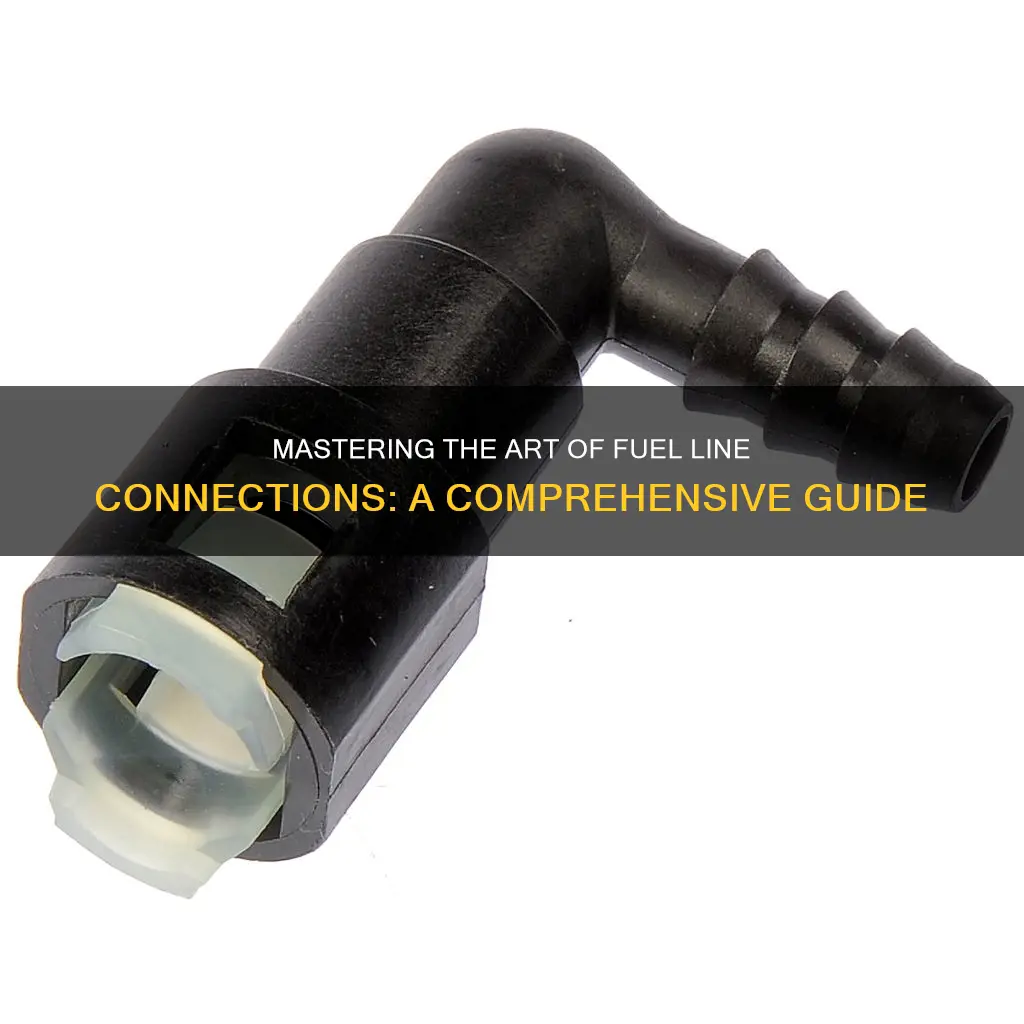
Connecting to 1.4-inch fuel lines requires careful preparation and adherence to safety guidelines. This process involves ensuring a secure and leak-free connection to deliver fuel efficiently to engines. It's essential to use the right tools and materials, such as fuel line connectors, fittings, and seals, to ensure a tight fit. Proper alignment and sealing are crucial to prevent fuel leaks and ensure optimal engine performance. Understanding the specific requirements of your fuel system and following manufacturer guidelines will help you achieve a successful and safe connection.
What You'll Learn
- Fuel Line Materials: Choose appropriate materials like steel, brass, or rubber for durability and compatibility
- Fitting Selection: Opt for fittings like quick-connects, clips, or screws for secure connections
- Pressure Testing: Ensure lines are leak-free by testing with compressed air or fuel at recommended pressures
- Routing Techniques: Route lines away from heat sources and sharp edges for safety and longevity
- Maintenance Tips: Regularly inspect and replace lines to prevent clogs, corrosion, and fuel contamination
Fuel Line Materials: Choose appropriate materials like steel, brass, or rubber for durability and compatibility
When it comes to working with 1/4-inch fuel lines, selecting the right materials is crucial for ensuring a reliable and safe fuel system. The choice of material depends on various factors, including the specific application, environmental conditions, and the type of fuel being used. Here's a detailed guide on the appropriate materials for your fuel lines:
Steel: One of the most common and durable materials for fuel lines is steel. It offers excellent strength and resistance to corrosion, making it ideal for high-pressure applications and harsh environments. Steel fuel lines are often used in racing cars, heavy-duty machinery, and marine vessels where durability is essential. The material's rigidity provides structural support, ensuring the lines can withstand vibrations and movements without compromising performance. However, steel can be more rigid and less flexible compared to other options, so it might not be the best choice for tight spaces or complex routing.
Brass: Brass is another popular choice for fuel lines, particularly in applications where a balance between strength and flexibility is required. It is known for its excellent corrosion resistance, making it suitable for both gasoline and diesel fuel systems. Brass lines are often used in automotive applications, especially for older vehicles or classic car restoration projects. The material's flexibility allows for easier installation and routing, ensuring a neat and secure connection. Additionally, brass has a smooth interior surface, which can help reduce fuel flow restrictions and improve overall performance.
Rubber (Fluorocarbon or EPDM): Rubber, specifically fluorocarbon or EPDM (Ethylene Propylene Diene Monomer) rubber, is a lightweight and flexible material commonly used for fuel lines. It is highly resistant to fuel degradation and offers excellent flexibility, making it easy to bend and route around various engine components. Rubber fuel lines are often used in general automotive applications, lawn care equipment, and small engines. The material's flexibility ensures a secure connection without adding excessive rigidity to the system. However, rubber may not be suitable for high-pressure applications or extreme temperatures, so it's essential to consider the specific requirements of your project.
When choosing the material, consider factors such as the operating temperature range, fuel type, pressure requirements, and the overall environment in which the fuel lines will be used. Each material has its advantages and trade-offs, so selecting the right one will ensure a long-lasting and efficient fuel system. Remember to consult manufacturer guidelines and seek professional advice when necessary to ensure proper installation and compatibility.
WRX Fuel Line: Discover the Perfect OEM Size
You may want to see also
Fitting Selection: Opt for fittings like quick-connects, clips, or screws for secure connections
When it comes to connecting 1/4-inch fuel lines, the choice of fittings is crucial for a secure and reliable setup. Here's a detailed guide on why and how to select the right fittings for your fuel line connections:
Quick-Connect Fittings: These are an excellent choice for their ease of use and convenience. Quick-connect fittings typically feature a male end with a threaded or bayonet-style connection, which is then inserted into a female port on the fuel line. They are designed to provide a tight seal without the need for tools, making them ideal for temporary or DIY installations. Look for fittings with a robust construction to ensure they can withstand fuel pressure and temperature changes.
Clips or Compression Fittings: For a more permanent and secure connection, compression fittings are a popular option. These fittings use a combination of clips or compression nuts and sleeves to grip the fuel line tightly. The process involves inserting the fuel line into the fitting, then tightening the compression nut or clip to create a secure hold. This method provides excellent sealing and is less prone to leaks compared to quick-connects. Ensure you follow the manufacturer's instructions for the correct torque settings to avoid over-tightening, which can damage the fuel line.
Screw Fittings: Another reliable option is screw fittings, which offer a tight seal using screws to secure the fuel line in place. These fittings are often used in applications where quick disassembly is required, such as in racing or performance tuning. The process involves threading the fuel line into the fitting and tightening the screws to create a secure connection. While they may require more effort to install, screw fittings are known for their durability and ability to withstand high-pressure environments.
When selecting fittings, consider factors such as fuel type, pressure, and temperature ranges to ensure compatibility. Additionally, choose fittings that are designed for the specific fuel line material you are working with, as different materials may require unique sealing mechanisms. Properly prepared fuel lines and fittings, along with the right choice of fittings, will ensure a secure and efficient fuel supply system.
Fuel Line Valves: Direction Matters for Effective Shut-Off
You may want to see also
Pressure Testing: Ensure lines are leak-free by testing with compressed air or fuel at recommended pressures
When working with 1/4-inch fuel lines, ensuring a secure and leak-free connection is crucial to prevent fuel leaks and potential safety hazards. Pressure testing is a critical step in the installation process to verify the integrity of the connections. Here's a detailed guide on how to perform this test effectively:
Compressed Air Testing:
Start by using compressed air to test the fuel lines for any leaks. This method is suitable for both new installations and repairs. Begin by connecting a suitable air compressor to the fuel line's pressure regulator. Set the air pressure to a recommended level, typically around 100-150 psi, which is higher than the operating pressure of the fuel system. Ensure the air supply is regulated to maintain a steady pressure. Now, inspect the entire length of the fuel line, paying close attention to connections, fittings, and any potential leak points. Listen for hissing sounds or feel for any signs of air escaping, indicating a possible leak. If you detect any leaks, immediately shut off the air supply and address the issue by tightening connections or replacing damaged components.
Fuel Pressure Testing:
For a more comprehensive test, you can use fuel pressure to simulate real-world conditions. This method is especially important when dealing with high-pressure fuel systems. Connect a fuel pressure gauge to the fuel line, ensuring it is compatible with the fuel type (gasoline or diesel). Adjust the fuel pump to deliver the recommended pressure, which can vary depending on the engine and fuel system design. As with the air test, inspect the fuel line for any signs of leakage. Look for fuel seeping around connections, fittings, or where the line attaches to the fuel tank or engine. If leaks are found, tighten connections or replace components as necessary. Remember to drain the fuel system of any pressure after testing to prevent accidental fuel spills.
Recommended Pressures:
It's essential to consult the vehicle's manual or manufacturer guidelines for the specific pressure requirements of your fuel system. Different engines and fuel setups have unique pressure needs. Using the correct pressure during testing ensures accurate results and helps identify potential issues. For instance, a gasoline engine might require a pressure of 6-8 psi, while a diesel engine could need 30-50 psi. Always start with the lower end of the recommended range and gradually increase pressure if needed, allowing time to identify any leaks.
Safety Precautions:
When performing pressure tests, always prioritize safety. Wear appropriate personal protective equipment, such as safety goggles and gloves, to protect against potential fuel or air leaks. Ensure the work area is well-ventilated, especially when dealing with high-pressure fuel systems. Keep a fire extinguisher nearby as a precaution, especially when using compressed air or fuel. Additionally, always disconnect the fuel source before making any adjustments to the fuel lines to avoid accidental fuel release.
By following these pressure testing procedures, you can ensure that your 1/4-inch fuel lines are securely connected and leak-free, contributing to a safe and efficient fuel delivery system. Remember, proper installation and regular maintenance are key to avoiding costly repairs and potential engine damage caused by fuel leaks.
Diagnosing Clogged Fuel Lines: Signs and Solutions
You may want to see also
Routing Techniques: Route lines away from heat sources and sharp edges for safety and longevity
When connecting 1/4-inch fuel lines, proper routing is crucial for ensuring the safety and longevity of the system. One essential technique is to route the lines away from heat sources, such as exhaust manifolds, engine blocks, and other hot components. Heat can cause fuel lines to expand and contract rapidly, leading to potential damage, cracks, or even fuel leaks over time. By keeping the fuel lines at a safe distance from these heat sources, you minimize the risk of thermal stress and ensure the system's reliability.
Additionally, it is imperative to route the fuel lines away from sharp edges, protruding objects, and potential impact zones. Fuel lines should never be run along sharp corners or edges of panels, as this can lead to chafing, damage, or even complete rupture. A good practice is to use protective sleeves or tubing to shield the fuel lines from sharp edges, especially in areas where the lines pass through body panels or near moving parts. This simple measure significantly reduces the chances of accidental damage during the vehicle's operation.
To achieve this, consider the layout of the vehicle's interior and exterior. Plan the route of the fuel lines to avoid any sharp turns or tight spaces that could restrict movement or cause damage. It is often best to route the lines in a straight line or with gentle curves, ensuring they are not kinked or twisted, as this can lead to reduced flow and potential blockages. By maintaining a consistent and smooth path, you ensure the fuel lines remain flexible and functional over time.
Furthermore, when routing the fuel lines, it is essential to consider the accessibility for future maintenance. Avoid routes that would make it difficult to access and service the fuel lines, such as under carpets or in confined spaces. Proper routing should allow for easy inspection and potential replacement without extensive disassembly of the vehicle. This consideration is vital for long-term maintenance and the overall health of the fuel system.
In summary, when connecting 1/4-inch fuel lines, always prioritize safety and longevity by routing them away from heat sources and sharp edges. This simple yet critical step ensures the system's reliability, prevents damage, and minimizes the risk of fuel leaks. By following these routing techniques, you can create a robust and efficient fuel system that will serve your vehicle well over its lifetime.
Unleash the Power: Milwaukee's Fuel Line Revolution
You may want to see also
Maintenance Tips: Regularly inspect and replace lines to prevent clogs, corrosion, and fuel contamination
When it comes to maintaining your fuel system, regular inspection and timely replacement of 1/4-inch fuel lines are crucial. These lines are susceptible to various issues that can compromise their functionality and lead to more significant problems. Here's a comprehensive guide on why and how to keep your fuel lines in top condition.
Inspecting for Clogs: Fuel lines can become clogged over time due to the accumulation of dirt, debris, or even water. This is especially common in older vehicles or those with poorly maintained fuel systems. To inspect for clogs, start by checking for any visible signs of contamination, such as dirt or rust particles in the fuel tank or lines. You can use a fuel filter to catch any debris, and if it becomes clogged, it's a clear indicator of a larger issue. Regularly replacing the fuel filter as per the manufacturer's schedule can help prevent clogs and ensure optimal fuel flow.
Preventing Corrosion: Corrosion is a common enemy of fuel lines, particularly those made of metal. Over time, moisture absorption and the presence of fuel can lead to rust formation, which may result in leaks or reduced fuel pressure. To mitigate this, ensure that all fuel lines are properly insulated and sealed. Regularly check for any signs of corrosion, especially at the connections and bends. Applying a corrosion inhibitor or a protective coating can provide an extra layer of defense against rust.
Replacing Fuel Lines: Given the critical role of fuel lines in delivering fuel to the engine, it's essential to replace them when necessary. Wear and tear, clogs, or damage from accidents can render lines ineffective. Look out for signs like fuel leaks, engine misfires, or reduced performance, which may indicate a failing fuel line. When replacing, ensure you use high-quality replacement lines that meet or exceed the original specifications. Properly secure and route the new lines to avoid damage and ensure a tight connection.
Regular Maintenance Schedule: Establishing a regular maintenance routine is key to preventing major issues. Schedule inspections and replacements at recommended intervals, often aligned with your vehicle's service schedule. This proactive approach can save you from unexpected breakdowns and costly repairs. Additionally, consider using a fuel system cleaner to maintain the health of the entire fuel delivery system, including the lines.
By following these maintenance tips, you can ensure that your 1/4-inch fuel lines remain in excellent condition, providing reliable fuel delivery to your engine. Regular care will help prevent clogs, corrosion, and contamination, ultimately contributing to better engine performance and longevity.
Understanding the Mantis Fuel Line: Black Fuel Line Dimensions
You may want to see also
Frequently asked questions
To connect 1.4-inch fuel lines, you will typically need a fuel line coupling or fitting that matches the size of your fuel line. It's essential to have a fuel line crimping tool to ensure a secure and leak-tight connection. Additionally, you might require a fuel line cleaner to prepare the lines before assembly.
Start by cleaning the ends of the fuel lines to remove any dirt or debris. Then, insert the fuel line into the coupling, ensuring it is aligned correctly. Use the crimping tool to apply pressure and create a secure connection. Make sure the connection is tight and there are no gaps or leaks. It's a good practice to test the connection by applying pressure and checking for any signs of leakage.
It's crucial to use fuel line couplings specifically designed for the 1.4-inch size to ensure compatibility and a proper fit. Different types of couplings are available, such as compression, quick-connect, or barbed fittings. Choose the coupling that best suits your application and fuel system requirements. Always refer to the manufacturer's guidelines or consult a professional for the most suitable coupling type.