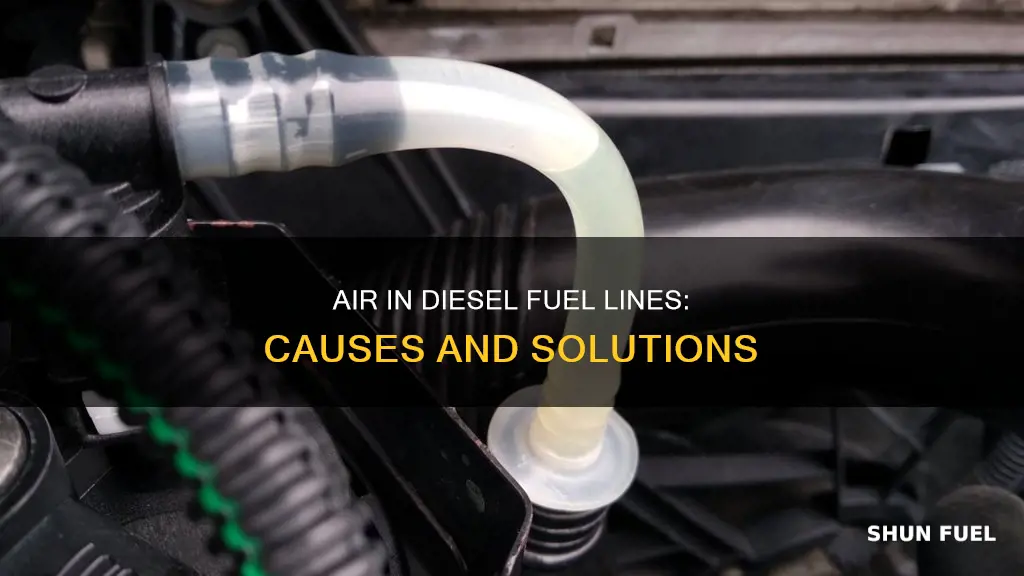
Air in diesel fuel lines is a common issue that can lead to engine performance problems. Understanding the causes of this air intrusion is crucial for maintaining the efficiency and reliability of diesel engines. This paragraph will explore the factors contributing to the presence of air in diesel fuel lines, including the role of fuel system design, engine operation, and environmental conditions. By examining these aspects, we can gain insights into how air enters the fuel lines and how to prevent or mitigate this problem.
Characteristics | Values |
---|---|
Contamination Sources | Air entering the fuel system through the fuel tank breathers, fuel filter, or injection pump seals. |
Fuel System Design | Open fuel systems without a fuel pump and return line can allow air to enter. |
Fuel Tank Issues | Leaking or damaged fuel tanks can introduce air and contaminants. |
Fuel Filter | Clogged or damaged fuel filters restrict flow, causing air to be drawn in. |
Fuel Pump | A faulty fuel pump may not prime the system properly, leading to air bubbles. |
Temperature and Pressure | High temperatures and low fuel pressure can contribute to air separation from the fuel. |
Engine Operation | Frequent starting and stopping can introduce air into the system. |
Fuel Quality | Poor-quality fuel with water or contaminants can cause air separation. |
Maintenance Neglect | Regular maintenance is crucial to prevent air-related issues. |
What You'll Learn
- Air Ingress: Air can enter fuel lines during refuelling or due to faulty seals
- Vapour Formation: High temperatures cause fuel vapour, leading to air bubbles
- Pump Issues: Faulty fuel pumps may introduce air into the system
- Filter Problems: Clogged filters restrict flow, allowing air to enter
- System Design: Poor design can trap air, especially in long lines
Air Ingress: Air can enter fuel lines during refuelling or due to faulty seals
Air ingress, or the presence of air in diesel fuel lines, is a common issue that can lead to various performance problems in diesel engines. This phenomenon occurs when air enters the fuel system, often during the refuelling process or due to faulty seals and gaskets. Understanding the causes and implementing preventive measures are crucial for maintaining the efficiency and longevity of diesel engines.
During the refuelling process, air can be drawn into the fuel lines if the fuel pump is not operational or if the fuel system is not properly sealed. When a diesel engine is running, the fuel pump creates a vacuum that draws fuel from the tank. If this vacuum is disrupted during refuelling, air can enter the system. This is why it is essential to ensure that the fuel pump is operational and that the fuel lines are sealed tightly to prevent air from entering.
Faulty seals and gaskets are another significant contributor to air ingress. These components play a critical role in maintaining the integrity of the fuel system by preventing air and fuel from leaking out. Over time, seals and gaskets can wear out, crack, or become damaged, allowing air to infiltrate the fuel lines. Common areas where these issues can occur include the fuel tank, fuel filter, and the connections between fuel lines and injectors. Regular inspection and replacement of these components are necessary to mitigate this problem.
To address air ingress, it is recommended to follow a few preventive measures. Firstly, ensure that the fuel pump is operational and functioning correctly before and after refuelling. This can be achieved by checking the pump's voltage and current draw, as well as listening for any unusual noises. Secondly, inspect the fuel lines and connections regularly for any signs of damage or leaks. Pay close attention to the seals and gaskets, as these are the primary barriers against air ingress. If any issues are found, they should be promptly repaired or replaced.
In summary, air ingress in diesel fuel lines is primarily caused by the refuelling process and faulty seals. By understanding these causes and implementing preventive measures, such as checking the fuel pump's functionality and inspecting seals, diesel engine owners can minimize the occurrence of air-related issues and ensure optimal engine performance. Regular maintenance and attention to these details will contribute to a more reliable and efficient diesel engine system.
Troubleshooting Clogged Fuel Lines: Common Causes and Solutions
You may want to see also
Vapour Formation: High temperatures cause fuel vapour, leading to air bubbles
The presence of air in diesel fuel lines is a common issue that can arise due to various factors, and one significant contributor is the phenomenon of vapor formation. When diesel fuel is exposed to high temperatures, it undergoes a process that leads to the creation of fuel vapor, which subsequently forms air bubbles within the fuel lines. This process is a natural consequence of the physical properties of diesel fuel and the conditions it is subjected to.
High temperatures play a crucial role in this process. When diesel fuel is heated, its molecules gain energy and begin to move more rapidly. As a result, the fuel's volume increases, and it transitions from a liquid state to a gaseous state, forming vapor. This vaporization process is more pronounced in diesel fuel due to its higher boiling point compared to gasoline. The higher the temperature, the more rapid the vaporization, leading to a higher concentration of fuel vapor in the system.
As the fuel vaporizes, it mixes with the surrounding air, creating a mixture of fuel and air. This mixture is less dense than the original liquid fuel, causing it to rise within the fuel lines. The rising vapor can lead to the formation of air bubbles, which are essentially pockets of this vaporized fuel. These bubbles can become trapped in the fuel lines, especially in areas with reduced flow velocity or where the fuel line design allows for the accumulation of air.
The presence of air bubbles in diesel fuel lines can have several implications. Firstly, it can lead to reduced fuel efficiency as the engine may not receive the precise fuel-air mixture required for optimal combustion. Air bubbles can also cause engine misfires, reduced power, and increased emissions. Additionally, the introduction of air into the fuel system can contribute to the formation of fuel system deposits and corrosion, further exacerbating the performance issues.
To mitigate the issue of air bubbles caused by vapor formation, it is essential to maintain the fuel system's integrity. This includes using fuel filters and separators to remove contaminants and ensure a clean fuel supply. Regular maintenance, such as fuel system flushing and replacement of worn components, can also help prevent the accumulation of air bubbles. Additionally, operating the engine within the recommended temperature range can minimize the occurrence of vaporization, thus reducing the likelihood of air-related problems in diesel fuel lines.
Winterizing Outboard: Fuel Line Disconnect: A Wise Move?
You may want to see also
Pump Issues: Faulty fuel pumps may introduce air into the system
When it comes to diesel fuel lines, one of the primary causes of air introduction is indeed related to pump issues, specifically faulty fuel pumps. These pumps play a critical role in the fuel system by ensuring a consistent and controlled flow of fuel from the tank to the engine. However, over time, they can develop problems that lead to air being drawn into the system.
A faulty fuel pump may have worn-out components, such as the impeller or the diaphragm, which are responsible for creating the necessary pressure to push fuel through the lines. As these parts wear down, the pump's ability to maintain a tight seal diminishes, allowing air to seep into the fuel stream. This issue is particularly common in older vehicles or those with high mileage, where the pump's longevity may be compromised.
Another potential cause is a damaged or cracked fuel pump housing. This housing encloses and protects the pump mechanism, and any cracks can lead to air entering the system. When the housing is compromised, it creates a pathway for air to infiltrate the fuel, especially if the pump is not functioning optimally. This can result in a loss of power and performance, as the engine receives a mixture of fuel and air instead of the pure fuel it requires.
To address this problem, it is essential to inspect and maintain the fuel pump regularly. Replacing worn-out pump components or the entire pump if necessary can prevent air from entering the diesel fuel lines. Additionally, ensuring that the fuel tank is properly sealed and that there are no leaks in the system can further mitigate the risk of air introduction. Regular servicing and attention to these potential pump issues can help maintain the efficiency and reliability of diesel engines.
Fuel Line Flaring: A Double-Edged Decision
You may want to see also
Filter Problems: Clogged filters restrict flow, allowing air to enter
A common issue that can lead to air in diesel fuel lines is filter problems, specifically clogged filters. Diesel fuel systems rely on filters to ensure clean and contaminant-free fuel is delivered to the engine. These filters are designed to capture and trap particles and contaminants that may be present in the fuel, such as dirt, water, and debris. Over time, these filters can become clogged, which has several consequences that can result in air entering the fuel lines.
When a filter becomes clogged, it restricts the flow of fuel. This restriction causes a back pressure in the system, pushing air into the fuel lines. Air can then enter the system through various points, such as the fuel pump, injectors, or even the fuel tank, depending on the specific design of the vehicle. This phenomenon is often referred to as 'air lock' or 'air in the fuel'.
The presence of air in the fuel can lead to several performance issues. One of the most common problems is engine misfires or rough idling. Air bubbles in the fuel can cause the engine to run inefficiently, leading to reduced power output and potential engine damage over time. Additionally, air in the fuel can cause the engine to hesitate or stall, especially during acceleration or when the engine is under load.
To address filter problems, regular maintenance and filter replacement are crucial. Diesel engines typically have multiple filters, including the fuel filter, water separator, and particulate filter. It is recommended to replace these filters at regular intervals as specified by the manufacturer. During maintenance, it is essential to inspect the filters for any signs of clogging or contamination and replace them if necessary.
In some cases, if the filter is severely clogged, it may require professional cleaning or replacement. This is especially true for high-pressure fuel systems or engines with advanced fuel injection systems. Proper filter maintenance ensures that the fuel system remains clean and efficient, minimizing the chances of air entering the fuel lines and improving overall engine performance.
VXR Pro 93 Fuel Line: Dimensions and Specifications
You may want to see also
System Design: Poor design can trap air, especially in long lines
Poor system design is a significant contributor to the presence of air in diesel fuel lines, particularly in long and complex fuel systems. When designing diesel fuel systems, engineers must consider several factors to ensure optimal performance and minimize air intrusion. One critical aspect is the layout and configuration of the fuel lines. Long, straight lines with minimal bends and twists are generally preferred as they reduce the likelihood of air trapping. Air tends to accumulate in tight turns and sharp angles, creating areas of low pressure where it can become trapped. To mitigate this, designers should aim for a more linear approach, ensuring that the fuel lines follow a smooth path.
Another design consideration is the use of filters and separators. These components are essential for removing contaminants, including air, from the fuel. However, if not properly designed or located, they can become a source of air entrapment. Filters, for instance, should be positioned near the fuel source or pump to capture any air bubbles that might form during the fueling process. Proper filter sizing and placement are crucial to ensuring efficient air removal without causing excessive pressure drops that could lead to air locking.
The design of the fuel tank and its connection to the main fuel line is also vital. If the tank is not well-ventilated or if the connection is poorly sealed, air can enter the system. Engineers should ensure that the tank has adequate ventilation to allow air to escape and that the fuel line connections are tight and secure. Additionally, the use of venturi devices or air-bleeding mechanisms can help in removing air from the system during operation.
In long fuel lines, the risk of air trapping increases due to the potential for dead zones or low-pressure areas. Designers should consider implementing air-release valves or vents at regular intervals to allow air to escape. These devices can be strategically placed to break the fuel line into smaller segments, reducing the chances of air accumulation. Proper ventilation at key points in the system can also help maintain a positive pressure, preventing air from entering and settling.
Furthermore, the use of compatible materials is essential to prevent air leakage and trapping. Different materials may have varying degrees of permeability, and selecting the right combination can ensure a tight seal. For instance, using materials with low permeability for fuel lines and compatible gaskets can minimize the entry of air and other contaminants. Proper sealing techniques and regular maintenance are also crucial to maintaining the integrity of the fuel system design.
Permatex on Fuel Lines: A Carburetor Repair Hack or a No-Go?
You may want to see also
Frequently asked questions
Air in diesel fuel lines is primarily caused by the natural tendency of air to enter a system when there is a pressure difference. This can happen due to several reasons: improper fuel tank venting, low fuel levels, fuel pump issues, or even the natural expansion and contraction of the fuel as it heats up or cools down.
When the fuel tank is not properly vented, it creates a vacuum, which pulls in air. This is especially common in older vehicles or when the fuel tank is located below the engine. Proper ventilation ensures that air can escape and maintain a consistent fuel-air ratio.
Yes, low fuel levels can result in a lack of pressure in the fuel lines, allowing air to enter. As the fuel level drops, the pressure in the system decreases, making it easier for air to infiltrate. This issue is often temporary and can be resolved by refilling the fuel tank.
The fuel pump is responsible for delivering fuel at the required pressure to the engine. If the fuel pump is faulty or not functioning correctly, it may not create enough pressure to push out any air that enters the system. Regular maintenance and checking for pump issues are essential to prevent air-related problems.
Preventive measures include ensuring proper fuel tank venting, keeping the fuel level full, regularly checking and replacing fuel filters, and maintaining a clean fuel system. Additionally, using a fuel additive that helps maintain fuel system cleanliness can also contribute to preventing air-related issues.