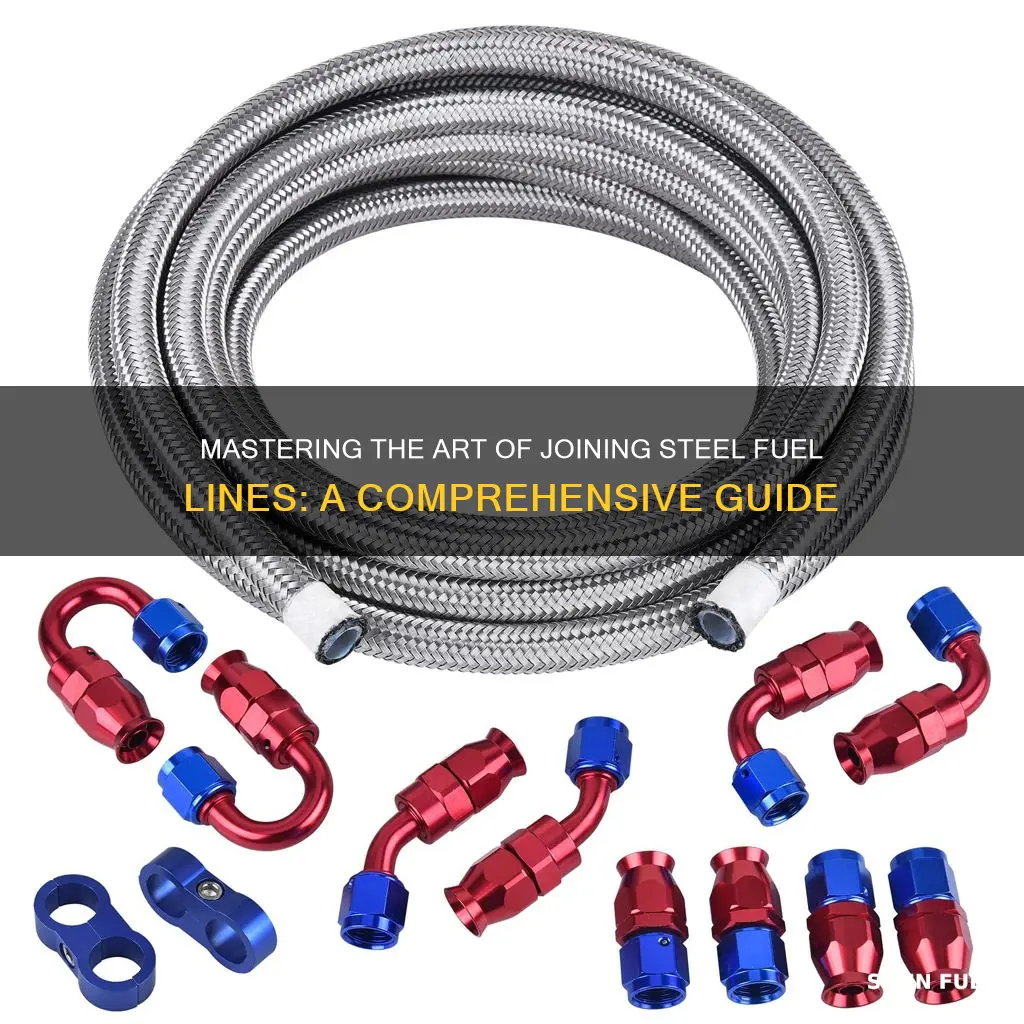
Joining steel fuel lines requires precision and adherence to safety standards. The process involves several steps, including cleaning and preparing the ends of the lines, using the appropriate welding or joining techniques, and ensuring the connections are secure and leak-free. It is crucial to follow manufacturer guidelines and industry best practices to guarantee the integrity and safety of the fuel system. This guide will provide a comprehensive overview of the methods and considerations for successfully joining steel fuel lines.
What You'll Learn
- Prepare Tools: Gather necessary tools like pipe cutters, files, and flux
- Measure and Mark: Accurately measure and mark the steel fuel line for cutting
- Cut and Deburr: Use a pipe cutter to cut the line, then deburr the edges
- Prepare Fittings: Clean and prepare fittings with flux for soldering or welding
- Connect and Test: Securely join the line to fittings, then test for leaks
Prepare Tools: Gather necessary tools like pipe cutters, files, and flux
When preparing to join steel fuel lines, having the right tools is essential to ensure a secure and reliable connection. Here's a detailed guide on gathering the necessary equipment:
Pipe Cutters: These are fundamental tools for any plumbing or fuel line work. You'll need a high-quality pipe cutter that can handle the thickness of your steel fuel lines. Look for a model with adjustable cutting wheels to accommodate different pipe sizes. A good pipe cutter will ensure clean, precise cuts, allowing for a tight and leak-free joint.
Files: While pipe cutters are crucial, files play a supporting role in preparing the pipe ends. Files are used to smooth and refine the cut edges, removing any burrs or sharp edges that could cause leaks or damage during the joining process. Get a set of files with various grits to ensure you can work on different pipe thicknesses and materials.
Flux: Flux is a chemical compound that helps remove oxidation and corrosion from the pipe surfaces, creating a clean and smooth interface for the joint. It also acts as a lubricant, making it easier to insert the pipes into the fitting. When choosing flux, opt for a product specifically designed for steel fuel lines to ensure compatibility and effectiveness.
Additionally, consider other general tools like sandpaper, safety gloves, and safety goggles. Sandpaper can be used for initial surface preparation, and gloves and goggles protect you during the cutting and filing process. Having these tools ready will ensure you're well-equipped to handle the physical aspects of joining the steel fuel lines.
Mastering Fuel Line Separation: A Step-by-Step Guide
You may want to see also
Measure and Mark: Accurately measure and mark the steel fuel line for cutting
Before you begin the process of joining steel fuel lines, it's crucial to ensure that you have accurately measured and marked the line for cutting. This step is essential to guarantee a precise and secure connection. Here's a detailed guide on how to measure and mark the steel fuel line:
Step 1: Gather the Necessary Tools
Start by gathering the required tools for the task. You will need a tape measure or a ruler, a pencil or a marker, and a straight edge or a square. These tools will help you take precise measurements and make accurate marks. Ensure that the tape measure is calibrated and can measure in the appropriate units (e.g., inches or centimeters).
Step 2: Measure the Required Length
Locate the section of the steel fuel line where you plan to make the connection. Use the tape measure to determine the exact length required for the new section. Measure from the starting point of the line to the desired connection point. Take note of this measurement, as it will guide the cutting process. Double-check the measurement to ensure accuracy, especially if the line has any bends or curves.
Step 3: Mark the Cutting Line
Once you have the measurement, it's time to mark the line for cutting. Place the straight edge or square along the fuel line, aligning it with the measured length. Use the pencil or marker to draw a clear and straight line along the edge of the straight edge. Ensure that the line is level and straight, as this will guide the cutting process and ensure a clean cut. Make multiple marks if the line is long, spacing them evenly to provide a clear indication of the cutting points.
Step 4: Verify the Marks
After marking the cutting line, carefully review the marks to ensure they are accurate and aligned with your measurement. Check that the marks are straight and evenly spaced, especially if you are joining multiple sections of fuel lines. Any discrepancies in the marks could lead to an improper connection. If everything looks correct, you are ready to proceed to the cutting step, ensuring that your preparation is thorough and precise.
Accurate measurement and marking are fundamental to the success of joining steel fuel lines. This process ensures that the new section fits perfectly, promoting a secure and reliable connection. By following these steps, you can achieve professional results and minimize the risk of errors during the joining process.
Chevy Fuel Line Reversal: A Step-by-Step Guide
You may want to see also
Cut and Deburr: Use a pipe cutter to cut the line, then deburr the edges
When joining steel fuel lines, ensuring a clean and precise cut is crucial for a secure and reliable connection. Here's a step-by-step guide on how to cut and deburr the fuel lines effectively:
Cutting the Line:
Start by identifying the desired length of the fuel line. Use a pipe cutter, which is a specialized tool designed for cutting metal pipes. Position the cutter at the marked spot on the line and apply firm pressure. The cutter will create a clean, straight cut, ensuring minimal material is removed. It's important to use the right force to avoid crushing the metal or creating uneven edges. After cutting, inspect the ends to ensure they are straight and free of any burrs.
Deburring the Edges:
Burrs are sharp, protruding edges that can cause damage or injury during the assembly process. To remove these, you can use a deburring tool or a file. Start by gently filing the cut edges in a circular motion, following the natural curve of the pipe. Work along the entire length of the cut, ensuring you smooth out any rough spots. The goal is to create a smooth, rounded surface that is free of sharp angles. For smaller fuel lines, a fine-grit sandpaper can also be used to achieve a similar effect. Take care not to over-file, as it may weaken the metal.
Deburring is a critical step to ensure the safety and functionality of the fuel line connection. It prevents the formation of sharp edges that could lead to leaks or damage during installation. By taking the time to cut and deburr the line properly, you'll create a solid foundation for a successful join, ensuring the fuel lines are ready for efficient and safe use. Remember, precision and attention to detail are key when working with metal pipes.
Dodge Hellcat Fuel Line Sizing: A Comprehensive Guide
You may want to see also
Prepare Fittings: Clean and prepare fittings with flux for soldering or welding
When joining steel fuel lines, proper preparation of the fittings is crucial to ensure a secure and leak-free connection. This process involves cleaning the fittings and applying flux, which is a chemical compound that helps facilitate the soldering or welding process. Here's a step-by-step guide on how to prepare the fittings effectively:
Cleaning the Fittings: Begin by thoroughly cleaning the steel fuel lines and fittings. Over time, fuel lines can accumulate dirt, grease, and debris, which can interfere with the joining process. Use a wire brush or a specialized cleaning tool to remove any contaminants from the surfaces of the fittings. Pay close attention to the threads and any crevices where dirt might accumulate. It is essential to ensure that the fittings are free from any debris or residue that could hinder the joining process.
Rinsing and Drying: After cleaning, rinse the fittings with a suitable solvent or water to remove any remaining dirt or cleaning agents. Ensure that all traces of cleaning products are washed away, as they can leave a residue that may affect the bonding process. Once rinsed, allow the fittings to air dry completely. You can use a soft cloth or towel to speed up the drying process and ensure there is no moisture left on the surfaces.
Flux Application: Flux is a critical component in joining steel fuel lines. It serves multiple purposes: it removes oxidation, improves solder flow, and acts as a lubricant during the joining process. There are different types of flux available, including acid, rosin, and water-soluble fluxes. Choose a flux suitable for the specific joining method you will use (soldering or welding). Apply a small amount of flux to the threads and any other surfaces that will be in contact during the joint. Ensure an even coating, being careful not to overapply, as excess flux can lead to issues during the soldering or welding process.
Preparation for Soldering or Welding: With the fittings now clean and fluxed, they are ready for the chosen joining method. If soldering, ensure you have the appropriate soldering iron temperature and a suitable solder alloy. For welding, prepare your welding equipment and ensure the fittings are positioned correctly for the welding process. Proper preparation at this stage will significantly contribute to the success and longevity of the fuel line connection.
Mysterious Engine Issues: Uncover Air in Diesel Fuel Line Symptoms
You may want to see also
Connect and Test: Securely join the line to fittings, then test for leaks
When joining steel fuel lines, ensuring a secure and leak-free connection is crucial to prevent fuel leaks and potential hazards. Here's a step-by-step guide on how to connect the line to fittings and test for any potential issues:
Connection Process:
- Prepare the Materials: Ensure you have the correct fittings, such as unions, elbows, or tees, specifically designed for steel fuel lines. Check the compatibility of the fittings with the fuel line material. Gather the necessary tools, including wrenches, pipe thread seal tape, and a fuel line cutter or shears.
- Clean and Prepare the Fittings: Remove any dirt or debris from the fittings and fuel line ends. Use a wire brush or a cleaning tool to ensure a smooth and clean surface for the connection. This step is essential to create a tight seal.
- Apply Thread Seal Tape or Compound: Wrap the male threads of the fitting and the fuel line with thread seal tape, ensuring full coverage. Alternatively, you can use a thread sealing compound, following the manufacturer's instructions for application. This step prevents leaks and provides a reliable connection.
- Connect the Fittings: Insert the fuel line into the fitting, ensuring it is aligned correctly. Tighten the fitting using the appropriate wrench, following the manufacturer's torque specifications. Over-tightening can damage the fuel line, so be cautious and use the correct amount of force.
- Secure with Clamps (Optional): For added security, especially in high-vibration environments, consider using fuel line clamps to hold the connection in place. This extra step can prevent accidental disconnections.
Testing for Leaks:
After the connections are made, it's crucial to test for any potential leaks:
- Visual Inspection: Start by visually examining the connections for any signs of fuel leakage. Look for any wet spots, stains, or fuel residue around the fittings. Even a small leak can be a potential safety hazard.
- Bubble Test: Fill a clean container with soapy water and carefully pour it around the connections. If there are any leaks, you will see bubbles forming on the surface, indicating the presence of fuel. This test is simple and effective.
- Pressure Test: For a more comprehensive test, use a fuel line pressure gauge. Connect the gauge to the fuel line and apply pressure according to the manufacturer's recommendations. Observe the gauge for any pressure drops or leaks. This test ensures the integrity of the connection and identifies potential issues.
- Final Check: Once you've identified and addressed any leaks, recheck the connections to ensure they are tight and secure. Make any necessary adjustments or retightening to guarantee a reliable fuel line system.
Remember, proper connection and testing techniques are vital to maintaining a safe and efficient fuel system. Always follow manufacturer guidelines and safety protocols when working with fuel lines.
Unraveling the Mystery: Why Diesel Engines Need Two Fuel Lines
You may want to see also
Frequently asked questions
Joining steel fuel lines requires careful preparation and the use of specific techniques to ensure a secure and leak-free connection. The process typically involves cleaning and preparing the ends of the fuel lines, using a suitable primer or adhesive, and then employing methods like welding, soldering, or compression fittings.
Yes, several tools are essential for this task. These include a fuel line cutter or shears for precise cutting, a deburring tool to remove sharp edges, a fuel line primer or adhesive, a welding or soldering kit (if applicable), and compression fittings or clamps. Having the right tools will make the joining process more efficient and effective.
Achieving a secure connection is crucial to prevent fuel leaks. Start by ensuring the fuel lines are properly aligned and the ends are clean and free of debris. Apply the primer or adhesive as per the manufacturer's instructions, and then use welding, soldering, or compression fittings to create a tight seal. Regularly check for any signs of leakage after the connection is made.
While it is possible to join steel fuel lines without specialized training, it is highly recommended to have some knowledge and experience in plumbing or automotive repairs. Proper training ensures you understand the importance of safety, the correct use of tools, and the potential risks associated with fuel line work. If you're unsure, consulting a professional or referring to detailed tutorials can provide valuable guidance.
One of the most critical mistakes is not properly cleaning the fuel lines, which can lead to poor adhesion or sealing. Additionally, using the wrong type of primer or adhesive, or neglecting to follow manufacturer instructions, can result in an ineffective connection. Always ensure you have the right tools, take safety precautions, and double-check your work to avoid common pitfalls when joining steel fuel lines.