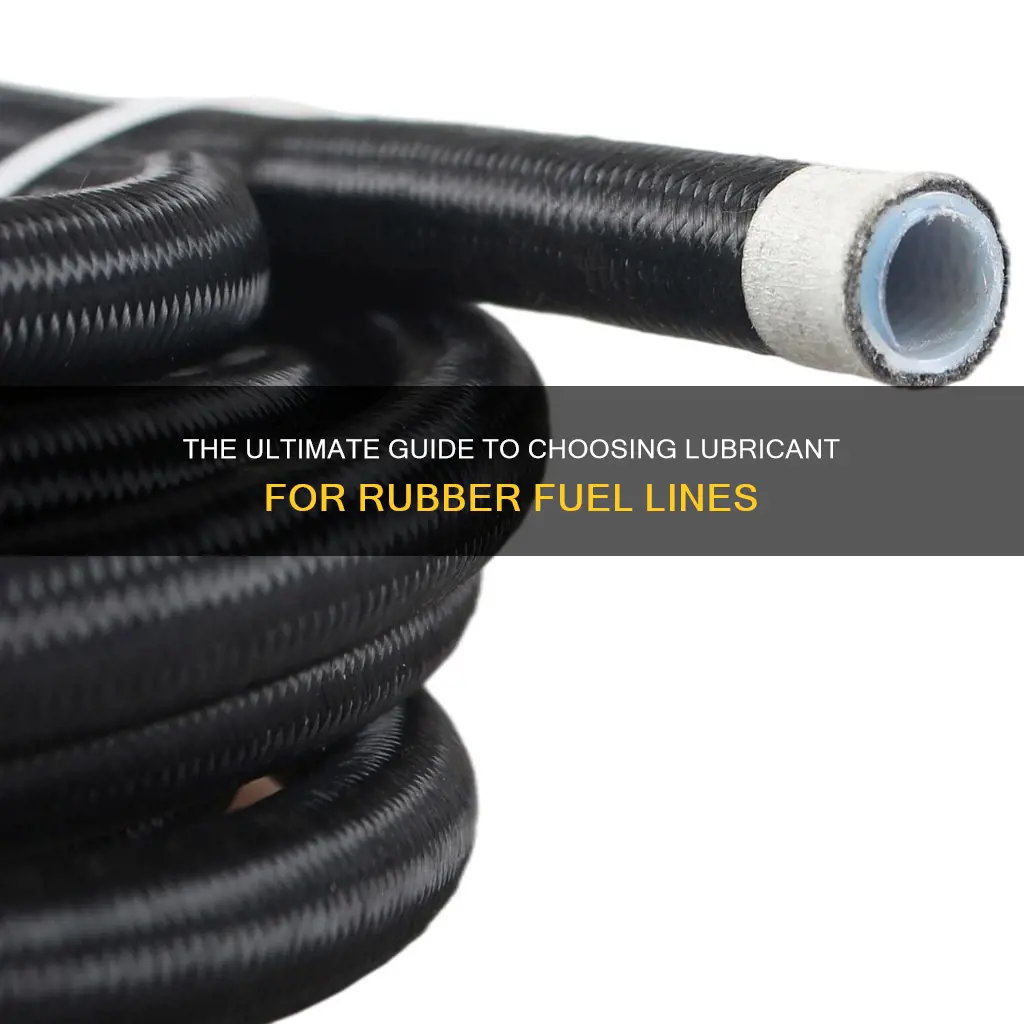
When installing a rubber fuel line, it's crucial to use the right lubricant to ensure a secure and leak-free connection. The choice of lube can significantly impact the installation process and the long-term performance of the fuel line. This guide will explore the various lubricants available and their suitability for this task, helping you make an informed decision to ensure a successful and safe installation.
What You'll Learn
- Material Compatibility: Ensure the lube is compatible with rubber and fuel to prevent degradation
- Consistency: Choose a lube with the right viscosity for easy application and no leakage
- Temperature Tolerance: Select a lube that performs well in both hot and cold conditions
- Environmental Impact: Opt for eco-friendly lubricants to minimize environmental harm
- Application Technique: Follow specific methods for best results, avoiding over-lubrication
Material Compatibility: Ensure the lube is compatible with rubber and fuel to prevent degradation
When it comes to maintaining a rubber fuel line, choosing the right lubricant is crucial to ensure the longevity and functionality of the fuel system. One of the primary considerations is material compatibility, especially when dealing with rubber components. Rubber is a versatile material used extensively in fuel lines due to its flexibility and durability. However, it is sensitive to certain chemicals, and using the wrong lubricant can lead to degradation, cracking, or even failure of the rubber fuel line.
The compatibility of lubricants with rubber is essential because some substances can cause the rubber to become brittle, soft, or discolored over time. This degradation can result in fuel leaks, reduced performance, and potential safety hazards. Therefore, it is imperative to select a lubricant that is specifically formulated to be compatible with rubber and fuel. Look for lubricants that are designed for fuel system applications and are known to withstand the corrosive effects of gasoline, diesel, or other fuels.
A suitable lubricant should be able to provide a protective barrier between the rubber and the fuel, preventing direct contact and potential chemical reactions. This is particularly important in fuel lines, as they are constantly exposed to the corrosive nature of fuels. The lubricant should also have a stable chemical composition that does not break down or react with the rubber over time.
To ensure compatibility, consider the following: check the manufacturer's guidelines for your specific fuel line material. Some rubber types, like natural rubber or butyl rubber, may require different lubricants compared to synthetic rubbers. Additionally, the fuel type is a critical factor. Gasoline-based fuels may require different lubricants than diesel or aviation fuels. Always opt for lubricants recommended by the fuel line manufacturer or industry experts to guarantee the best results.
In summary, when lubricating a rubber fuel line, prioritize material compatibility to prevent degradation. Choose lubricants specifically designed for fuel system applications, ensuring they are compatible with both the rubber and the type of fuel used. This approach will help maintain the integrity of the fuel line, ensuring optimal performance and safety. Remember, the right lubricant can make a significant difference in the longevity of your fuel system components.
Unveiling the Secrets: Corvette Fuel Line Sizing, 1969 Edition
You may want to see also
Consistency: Choose a lube with the right viscosity for easy application and no leakage
When it comes to choosing the right lubricant for your rubber fuel line, consistency in viscosity is key. The lube you select should have a consistency that allows for easy application without any leakage or mess. This is especially important when working with fuel lines, as any excess lube can lead to potential issues.
The ideal lube should be thin enough to easily flow into the fuel line, ensuring complete coverage of the rubber surface. A common mistake is using a lube that is too thick, which can make it difficult to apply and may result in clumping or uneven distribution. On the other hand, a lube that is too thin might not provide the necessary protection and could lead to leakage.
To determine the right viscosity, consider the temperature and environmental conditions. Colder temperatures may require a thicker lube to maintain its consistency, while warmer temperatures might call for a thinner option. It's essential to choose a lube that remains stable and easy to work with across a range of temperatures to ensure optimal performance.
A good rule of thumb is to select a lube that is specifically designed for fuel lines or rubber components. These lubricants are formulated to have a consistent viscosity, ensuring they remain effective in various conditions. They are typically thin and easy to apply, allowing for a smooth and efficient process when installing or replacing fuel lines.
Additionally, consider the duration of the lube's effectiveness. Some lubricants may require frequent reapplication, especially in high-temperature environments. Choosing a lube with a longer-lasting consistency can save time and effort, ensuring your fuel line remains protected without the need for constant re-lubrication.
1956 Chevy Fuel Line: Size Matters for Performance
You may want to see also
Temperature Tolerance: Select a lube that performs well in both hot and cold conditions
When it comes to choosing the right lubricant for your rubber fuel line, temperature tolerance is a critical factor to consider. Rubber is a material that can be sensitive to extreme temperatures, and using a lube that doesn't perform well in both hot and cold conditions can lead to issues. Here's a detailed guide on how to select a lubricant that will ensure your fuel line functions optimally in various temperature environments:
Understanding Temperature Tolerance: Temperature tolerance refers to a lubricant's ability to maintain its properties and performance across a wide range of temperatures. Rubber fuel lines are often exposed to varying conditions, from the engine's high-temperature environment to cold outdoor temperatures. A lube with excellent temperature tolerance will remain effective and stable, ensuring the fuel line's integrity and functionality.
Hot Conditions: In high-temperature environments, such as those found near an engine, the lube should remain stable and not break down. It should resist thermal degradation, which can cause the lubricant to become thin and lose its protective properties. Look for lubricants designed for high-temperature applications, often containing synthetic base oils and additives that provide thermal stability. These lubricants will ensure that the fuel line remains protected even when operating at maximum engine power.
Cold Conditions: Conversely, in cold temperatures, the lube should remain viscous and not become too thin, which could lead to fuel leakage or reduced performance. Cold-weather lubricants are formulated to maintain their consistency, providing a reliable seal between the fuel line and the rubber material. These lubricants often contain special additives that prevent the oil from freezing or becoming too runny.
Multi-Purpose Lubricants: For optimal performance, consider using a multi-purpose lube that excels in both hot and cold conditions. These lubricants are engineered to provide consistent protection across a wide temperature range. They are ideal for applications where the fuel line may be exposed to varying temperatures, such as in different climates or during seasonal changes. Look for products specifically designed for rubber fuel lines, as they will have the necessary additives to ensure long-lasting performance.
Testing and Compatibility: Always test any new lubricant on a small section of the fuel line before applying it to the entire assembly. This ensures compatibility and helps identify any potential issues. Additionally, check the manufacturer's guidelines for temperature recommendations to ensure you select a lube that meets or exceeds their specifications.
By choosing a lubricant with excellent temperature tolerance, you can ensure that your rubber fuel line remains protected and functions efficiently, regardless of the environmental conditions it encounters. This will contribute to the overall reliability and longevity of your fuel system.
Understanding Fuel Line Hose Clamp Sizes: A Comprehensive Guide
You may want to see also
Environmental Impact: Opt for eco-friendly lubricants to minimize environmental harm
The choice of lubricant when working with rubber fuel lines is crucial, especially from an environmental perspective. Traditional lubricants can have detrimental effects on the ecosystem, so it's essential to opt for eco-friendly alternatives. Here's a detailed guide on why and how to choose environmentally conscious lubricants:
Understanding the Environmental Concerns:
When using lubricants, especially those containing petroleum-based chemicals, there is a risk of environmental contamination. These chemicals can leach into the soil and water sources, posing a significant threat to local ecosystems and wildlife. Additionally, the production and disposal of such lubricants contribute to air pollution and can have long-lasting effects on the environment. It is imperative to address these concerns by adopting more sustainable practices.
Eco-Friendly Lubricant Options:
- Biodegradable Lubricants: Look for lubricants specifically designed to be biodegradable. These products are formulated with natural, plant-based ingredients that break down safely over time. Biodegradable lubricants are less harmful to the environment and can be safely disposed of or recycled.
- Synthetic Eco-Friendly Lubricants: Modern technology offers synthetic lubricants made from renewable resources. These lubricants are designed to provide excellent performance while minimizing environmental impact. They often contain bio-based additives, ensuring they are less toxic and more sustainable.
- Water-Based Lubricants: Water-based lubricants are an excellent choice for their low environmental impact. These lubricants are typically non-toxic and can be safely used around water sources without causing ecological damage.
Minimizing Environmental Harm:
When applying lubricants to rubber fuel lines, consider the following:
- Use the Right Amount: Apply only the required amount of lubricant to avoid wastage and potential environmental contamination.
- Proper Disposal: Always dispose of used lubricants responsibly. Check local regulations for guidelines on recycling or disposing of eco-friendly lubricants.
- Choose Sustainable Brands: Support manufacturers who prioritize sustainability. Many companies now offer eco-friendly lubricant options, ensuring a greener approach to maintenance.
By making informed choices and selecting environmentally conscious lubricants, you contribute to a more sustainable future. This approach not only protects the environment but also ensures that your work practices align with eco-friendly standards, making it a responsible and ethical decision. Remember, small changes in lubricant selection can lead to significant environmental benefits.
Choosing the Right Hose for Your 1.4-Inch Fuel Line
You may want to see also
Application Technique: Follow specific methods for best results, avoiding over-lubrication
When working with rubber fuel lines, it's crucial to use the right lubricant to ensure a smooth and secure installation. The goal is to create a thin, even layer of lube that facilitates the insertion of the fuel line without causing damage or reducing its lifespan. Over-lubrication can lead to issues such as excess material that may interfere with the line's function or cause it to become difficult to handle. Therefore, precision and a methodical approach are key.
Start by cleaning the area where the fuel line will be installed. Remove any dirt, debris, or old lubricant to ensure a clean surface. This step is essential as any contaminants can affect the bonding and performance of the fuel line. Use a mild detergent or isopropyl alcohol to clean the area, ensuring it is completely dry before proceeding.
The next step is to choose the appropriate lubricant. Silicone-based lubricants are often recommended for rubber fuel lines due to their compatibility and ability to provide a smooth, even coating. Apply a small amount of lubricant to the end of the fuel line, ensuring it is evenly distributed. Too much lube at this stage can be problematic, so a light, consistent application is ideal.
Now, carefully insert the fuel line into the designated port, ensuring it is aligned correctly. As you push the line in, maintain a steady pace to avoid any sudden movements that could cause over-lubrication. The goal is to create a seamless connection without any excess lube protruding from the line. Once fully inserted, wipe away any excess lubricant to prevent it from causing issues during the installation process.
Finally, allow the fuel line to set according to the manufacturer's instructions. This may involve waiting for a specified period to ensure the lubricant is fully integrated and the line is secure. By following these steps, you can ensure a successful installation that maximizes the performance and longevity of your rubber fuel line. Precision and attention to detail are vital to achieving the best results.
Unraveling the Mystery: What's the Deal with Fuel Line Sensors?
You may want to see also
Frequently asked questions
When working with rubber fuel lines, it's important to use a lubricant that is compatible with the material to avoid damage. A suitable option is a high-quality silicone-based grease or a specialized rubber installation compound. These lubricants provide a smooth and even coating, making it easier to slide the fuel line into place without causing any tears or permanent deformation.
While petroleum jelly is a common household item, it is not recommended for lubricating rubber fuel lines. Jelly can leave a sticky residue, which may attract dirt and debris, leading to potential blockages. Additionally, it can make the rubber more susceptible to damage over time. It's best to opt for a dedicated lubricant designed for rubber applications.
The amount of lubricant required depends on the size of the fuel line and the specific application. As a general guideline, a thin, even layer of lubricant should be applied along the length of the fuel line, ensuring that it covers the entire surface. Too much lubricant can lead to excess material getting into the fuel system, which may cause issues. A light coating that facilitates smooth installation is usually sufficient.