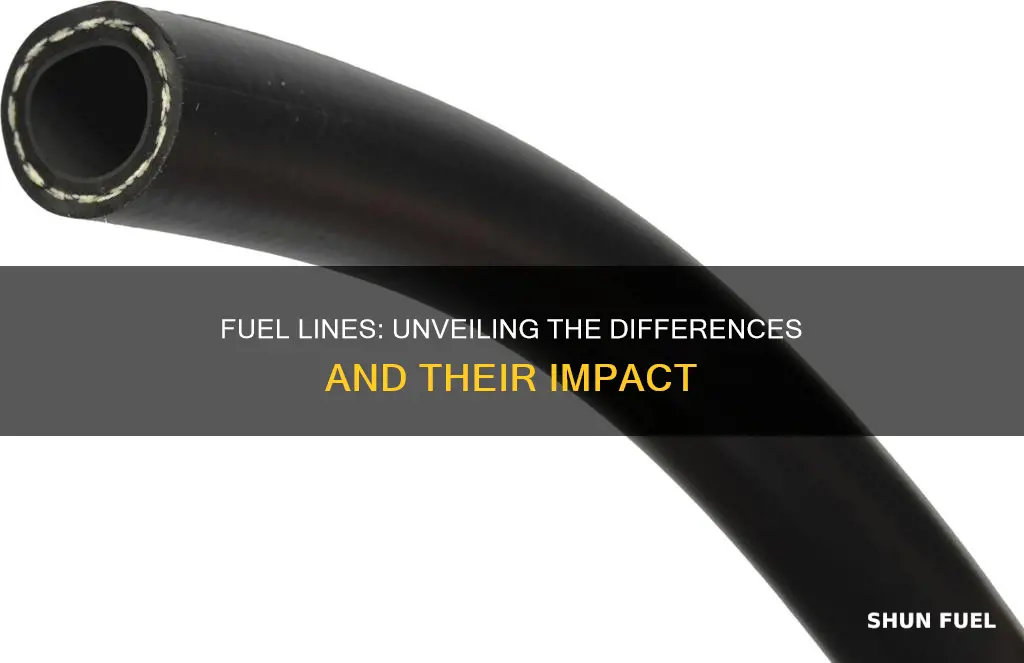
The question of whether there is a difference in fuel lines is an important one, especially for vehicle owners and mechanics. Fuel lines are a critical component of any engine, responsible for delivering fuel from the tank to the engine's intake system. While the primary function of fuel lines is to transport fuel, there are variations in design, material, and construction that can impact performance, durability, and safety. Understanding these differences is crucial for maintaining and optimizing vehicle performance, ensuring efficient fuel delivery, and preventing potential issues such as fuel leaks or engine misfires. This introduction sets the stage for a detailed exploration of the various factors that distinguish different types of fuel lines.
What You'll Learn
- Fuel Line Material: Different materials offer varying durability and resistance to corrosion
- Fuel Line Diameter: Thicker lines provide higher flow rates and pressure, crucial for performance
- Fuel Line Routing: Proper routing prevents kinking and ensures consistent fuel delivery
- Fuel Line Length: Longer lines may require additional components for filtration and pressure regulation
- Fuel Line Compatibility: Using the correct type ensures compatibility with the fuel system and engine
Fuel Line Material: Different materials offer varying durability and resistance to corrosion
When it comes to fuel lines, the choice of material is crucial as it directly impacts the performance and longevity of the system. Different materials offer varying levels of durability and resistance to corrosion, which are essential factors to consider for optimal fuel delivery in vehicles. The primary purpose of fuel lines is to transport gasoline or diesel from the tank to the engine, and the material used plays a significant role in ensuring a reliable and efficient process.
One of the most common materials for fuel lines is rubber, which has been traditionally used due to its flexibility and ease of installation. Rubber fuel lines are known for their ability to absorb vibrations and reduce engine noise, providing a smooth fuel flow. However, rubber is susceptible to degradation over time, especially when exposed to certain chemicals in fuel, leading to cracks and leaks. This material is less resistant to corrosion and may not be suitable for long-term use in harsh environments.
In contrast, synthetic rubber compounds, such as EPDM (Ethylene Propylene Diene Monomer) rubber, offer improved durability and resistance to fuel-related chemicals. These compounds are designed to withstand the corrosive effects of gasoline and diesel, ensuring a longer lifespan for the fuel lines. EPDM rubber fuel lines are more flexible and can handle temperature variations, making them a popular choice for modern vehicles.
Another popular material is braided steel, which provides excellent resistance to corrosion and extreme temperatures. Steel fuel lines are known for their strength and rigidity, making them ideal for high-performance vehicles or those operating in demanding conditions. The braided design offers flexibility while maintaining structural integrity, ensuring a reliable fuel supply. However, steel lines may be more rigid and less flexible compared to rubber, which could be a consideration for certain vehicle designs.
Additionally, some fuel lines use a combination of materials, such as a steel outer layer and a synthetic inner layer. This design provides the benefits of both materials, offering the flexibility and corrosion resistance of synthetic rubber with the strength and temperature tolerance of steel. Such hybrid fuel lines are often used in high-performance or racing applications where durability and reliability are critical.
In summary, the material of fuel lines significantly influences their performance and longevity. Rubber, synthetic rubber, braided steel, and hybrid combinations each offer unique advantages in terms of flexibility, corrosion resistance, and temperature tolerance. Choosing the right material ensures a reliable fuel supply, reduces the risk of leaks or damage, and ultimately contributes to the overall efficiency and safety of the vehicle's fuel system.
Powerful Engine, Right Fuel Line? Size Matters!
You may want to see also
Fuel Line Diameter: Thicker lines provide higher flow rates and pressure, crucial for performance
The diameter of the fuel line is a critical factor in determining the performance and efficiency of a vehicle's fuel delivery system. Thicker fuel lines, typically with a larger diameter, offer several advantages that can significantly impact the overall driving experience. One of the primary benefits is the ability to handle higher flow rates of fuel. As engines demand more fuel to meet increased power requirements, a larger diameter fuel line becomes essential. This thicker line can accommodate a greater volume of fuel, ensuring that the engine receives the required amount of fuel at the right pressure, even under high-load conditions.
In high-performance vehicles, where engine power and responsiveness are paramount, thicker fuel lines play a vital role. These lines can maintain a consistent fuel pressure, which is crucial for precise fuel injection and combustion. With a larger diameter, the fuel line reduces the restriction in the fuel flow path, allowing for a more efficient and rapid delivery of fuel to the engine. This results in improved engine performance, faster response times, and better overall power delivery.
The pressure within the fuel system is another critical aspect influenced by fuel line diameter. Thicker lines can withstand higher pressure differentials, which is essential for maintaining optimal fuel pressure throughout the system. This is particularly important in high-performance applications where engines operate at elevated RPMs and require a precise fuel-air mixture for efficient combustion. By using thicker fuel lines, the risk of fuel pressure drop is minimized, ensuring that the engine receives the necessary fuel pressure for optimal performance.
Furthermore, thicker fuel lines contribute to the overall reliability and longevity of the fuel system. With a larger diameter, these lines are less prone to restrictions and blockages caused by contaminants or fuel system wear. This increased durability ensures that the fuel system can handle the demands of high-performance driving without compromising on performance or safety. Additionally, thicker lines can reduce the likelihood of fuel leaks, providing a more secure and efficient fuel delivery system.
In summary, the diameter of the fuel line is a critical consideration for vehicle performance and efficiency. Thicker fuel lines offer higher flow rates, improved pressure maintenance, and enhanced reliability, making them essential for high-performance engines. By investing in thicker fuel lines, vehicle owners can ensure that their engines receive the necessary fuel for optimal power delivery and a responsive driving experience. This simple upgrade can significantly impact the overall performance and longevity of a vehicle's fuel system.
Mini Cooper's Torque Stage: Unlocking Power with Fuel Lines
You may want to see also
Fuel Line Routing: Proper routing prevents kinking and ensures consistent fuel delivery
Fuel line routing is a critical aspect of vehicle maintenance that often goes overlooked, but it plays a significant role in ensuring optimal performance and longevity of the fuel system. Proper routing is essential to prevent kinking, which can lead to inconsistent fuel delivery and potential engine issues. Here's an in-depth look at why and how to route fuel lines correctly:
Understanding the Importance of Fuel Line Routing:
Fuel lines are responsible for transporting fuel from the tank to the engine, and their placement directly impacts the efficiency and reliability of the fuel system. Kinking occurs when the fuel lines are bent, twisted, or routed in a way that creates a sharp bend or fold. This can restrict fuel flow, leading to reduced power, poor engine performance, and even potential engine damage over time. Proper routing ensures a smooth and consistent path for the fuel, allowing it to flow freely to the engine.
Key Considerations for Fuel Line Routing:
- Flexibility and Movement: Fuel lines should be routed in a way that allows for natural movement and expansion. This is crucial for vehicles with suspension systems that can move the fuel tank and engine during operation. Avoid tight bends or fixed routes that restrict movement, as this can lead to kinking over time.
- Closeness to the Ground: In many vehicles, the fuel lines are routed close to the ground. This design choice ensures that the fuel lines are protected from damage by road debris and potential impacts. However, it also means that the lines can be more susceptible to kinking, especially if the vehicle has a low ground clearance.
- Avoidance of Heat Sources: Fuel lines should be kept away from heat sources like exhaust systems, engine components, and under-hood components. High temperatures can cause the fuel lines to degrade and become brittle, leading to potential leaks and fuel contamination.
- Secure Mounting: Properly secure the fuel lines to prevent excessive movement. Use appropriate mounting points and brackets to ensure the lines remain in place and do not rub against other components, which could cause damage or wear.
Best Practices for Fuel Line Routing:
- Route the fuel lines as close to the fuel tank as possible to minimize the length of the line, reducing the potential for kinking.
- Use flexible fuel lines with a suitable diameter to accommodate the fuel flow rate and ensure smooth bending.
- Consider using a fuel line protector or shield to guard against sharp edges and potential damage.
- Regularly inspect the fuel lines for any signs of wear, damage, or kinking, especially in areas where the lines are more susceptible to impact or heat.
By implementing these routing practices, you can ensure that your fuel lines are properly protected, preventing kinking and maintaining a consistent fuel supply to the engine. This, in turn, contributes to improved engine performance, fuel efficiency, and overall vehicle reliability. Remember, proper fuel line routing is a simple yet crucial maintenance task that can save you from potential headaches and costly repairs in the long run.
Goped Fuel Lines: Unlocking the Mystery of Dual Lines
You may want to see also
Fuel Line Length: Longer lines may require additional components for filtration and pressure regulation
When considering fuel lines for your vehicle, the length of the line is an important factor that can impact performance and maintenance. Longer fuel lines may seem like an advantage, providing more flexibility and potentially reducing the risk of damage from minor impacts. However, there are several considerations to keep in mind.
One of the primary concerns with longer fuel lines is the potential for increased fuel contamination. As the line extends, it creates more surface area exposed to the environment. This can lead to the accumulation of dirt, debris, and moisture, which can contaminate the fuel and potentially cause performance issues. To mitigate this, longer fuel lines often require additional filtration systems to ensure clean fuel delivery to the engine. These filters can be located at various points along the line, including at the fuel pump and near the engine.
Another critical aspect of longer fuel lines is pressure regulation. Fuel lines need to maintain a consistent pressure to ensure optimal engine performance. Longer lines can introduce pressure drops, especially when the vehicle is stationary or during rapid acceleration. To address this, pressure regulators or pressure relief valves may be installed along the fuel line to maintain the required pressure levels. These components are designed to adjust the pressure as needed, ensuring a steady supply of fuel to the engine.
In some cases, longer fuel lines might also require specialized fittings and connectors to ensure a secure and leak-free connection. These fittings are often made of high-quality materials that can withstand the pressure and temperature fluctuations associated with fuel systems. Proper installation and regular maintenance of these connections are essential to prevent fuel leaks and ensure the overall reliability of the fuel system.
Additionally, longer fuel lines may also impact the vehicle's aesthetics and under-the-hood organization. Longer lines can create more space under the vehicle, allowing for easier maintenance and potential upgrades. However, careful planning is required to ensure that the fuel lines are routed in a way that minimizes clutter and potential hazards.
In summary, while longer fuel lines can offer some benefits in terms of flexibility, they also introduce challenges related to fuel contamination, pressure regulation, and component requirements. It is essential to consider these factors when designing or modifying a fuel system to ensure optimal performance and longevity. Proper installation, including the use of additional filtration and pressure regulation components, can help mitigate the potential issues associated with longer fuel lines.
Choosing the Right Fuel Line for Small Gas Engines: A Guide
You may want to see also
Fuel Line Compatibility: Using the correct type ensures compatibility with the fuel system and engine
When it comes to vehicle maintenance, one of the critical components that often requires attention is the fuel line. The fuel line is responsible for transporting gasoline or diesel from the tank to the engine, and using the correct type of fuel line is essential for ensuring compatibility with the fuel system and engine. This is because different types of fuel lines have varying materials, diameters, and lengths, which can impact their performance and longevity.
The primary concern with fuel line compatibility is the potential for contamination or degradation of the fuel. If the fuel line is not compatible with the type of fuel it carries, it can lead to fuel contamination, which can cause engine misfires, reduced performance, and even permanent damage. For example, using a fuel line designed for gasoline in a diesel engine or vice versa can result in the introduction of water or impurities into the fuel, leading to engine issues.
To ensure compatibility, it is crucial to understand the specifications of your vehicle's fuel system and engine. Automotive manuals and manufacturer guidelines provide detailed information about the recommended fuel line types, including their dimensions and materials. These specifications are carefully designed to match the engine's requirements, ensuring optimal fuel delivery and combustion. Using the correct fuel line ensures that the fuel is transported efficiently without any loss or contamination, which is vital for maintaining engine performance and reliability.
In addition to compatibility, the material of the fuel line is another critical factor. Common materials used for fuel lines include rubber, vinyl, and braided steel. Rubber fuel lines are known for their flexibility and resistance to fuel degradation, making them suitable for long-term use. Vinyl fuel lines, on the other hand, offer excellent chemical resistance and are often used in high-temperature environments. Braided steel fuel lines provide superior durability and are less susceptible to damage from fuel contaminants. The choice of material depends on the specific needs of the fuel system and engine, as well as environmental factors.
When replacing or upgrading fuel lines, it is imperative to choose the correct type that matches the original equipment manufacturer's (OEM) specifications. This ensures that the fuel line will seamlessly integrate into the fuel system, providing reliable performance. Attempting to use an incompatible fuel line can lead to fuel leaks, engine performance issues, and potential safety hazards. Therefore, always consult the vehicle's manual or seek professional advice to determine the appropriate fuel line type for your specific make and model.
Mastering Motorcycle Fuel Lines: A Step-by-Step Guide to Tearing and Installing
You may want to see also
Frequently asked questions
The main distinction lies in their flexibility and durability. Rubber fuel lines are more flexible, making them easier to route through tight spaces in engines. However, they may degrade over time due to fuel exposure, leading to potential leaks. Braided fuel lines, on the other hand, offer superior durability and resistance to fuel degradation, ensuring a longer-lasting solution.
The choice of material for fuel lines can influence engine performance. Braided steel or stainless steel fuel lines provide excellent heat resistance, which is crucial in high-temperature engine environments. This ensures that the fuel remains stable and doesn't degrade, resulting in improved engine performance and efficiency.
Yes, regular maintenance is essential to ensure the longevity of fuel lines. It is recommended to inspect fuel lines periodically for any signs of damage, cracks, or leaks. Cleaning the fuel lines to remove contaminants and using fuel system additives can also help maintain optimal performance.
Absolutely. The quality and compatibility of fuel lines can impact fuel efficiency. Clogged or damaged fuel lines may restrict fuel flow, leading to reduced power and fuel economy. Using high-quality, compatible fuel lines ensures efficient fuel delivery to the engine, optimizing performance and fuel consumption.
Several indicators suggest that a fuel line replacement is necessary. These include fuel leaks, engine misfires, reduced power, and unusual noises from the fuel system. If you notice any of these symptoms, it's advisable to inspect the fuel lines for damage and consider replacing them to restore engine performance.