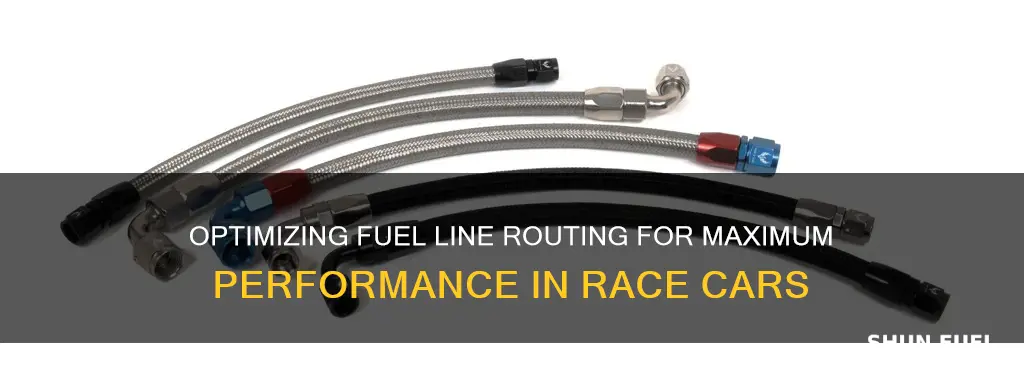
When it comes to racing cars, the placement of fuel lines is a critical aspect of performance and safety. The fuel lines must be strategically routed to ensure efficient fuel delivery while maintaining optimal aerodynamics and minimizing potential hazards. This paragraph will explore the various considerations and techniques involved in determining the ideal route for fuel lines in race cars, covering factors such as engine placement, vehicle design, and performance requirements.
What You'll Learn
- Engine Bay Layout: Consider fuel line placement to avoid interference with engine components
- Fuel Pump Location: Position the pump close to the tank for optimal flow
- Line Routing Material: Choose flexible, heat-resistant materials for durability and safety
- Grounding and Bonding: Ensure proper grounding to prevent static buildup and sparks
- Safety and Regulations: Adhere to racing safety standards for fuel line installation
Engine Bay Layout: Consider fuel line placement to avoid interference with engine components
When designing the engine bay layout of a race car, careful consideration of fuel line routing is crucial to ensure optimal performance and safety. Fuel lines play a critical role in delivering fuel to the engine, and their placement can significantly impact the overall efficiency and reliability of the vehicle. One of the primary goals is to avoid any interference with essential engine components, as this can lead to performance issues and potential damage.
The engine bay of a race car is typically a confined space with limited room for components. Therefore, it is essential to plan the layout strategically. Fuel lines should be routed in a way that minimizes the risk of contact with moving parts, such as the engine block, valves, and camshafts. These components can cause damage to the fuel lines if they come into contact, leading to fuel leaks or even fuel system failures during high-performance driving.
A common approach is to use a combination of flexible hoses and rigid pipes to route the fuel lines. Flexible hoses are ideal for areas where the lines need to move with the engine's vibrations, while rigid pipes can provide a more secure and stable path. The hoses should be secured in place using appropriate clamps and ties to prevent them from becoming loose or damaged. It is also important to ensure that the fuel lines are not routed too close to hot surfaces, as this can cause the fuel to degrade or even ignite.
Additionally, the placement of the fuel pump and tank should be considered. The fuel pump should be positioned to provide an adequate flow rate to the engine, and its location should allow for easy access during maintenance. The fuel tank, on the other hand, should be placed in a way that minimizes the length of the fuel lines, reducing the risk of sloshing and potential contamination. Proper ventilation of the fuel tank area is also essential to prevent the buildup of harmful vapors.
In summary, the engine bay layout of a race car requires meticulous planning to ensure the safe and efficient routing of fuel lines. By avoiding interference with engine components, using appropriate materials, and considering the placement of fuel-related components, engineers can optimize the performance and reliability of the vehicle. This attention to detail is vital in the high-performance world of racing, where every second counts.
Fuel Pump Ball Location: A Guide to Finding the Perfect Spot
You may want to see also
Fuel Pump Location: Position the pump close to the tank for optimal flow
When designing the fuel system for a race car, the placement of the fuel pump is a critical consideration. The ideal location for the fuel pump is as close to the fuel tank as possible. This proximity ensures optimal flow and performance, which is crucial for high-performance racing applications. By minimizing the distance between the pump and the tank, you reduce the pressure drop in the fuel line, allowing for a more efficient and responsive fuel delivery system.
The primary benefit of positioning the fuel pump near the tank is the improved flow rate. When the pump is closer to the source, it can deliver fuel more efficiently, providing a steady and consistent supply to the engine. This is especially important in racing, where quick acceleration and precise throttle response are essential. With the pump closer to the tank, you can ensure that the engine receives the required amount of fuel without any lag or delay, resulting in better performance and responsiveness.
Additionally, placing the fuel pump in this manner helps to reduce the risk of fuel pressure issues. Longer fuel lines can lead to pressure drops, especially at higher speeds or during aggressive driving maneuvers. By keeping the pump close to the tank, you minimize the length of the fuel lines, thereby reducing the chances of pressure loss and ensuring that the engine always receives the correct fuel pressure. This is a critical factor in maintaining engine performance and preventing potential issues related to fuel delivery.
Another advantage is the ease of installation and maintenance. When the fuel pump is positioned near the tank, it simplifies the routing of fuel lines, making the overall setup more organized and accessible. This accessibility is beneficial during track preparation and post-race inspections, allowing mechanics to quickly identify and address any potential issues with the fuel system. Proper placement also ensures that the fuel lines are less prone to damage from vibrations or impacts, further enhancing the reliability of the fuel delivery system.
In summary, the key to an efficient and high-performing fuel system in a race car is to position the fuel pump as close to the tank as possible. This approach optimizes fuel flow, reduces pressure drops, and ensures a consistent supply of fuel to the engine. By following this practice, race car engineers can create a robust and responsive fuel system, contributing to the overall success and competitiveness of the vehicle on the track.
Understanding Husqvarna Line Trimmer Fuel Mix: A Comprehensive Guide
You may want to see also
Line Routing Material: Choose flexible, heat-resistant materials for durability and safety
When designing the fuel line routing for a race car, the choice of materials is critical to ensure both performance and safety. The fuel lines must be flexible enough to accommodate the dynamic nature of the vehicle during acceleration, deceleration, and cornering, while also being able to withstand the high temperatures generated by the engine and exhaust systems.
Flexible materials are essential to allow the fuel lines to move and bend without restricting flow or causing damage. This is particularly important in high-performance applications where the vehicle's body and engine components are in constant motion. Materials like high-temperature silicone hoses and braided stainless steel are commonly used for their flexibility and ability to resist wear and tear. Silicone hoses offer excellent heat resistance, ensuring that the fuel lines can handle the extreme temperatures encountered in racing environments. Braided stainless steel provides additional strength and durability, making it ideal for high-pressure fuel systems.
Heat resistance is another critical factor in material selection. Race cars generate a significant amount of heat, and fuel lines must be able to operate reliably without degradation over time. Materials that can withstand temperatures up to 400°F (204°C) or higher are recommended. This ensures that the fuel lines remain flexible and functional even when exposed to the intense heat of the engine bay and exhaust system.
In addition to flexibility and heat resistance, the chosen material should also offer chemical resistance to prevent fuel leaks and ensure the longevity of the fuel system. The fuel lines should be able to resist the corrosive effects of gasoline and other fuels, especially in the presence of engine oil and other contaminants. Materials like fluoropolymer-lined hoses and stainless steel braids are often used for their superior chemical resistance.
Finally, the material should be easy to install and maintain. This is crucial for race teams, where quick and efficient maintenance is essential. Materials that can be easily routed and secured without specialized tools or extensive training will save time and reduce the risk of errors during setup and repairs. By carefully considering the material properties, race car engineers can ensure that the fuel line routing is both functional and safe, contributing to the overall performance and reliability of the vehicle.
Poulan PP3516AVX Fuel Line Length: Expert Guide
You may want to see also
Grounding and Bonding: Ensure proper grounding to prevent static buildup and sparks
Grounding and bonding are critical aspects of ensuring the safety and performance of a race car's fuel system. Proper grounding is essential to prevent static electricity buildup, which can lead to sparks and potentially ignite fuel vapor, posing a significant fire hazard. Here's a detailed guide on how to ensure effective grounding and bonding for your race car's fuel lines:
Understanding the Importance of Grounding:
Grounding serves as a path for electrical charges to flow into the earth, neutralizing any excess charge. In the context of a race car, it helps dissipate static electricity that can accumulate on various components, including the fuel tank, lines, and injectors. When static electricity builds up, it can create sparks, especially in the presence of fuel vapor, which is highly flammable. By grounding these components, you provide a safe path for the electricity to discharge, reducing the risk of ignition.
Grounding Points and Connections:
- Fuel Tank Grounding: The fuel tank should be grounded to the vehicle's chassis or a dedicated grounding point. This is typically achieved by connecting a grounding strap or wire from the tank to a sturdy metal part of the car, such as the engine block or a chassis ground point. Ensure the connection is secure and corrosion-resistant.
- Fuel Lines: Each fuel line should be grounded at multiple points along its length. This can be done by soldering or welding grounding clips or straps to the fuel lines and then connecting them to the chassis or other grounded components. Regular grounding points along the line help prevent static buildup and ensure a continuous path to ground.
- Fuel Injectors: Grounding the fuel injectors is crucial. Connect the injectors' electrical connections to the chassis or a dedicated grounding point. This ensures that any static electricity generated by the injectors is safely directed to the ground.
Bonding Techniques:
Bonding is the process of creating a conductive path between different components to ensure they maintain the same electrical potential. In the context of fuel systems, bonding helps prevent the buildup of static charges between components.
- Bonding Fuel Lines: When routing fuel lines, ensure they are bonded together at regular intervals, especially where they might come into contact with each other or other conductive components. This can be achieved by using bonding straps or clips and connecting them to the chassis or other grounded points.
- Grounding the Engine Bay: The engine bay should also be properly grounded. Use grounding straps to connect the engine block, intake manifold, and other metal components to the chassis. This helps dissipate static charges that could accumulate in the bay.
Additional Considerations:
- Inspect all grounding and bonding connections regularly for corrosion or damage. Corroded connections can compromise the grounding system's effectiveness.
- Consider using grounding compounds or paints on metal surfaces to improve conductivity and ensure a reliable ground.
- In high-performance racing environments, additional grounding measures might be necessary due to the intense electrical activity. Consult with engineers or experts to design a comprehensive grounding system tailored to your race car's specifications.
By implementing these grounding and bonding techniques, you create a robust electrical system that minimizes the risk of static-related issues in your race car's fuel lines. Proper grounding and bonding are essential for both safety and optimal performance, ensuring your vehicle operates efficiently and securely on the track.
Dodge Hellcat Fuel Line Sizing: A Comprehensive Guide
You may want to see also
Safety and Regulations: Adhere to racing safety standards for fuel line installation
When it comes to fuel line installation in a race car, adhering to safety standards and regulations is paramount. The primary goal is to ensure that the fuel lines are secure, properly routed, and resistant to potential hazards during high-speed racing. Here's a detailed guide on how to achieve this:
- Understanding the Regulations: Begin by familiarizing yourself with the specific rules and regulations set by the racing organization or governing body. Different racing series may have unique requirements, so it's crucial to consult the technical regulations. These guidelines often include specifications for fuel line diameter, material, routing, and protection to ensure the safety of the vehicle and its occupants.
- Material Selection: Choose the right fuel line material. High-quality, flexible, and durable materials like braided stainless steel are commonly used. These materials can withstand high temperatures, pressure, and the rigors of racing conditions. Ensure the fuel lines are compatible with the fuel type used in your vehicle to prevent any potential leaks or contamination.
- Routing and Protection: Proper routing is critical to safety. Fuel lines should be routed away from moving parts, hot surfaces, and potential impact zones. Here are some key considerations:
- Keep fuel lines away from the engine's hot components to prevent damage and potential fuel vaporization.
- Route the lines away from suspension components and steering linkages to avoid damage during cornering and braking.
- Ensure the lines are not routed too close to the ground, as this can lead to damage from road debris or tire wear.
- Use protective sleeves or shields to guard against sharp edges, vibrations, and potential impacts.
- Secure Mounting: Securely mount the fuel lines to prevent movement and potential damage. Use appropriate clamps or brackets that provide a firm hold without causing excessive pressure on the lines. Ensure that the mounting points are accessible for regular inspections and adjustments.
- Regular Inspections: Implement a rigorous inspection routine. Check the fuel lines for any signs of damage, cracks, or leaks regularly. Pay attention to areas where the lines are most susceptible to wear, such as bends, connections, and mounting points. Promptly address any issues to prevent fuel leaks, which can be extremely dangerous.
- Compliance and Documentation: Maintain thorough documentation of your fuel line installation process. This includes diagrams, photos, and records of materials used. Such documentation ensures compliance with regulations and provides valuable information for future inspections or modifications.
By strictly adhering to these safety and regulatory standards, you can ensure that your race car's fuel lines are installed correctly, minimizing the risk of fuel-related incidents and contributing to a safer racing environment.
Leaky Fuel Line: Signs, Causes, and Repairs
You may want to see also
Frequently asked questions
Fuel line routing is a critical aspect of race car engineering. It's essential to ensure the lines are routed away from high-temperature areas, such as the exhaust manifold and engine bay, to prevent damage and potential fuel leaks. A common practice is to run the fuel lines along the firewall, using rubber or plastic hoses, and securing them with clips or ties to maintain tension and prevent chafing.
While it might be tempting to reuse fuel lines, it's not recommended. Race car fuel lines are designed to withstand high-performance environments, including extreme temperatures and pressure. Street car fuel lines may not meet these standards and could fail prematurely during racing, leading to dangerous situations. Always use fuel lines specifically designed for racing applications.
Routing the fuel lines away from sharp bends and incorporating flexible, vibration-damping materials can help. Consider using fuel line protectors or sleeves to shield the lines from sharp edges and vibrations. Regularly inspect the lines for any signs of wear and replace them if necessary to ensure the integrity of the fuel system.
Yes, racing organizations often have strict rules regarding fuel line placement to ensure safety. These rules may vary depending on the series and track. It's crucial to familiarize yourself with the regulations provided by the governing body of your racing series to ensure compliance and avoid penalties.
Fuel lines should be secured using clips, ties, or brackets to maintain tension and prevent movement. Route the lines through the body panels or use dedicated fuel line brackets to attach them securely. Proper securing ensures that the lines remain in place during high-speed maneuvers and reduces the risk of damage or fuel spillage.