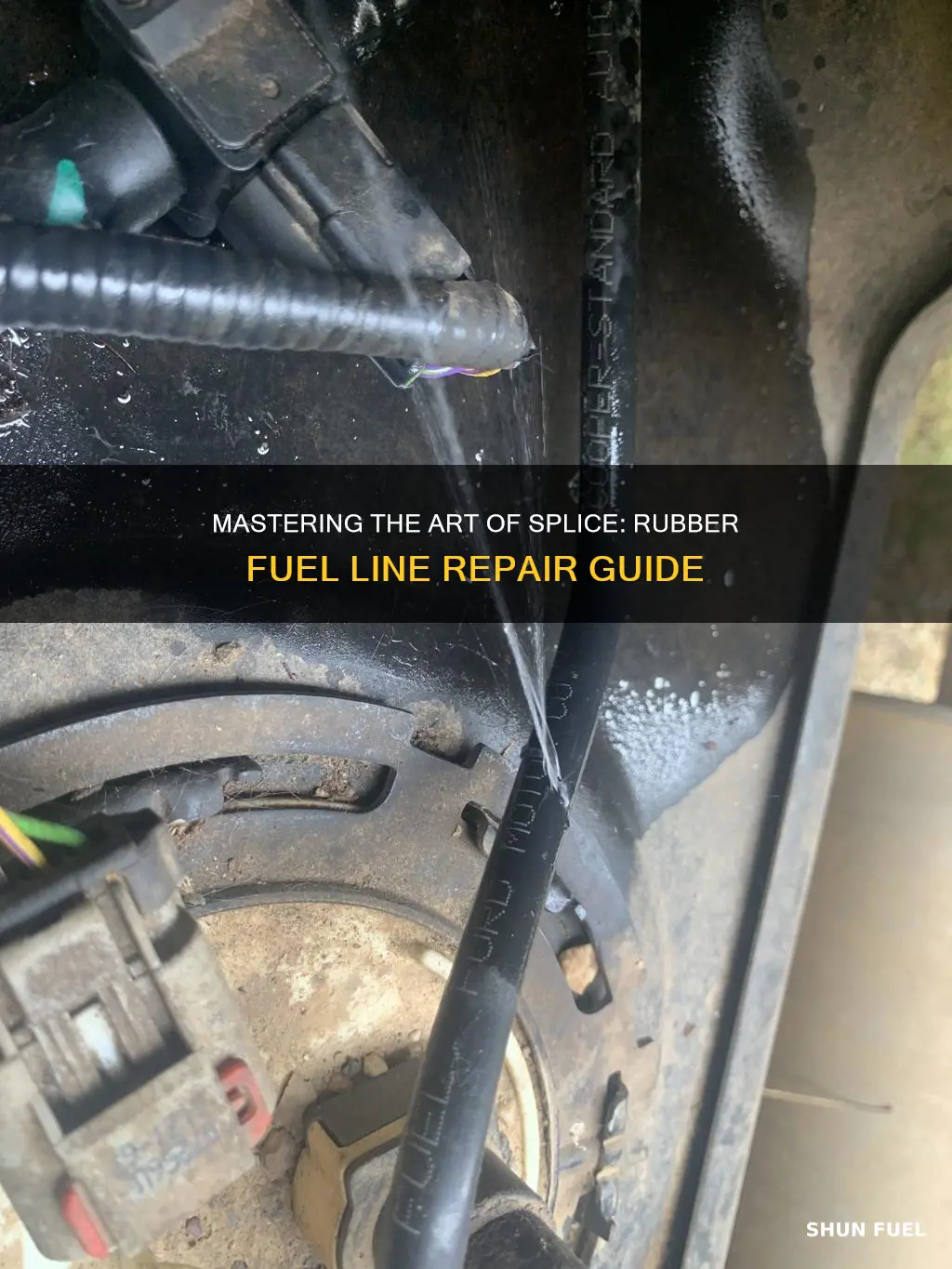
Splicing a rubber fuel line is a crucial repair for maintaining the functionality of your vehicle's fuel system. This process involves joining two sections of the rubber line to restore continuity and prevent fuel leaks. It requires careful preparation, including cleaning the surfaces, ensuring a tight fit, and using the appropriate adhesive or sealant to ensure a durable and leak-free connection. This guide will provide a step-by-step approach to mastering the art of splicing rubber fuel lines, ensuring your vehicle remains reliable and safe.
What You'll Learn
- Prepare Tools: Gather necessary tools: rubber gloves, fuel line cutter, pipe wrench, and cleaning supplies
- Inspect Line: Check for damage, cracks, or leaks. Ensure compatibility with fuel type
- Cut and Prepare: Use a sharp blade to cut the line, leaving a few inches of clean, intact material
- Clean the Area: Remove dirt and debris from the line and surrounding area to ensure a secure connection
- Connect and Secure: Slide the new line onto the fitting, tighten securely, and use clamps to hold in place
Prepare Tools: Gather necessary tools: rubber gloves, fuel line cutter, pipe wrench, and cleaning supplies
Before you begin the process of splicing a rubber fuel line, it's crucial to ensure you have the right tools and materials ready. This will make the task more efficient and help you avoid any unnecessary complications. Here's a detailed guide on preparing the necessary tools:
Rubber Gloves: Protecting your hands is essential when working with rubber materials. Rubber gloves will shield your hands from potential irritation or allergic reactions caused by the rubber. Choose gloves made from a durable material that is resistant to chemicals and abrasion. This will ensure a comfortable and safe working environment.
Fuel Line Cutter: A fuel line cutter is a specialized tool designed to cut through rubber fuel lines efficiently. It allows you to make clean and precise cuts, which is vital for a successful splice. Look for a cutter with adjustable settings to accommodate different fuel line diameters. This tool will enable you to create a seamless connection between the existing line and the new splice.
Pipe Wrench: A pipe wrench is an indispensable tool for tightening and loosening fittings and connections. When splicing a fuel line, you'll need to secure the ends of the line to prevent any leaks. A pipe wrench provides the necessary grip and leverage to tighten the fittings securely. Ensure you have a wrench with adjustable jaws to accommodate various sizes of fittings.
Cleaning Supplies: Keeping the work area clean is essential for a professional and safe splice. Gather cleaning supplies such as rags, brushes, and cleaning solvents. These will help remove any dirt, grease, or contaminants from the fuel line and fittings. Cleaning ensures a proper bond between the splice and the existing line, reducing the risk of leaks. Additionally, a clean work area minimizes the chances of accidents and makes the splicing process more manageable.
Having these tools and supplies ready will set you up for success when splicing a rubber fuel line. It ensures that you have everything required to complete the task efficiently and effectively, minimizing the risk of errors or complications. Remember, proper preparation is key to a successful repair or modification.
Replacing Fuel Line in Poulan Chainsaw: A Step-by-Step Guide
You may want to see also
Inspect Line: Check for damage, cracks, or leaks. Ensure compatibility with fuel type
When inspecting a rubber fuel line, it's crucial to thoroughly examine it for any signs of damage, cracks, or leaks. Start by visually assessing the line for any visible tears, punctures, or discolored areas. Rubber fuel lines are susceptible to wear and tear from fuel exposure, temperature fluctuations, and mechanical stress. Look for any signs of deterioration, especially at the connections and bends, as these areas are prone to developing issues over time.
Check for cracks along the length of the line, as even small cracks can lead to fuel leaks, which can be dangerous and cause environmental damage. Inspect the connections between the fuel line and the fuel tank, pump, and other components. Ensure that all fittings are tight and secure, as loose connections can result in fuel leakage. Pay attention to the condition of the O-rings or gaskets used in these connections, as they play a vital role in preventing leaks.
Leak detection is essential. Soak the fuel line with a small amount of soapy water and observe if any bubbles appear. Bubbles indicate the presence of a leak, as they signify the escape of fuel. If you notice any bubbles, the line may require replacement or splicing.
Regarding compatibility, it's important to ensure that the rubber fuel line is suitable for the type of fuel it will carry. Different fuels have varying chemical compositions and properties, and using the wrong type of fuel line can lead to degradation and potential leaks. Check the manufacturer's specifications to determine the compatible fuel types for the line. This information is typically available in the product documentation or on the manufacturer's website. Using the correct fuel line ensures the safety and efficiency of your fuel system.
If you find any damage or leaks, it's best to replace the affected section of the fuel line. For splicing, follow the instructions provided by the manufacturer or seek professional guidance. Proper splicing techniques and materials ensure a secure and reliable connection, minimizing the risk of future issues. Regular inspection and maintenance of the fuel line will help prevent costly repairs and ensure the safe operation of your vehicle or equipment.
Understanding the Role of Fuel Line Hoses in the Evaporative Emissions System
You may want to see also
Cut and Prepare: Use a sharp blade to cut the line, leaving a few inches of clean, intact material
When splicing a rubber fuel line, the first crucial step is to carefully cut the line, ensuring a precise and clean cut. This initial preparation is essential to guarantee a successful splice. Start by identifying the section of the line you need to replace or repair. Use a sharp blade, such as a utility knife or a specialized fuel line cutter, to make a clean cut. The goal is to leave a few inches of clean, intact material on either side of the damaged or old section. This intact portion will serve as the foundation for your splice, providing the necessary length and stability.
Take your time with this step, as precision is key. Measure and mark the cut line, ensuring it is straight and aligned. A slight curve or uneven cut can lead to issues during the splicing process. Once you've made the cut, inspect the edges to ensure they are smooth and free of any debris or sharp edges that could compromise the splice. This initial preparation sets the stage for a strong and reliable connection between the old and new sections of the fuel line.
The next step is to carefully remove any old or damaged material from the cut ends, ensuring you don't damage the remaining intact portion. Use a file or sandpaper to smooth any rough edges, creating a clean surface for the splice. This process might require some patience, especially if the line is old and brittle. Take your time to ensure you're not causing any unnecessary damage to the line.
By following these detailed steps, you'll be well-prepared to proceed with the splicing process, ensuring a robust and long-lasting repair for your rubber fuel line. Remember, a clean and precise cut is the foundation for a successful splice.
Where to Find the Best Deals on Diesel Fuel Lines
You may want to see also
Clean the Area: Remove dirt and debris from the line and surrounding area to ensure a secure connection
Before you begin the splicing process, it's crucial to ensure that the area around the fuel line is clean and free from any contaminants. Start by identifying the section of the rubber fuel line that needs splicing. Inspect the line for any visible damage, cracks, or areas of deterioration. Once you've located the damaged section, clear the immediate area around it. Remove any dirt, debris, or old fuel residue that might interfere with the splicing process. Use a soft-bristled brush or a clean cloth to gently scrub the surface of the fuel line and the surrounding area. Pay close attention to the connection points and ensure that no contaminants are present.
Dirt and debris can compromise the integrity of the splice, so it's essential to be thorough. If you encounter any stubborn dirt or residue, use a mild detergent or a specialized fuel line cleaner to dissolve it. Rinse the area with clean water to remove any traces of the cleaner. Ensure that the water is free from any contaminants that could affect the splicing material. Allow the area to dry completely before proceeding.
When cleaning the surrounding area, be cautious not to damage the fuel line or any nearby components. Take your time and work carefully to avoid any unnecessary wear and tear. If there are any sharp edges or protruding objects near the fuel line, ensure they are securely fastened or removed to prevent accidental punctures during the splicing process.
A clean and prepared surface is crucial for a successful splice. By removing dirt and debris, you create a suitable environment for the splicing material to adhere properly. This step ensures that the splice will be secure and resistant to fuel leakage. Remember, a thorough cleaning process is an essential foundation for a reliable fuel line repair.
Ford Black Box Fuel Line Clip Removal: A Step-by-Step Guide
You may want to see also
Connect and Secure: Slide the new line onto the fitting, tighten securely, and use clamps to hold in place
When splicing a rubber fuel line, the process of connecting and securing it is crucial to ensure a reliable and safe fuel system. Here's a step-by-step guide to achieving a secure connection:
Start by carefully sliding the new rubber fuel line onto the fitting. Ensure that the line is aligned properly with the existing line and the fitting is clean and free of any debris. Take your time with this step to avoid any unnecessary strain on the line. Once the line is positioned correctly, it's time to tighten the connection. Use a wrench or a suitable tool to tighten the fitting securely. Apply firm pressure to ensure a tight seal, but be careful not to over-tighten, as this can damage the rubber material. The goal is to create a snug fit that prevents any fuel leakage.
After tightening, the next step is to secure the connection further. This is where clamps come into play. Rubber fuel lines can be sensitive to movement, so using clamps is essential to hold the new line in place. Slide the clamp onto the fitting, ensuring it covers the entire length of the new line. Tighten the clamp securely, but again, be mindful of the material and avoid excessive force. The clamp should provide a firm grip without causing any permanent deformation of the rubber line.
It's important to double-check the tightness of the connection at this stage. Give the fitting a gentle tug to ensure the line is securely attached and there is no play in the connection. If everything feels solid, you can proceed to the final steps of your fuel line splicing project. Remember, a well-connected and secured fuel line is a critical component of your vehicle's safety and performance.
By following these instructions, you'll create a robust and reliable splice for your rubber fuel line, ensuring a continuous and safe fuel supply to your engine. Always prioritize safety and take the time to do it right.
Unveiling the Best: Who Sells Hard Fuel Lines?
You may want to see also
Frequently asked questions
Splicing a rubber fuel line is a process of joining two or more sections of rubber tubing together to create a continuous fuel line. This is often necessary when replacing damaged or worn-out fuel lines, extending existing lines, or creating custom fuel lines for specific applications.
The primary tools needed are a fuel line cutter, a fuel line crimper, a heat source (such as a heat gun or torch), and a suitable adhesive or sealant. You will also need the replacement rubber fuel line sections, primer, and any necessary fittings or adapters.
Start by cleaning the ends of the fuel lines. Remove any dirt, debris, or old adhesive using a cloth or brush. Then, cut the lines to the desired length, ensuring a smooth and even cut. Remove any excess material and deburr the edges to provide a clean surface for bonding.
Begin by applying a thin layer of primer to the prepared ends of the fuel lines. Let it dry according to the manufacturer's instructions. Then, heat the ends of the lines until they are pliable. Carefully align the ends and use the crimper to create a secure connection. Ensure the splice is tight and free of any air bubbles. Finally, apply the adhesive or sealant to reinforce the splice.
After splicing, allow the adhesive and sealant to cure fully. Test the splice by applying pressure and checking for any leaks. If everything is secure, the spliced fuel line should now be ready for use. Regularly inspect the splice and the surrounding area for any signs of damage or deterioration, and replace the line if necessary.