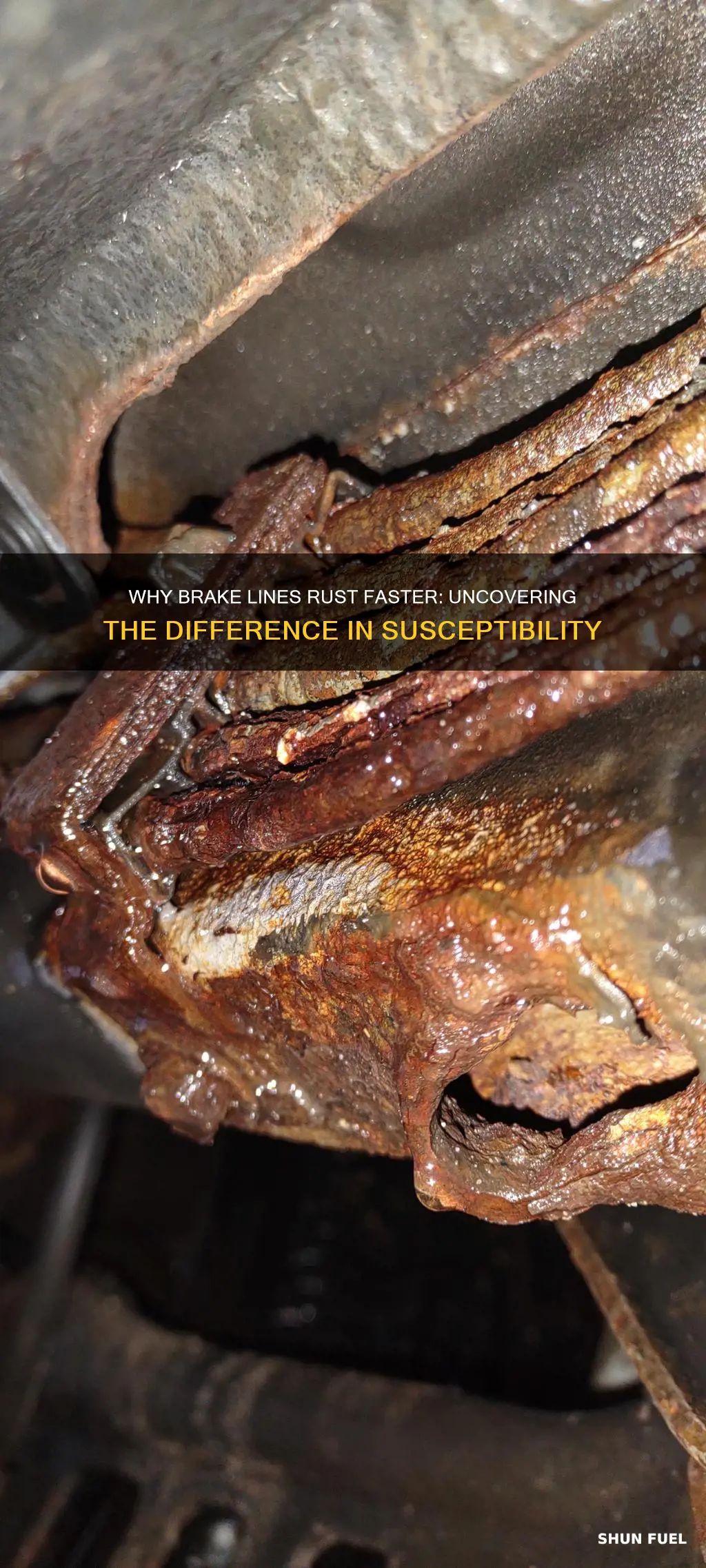
Brake lines, also known as brake hoses, are more prone to rusting compared to fuel lines due to their exposure to harsh environmental conditions. The primary reason is the presence of moisture, which can easily penetrate the protective outer layer of brake lines, especially when they are not properly sealed or protected. This moisture, combined with the corrosive nature of brake fluid, accelerates the rusting process. Additionally, brake lines are often located in areas with higher humidity or near the exhaust system, which can further contribute to their deterioration. Understanding these factors is crucial for vehicle owners and mechanics to ensure proper maintenance and longevity of the braking system.
Characteristics | Values |
---|---|
Material Composition | Brake lines are typically made from steel or stainless steel, which are more susceptible to corrosion compared to fuel lines made from copper or brass. |
Exposure to Moisture | Brakes are often exposed to moisture from road spray, especially in wet conditions, leading to faster rust formation. |
Chemical Environment | Brake fluid contains minerals and additives that can accelerate corrosion, whereas fuel lines are designed to withstand the chemicals in gasoline or diesel. |
Temperature Effects | Higher temperatures can accelerate rusting in brake lines, as heat increases the rate of corrosion reactions. |
Oxidation Resistance | Copper and brass used in fuel lines offer better natural resistance to oxidation, making them less prone to rust. |
Maintenance and Care | Regular maintenance and inspection of brake lines are crucial to prevent rust, as corrosion can compromise the structural integrity of the lines. |
Design and Placement | The design and placement of brake lines, often located closer to the ground, can expose them to more environmental factors, increasing the risk of rust. |
What You'll Learn
- Material Differences: Brake lines use steel, which is more susceptible to corrosion than fuel lines' stainless steel or copper alloys
- Moisture Exposure: Frequent contact with moisture and road grime accelerates rust formation on brake lines
- Pressure and Vibration: The high pressure and vibrations in brake systems create stress, promoting rust formation
- Lack of Protection: Brake lines often lack protective coatings, making them more prone to corrosion compared to fuel lines
- Environmental Factors: Rusting is faster in harsh environments with high humidity, salt, and road salt exposure
Material Differences: Brake lines use steel, which is more susceptible to corrosion than fuel lines' stainless steel or copper alloys
The primary reason brake lines tend to rust faster than fuel lines is the material composition of these components. Brake lines are typically constructed from steel, a metal that is inherently more prone to corrosion compared to the materials used in fuel lines. Steel's susceptibility to rust is due to its iron content, which reacts with oxygen and moisture in the air to form iron oxide, commonly known as rust. This process is accelerated in the presence of salt and other corrosive elements found on roads and in harsh environments.
In contrast, fuel lines are often made from stainless steel or copper alloys. Stainless steel, in particular, is an alloy of iron that contains a minimum of 10.5% chromium, which forms a protective oxide layer on the surface, preventing rust and corrosion. This protective layer is known as the 'passivation' layer, and it significantly enhances the material's resistance to corrosion. Copper alloys, such as brass or bronze, also offer excellent corrosion resistance due to their natural patina, a protective layer that forms over time, shielding the metal from further deterioration.
The choice of materials is crucial in determining the longevity and reliability of a vehicle's braking system. Steel brake lines, while cost-effective, require regular maintenance and inspection to prevent rust-related issues. Over time, rust can compromise the structural integrity of the brake lines, leading to reduced braking performance and potential safety hazards. In contrast, the use of stainless steel or copper alloys in fuel lines ensures a longer lifespan and better resistance to corrosion, even in challenging environmental conditions.
Understanding the material differences between brake lines and fuel lines is essential for vehicle owners and mechanics. By recognizing the inherent corrosion susceptibility of steel, one can take proactive measures to mitigate the effects of rust, such as regular cleaning, coating, or the use of protective materials. This knowledge also highlights the importance of choosing high-quality materials for vehicle components to ensure optimal performance and safety.
In summary, the material composition of brake lines and fuel lines plays a significant role in their susceptibility to corrosion. Steel, used in brake lines, is more prone to rust due to its iron content, while stainless steel and copper alloys, commonly found in fuel lines, offer superior corrosion resistance. This difference in materials directly impacts the maintenance and longevity of a vehicle's braking system, emphasizing the need for informed choices in automotive engineering and maintenance.
Optimizing Performance: Choosing the Right Fuel Lines for Your 70-HP Johnson Engine
You may want to see also
Moisture Exposure: Frequent contact with moisture and road grime accelerates rust formation on brake lines
Brake lines, unlike fuel lines, are more susceptible to rust due to their frequent exposure to moisture and road grime. When brake lines are exposed to these elements, they can corrode and weaken over time, leading to potential brake failure. This is a critical issue as brakes are a vital component of a vehicle's safety system.
Moisture, in particular, is a major contributor to the rusting process. When brake lines are exposed to water, whether from rain, snow, or even condensation, the moisture can seep into the lines and come into contact with the metal components. Over time, this moisture can lead to the formation of rust, which can eat away at the metal and cause it to deteriorate.
Road grime, which includes dirt, dust, and other debris, can also play a significant role in the rusting process. When brake lines are frequently exposed to these gritty substances, they can become embedded in the small crevices and openings of the lines. This grime can trap moisture and create an environment conducive to rust formation. The constant friction and heat generated by the brakes during operation can further accelerate this process.
To prevent brake line corrosion, it is essential to maintain a clean and dry environment around the brake system. Regularly inspecting and cleaning the brake lines, especially in areas where they are exposed to moisture or road grime, can help remove any built-up corrosion. Additionally, using rust inhibitors or protective coatings on the brake lines can provide an extra layer of defense against moisture and corrosion.
In summary, the frequent contact with moisture and road grime is a primary reason why brake lines rust faster than fuel lines. Understanding this vulnerability allows vehicle owners and mechanics to take proactive measures to ensure the longevity and reliability of the braking system. Regular maintenance and the use of protective measures can help mitigate the risks associated with brake line corrosion.
Unraveling the Smelly Mystery: Why Braided Fuel Lines Stink
You may want to see also
Pressure and Vibration: The high pressure and vibrations in brake systems create stress, promoting rust formation
The brake system is a critical component of any vehicle, and its performance is heavily reliant on the integrity of its components, especially the brake lines. One of the primary reasons brake lines tend to rust faster than fuel lines is the unique operating conditions they face. Brake lines operate under high pressure, which is essential for the effective transfer of braking force to the wheels. This high pressure, however, creates a challenging environment for the materials used in the brake lines.
The stress and pressure within the brake system are significant, especially during hard braking or when driving over rough terrain. This stress can lead to the deformation of the brake line material, particularly if it is not of high quality or has been compromised by previous damage. Over time, this deformation can result in the formation of small cracks or imperfections in the brake line walls. These cracks provide an entry point for moisture and contaminants, which are the primary catalysts for rust formation.
Vibration is another critical factor in the accelerated rusting of brake lines. The brake system experiences intense vibrations during operation, which can cause the brake lines to flex and move. This movement, combined with the high pressure, can lead to the development of stress points and potential weaknesses in the brake line material. As a result, the brake lines may begin to show signs of corrosion, especially in areas where the vibrations are most pronounced.
The combination of high pressure and vibration creates a unique challenge for brake lines. The stress and movement cause the brake lines to be susceptible to internal corrosion, which can lead to a loss of structural integrity over time. This corrosion is often more rapid in brake lines compared to fuel lines because the brake system's operating conditions are more demanding and less forgiving.
To mitigate this issue, it is essential to use high-quality brake line materials that can withstand the high pressure and vibrations. Regular maintenance, including checking for any signs of corrosion or damage, is also crucial. Ensuring that the brake system is properly bled and that all components are securely installed can help prevent the issues associated with pressure and vibration, thus reducing the likelihood of brake line rusting.
Fuel Pump Upgrade: Big Line Solutions for Your Chevy Yukon
You may want to see also
Lack of Protection: Brake lines often lack protective coatings, making them more prone to corrosion compared to fuel lines
Brake lines, an essential component of a vehicle's braking system, are more susceptible to corrosion and rust compared to fuel lines, and this phenomenon can be attributed to the lack of protective coatings on brake lines. While fuel lines are typically insulated with rubber or protective materials, brake lines are often left exposed, making them more vulnerable to the elements.
The primary reason for this difference in protection is the design and function of these lines. Fuel lines are designed to carry volatile liquids, such as gasoline or diesel, which are inherently corrosive to metal. As a result, fuel lines are often encased in protective materials to prevent rust and ensure the longevity of the vehicle's engine. In contrast, brake lines transmit hydraulic fluid, which, while not as volatile, still contains moisture and can lead to corrosion over time.
Brake lines are typically made of steel or other metal alloys, which are inherently susceptible to rust and corrosion when exposed to moisture and air. Without proper insulation or protective coatings, these metal components can quickly deteriorate, leading to a loss of braking performance and potential safety hazards. This is especially critical as brake lines play a crucial role in slowing down and stopping a vehicle, and any compromise in their integrity can have severe consequences.
The lack of protective coatings on brake lines is a design choice that prioritizes other factors. Brake lines need to be flexible to accommodate the movement of the vehicle's suspension and the expansion and contraction of the hydraulic fluid. This flexibility often comes at the cost of additional protective layers, leaving the metal more exposed to the environment. As a result, brake lines are more prone to rust, especially in harsh weather conditions or in vehicles with poor maintenance records.
To address this issue, vehicle owners can take proactive measures. Regular inspections and maintenance can help identify and replace corroded brake lines before they compromise the braking system's performance. Additionally, using rust inhibitors or protective coatings specifically designed for brake lines can provide an extra layer of defense against corrosion, ensuring the longevity and reliability of the braking system.
Understanding the Role of Fuel Return Lines in Engine Systems
You may want to see also
Environmental Factors: Rusting is faster in harsh environments with high humidity, salt, and road salt exposure
The environment plays a significant role in the accelerated rusting of brake lines compared to fuel lines. Brake lines are more susceptible to corrosion in harsh environmental conditions, particularly those with high humidity, salt, and road salt exposure. These factors contribute to the rapid deterioration of brake lines, leading to potential safety hazards.
High humidity is a key environmental factor that promotes rusting. When brake lines are exposed to moist conditions, water vapor can penetrate the metal surface, leading to the formation of rust. This is especially problematic in regions with frequent rainfall or high levels of atmospheric moisture. Over time, the constant presence of moisture can cause the brake lines to weaken and become less effective, potentially resulting in brake failure.
Salt and road salt are common culprits in rusting acceleration. When brake lines are exposed to salt on the road, it acts as an electrolyte, facilitating the electrochemical reaction that leads to rust formation. Road salt, often used to melt ice and snow, is particularly damaging as it can penetrate the metal surface and accelerate corrosion. In coastal areas or regions with heavy snowfall, the constant exposure to salt can significantly shorten the lifespan of brake lines.
The combination of high humidity and salt exposure creates an ideal environment for rusting. When brake lines are subjected to both factors, the moisture facilitates the movement of ions, allowing salt to penetrate the metal surface more easily. This results in a faster and more aggressive corrosion process. In such conditions, brake lines may corrode rapidly, leading to reduced brake performance and potential safety issues.
To mitigate the effects of environmental factors, regular maintenance and inspections are crucial. Brake lines should be checked for signs of corrosion, especially in areas with harsh weather conditions. Applying rust inhibitors or protective coatings can help slow down the rusting process. Additionally, ensuring proper drainage and ventilation in the brake system can reduce the risk of moisture accumulation, thus minimizing the impact of high humidity.
Fuel Line Faults: Common Issues and Solutions
You may want to see also
Frequently asked questions
Brake lines are typically exposed to more moisture and contaminants due to their location near the wheels and the road. When brake lines are submerged in water or exposed to road spray, they are more susceptible to corrosion. Additionally, brake lines often carry brake fluid, which can be corrosive to certain metals over time.
Yes, traditional brake lines were often made of steel, which is susceptible to rust, especially in moist environments. Modern brake systems may use stainless steel or other corrosion-resistant materials to mitigate this issue. However, the design and placement of brake lines can still influence their exposure to moisture and contaminants.
Absolutely. Regular inspection and maintenance of brake systems are crucial. This includes checking for any signs of corrosion, ensuring proper fluid levels, and using brake fluids that offer some level of corrosion protection. Keeping the brake system clean and dry can significantly reduce the risk of rust formation in brake lines.