lines in various applications due to its lightweight nature and ability to withstand high temperatures. However, one significant concern when considering aluminum for fuel lines is its corrosion resistance. While aluminum is an excellent material for many applications, it is not inherently resistant to corrosion, especially in certain environments.
Corrosion occurs when aluminum comes into contact with certain chemicals, moisture, or electrolytes, leading to the formation of oxides and other compounds on its surface. In the context of fuel lines, this corrosion can have detrimental effects on the system's performance and longevity. Over time, the corroded aluminum can become brittle, leading to cracks or even complete failure of the fuel line. This is particularly critical in fuel systems, where the integrity of the fuel supply is essential for the safe operation of vehicles or machinery.
The environment in which the fuel line is used plays a crucial role in determining the likelihood of corrosion. For instance, fuel lines in marine environments are more susceptible to corrosion due to the presence of saltwater, which contains electrolytes that accelerate the corrosion process. Similarly, fuel lines in industrial settings, where exposure to harsh chemicals or moisture is common, may also face a higher risk of corrosion. In such cases, alternative materials like stainless steel or specialized coatings on aluminum tubing might be necessary to ensure long-term durability.
To mitigate the corrosion issue, manufacturers often employ various techniques. One common method is to apply protective coatings to the aluminum tubing. These coatings can include zinc plating, chromate conversion coatings, or specialized polymer coatings designed to create a barrier between the aluminum and corrosive elements. Additionally, some fuel lines use a combination of materials, such as a stainless steel outer shell with an aluminum inner tube, to take advantage of the strength and thermal properties of aluminum while minimizing corrosion.
In summary, while aluminum tubing offers several advantages for fuel lines, its susceptibility to corrosion in certain environments is a critical consideration. Proper material selection, protective coatings, and careful environmental management are essential to ensure the durability and reliability of fuel systems using aluminum components. Understanding these factors can help engineers and designers make informed decisions when specifying fuel line materials for different applications.
Will 5/16 Fuel Line Handle 330HP? Unlocking Engine Potential
You may want to see also
Flexibility: Aluminum tubing offers good flexibility, making it suitable for fuel lines with bends
Aluminum tubing is an excellent choice for fuel lines due to its inherent flexibility, which is a crucial factor in ensuring a reliable and efficient fuel system. When it comes to fuel lines, especially in automotive applications, the ability to navigate through tight spaces and accommodate bends is essential. This is where aluminum tubing truly shines.
The flexibility of aluminum tubing is attributed to its material properties. Aluminum is known for its ductility, allowing it to bend and twist without permanent deformation. This characteristic is particularly advantageous when dealing with fuel lines that may need to follow the contours of a vehicle's engine bay, which often involves intricate and complex routes. By using aluminum tubing, you can ensure that the fuel lines remain flexible and adaptable, reducing the risk of damage during installation and operation.
In comparison to other materials, such as steel or plastic, aluminum tubing offers a unique advantage in terms of flexibility. Steel, while strong, is more rigid and less pliable, making it less ideal for fuel lines that require frequent bending. Plastic tubing, on the other hand, may lack the durability needed for fuel lines, as it can become brittle over time. Aluminum strikes a perfect balance between flexibility and strength, making it an excellent choice for this application.
When designing a fuel system, engineers often face the challenge of routing fuel lines around various components. Aluminum tubing's flexibility allows it to navigate these obstacles effortlessly. It can easily conform to the shape of the engine bay, providing a clean and efficient layout. This not only improves the overall aesthetics of the vehicle but also ensures that the fuel lines are protected from potential damage caused by sharp bends or tight turns.
Furthermore, the flexibility of aluminum tubing contributes to the long-term reliability of the fuel system. Over time, fuel lines may experience vibrations and movements due to engine operation. With aluminum tubing, these movements can be absorbed, reducing the risk of fuel leaks or damage to the fuel lines. This flexibility is especially important in high-performance vehicles or those with rough terrain capabilities, where fuel lines are subjected to more demanding conditions.
Buick Rendezvous Fuel Line Sizing: A Comprehensive Guide
You may want to see also
Weight: Lighter than steel, aluminum tubing reduces vehicle weight and fuel consumption
The use of aluminum tubing in vehicles, particularly for fuel lines, offers a significant advantage in terms of weight reduction. Aluminum is a lightweight metal, approximately one-third the density of steel, which means it can drastically reduce the overall weight of a vehicle. This is a crucial factor in modern automotive design, as vehicle weight directly impacts fuel efficiency and performance.
When it comes to fuel lines, aluminum tubing is an excellent choice. The primary function of fuel lines is to transport fuel from the tank to the engine, and any weight reduction in this system can lead to improved fuel economy. Lighter fuel lines mean less strain on the engine, allowing for more efficient combustion and, consequently, better fuel efficiency. This is especially important in high-performance vehicles or those with limited engine power, where every pound saved can make a noticeable difference in acceleration and overall driving experience.
The benefits of using aluminum tubing for fuel lines are twofold. Firstly, the reduced weight of the tubing itself contributes to the overall weight loss of the vehicle. Secondly, aluminum's natural corrosion resistance and ability to withstand high temperatures make it a durable material for fuel lines. This ensures that the tubing can handle the demands of fuel transport without compromising on safety or performance.
Incorporating aluminum tubing into fuel line design is a strategic move for manufacturers. It allows them to meet the growing demand for fuel-efficient vehicles without sacrificing performance. The use of lightweight materials is a key trend in the automotive industry, and aluminum tubing plays a vital role in achieving these goals. By reducing the weight of fuel lines, manufacturers can contribute to a more sustainable and environmentally friendly approach to vehicle design.
In summary, aluminum tubing's lightweight nature makes it an ideal choice for fuel lines, offering a practical solution to enhance vehicle performance and fuel efficiency. This simple yet effective approach to material selection demonstrates how innovative design can lead to significant improvements in modern automobiles.
Diesel Fuel Line Bio Removal: Tips and Tricks
You may want to see also
Cost: Aluminum tubing is generally more affordable than other materials, making it a cost-effective option
Aluminum tubing offers a cost-effective solution for fuel lines, especially when compared to other materials like stainless steel or brass. The affordability of aluminum is a significant advantage, especially for those on a budget or working on projects with limited financial resources. This material is readily available and often comes at a lower price point, making it an attractive option for fuel line applications.
The cost-effectiveness of aluminum tubing is a result of its abundance and the efficiency of its production process. Aluminum is a widely produced metal, and its availability in the market keeps the prices relatively stable and low. Manufacturers can produce aluminum tubing at a lower cost, which is then reflected in the final price for consumers. This affordability factor allows for more flexibility in project planning and budgeting, as it is a more economical choice without compromising on quality.
When considering fuel lines, the cost of materials can be a critical factor, especially for large-scale projects or applications requiring extensive tubing. Aluminum tubing provides a viable alternative to more expensive materials, ensuring that the overall project remains within budget constraints. This is particularly beneficial for DIY enthusiasts, hobbyists, and professionals who require a cost-efficient solution without sacrificing performance.
Furthermore, the affordability of aluminum tubing does not mean a compromise on its quality. This material is known for its durability and corrosion resistance, making it suitable for fuel line applications. It can withstand the challenges of fuel transport, including exposure to heat, chemicals, and varying environmental conditions. Despite its cost-effectiveness, aluminum tubing offers the necessary strength and reliability required for safe and efficient fuel line systems.
In summary, aluminum tubing's affordability is a key advantage, making it a cost-effective choice for fuel lines. Its availability, production efficiency, and competitive pricing ensure that projects can stay within budget while still benefiting from a durable and reliable material. This makes aluminum tubing an excellent option for those seeking a balance between cost and performance in their fuel line installations.
Fuel Shopping: State Line Laws and Legalities
You may want to see also
Frequently asked questions
Yes, aluminum tubing can be used for fuel lines, but it requires careful consideration. Aluminum is lightweight and offers good thermal conductivity, which can be beneficial for fuel systems. However, it is important to choose the right type of aluminum alloy and ensure proper installation to prevent leaks and corrosion.
Aluminum tubing is often preferred for fuel lines due to its corrosion resistance, especially in marine or outdoor applications. It is also relatively easy to work with and can be joined using various methods like soldering, welding, or compression fittings. Additionally, aluminum's thermal properties can help regulate fuel temperature, which is crucial for performance and longevity.
Absolutely! When using aluminum tubing, it is essential to select a suitable alloy, such as 6061 or 3003, which offers good strength and corrosion resistance. The tubing should be properly lubricated to facilitate installation and prevent damage to the fuel line. Regular inspections and maintenance are recommended to ensure the integrity of the fuel system, especially in high-pressure applications.