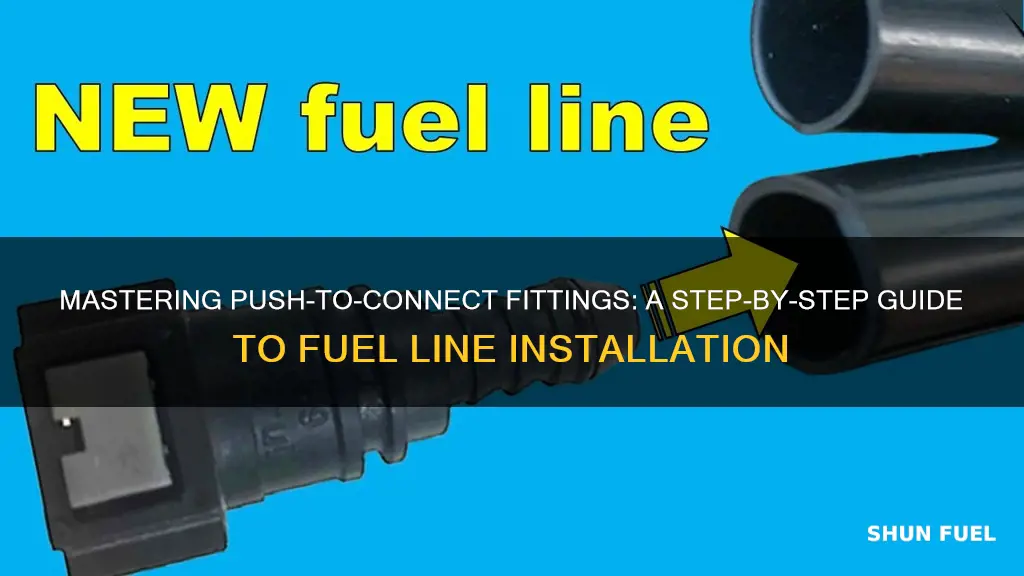
Installing push-to-connect fittings for fuel lines is a straightforward process that can be completed with basic tools and a bit of patience. This method of connecting fuel lines is popular due to its ease of use and the ability to make secure, leak-free connections without the need for soldering or welding. The process involves inserting the fuel line into the fitting and pushing it until it locks into place, ensuring a tight seal. This guide will provide a step-by-step overview of the installation process, including preparing the fittings and fuel line, ensuring a proper fit, and making the connection to guarantee a reliable fuel supply system.
What You'll Learn
- Preparation: Clean and inspect fuel lines, ensuring no damage or debris
- Fitting Selection: Choose fittings compatible with fuel line material and size
- Connection Technique: Apply thread seal tape and tighten fittings securely
- Leak Test: Check for leaks by applying pressure and inspecting for drips
- Safety Measures: Wear protective gear and ensure proper ventilation during installation
Preparation: Clean and inspect fuel lines, ensuring no damage or debris
Before you begin the installation process of push-to-connect fittings for your fuel line, it is crucial to ensure that the fuel lines are in optimal condition. Start by thoroughly cleaning the fuel lines to remove any dirt, grime, or debris that may have accumulated over time. This step is essential as it ensures a proper connection and prevents any potential issues during the installation. Use a suitable cleaning agent or a mixture of water and detergent to scrub the interior of the fuel lines. Pay close attention to any bends or joints, as these areas can often accumulate more debris.
Once the cleaning process is complete, it's time to inspect the fuel lines for any signs of damage or wear. Carefully examine the lines for any cracks, punctures, or leaks. Look for any visible signs of corrosion or deterioration, especially in areas where the lines are exposed to the elements. If you notice any damage, it is best to replace the affected section to ensure a secure and safe installation. Check for any kinks or twists in the fuel lines, as these can affect the flow of fuel and potentially cause issues during operation.
To further ensure the integrity of the fuel lines, consider using a fuel line inspection kit. These kits often include specialized tools and lighting to help identify any hidden damage or issues. You can also use a mirror or a camera to inspect hard-to-reach areas. If you find any issues, such as small punctures or leaks, it is recommended to repair or replace the affected line before proceeding with the installation.
Additionally, make sure to wear protective gear, such as gloves and safety goggles, to protect yourself from any potential hazards during the cleaning and inspection process. This is especially important when dealing with fuel, as it can be flammable and hazardous. By taking the time to properly clean and inspect the fuel lines, you are setting the foundation for a successful and safe installation of the push-to-connect fittings.
Clogged Fuel Line? Fix Your Lawn Mower's Performance with These Steps
You may want to see also
Fitting Selection: Choose fittings compatible with fuel line material and size
When it comes to installing push-to-connect fittings for fuel lines, the first step is crucial: selecting the right fittings. This ensures a secure and leak-free connection, which is essential for any fuel system. The process begins with understanding the fuel line material and its diameter. Different materials, such as rubber, vinyl, or braided steel, require specific fittings to ensure compatibility and a tight seal. For instance, rubber fuel lines often use fittings made from the same material to maintain flexibility and prevent cracking. Similarly, vinyl fuel lines might call for fittings with a compatible inner diameter to ensure a snug fit.
The size of the fuel line is another critical factor. Fittings should match the inside diameter of the fuel line to create a proper seal. Most push-to-connect fittings come in various sizes, allowing you to choose the one that fits your fuel line perfectly. It's important to measure the fuel line's diameter accurately to avoid any issues with installation. Using a caliper or a simple ruler can help you determine the correct size.
Additionally, consider the type of fitting needed. Push-to-connect fittings typically come in two main styles: barbed and compression. Barbed fittings are ideal for fuel lines with a smooth interior, while compression fittings are better suited for lines with a slightly textured surface. The choice depends on the specific requirements of your fuel line and the overall design of your system.
To ensure a successful installation, always refer to the manufacturer's guidelines for your chosen fittings. These guidelines will provide detailed instructions on how to properly connect the fittings to the fuel line, including any specific tools or techniques required. Following these instructions will help you achieve a secure and reliable connection.
In summary, selecting the right fittings is the foundation of a successful fuel line installation. By considering the material and size of your fuel line, you can choose fittings that will create a tight, leak-free seal. Remember to measure accurately and refer to manufacturer guidelines for the best results.
Kawasaki 600 Fuel Line Hook-Up: A Step-by-Step Guide
You may want to see also
Connection Technique: Apply thread seal tape and tighten fittings securely
When installing push-to-connect fittings for a fuel line, ensuring a secure and leak-free connection is crucial. Here's a step-by-step guide on how to achieve this by applying thread seal tape and tightening the fittings securely:
Prepare the Components: Begin by ensuring you have the necessary tools, including thread seal tape (also known as Teflon tape or pipe compound). Inspect the fittings and fuel line for any damage or debris. Clean the threads of both the fitting and the fuel line to remove any dirt or old tape.
Apply Thread Seal Tape: Wrap the thread seal tape around the threads of the fitting and the fuel line. Start with a small section of tape and overlap it slightly to create a secure bond. Continue wrapping in a clockwise direction, ensuring that the tape is applied firmly and evenly. The tape acts as a barrier, preventing fuel line leaks and providing a reliable connection. Use enough tape to cover the entire thread length, typically 1-2 full turns.
Tighten Securely: Once the tape is applied, it's time to tighten the fitting. Use a wrench or pliers to secure the fitting onto the fuel line. Apply firm pressure and tighten the fitting by hand first. Then, using the wrench, give it an additional quarter to half turn. This ensures a tight seal and prevents the fitting from loosening over time. Be careful not to over-tighten, as it may damage the threads or the fuel line.
Final Check: After tightening, inspect the connection for any signs of leakage. Look for any wet spots or fuel seeping around the fitting. If everything appears secure, test the connection by running the fuel line under pressure or simply checking for leaks over time.
Remember, the key to a successful installation is a clean surface, proper application of thread seal tape, and a secure, firm tightening process. This technique ensures a reliable and long-lasting connection for your fuel line.
Braided Fuel Line Heat Resistance: Unraveling the Truth
You may want to see also
Leak Test: Check for leaks by applying pressure and inspecting for drips
When installing push-to-connect fittings for a fuel line, a critical step is the leak test, which ensures the system is secure and free from any potential leaks. This process involves applying pressure to the fittings and inspecting for any drips or signs of leakage. Here's a detailed guide on how to perform this test effectively:
Preparation: Before starting, ensure you have the necessary tools, including a pressure gauge, a source of compressed air or a pump, and a clean cloth or rag. It's also essential to have a well-lit area for inspection. Turn off the fuel supply to the system you are working on to prevent any accidental fuel release during the test.
Applying Pressure: Start by connecting the fittings as you would during a typical installation. Securely attach the fittings to the fuel line and any other components, following the manufacturer's instructions. Then, use the pressure gauge to apply a specific amount of pressure, typically around 20-30 psi, to the system. This pressure should be maintained for a recommended duration, usually a few minutes, allowing the system to stabilize.
Leak Inspection: With the pressure applied, carefully inspect the entire system for any signs of leakage. Check all connections, including the push-to-connect fittings, for any drips or moisture. Pay close attention to the threads, seals, and O-rings, as these are common areas where leaks can occur. If you notice any moisture or a droplet forming, it indicates a potential leak. Additionally, look for any visible damage or deformation on the fittings, as this could also lead to leakage.
Troubleshooting: If you detect a leak, immediately release the pressure and identify the source. Tighten any loose connections or replace damaged components. Ensure that all fittings are properly aligned and seated. If the leak persists, consider using a different fitting or seeking professional advice to ensure a proper installation.
Documentation: After the leak test, document the results. Note any issues found and the corresponding actions taken to rectify them. This documentation will be valuable for future reference, especially if any problems arise during the system's operation.
By following these steps, you can ensure that your push-to-connect fuel line installation is secure and leak-free, providing a reliable and safe fuel system for your vehicle or equipment. Remember, proper leak testing is crucial to prevent fuel wastage, potential engine damage, and safety hazards.
O-Ring Compatibility: Can Regular O-Rings Be Used on Fuel Lines?
You may want to see also
Safety Measures: Wear protective gear and ensure proper ventilation during installation
When working with fuel lines and push-to-connect fittings, it's crucial to prioritize safety to avoid any potential hazards. Here are some essential safety measures to keep in mind during the installation process:
Protective Gear: Before beginning the installation, ensure you are adequately protected. Wear safety goggles to shield your eyes from any potential splashes or debris. Gloves are essential to provide a secure grip and protect your hands from sharp edges or hot surfaces. Consider wearing a respirator or a mask to prevent inhaling any harmful fumes or vapors that may be released during the process. Additionally, long sleeves and closed-toe shoes can offer extra protection and comfort.
Ventilation: Proper ventilation is critical to maintaining a safe working environment. Fuel lines and fittings can release volatile substances, so ensure you are working in a well-ventilated area or, if possible, outdoors. Open windows and doors to allow fresh air circulation. If working in a confined space, consider using a portable air purifier or a fan to increase air movement and reduce the concentration of any potentially harmful gases. Adequate ventilation helps prevent the buildup of flammable gases and ensures a safer working condition.
It is important to be cautious and aware of your surroundings during the installation. Keep a clear workspace to avoid trips and falls, and ensure that all tools and materials are securely stored to prevent accidental contact. Always follow the manufacturer's guidelines and safety data sheets for the specific products you are using. By taking these safety measures, you can minimize risks and ensure a successful and secure installation process. Remember, safety should always be the top priority when dealing with fuel systems.
Understanding Fuel Pump and Injection Line Connections
You may want to see also
Frequently asked questions
Push-to-Connect fittings are designed to make fuel line installations quick and secure. They eliminate the need for traditional methods like soldering or welding, which can be time-consuming and may not always provide a tight seal. PTC fittings offer a reliable and cost-effective solution for connecting fuel lines to fuel tanks, pumps, or other components in automotive or industrial applications.
Before installing a Push-to-Connect fitting, ensure the fuel line is clean and free of any debris or contaminants. Use a fuel line cleaner or a mild detergent to wash the line, then rinse and dry it thoroughly. The fitting should also be free of any dirt or old sealant. It's important to follow the manufacturer's guidelines for the specific fuel line and fitting you are using to ensure compatibility and optimal performance.
Yes, Push-to-Connect fittings are designed for multiple installations and can be reused. However, it's crucial to inspect the fittings for any signs of damage or wear before reuse. Check for cracks, brittleness, or any debris that might affect the seal. If the fittings appear to be in good condition, they can be reused with proper preparation and cleaning as mentioned in the previous answer. Always ensure that the fuel line and fittings are compatible with the system's requirements.