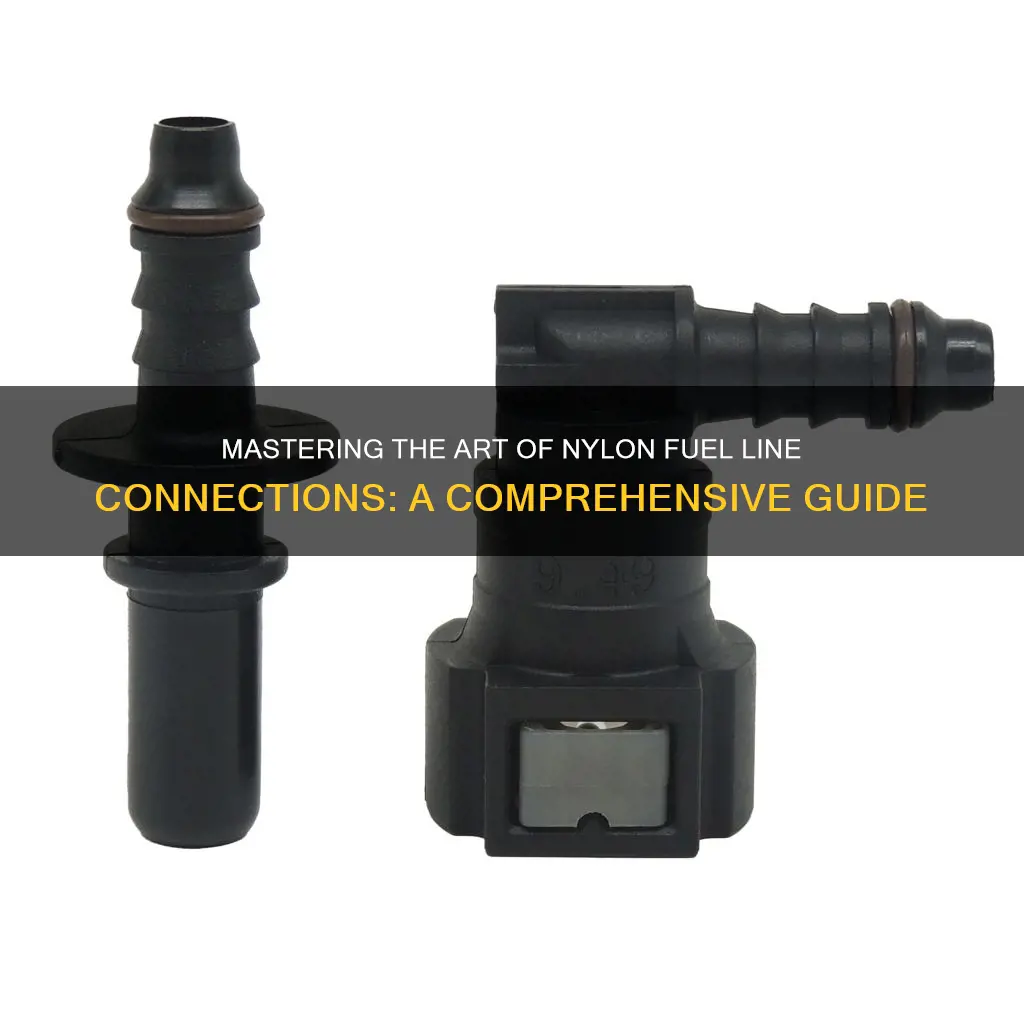
Nylon fuel lines are a popular choice for fuel delivery systems due to their flexibility, durability, and resistance to fuel-related chemicals. Connecting these lines requires careful attention to ensure a secure and leak-free installation. This guide will provide a step-by-step process for connecting nylon fuel lines, covering essential tools, preparation, and techniques to achieve a reliable and safe fuel system.
What You'll Learn
- Prepare Tools: Gather necessary tools: wrench, fuel line connectors, and cleaning supplies
- Inspect Fuel Line: Check for damage, cracks, or leaks before connecting
- Clean Connections: Ensure all connections are free of debris and old fuel residue
- Connect Fuel Line: Tighten connectors securely, following manufacturer's instructions
- Test for Leaks: After connecting, start engine and check for any fuel leaks
Prepare Tools: Gather necessary tools: wrench, fuel line connectors, and cleaning supplies
Before you begin the process of connecting a nylon fuel line, it's crucial to ensure you have the right tools and materials ready. This preparation will make the task more efficient and less prone to errors. Here's a step-by-step guide on gathering the necessary tools:
Wrench: A wrench is an essential tool for any fuel line installation or repair. You'll need a wrench that fits the size of the fuel line you are working with. Common sizes include 1/4-inch, 3/8-inch, and 1/2-inch. Ensure you have a adjustable wrench or a set of wrenches that can accommodate these sizes. Wrenches are used to tighten and secure the fuel line connectors, ensuring a proper seal.
Fuel Line Connectors: These connectors are specifically designed to join fuel lines together. Look for nylon fuel line connectors that match the diameter of your fuel line. Common types include quick-connect fittings, push-to-connect fittings, and clamp-style connectors. Having a variety of connector types can be beneficial, as different applications may require specific connector styles.
Cleaning Supplies: Cleaning is an often-overlooked but crucial step in the process. You'll need a few cleaning supplies to ensure a smooth and effective connection. This includes a fuel line cleaner or a suitable solvent to remove any contaminants. Additionally, have some rags or cleaning cloths ready to wipe down the fuel lines and connectors, ensuring a clean and dry surface before assembly.
Having these tools and supplies prepared will make the connection process much smoother. It's always a good practice to double-check your tools before starting any project to avoid any last-minute complications. With the right tools in hand, you'll be well-equipped to handle the installation or repair of your nylon fuel line.
Mastering Fuel Line Disconnects: A Step-by-Step Guide
You may want to see also
Inspect Fuel Line: Check for damage, cracks, or leaks before connecting
Before attempting to connect any fuel line, it is crucial to inspect the existing fuel line for any signs of damage, cracks, or leaks. This step is essential to ensure the safety and proper functioning of your vehicle's fuel system. Here's a detailed guide on how to inspect the fuel line:
Start by visually examining the fuel line for any visible damage. Look for tears, punctures, or any signs of wear and tear. Check for any bends or kinks that might have occurred during installation or previous repairs. Pay close attention to the areas where the fuel line connects to the fuel tank, engine, and other components. Even small cracks or small holes can lead to significant issues if left unattended. Inspect the fuel line's flexibility and ensure it can move without excessive rigidity.
Next, check for any signs of corrosion or deterioration. Over time, fuel lines can develop rust or become brittle due to exposure to fuel and engine heat. Look for any discolored or softened areas along the length of the line. If you notice any corrosion, it may indicate a more serious issue, and the fuel line might need to be replaced.
The most critical aspect of this inspection is to look for leaks. Turn on the fuel pump and listen for any hissing or bubbling sounds, which could indicate a leak. You can also use a soapy water solution to test for leaks. Apply the solution to the fuel line and look for any bubbles forming, which would signify a leak. Leaks can lead to fuel wastage, engine performance issues, and potential safety hazards.
If you find any damage, cracks, or leaks during the inspection, it is strongly recommended to replace the fuel line. Attempting to connect a damaged line can lead to further complications and potential safety risks. Always ensure that you have the necessary tools and knowledge before starting any fuel line work, and if in doubt, consult a professional mechanic.
Aluminum Fuel Lines: Pros and Cons for Fuel Injection Systems
You may want to see also
Clean Connections: Ensure all connections are free of debris and old fuel residue
When working with nylon fuel lines, ensuring clean connections is crucial for optimal performance and safety. Here's a step-by-step guide to achieving this:
Prepare the Components: Before making any connections, inspect the nylon fuel lines, fittings, and connectors. Look for any signs of damage, cracks, or wear. Ensure that all parts are in good condition and suitable for use. It is essential to start with clean and undamaged materials to avoid introducing contaminants during the connection process.
Debris Removal: Start by removing any debris or old fuel residue from the connection points. This step is critical to prevent blockages and ensure a tight seal. Use a soft-bristled brush or a small air hose to gently clean the interior of the fuel line and the threads of the fittings. Pay close attention to any bends or elbows in the line, as debris can accumulate in these areas.
Cleaning Agent: For stubborn residue or old fuel buildup, consider using a mild cleaning agent specifically designed for fuel lines. These agents can help dissolve and remove any remaining contaminants. Follow the manufacturer's instructions for application and ensure proper ventilation in the work area. After cleaning, rinse the fuel line thoroughly to eliminate any cleaning agent residue.
Tighten Connections Securely: Once the connections are clean, proceed with the assembly. Ensure that all fittings are tightened securely but carefully to avoid over-tightening, which can damage the nylon fuel line. Use the appropriate tools for tightening, such as wrenches or torque wrenches, to achieve the recommended torque specifications. A secure connection will prevent leaks and ensure the integrity of the fuel system.
Final Inspection: After completing the connections, perform a final inspection to verify the quality of the work. Check for any signs of leaks around the fittings and ensure that all connections are tight and secure. Look for any visible damage or contamination that may have occurred during the cleaning process. If everything appears satisfactory, your nylon fuel line connections are ready for use.
Remember, taking the time to clean and properly connect fuel lines is essential for maintaining a reliable and safe fuel system. Regular maintenance and attention to detail will contribute to the overall performance and longevity of your vehicle's fuel infrastructure.
Understanding Truck Fuel Lines: A Comprehensive Guide to Different Types
You may want to see also
Connect Fuel Line: Tighten connectors securely, following manufacturer's instructions
When connecting a nylon fuel line, ensuring a secure and tight fit is crucial to prevent leaks and maintain the integrity of your fuel system. Here's a step-by-step guide to help you achieve a proper connection:
Start by preparing the fuel line and connectors. Clean the ends of the fuel line and the connectors to remove any dirt, debris, or old fuel residue. This step is essential to ensure a clean and reliable connection. Use a suitable cleaner and a soft cloth or brush to wipe down the surfaces, ensuring no contaminants remain.
Next, align the fuel line with the connector, ensuring it fits snugly. The key to a successful connection is precision. Make sure the fuel line is straight and properly positioned within the connector. Check the manufacturer's specifications or diagrams for guidance on the correct orientation.
Now, it's time to tighten the connector. Use the appropriate tool, typically a fuel line crimping tool or a wrench, to secure the connection. Follow the manufacturer's instructions for the correct torque specifications. Over-tightening can damage the fuel line, while under-tightening may result in a weak connection. Aim for a firm, yet gentle, grip to achieve the desired tightness.
After tightening, inspect the connection for any signs of leakage. Apply a small amount of fuel or a suitable sealant to the joint and observe if any fuel seeps through. If there are no leaks, your connection is secure. However, if any issues arise, recheck the alignment and tightening process, ensuring you haven't missed any steps or adjustments needed for a perfect fit.
Remember, each fuel line and connector may have specific requirements, so always refer to the manufacturer's guidelines. Following these instructions will help you establish a reliable and safe fuel line connection.
Dual Vacuum Lines: Jeep Fuel Pump Connection Guide
You may want to see also
Test for Leaks: After connecting, start engine and check for any fuel leaks
After successfully connecting the nylon fuel line, it is crucial to conduct a thorough test to ensure there are no leaks. This step is essential to prevent potential issues and maintain the integrity of your fuel system. Here's a detailed guide on how to perform this test:
Step 1: Engine Preparation: Before starting the engine, ensure it has been properly cooled down, especially if it has been running recently. This is important to avoid any potential hazards caused by hot engine components. Additionally, make sure the fuel cap is tightly closed to prevent any fuel evaporation during the test.
Step 2: Visual Inspection: Begin by visually inspecting the entire fuel system, including the nylon fuel line, for any visible signs of damage or disconnection. Look for any cracks, tears, or bends in the line, as these could indicate potential leak points. Check all connections, including the fuel pump, injectors, and the fuel tank, to ensure they are secure and properly seated.
Step 3: Fuel System Pressure Test: To further ensure the integrity of the fuel line, you can perform a pressure test. This can be done using a fuel pressure gauge or a hand pump. Start the engine and allow it to idle. Connect the gauge to the fuel rail or injectors and measure the pressure. The reading should be within the manufacturer's specified range. If the pressure is too low, it may indicate a restriction or leak in the system.
Step 4: Leak Detection: The most critical part of the test is to check for fuel leaks. Turn the engine on and listen carefully for any hissing or bubbling sounds around the connections and joints of the fuel line. You can also use a soapy water solution and apply it to the fuel line connections to create a visual indicator of leaks. If bubbles appear, it confirms a leak. Additionally, check for any fuel accumulation or stains around the engine bay, as these could indicate a hidden leak.
Step 5: Addressing Leaks: If any leaks are detected, it is imperative to address them immediately. Tighten loose connections, replace damaged sections of the fuel line, or repair any faulty components. Ensure all fuel system components are properly sealed and secured to prevent further leaks.
By following these steps, you can effectively test for leaks after connecting the nylon fuel line, ensuring a safe and efficient fuel system. Regular maintenance and inspections are key to preventing potential fuel-related issues.
Fuel Line Removal: A Guide to Draining Gas Safely
You may want to see also
Frequently asked questions
Connecting a nylon fuel line to a fuel tank requires a few steps to ensure a secure and leak-free installation. First, ensure you have the correct size of fuel line and fittings. Then, prepare the fuel line by cleaning it and removing any debris or old fuel line material. Use a fuel line primer on the inner surface of the line and the fitting to create a bond. Apply a thin layer of fuel line adhesive or tape around the fitting, then insert the fuel line into the fitting, pushing it in until it is snug. Finally, use fuel line connectors or clamps to secure the connection.
Achieving a tight seal is crucial to prevent fuel leaks. Start by ensuring the fuel line and fitting are clean and free of any contaminants. Apply a small amount of fuel line compound or tape around the fitting, then insert the fuel line, pushing it firmly into the fitting. Use a fuel line clamp or connector to secure the connection, tightening it by hand first, then using a wrench to ensure a snug fit. Avoid over-tightening to prevent damage to the fuel line.
Yes, you can use heat to facilitate the connection of nylon fuel lines, but it should be done with caution. Heat can help create a stronger bond and make the connection process easier. Apply heat to the fuel line and fitting, ensuring an even temperature distribution. Use a heat shrink sleeve or tape to cover the connection, then insert the fuel line into the fitting. Once connected, allow the assembly to cool, and the heat will create a secure bond. Always monitor the temperature to avoid overheating the fuel line.