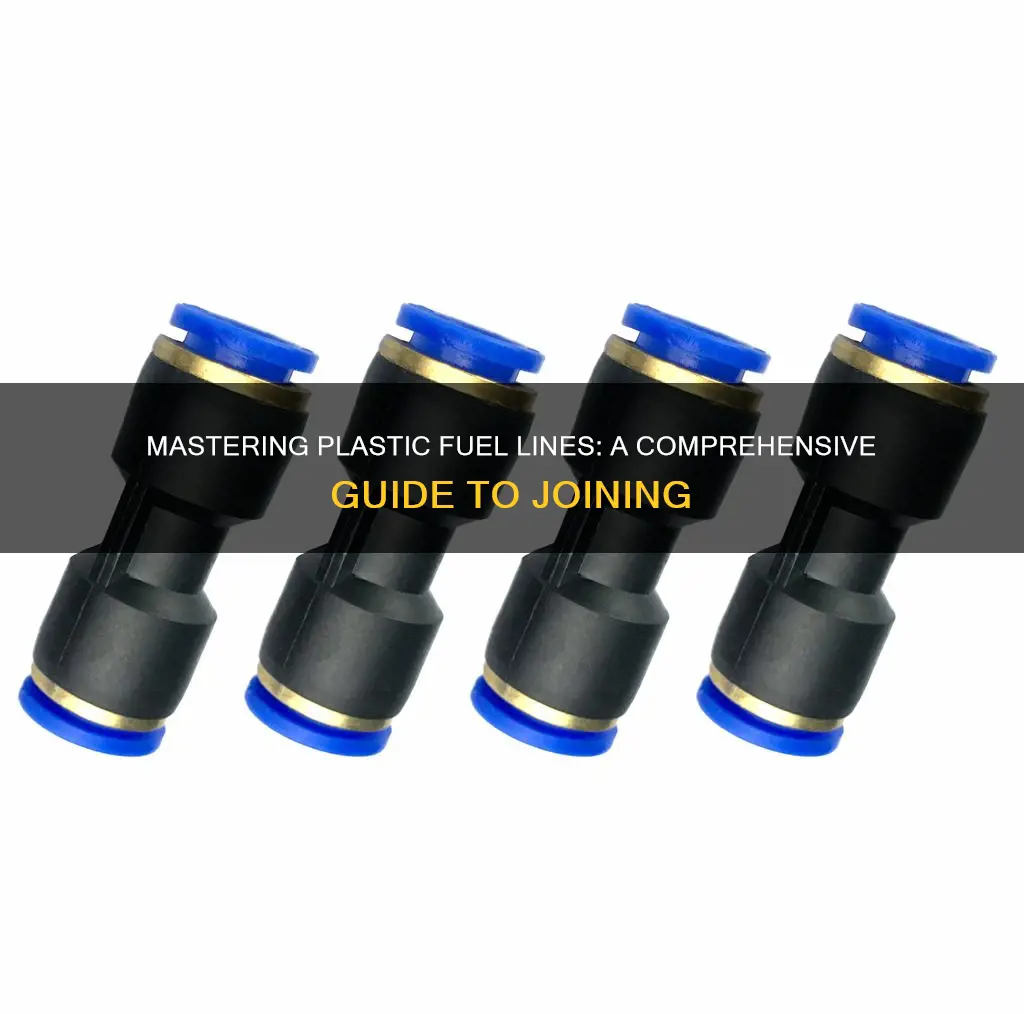
Joining plastic fuel lines requires careful preparation and the right tools to ensure a secure and leak-free connection. This process involves cleaning and preparing the ends of the fuel lines, using a suitable solvent or adhesive to bond them together, and then clamping or crimping the connection to create a tight seal. It's important to follow manufacturer guidelines and use the appropriate materials to ensure the safety and efficiency of the fuel system. With the right techniques and attention to detail, you can effectively join plastic fuel lines and maintain the integrity of your vehicle's fuel supply.
What You'll Learn
- Prepare Tools: Gather necessary tools like fuel line connectors, clamps, and cleaning supplies
- Inspect Lines: Check for damage, cracks, or leaks before connecting
- Clean Surfaces: Ensure both ends are free of debris and contaminants
- Connect Lines: Tighten connectors securely, following manufacturer's instructions
- Test System: Run a fuel pressure test to ensure proper connection and no leaks
Prepare Tools: Gather necessary tools like fuel line connectors, clamps, and cleaning supplies
Before you begin the process of joining plastic fuel lines, it's crucial to ensure you have all the necessary tools and materials ready. This preparation will make the task more efficient and help you avoid any delays or complications during the installation. Here's a step-by-step guide on gathering the required tools:
Fuel Line Connectors: These are essential components that will allow you to join the plastic fuel lines securely. Look for connectors that are specifically designed for plastic fuel lines and ensure they are compatible with the diameter and type of fuel line you are working with. Common types include quick-connect fittings, push-to-connect fittings, or clamp-style connectors. Having a variety of connector sizes is beneficial to accommodate different fuel line lengths.
Clamps: Clamps are used to secure the fuel lines and connectors in place. Get a set of high-quality metal or plastic clamps that fit the diameter of your fuel lines. Ensure they have a good grip and are easy to adjust. You might also consider getting some additional clamps in case you need to make adjustments or have extra fuel lines to connect.
Cleaning Supplies: Proper cleaning is often overlooked but is a critical step in the process. Gather some cleaning supplies such as a fuel line cleaner, a brush or cleaning tool specifically designed for fuel lines, and a rag or cloth for wiping. Cleaning the fuel lines and connectors will remove any dirt, debris, or old fuel residue, ensuring a proper bond and preventing potential leaks.
Additionally, consider having some tape or adhesive tape specifically designed for fuel line repairs. This can be useful for temporary fixes or if you need to make adjustments before finalizing the connection. It's also a good idea to keep a small inventory of replacement fuel lines, especially if you're working on an older vehicle or one with specific fuel line requirements.
By having these tools and supplies readily available, you'll be well-prepared to tackle the task of joining plastic fuel lines efficiently and effectively. Remember, proper preparation is key to a successful and safe fuel system installation.
Mastering Fuel Routing: A Guide to Walbro Carb Installations
You may want to see also
Inspect Lines: Check for damage, cracks, or leaks before connecting
Before attempting to join any plastic fuel lines, it is crucial to thoroughly inspect them for any signs of damage, cracks, or leaks. This step is essential to ensure the safety and efficiency of your fuel system. Here's a detailed guide on how to inspect the lines effectively:
Visual Inspection: Start by visually examining the fuel lines for any visible defects. Look for cracks, brittleness, or any signs of wear and tear. Check for any discoloration or hardening of the plastic material, which could indicate prolonged exposure to heat or fuel contaminants. Pay close attention to bends and fittings, as these areas are more prone to damage. Inspect both the interior and exterior of the lines to ensure no cracks or splits are present.
Leak Testing: A critical part of the inspection process is to check for leaks. Start by removing the fuel lines from the vehicle and placing them in a controlled environment. Use a soapy water solution and carefully apply it to the lines, ensuring you cover all connections and fittings. If bubbles appear at any point, it indicates a potential leak. This simple test can help identify weak spots or damaged areas that may cause fuel leaks, which can be extremely dangerous.
Pressure Testing (Optional): For a more comprehensive assessment, consider using a fuel pressure tester. This test involves connecting the tester to the fuel line and measuring the pressure. If the pressure drops or fluctuates, it suggests a potential issue with the line's integrity. This method is particularly useful for identifying internal damage or blockages that may not be visible to the naked eye.
Documentation and Comparison: Take detailed notes of the inspection process, including the condition of the lines and any defects found. Compare the current state of the lines with previous inspections or known good lines to identify any deterioration or changes. This documentation will be valuable for future reference and can help you track the overall health of your fuel system.
By following these inspection procedures, you can ensure that any potential issues with the plastic fuel lines are identified early on. This preventative measure will contribute to a safer and more reliable fuel system, reducing the risk of fuel-related problems and costly repairs. Remember, proper inspection and maintenance are key to keeping your vehicle's fuel system in optimal condition.
Bleed Massey Ferguson 245 Fuel Line: A Step-by-Step Guide
You may want to see also
Clean Surfaces: Ensure both ends are free of debris and contaminants
When joining plastic fuel lines, ensuring that both ends are clean and free of contaminants is crucial for a successful and safe connection. This process begins with meticulous surface preparation, which is often overlooked but is essential for a reliable bond. Here's a detailed guide on how to achieve this:
Step 1: Debris Removal
Start by removing any visible debris from the ends of the fuel lines. This includes dirt, rust, old adhesive residues, or any other foreign matter. Use a fine-grit sandpaper or a specialized deburring tool to gently remove these contaminants. Be thorough but careful to avoid damaging the plastic material. For hard-to-reach areas, consider using a small brush or a compressed air blast to dislodge particles.
Step 2: Cleaning with Solvents
After debris removal, it's imperative to clean the surfaces with an appropriate solvent. This step ensures that any remaining contaminants, such as oils or greases, are eliminated. Choose a solvent that is compatible with the type of plastic fuel line you are working with. Common choices include acetone, methyl ethyl ketone (MEK), or isopropyl alcohol. Apply the solvent generously to a clean cloth and rub the ends of the fuel lines in a circular motion, ensuring complete coverage. Allow the solvent to work for a few minutes to dissolve and lift away any remaining contaminants.
Step 3: Rinsing and Drying
Once the solvent has done its job, rinse the cleaned areas with clean water to remove any residue. Ensure that no traces of the solvent remain, as they can attract dirt and cause future issues. After rinsing, thoroughly dry the surfaces with a lint-free cloth. Moisture can interfere with the bonding process, so it's crucial to eliminate any remaining water droplets.
Step 4: Inspect for Contaminants
Finally, inspect the cleaned and dried surfaces closely. Use a magnifying glass if necessary to ensure you don't miss any hidden contaminants. If any debris or contaminants are still present, repeat the cleaning process until the surfaces are pristine. This meticulous attention to detail will ensure a strong and durable connection when joining the plastic fuel lines.
By following these steps, you'll create a clean and contaminant-free environment for the fuel line connection, setting the stage for a successful and long-lasting join.
Thawing Fuel Lines: Quick Fixes for Frozen Fuel Lines
You may want to see also
Connect Lines: Tighten connectors securely, following manufacturer's instructions
When joining plastic fuel lines, ensuring a secure and tight connection is crucial to prevent fuel leaks and maintain the integrity of your vehicle's fuel system. Here's a step-by-step guide on how to connect these lines effectively:
Prepare the Components: Before you begin, ensure you have the correct connectors and fittings for your specific fuel line application. Check the manufacturer's recommendations to ensure compatibility. Clean the ends of the fuel lines and connectors to remove any dirt, debris, or old sealant. This step is essential to create a clean and secure connection.
Assembly: Start by inserting the male end of one fuel line into the female connector, aligning the threads or locking mechanism. Ensure it is fully inserted and seated correctly. Repeat this process for the second fuel line, connecting it to the appropriate fitting or another line. Use your hands or a pair of pliers to hold the connectors in place temporarily while you proceed to the next step.
Tightening the Connectors: The key to a successful connection is applying the right amount of torque. Refer to the manufacturer's instructions or the vehicle's service manual for the specific torque value required. Use a torque wrench to tighten the connectors to the specified value. Over-tightening can damage the fuel lines, while under-tightening may result in a weak connection. Aim for a secure, tight fit without forcing anything to avoid damage.
Final Checks: After tightening, inspect the connections for any signs of leakage. Apply a small amount of fuel or a suitable sealant to the connection and observe for any seepage. If everything is secure, your fuel lines should now be properly joined and ready for use.
Remember, each fuel line system may have unique requirements, so always refer to the manufacturer's guidelines for the best results. Following these steps will help ensure a reliable and safe fuel system in your vehicle.
Unleash the Power: NICOPP Lines for Fuel Efficiency
You may want to see also
Test System: Run a fuel pressure test to ensure proper connection and no leaks
To ensure the integrity of your fuel system when working with plastic fuel lines, it's crucial to perform a fuel pressure test as a final step in the installation process. This test will verify that the connections are secure and there are no leaks, which is essential for the safe and efficient operation of your vehicle. Here's a detailed guide on how to conduct this test:
Preparation:
Before starting, ensure you have the necessary tools and equipment, including a fuel pressure gauge, a source of compressed air or a pump, and a container to collect any fuel that may be released during the test. It's also a good practice to wear protective gear, such as gloves and safety goggles, to prevent any potential fuel-related hazards.
Test Procedure:
- Connect the Gauge: Attach the fuel pressure gauge to the fuel line where it connects to the fuel pump or the fuel rail. Ensure a tight and secure connection.
- Apply Pressure: Using the compressed air or pump, apply a measured amount of pressure to the fuel system. Start with a low pressure and gradually increase it. The specific pressure value will depend on your vehicle's requirements, which you can find in the vehicle's manual.
- Monitor for Leaks: While applying pressure, closely observe the gauge for any fluctuations or drops in pressure. These changes could indicate a leak in the system. Also, check for any visible signs of fuel escaping from connections or joints.
- Check Connections: Inspect all connections, including the fuel pump, fuel filter, and any adapters or fittings. Ensure that all components are properly seated and tightened. Look for any signs of damage or deformation that might have occurred during the installation process.
- Leak Test: If you detect any pressure drops or suspect a leak, release the pressure and carefully inspect the affected area. Apply a small amount of soapy water or a leak detection dye to the connections and observe if any bubbles form or the dye appears, indicating a leak.
Interpreting Results:
- If the pressure holds steady and no leaks are detected, your fuel system is likely functioning correctly, and the connections are secure.
- If you find any leaks or pressure drops, it's essential to identify and fix the issue before proceeding. This might involve tightening connections, replacing damaged components, or re-installing certain parts.
Remember, this test is a critical step in ensuring the reliability and safety of your vehicle's fuel system. It's always better to be thorough and catch potential issues early on to avoid more significant problems down the line.
Cold Fuel Lines: Preventing Engine Damage in Freezing Temperatures
You may want to see also
Frequently asked questions
Plastic fuel lines are commonly used in modern vehicles, especially those with fuel injection systems. If your car is relatively new, it's likely to have plastic lines. You can check the owner's manual or consult a mechanic to confirm the type of fuel lines your vehicle uses.
Replacing plastic fuel lines typically requires a few essential tools. You'll need a fuel line cutter or a set of pipe cutters, a fuel line crimper or a set of line tools, and a fuel line cleaner. It's also recommended to have a new set of fuel lines ready that match your vehicle's specifications.
While it is possible to join plastic fuel lines without specialized skills, it requires patience and attention to detail. Ensure you have a clean work area and follow the manufacturer's instructions for the specific fuel line type you are working with. It's a good idea to practice on a spare line before installing it in your vehicle to get a feel for the process.