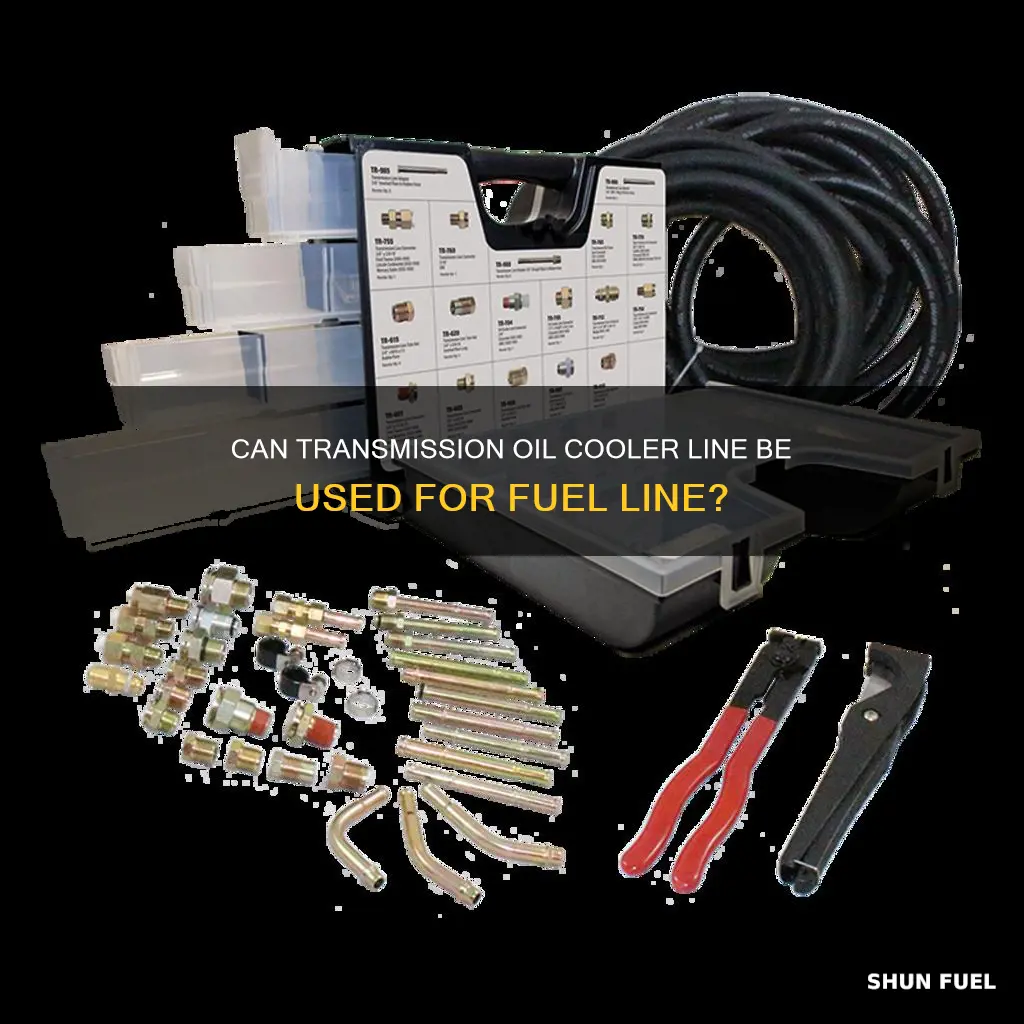
The automotive world often encounters unique challenges, and one such scenario involves the repurposing of transmission oil cooler lines for fuel lines. While it might seem unconventional, this practice can be a practical solution for certain vehicles, especially those with specific performance requirements or unique engine configurations. By utilizing transmission oil cooler lines, which are designed to dissipate heat from the transmission fluid, as fuel lines, enthusiasts and mechanics can optimize fuel flow and temperature management. This innovative approach not only showcases the adaptability of automotive components but also highlights the creativity required to tailor solutions to individual vehicle needs.
What You'll Learn
- Cooling System: The transmission oil cooler line is designed to cool the transmission fluid, not fuel
- Fuel Lines: Fuel lines are typically made of rubber or plastic and carry fuel from the tank to the engine
- Material Differences: Transmission oil cooler lines are often made of steel or aluminum, while fuel lines are made of rubber or plastic
- Pressure Considerations: Fuel lines must withstand high pressure, unlike transmission oil cooler lines
- System Compatibility: Using a transmission oil cooler line for a fuel line can lead to system incompatibility issues
Cooling System: The transmission oil cooler line is designed to cool the transmission fluid, not fuel
The transmission oil cooler line is a crucial component of a vehicle's cooling system, specifically designed to manage the temperature of the transmission fluid. It plays a vital role in maintaining the optimal performance and longevity of the transmission by preventing overheating and ensuring efficient operation. This specialized cooler line is not intended for use with fuel, as the two fluids have distinct properties and functions within the vehicle.
In the context of the cooling system, the transmission oil cooler line is typically located near the engine, often integrated into the radiator or positioned alongside it. Its primary function is to transfer excess heat from the transmission fluid to the surrounding air, thus regulating the fluid's temperature. This is essential because transmission fluid operates at high temperatures, and excessive heat can lead to fluid degradation, reduced performance, and potential damage to the transmission components.
It is important to understand that the transmission oil cooler line is specifically engineered to handle the unique challenges posed by transmission fluid. This fluid is designed to lubricate and protect the transmission's moving parts, and its temperature must be carefully controlled to ensure optimal performance. Using a transmission oil cooler line for fuel cooling would be incorrect and potentially harmful, as fuel has different cooling requirements and properties compared to transmission fluid.
When it comes to fuel cooling, a separate system is typically employed, often consisting of a fuel cooler or a cooler line dedicated to the fuel system. This ensures that the fuel remains at the appropriate temperature for efficient combustion in the engine. Mixing the transmission oil cooler line with fuel cooling would be a mistake, as it could lead to improper cooling of the fuel, potentially causing engine performance issues.
In summary, the transmission oil cooler line is a specialized component that serves a critical function in the cooling system, specifically for transmission fluid. It is not meant for fuel cooling, and using it for that purpose would be incorrect and potentially detrimental to the vehicle's performance. Understanding the differences between transmission fluid and fuel is essential for maintaining the proper functioning of a vehicle's cooling system.
PTFE Tape: A Reliable Seal for Automotive Fuel Lines?
You may want to see also
Fuel Lines: Fuel lines are typically made of rubber or plastic and carry fuel from the tank to the engine
Fuel lines are an essential component of any vehicle's fuel system, playing a critical role in ensuring that the engine receives the necessary fuel for operation. These lines are typically constructed from materials such as rubber or plastic, chosen for their flexibility and durability to withstand the rigors of the automotive environment. The primary function of fuel lines is to transport fuel from the fuel tank to the engine, where it is injected into the combustion chamber to power the vehicle. This process requires a precise and controlled flow of fuel, and the fuel lines are designed to maintain this flow under various operating conditions.
The construction of fuel lines involves careful consideration of the materials used. Rubber is a common choice due to its inherent flexibility, which allows the lines to accommodate the natural movement and vibrations within the vehicle's engine bay. This flexibility is crucial to prevent damage to the fuel lines during engine operation and when the vehicle is in motion. Additionally, rubber fuel lines are resistant to fuel degradation, ensuring that the fuel remains stable and of high quality throughout its journey from the tank to the engine.
Plastic fuel lines, while less common, offer advantages such as reduced weight and increased resistance to corrosion. Plastic is often used in high-temperature environments or where flexibility is not as critical, as it can be more rigid than rubber. However, plastic fuel lines may require more frequent inspection and maintenance due to their potential for cracking or becoming brittle over time.
The design of fuel lines also includes various fittings and connectors to ensure a secure and leak-free connection. These fittings are often made of metal or a durable plastic material to withstand the pressure and temperature changes that occur during engine operation. Proper installation and regular maintenance of these connections are essential to prevent fuel leaks, which can lead to engine misfires, reduced performance, and potential safety hazards.
In summary, fuel lines are a vital part of a vehicle's fuel system, responsible for delivering fuel from the tank to the engine with precision and reliability. The choice of materials, such as rubber or plastic, is crucial to ensure flexibility, durability, and resistance to fuel degradation. Proper installation and maintenance of fuel lines are essential to guarantee safe and efficient engine operation.
Mastering Your Engine's Performance: A Guide to Using Protec Fuel Line Cleaner
You may want to see also
Material Differences: Transmission oil cooler lines are often made of steel or aluminum, while fuel lines are made of rubber or plastic
The materials used for transmission oil cooler lines and fuel lines are distinct and carefully chosen to suit their respective functions. Transmission oil cooler lines, which are an essential component in managing the temperature of the transmission fluid, are typically constructed from steel or aluminum. These materials offer several advantages. Steel, known for its strength and durability, provides excellent resistance to heat and pressure, ensuring the line can withstand the demanding conditions within the transmission system. Aluminum, on the other hand, is valued for its lightweight properties, which help reduce the overall weight of the vehicle, thus improving fuel efficiency. The choice of steel or aluminum for these lines is crucial to maintaining the performance and longevity of the transmission.
In contrast, fuel lines have a different set of requirements and are therefore made from rubber or plastic. Rubber is a common material for fuel lines due to its flexibility, which allows it to accommodate the natural movement and expansion of the fuel system. This flexibility is essential to prevent cracks and leaks, ensuring the fuel remains contained and safely transported to the engine. Plastic, often in the form of high-density polyethylene (HDPE) or polyvinyl chloride (PVC), is another popular choice for fuel lines. These plastics offer excellent chemical resistance, preventing fuel degradation and ensuring the fuel's quality remains intact. The use of rubber or plastic in fuel lines is critical to maintaining the vehicle's performance and safety, as it directly impacts the efficiency of fuel delivery.
The material differences between these two types of lines are significant and directly relate to their respective functions. Transmission oil cooler lines, with their steel or aluminum construction, are designed to handle high temperatures and pressures, ensuring the transmission operates optimally. Meanwhile, fuel lines, made from rubber or plastic, provide the necessary flexibility and chemical resistance to safely convey fuel to the engine. These distinct material choices are a testament to the precision and engineering required in automotive design, where each component plays a vital role in the overall performance and safety of the vehicle.
Understanding these material differences is essential for anyone working on vehicle maintenance or repairs. When replacing or upgrading these lines, it is crucial to choose the correct material to ensure compatibility and optimal performance. For instance, using steel for fuel lines or rubber for transmission oil cooler lines could lead to performance issues and potential safety hazards. Therefore, a thorough understanding of these material choices is key to successful vehicle maintenance.
In summary, the materials used in transmission oil cooler lines and fuel lines are carefully selected to meet the specific demands of their respective functions. Steel and aluminum provide strength and heat resistance for transmission lines, while rubber and plastic offer flexibility and chemical resistance for fuel lines. Recognizing these material differences is essential for maintaining vehicle performance and safety, ensuring that each component functions as intended.
Fuel Return Line: Uncovering the Mystery of the 2000 Model
You may want to see also
Pressure Considerations: Fuel lines must withstand high pressure, unlike transmission oil cooler lines
The primary distinction between fuel lines and transmission oil cooler lines lies in their respective functions and the pressures they encounter. Fuel lines are designed to transport fuel from the tank to the engine, a process that involves high-pressure fuel, often ranging from 50 to 100 psi (pounds per square inch) or even higher in some performance vehicles. This high pressure is necessary to ensure efficient fuel atomization and proper engine operation. In contrast, transmission oil cooler lines are responsible for managing the temperature of transmission fluid, which operates at much lower pressures, typically around 10 to 20 psi.
The pressure requirements for fuel lines are critical to engine performance and safety. If a fuel line cannot withstand the high pressure, it may fail, leading to potential engine misfires, reduced power, or even dangerous fuel leaks. Modern fuel lines are typically made from high-strength materials like steel or braided stainless steel to handle these pressures effectively. These materials are carefully selected to ensure flexibility, durability, and resistance to fuel degradation over time.
In contrast, transmission oil cooler lines face different challenges. While they do not experience the same extreme pressures as fuel lines, they must still maintain the temperature of the transmission fluid, which is crucial for optimal gear shifting and drivability. The pressure in these lines is relatively low, and the primary concern is often the efficient transfer of heat rather than withstanding high pressure.
The design and construction of fuel lines and transmission oil cooler lines reflect these pressure considerations. Fuel lines are often thicker-walled and more rigid to handle the high pressure, while transmission oil cooler lines may be thinner and more flexible to accommodate the lower pressure and the need for efficient heat transfer. Additionally, fuel lines often feature protective coatings or shielding to prevent damage from fuel contaminants or heat, whereas transmission oil cooler lines might focus on heat dissipation materials.
Understanding these pressure considerations is essential for mechanics and engineers when selecting or designing fuel lines and transmission oil cooler lines. Proper pressure management ensures the longevity and reliability of the vehicle's critical systems, contributing to a smooth and safe driving experience.
Ford Fuel Line Fixes: A Comprehensive Guide to Repairing Your System
You may want to see also
System Compatibility: Using a transmission oil cooler line for a fuel line can lead to system incompatibility issues
The use of a transmission oil cooler line for a fuel line can introduce several system compatibility challenges that may lead to performance issues and potential safety concerns. Firstly, the materials and construction of these lines are designed with specific fluids in mind. Transmission oil cooler lines are typically made from durable materials like steel or aluminum, with a robust inner lining to withstand the high temperatures and pressures associated with transmission fluid. In contrast, fuel lines are usually constructed from materials like rubber or flexible plastic to accommodate the fluid's lower pressure and temperature requirements. Mixing these materials can result in compatibility problems, as the fuel line may not be able to withstand the harsher conditions of transmission fluid, leading to potential leaks or damage over time.
Secondly, the diameters and fittings of these lines are standardized for specific applications. Transmission oil cooler lines often have larger diameters to handle the higher flow rates of transmission fluid, while fuel lines are designed for the lower flow rates of fuel. Using a transmission oil cooler line for a fuel line might result in reduced performance due to the mismatch in flow capacity, affecting the engine's efficiency and power output. Additionally, the fittings and connectors used for these lines are not interchangeable, as they are engineered to fit specific systems. Attempting to use a transmission oil cooler line in a fuel system could lead to improper connections, causing fuel leaks or airlock issues.
Furthermore, the pressure and temperature requirements of transmission fluid and fuel are vastly different. Transmission fluid operates under higher pressure and temperature ranges, which may exceed the limits of a fuel line designed for lower pressure and temperature conditions. Over time, this can lead to premature aging of the fuel line material, causing cracks or leaks. In extreme cases, the fuel line may not be able to handle the increased stress, potentially resulting in fuel leaks or even a fire hazard.
In terms of system integration, the fuel system has specific requirements for filtration and contamination control. Using a transmission oil cooler line in this context might not provide the necessary protection against fuel contaminants, as the line's design and materials may not be optimized for fuel filtration. This could lead to fuel system degradation and potential engine damage.
To ensure optimal performance and safety, it is crucial to use components designed specifically for their intended applications. While it might be tempting to repurpose existing parts, the potential risks and performance issues associated with using a transmission oil cooler line for a fuel line cannot be overlooked. Proper system compatibility is essential to maintain the integrity and reliability of the vehicle's fuel delivery system.
Fuel Pressure Line: Can You Suck Through It?
You may want to see also
Frequently asked questions
A transmission oil cooler line is a crucial component in a vehicle's transmission system. It is designed to regulate the temperature of the transmission fluid, ensuring it remains within an optimal range. This is essential for the efficient operation and longevity of the transmission, as excessive heat can cause damage to internal components.
While both lines are used to transport fluids in a vehicle, they serve distinct purposes. The transmission oil cooler line, as the name suggests, is specifically for the transmission fluid, which is responsible for lubricating and cooling the transmission. On the other hand, a fuel line transports gasoline or diesel from the tank to the engine, playing a vital role in the vehicle's ability to run.
No, it is not recommended to use a transmission oil cooler line as a fuel line. These lines are engineered with specific materials and diameters to handle the unique requirements of their respective fluids. Using a transmission oil cooler line for fuel could lead to issues such as improper fuel flow, potential contamination, and reduced performance. It is always best to use the correct type of line for the intended purpose.
Yes, several problems can arise with transmission oil cooler lines and fuel lines. For transmission lines, leaks or blockages can cause transmission slippage or overheating. Fuel lines may experience leaks, cracks, or damage from vibrations, leading to potential engine misfires or fuel leaks. Regular inspection and maintenance are essential to identify and address these issues promptly.