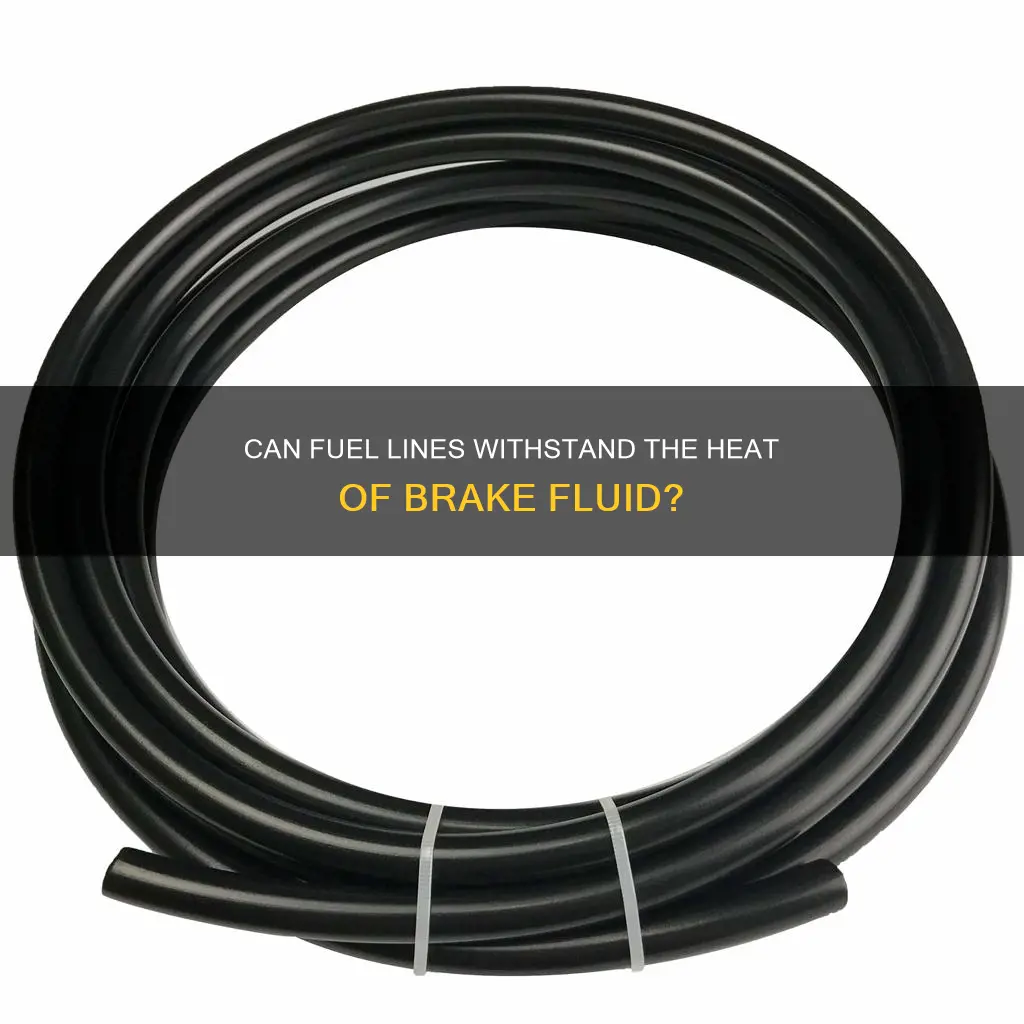
The compatibility of fuel lines with brake fluid is a critical consideration in vehicle maintenance. When selecting or replacing fuel lines, it's essential to ensure they are designed to withstand the corrosive nature of brake fluid. This is because brake fluid can cause degradation and damage to certain materials over time, potentially leading to leaks or system failures. Understanding the specific requirements and compatibility of different fuel line materials with brake fluid is crucial to ensure the safety and reliability of a vehicle's braking system.
Characteristics | Values |
---|---|
Compatibility | Fuel lines are not designed to withstand brake fluid. Brake fluid is highly corrosive and can damage fuel lines over time. |
Material | Fuel lines are typically made of rubber or plastic, which are not compatible with brake fluid. |
Pressure Rating | Fuel lines are not rated to handle the pressure of brake systems. |
Temperature Range | The temperature range of fuel lines is generally not suitable for brake fluid, which can cause degradation and failure. |
Chemical Resistance | Brake fluid contains chemicals that can degrade the material of fuel lines, leading to cracks and leaks. |
Flexibility | While fuel lines are flexible, they may not be flexible enough to accommodate the movement and vibrations of a brake system. |
Cost | Replacing fuel lines with compatible materials can be expensive. |
Maintenance | Regular inspection and replacement of fuel lines are necessary to prevent issues with brake fluid contamination. |
What You'll Learn
- Material Compatibility: Different fuel lines have varying resistance to brake fluid, so check the material
- Temperature Tolerance: Extreme temperatures can affect fuel line performance, especially with brake fluid
- Pressure Resistance: High-pressure systems require fuel lines that can withstand brake fluid pressure
- Flexibility: Flexibility is crucial for fuel lines to accommodate engine movement without cracking
- Durability: Long-lasting fuel lines should be resistant to corrosion and wear from brake fluid
Material Compatibility: Different fuel lines have varying resistance to brake fluid, so check the material
When it comes to automotive maintenance, ensuring the compatibility of various components is crucial, especially when dealing with different fluids like fuel and brake fluid. One often overlooked aspect is the compatibility of fuel lines with brake fluid. While fuel lines are designed to withstand the pressures and temperatures associated with fuel systems, they may not always be compatible with brake fluid, which can lead to potential issues and system failures.
The primary concern with material compatibility is the potential for degradation or corrosion. Different materials have varying levels of resistance to brake fluid, which can cause the fuel line to deteriorate over time. For instance, rubber fuel lines may not be suitable for long-term use with brake fluid, as the fluid can cause the rubber to become brittle and crack. This can result in fuel leaks, which can be dangerous and require immediate attention. On the other hand, some fuel lines made from more durable materials like stainless steel or high-density polyethylene (HDPE) may offer better resistance to brake fluid, ensuring a longer lifespan and reduced risk of system failure.
To ensure the longevity and reliability of your vehicle's fuel system, it is essential to choose the right fuel line material. When selecting a fuel line, consider the specific requirements of your vehicle and the type of brake fluid used. Some manufacturers provide recommendations or specifications regarding the compatibility of certain materials with brake fluid. Consulting the vehicle's manual or contacting the manufacturer can provide valuable insights into the best material choices.
Additionally, regular inspection and maintenance of fuel lines are vital, especially in vehicles with older brake systems. Over time, even compatible fuel lines may show signs of wear and tear, making it essential to check for any cracks, leaks, or signs of corrosion. Replacing worn-out fuel lines with new ones made from compatible materials can help prevent potential issues and ensure the overall safety and performance of the vehicle.
In summary, material compatibility is a critical factor when considering the use of fuel lines in vehicles with brake fluid systems. Different materials offer varying levels of resistance, and choosing the right one can prevent degradation, corrosion, and potential system failures. By understanding the specific requirements and consulting relevant resources, vehicle owners can make informed decisions to maintain a reliable and safe driving experience.
Unveiling Destiny 2's Fuel Line: Location Guide
You may want to see also
Temperature Tolerance: Extreme temperatures can affect fuel line performance, especially with brake fluid
Extreme temperatures can significantly impact the performance and longevity of fuel lines, particularly when they are in contact with brake fluid. This is an important consideration for vehicle owners and mechanics alike, as it can affect the overall safety and efficiency of a vehicle's braking system.
Brake fluid is a specialized hydraulic fluid designed to transmit force and transfer pressure from the brake pedal to the brake pads or shoes, which then slow down or stop the vehicle. It operates under high pressure and temperature conditions, and its performance is critical to the vehicle's braking efficiency. When brake fluid comes into contact with fuel lines, it can lead to several potential issues.
In extremely hot environments, brake fluid can undergo thermal expansion, increasing its volume and pressure. This expansion can cause the fuel lines to stretch and potentially damage the internal walls of the lines, leading to leaks or reduced fuel flow. Over time, this may result in fuel starvation, affecting the vehicle's engine performance and potentially causing it to stall. Additionally, the heat can cause the fuel lines to become brittle, making them more susceptible to cracking or splitting, especially at bends or joints.
Conversely, in cold temperatures, brake fluid can become more viscous, increasing its resistance to flow. This can lead to reduced braking performance, as the brake fluid may not be able to transmit pressure effectively. The fuel lines, being in close proximity to the brake fluid, can also be affected by this change in viscosity, potentially causing restrictions in fuel flow and impacting engine operation.
To ensure optimal performance, it is crucial to use the correct type of brake fluid and fuel lines designed for the specific vehicle and climate conditions. Regular maintenance, including checking for any signs of damage or leaks, is essential to identify and address potential issues early on. By understanding the temperature tolerance of fuel lines and their interaction with brake fluid, vehicle owners can take proactive measures to maintain the integrity of their braking system and overall vehicle performance.
Optimizing Performance: Choosing the Right Fuel Line for Your Atomic 4 Engine
You may want to see also
Pressure Resistance: High-pressure systems require fuel lines that can withstand brake fluid pressure
In high-performance vehicles, the braking system plays a critical role in ensuring safe and efficient operation. One crucial component that often goes unnoticed is the fuel line, which is responsible for delivering fuel to the engine. However, when it comes to high-pressure braking systems, the fuel line's ability to withstand the pressure of brake fluid becomes a critical factor.
Brake fluid is a highly pressurized liquid that transmits force from the brake pedal to the brake pads or shoes, causing them to press against the rotors or drums and slow down or stop the vehicle. This high-pressure environment demands fuel lines that are specifically designed to handle such forces without compromising performance or safety. The fuel lines must be able to resist the pressure exerted by the brake fluid to ensure a consistent and reliable fuel supply to the engine.
The pressure resistance of fuel lines is essential for several reasons. Firstly, it ensures that the fuel remains under the correct pressure, allowing for efficient atomization and combustion in the engine. If the fuel lines cannot withstand the pressure, it may lead to fuel leaks or improper fuel delivery, resulting in reduced engine performance or even dangerous situations. Secondly, high-pressure systems often involve higher temperatures due to the increased friction and heat generated during braking. The fuel lines must be able to handle these elevated temperatures without degrading or becoming brittle, which could lead to fuel leaks or system failures.
To achieve pressure resistance, fuel lines for high-pressure systems are typically constructed using materials that offer excellent durability and flexibility. These materials can include specialized rubber compounds, synthetic polymers, or even metal braids, depending on the specific application and vehicle requirements. The design of the fuel lines may also incorporate features such as reinforced walls, protective jackets, or internal reinforcements to enhance their ability to withstand pressure and temperature variations.
In summary, when dealing with high-pressure braking systems, it is imperative to select fuel lines that can withstand the pressure of brake fluid. This ensures optimal engine performance, safety, and reliability. By choosing the right materials and designs, engineers can create fuel lines that meet the demanding requirements of modern vehicles, providing a robust and efficient connection between the braking system and the engine.
Troubleshooting Evaporation: Fixing Mazda's Fuel Line Issues
You may want to see also
Flexibility: Flexibility is crucial for fuel lines to accommodate engine movement without cracking
Flexibility is a critical attribute of fuel lines, especially in automotive applications, as it enables the lines to withstand the dynamic nature of the engine's movement. When an engine operates, it experiences significant vibrations and thermal expansion, which can cause the various components to shift and move. Fuel lines, responsible for transporting fuel from the tank to the engine, must be able to flex and bend without compromising their structural integrity. This flexibility is essential to prevent the lines from cracking or breaking, which could lead to fuel leaks and potential engine misfires or stalls.
The design of fuel lines takes into account the need for flexibility to ensure a long-lasting and reliable connection. Engineers often use materials with inherent flexibility, such as rubber or certain types of synthetic compounds, which can stretch and return to their original shape without permanent deformation. These materials are carefully selected to maintain their flexibility even under the extreme temperatures and conditions found in an engine bay.
In addition to the choice of material, the construction of the fuel line itself plays a vital role in its flexibility. The line may feature a braided or reinforced design, where multiple layers of material are intertwined to provide strength and flexibility. This construction technique allows the fuel line to bend around corners, accommodate engine movement, and maintain a secure connection without the risk of cracking.
Furthermore, the installation process is crucial to ensuring flexibility. Fuel lines are typically routed through the engine compartment in a way that allows for natural movement and expansion. Proper routing minimizes sharp bends and tight spaces, reducing stress on the line and promoting its longevity. Regular maintenance, such as checking for any signs of damage or wear, is also essential to preserve the flexibility of fuel lines and prevent potential issues.
In summary, flexibility is a key consideration in the design and installation of fuel lines to ensure they can withstand the rigors of the engine environment. By utilizing flexible materials and thoughtful construction techniques, fuel lines can effectively accommodate engine movement, providing a reliable and safe fuel supply to the engine without the risk of cracking or failure. This aspect of fuel line design is often overlooked but is vital to the overall performance and safety of the vehicle.
Houston Fuel Lines: Uncovering Hidden Issues and Solutions
You may want to see also
Durability: Long-lasting fuel lines should be resistant to corrosion and wear from brake fluid
When considering the compatibility of fuel lines with brake fluid, it's crucial to focus on the durability aspect, specifically how these fuel lines withstand the corrosive and wear-inducing effects of brake fluid. This is a critical factor in ensuring the long-term reliability and safety of a vehicle's braking system.
Brake fluid, often a glycol-ether or silicone-based liquid, can be highly corrosive to certain materials. Over time, it can lead to the degradation of rubber and plastic components, including fuel lines. The constant exposure to brake fluid can cause these materials to become brittle, crack, or even rupture, leading to potential leaks and system failures. Therefore, fuel lines designed for use with brake fluid must be made from materials that offer excellent resistance to corrosion and wear.
One of the key materials used for this purpose is stainless steel. Stainless steel fuel lines are known for their superior resistance to corrosion, even in the presence of brake fluid. This is due to the inherent properties of stainless steel, which form a protective oxide layer on the surface, preventing further corrosion. Additionally, stainless steel is highly durable and can withstand the mechanical stresses that fuel lines may experience during the vehicle's operation.
Another material that has gained popularity for fuel lines in brake systems is high-density polyethylene (HDPE). HDPE is a type of plastic that offers excellent resistance to corrosion and chemical attack. It is also flexible and can accommodate the movement of the fuel lines without becoming brittle or cracking. The use of HDPE fuel lines ensures that the system remains reliable and safe over an extended period.
In summary, when dealing with the compatibility of fuel lines and brake fluid, durability is paramount. Fuel lines should be resistant to the corrosive and wear-inducing effects of brake fluid to ensure the long-term reliability and safety of the braking system. Materials like stainless steel and high-density polyethylene are ideal choices for fuel lines in such applications, providing the necessary durability and peace of mind for vehicle owners.
Unveiling the Secrets: Red Line Fuel System Explained
You may want to see also
Frequently asked questions
No, the fuel line will not be damaged by brake fluid. Both substances are designed to be compatible with each other and will not cause any adverse reactions or degradation when in close proximity.
It is highly unlikely for brake fluid to leak into the fuel system. The fuel lines and fittings are typically made of materials that are resistant to brake fluid, ensuring that the two systems remain separate and do not mix.
No special seals or adapters are required. Standard fuel line fittings and connections are usually sufficient and compatible with brake fluid. However, it is always a good practice to ensure proper sealing and regular maintenance to prevent any potential issues.