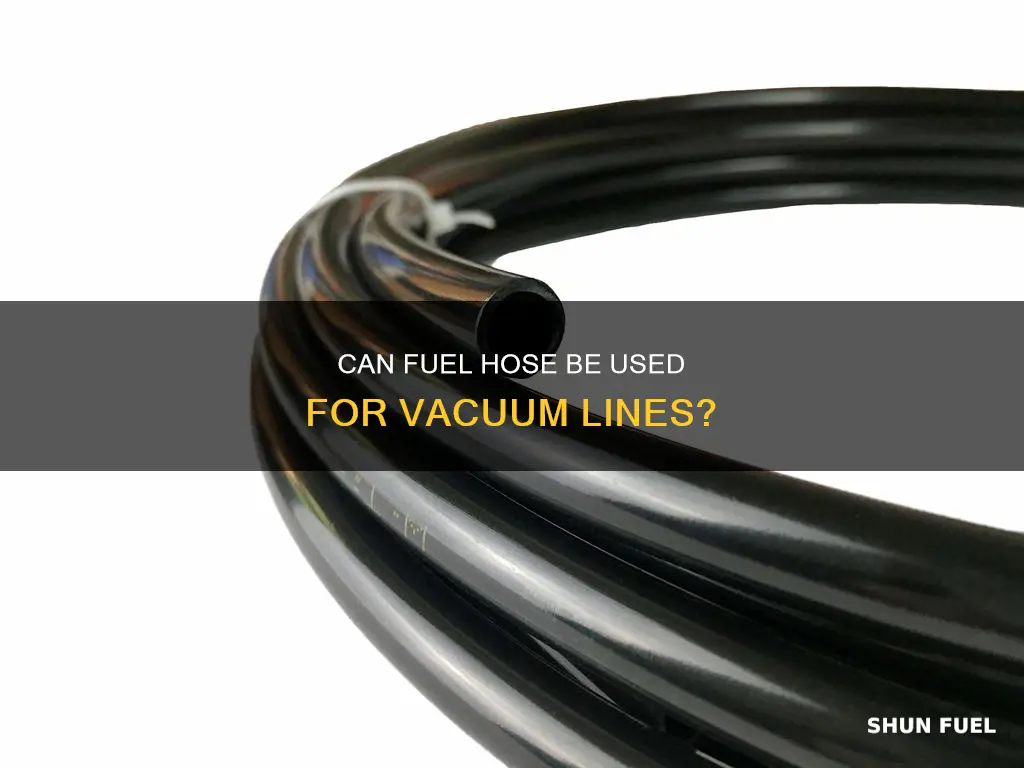
The question of whether fuel hoses can be used for vacuum lines is an important consideration for vehicle maintenance and safety. Fuel hoses and vacuum lines serve distinct purposes in a vehicle's engine system, and understanding their differences is crucial. While fuel hoses are designed to handle the high-pressure fuel required for engine operation, vacuum lines are responsible for transmitting suction to control various engine functions. This introduction sets the stage for a detailed exploration of the compatibility and potential risks associated with using fuel hoses for vacuum lines.
What You'll Learn
- Hose Material: Fuel hoses and vacuum lines use similar materials, making them interchangeable
- Pressure Rating: Both hoses can handle similar pressure levels, ensuring compatibility
- Temperature Tolerance: They can withstand similar temperature ranges, a key factor for compatibility
- Flexibility: The flexibility of fuel hoses makes them suitable for use in vacuum systems
- Chemical Resistance: Both hoses resist similar chemicals, ensuring they can be used interchangeably
Hose Material: Fuel hoses and vacuum lines use similar materials, making them interchangeable
The question of whether a fuel hose can be used for vacuum lines often arises due to the similarity in their construction and the materials they are made from. Both fuel hoses and vacuum lines are designed to transmit fluid or gas under pressure, and their performance and safety are heavily reliant on the choice of materials. This interchangeability is a result of the shared requirements and the fact that the materials used for both applications are often quite similar.
One of the key materials used in the construction of these hoses is rubber, which is known for its flexibility, durability, and resistance to various chemicals and temperatures. Natural rubber is commonly used for its excellent elasticity and ability to withstand pressure. However, for vacuum lines, a more cost-effective and lightweight alternative, such as synthetic rubber, can be utilized without compromising performance. Both types of rubber hoses are designed to handle the specific demands of their respective applications.
In addition to rubber, hoses for both fuel and vacuum systems often incorporate layers of reinforcement to enhance their structural integrity. These reinforcements typically include steel wires or fibers, which provide additional strength and flexibility. The placement of these reinforcements is crucial, as they must be positioned to withstand the forces exerted by the transmitted fluid or gas. This design consideration ensures that the hose can handle the pressure and movement associated with its use.
The materials used in the construction of fuel hoses and vacuum lines also include protective coatings to prevent damage from abrasion, chemicals, and environmental factors. These coatings can be made from various materials, such as rubber, plastic, or synthetic compounds, depending on the specific requirements of the application. The choice of coating ensures that the hose remains intact and functional over its lifespan.
Given the similarities in the materials and construction methods, it is often safe to assume that a fuel hose can be used for a vacuum line, provided it meets the necessary specifications and pressure ratings. However, it is essential to consider the specific requirements of the vacuum system, including the type of fluid or gas it will handle and any unique design considerations. Proper selection and installation of the hose will ensure optimal performance and safety in both applications.
Mastering the Art of Welding: Safe Techniques for Auto Fuel Lines
You may want to see also
Pressure Rating: Both hoses can handle similar pressure levels, ensuring compatibility
When considering the use of a fuel hose for vacuum applications, it's crucial to evaluate the pressure rating of both the fuel hose and the vacuum system. Both hoses are designed to handle similar pressure levels, ensuring compatibility and safe operation. This compatibility is essential to prevent damage to the hoses and potential safety hazards.
The pressure rating of a hose refers to the maximum pressure it can withstand without failing or leaking. For fuel hoses, this rating is typically specified in pounds per square inch (PSI) or bar. Similarly, vacuum systems have their own pressure requirements, often measured in inches of mercury (inHg) or millimeters of mercury (mmHg).
In the context of using a fuel hose for vacuuming, it's important to match the pressure capabilities of the hose to the demands of the vacuum system. If the vacuum system operates at a pressure significantly higher than the hose's rating, it could lead to excessive stress on the hose, potentially causing it to burst or fail. Conversely, if the hose is rated for much higher pressures than the vacuum system requires, it may be overkill and unnecessarily expensive.
To ensure compatibility, it's recommended to consult the specifications provided by the manufacturers of both the fuel hose and the vacuum system. These specifications will outline the pressure ratings for each component, allowing you to make an informed decision. By selecting a fuel hose with a pressure rating that aligns with the vacuum system's requirements, you can ensure optimal performance and safety.
Additionally, it's worth noting that some fuel hoses may have additional features or reinforcements designed to handle specific pressure ranges. For example, certain hoses might include layers of rubber or synthetic materials to enhance their pressure-bearing capacity. Understanding these features can further assist in making an appropriate choice for vacuum applications.
Subaru Impreza 2010: Canister Fuel Line Location Guide
You may want to see also
Temperature Tolerance: They can withstand similar temperature ranges, a key factor for compatibility
When considering the compatibility of fuel hoses and vacuum lines, temperature tolerance is a critical factor that often goes unnoticed. Both systems operate under varying thermal conditions, and the ability of these hoses to withstand these temperature fluctuations is essential for their long-term functionality and safety.
In the context of fuel hoses, these components are designed to handle the extreme temperatures associated with fuel systems. Fuel hoses are typically made from materials that can endure the high heat generated during combustion processes, ensuring they remain flexible and resistant to degradation. This is particularly important in high-performance vehicles or those operating in demanding environments.
Vacuum lines, on the other hand, are exposed to the ambient temperature of the surrounding environment, which can vary significantly depending on the application. However, they also need to withstand the temperatures generated by the engine during operation. The key here is that both systems experience a wide range of temperatures, and the hoses must be able to bridge this thermal gap without compromising their structural integrity.
The temperature tolerance of these hoses is a result of the careful selection of materials. For instance, rubber hoses are often used due to their flexibility and ability to resist heat and cold. These hoses can handle temperature extremes, making them suitable for both fuel and vacuum applications. Additionally, the construction process plays a vital role; hoses with multiple layers or braids can provide enhanced protection against temperature-related damage.
In summary, the temperature tolerance of fuel hoses and vacuum lines is a fundamental aspect of their design and functionality. By withstanding similar temperature ranges, these hoses ensure compatibility and reliability, allowing for efficient and safe operation in various automotive and industrial settings. This compatibility is a key consideration when designing and implementing these systems, ensuring optimal performance and longevity.
Understanding the Dual Fuel Lines in Your Chainsaw: A Guide
You may want to see also
Flexibility: The flexibility of fuel hoses makes them suitable for use in vacuum systems
The flexibility of fuel hoses is a key advantage that makes them an ideal choice for vacuum systems. This unique property allows the hoses to navigate around tight spaces and complex layouts, which is often a challenge in vacuum applications. When designing a vacuum system, engineers must consider the physical constraints of the environment, such as limited space, sharp corners, and varying pipe diameters. Fuel hoses, with their pliable nature, can easily conform to these demands, ensuring a secure and efficient connection without the risk of damage or disconnection.
In vacuum systems, the layout can be intricate, with numerous components and pipes in close proximity. The ability of fuel hoses to bend and twist without losing their structural integrity is crucial. This flexibility enables the hoses to reach the necessary locations, providing a reliable and consistent vacuum seal. For instance, in a laboratory setting, a fuel hose can be manipulated to connect a vacuum pump to a distant collection chamber, ensuring a tight seal despite the distance and the potential for sharp turns.
Furthermore, the flexibility of fuel hoses contributes to the overall safety and longevity of the vacuum system. Rigid hoses might struggle to accommodate the dynamic nature of vacuum operations, leading to potential damage or stress points. By using flexible hoses, the system can withstand the constant expansion and contraction that occurs during operation, reducing the risk of leaks, cracks, or other forms of hose failure. This is particularly important in high-vacuum environments where even a small breach can have significant consequences.
The design of fuel hoses also takes into account the need for durability and resistance to various substances. In a vacuum system, the hoses may be exposed to different chemicals, temperatures, and pressures. The flexibility of the hose material allows for the inclusion of reinforcing layers and protective coatings, ensuring that the hose can withstand these demanding conditions without losing its flexibility. This combination of flexibility and robustness is essential for the reliable operation of vacuum systems.
In summary, the flexibility of fuel hoses is a critical factor in their suitability for vacuum systems. It enables the hoses to navigate complex layouts, provides a secure and consistent vacuum seal, enhances safety by reducing potential failure points, and allows for the necessary durability in harsh environments. By leveraging this unique property, engineers can design efficient and reliable vacuum systems that meet the specific demands of various applications.
Mercury Verado Fuel Line Removal: A Step-by-Step Guide
You may want to see also
Chemical Resistance: Both hoses resist similar chemicals, ensuring they can be used interchangeably
When considering the use of a fuel hose for vacuum applications, it's important to understand the chemical resistance properties of both types of hoses. Both fuel hoses and vacuum hoses are designed to withstand a range of chemicals, making them suitable for various industrial and commercial uses. The key advantage here is their ability to resist similar chemicals, which allows for a seamless transition between the two applications.
In the context of chemical resistance, these hoses are engineered to handle specific types of chemicals commonly found in fuel and vacuum systems. For instance, they can effectively manage hydrocarbons, which are prevalent in fuel and can also be present in certain vacuum processes. Additionally, they often exhibit resistance to other common chemicals such as acids, bases, and solvents, ensuring their versatility across different environments.
The interchangeability of these hoses is a significant benefit. Since both hoses resist similar chemicals, they can be used interchangeably in applications where one might be more suitable than the other. This flexibility is particularly useful in situations where a specific hose type is not readily available or when a quick replacement is necessary. By understanding the chemical resistance properties, users can make informed decisions about hose selection, ensuring optimal performance and safety.
Furthermore, the chemical resistance of these hoses is not just about the materials used but also the construction and design. The hoses often feature protective layers or coatings that enhance their ability to resist chemicals. These layers can include rubber, neoprene, or specialized synthetic materials, each chosen for its ability to withstand specific chemical environments.
In summary, the chemical resistance of both fuel hoses and vacuum hoses is a critical factor in their interchangeability. By resisting similar chemicals, these hoses can be confidently used in a variety of applications, providing a practical solution for industries that require versatile and reliable hose systems. This understanding of chemical compatibility ensures that users can make the most of these hoses, optimizing their performance and longevity.
Scooter Fuel Lines: Powering the Engine's Heart
You may want to see also
Frequently asked questions
While fuel hoses and vacuum lines serve similar purposes in a vehicle's engine system, they are not interchangeable. Fuel hoses are designed to handle the high-pressure fuel that powers the engine, while vacuum lines are used to create a vacuum to control various engine functions. Using a fuel hose for a vacuum line could lead to issues with engine performance and safety.
Fuel hoses are typically made of rubber or synthetic materials and are designed to withstand high-pressure fuel, which can be highly flammable. Vacuum lines, on the other hand, are usually made of flexible materials like silicone or rubber and are used to create a vacuum to control functions like the brake booster, cruise control, and emissions systems.
Modifying vacuum lines to use a fuel hose is not recommended and can be dangerous. The materials and construction of fuel hoses are not suitable for creating a vacuum, and using one in this manner could lead to engine malfunctions, reduced performance, and potential safety hazards. It's best to use the appropriate components for each system to ensure optimal engine function and safety.