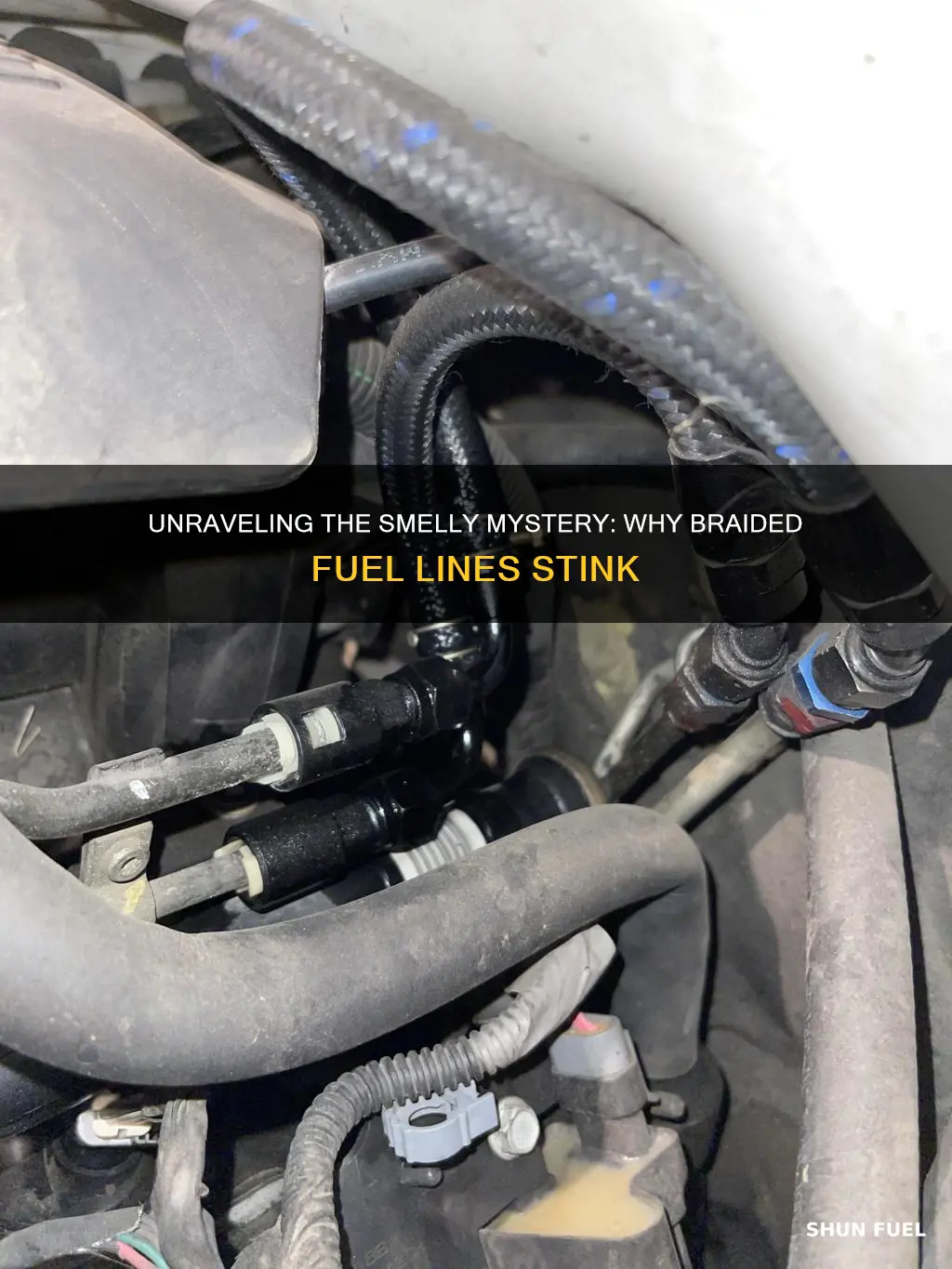
Braided fuel lines, while essential for vehicle performance, can sometimes emit a strong, unpleasant odor. This issue often arises due to the materials used in the construction of these lines, which can include rubber, plastic, or synthetic fibers. Over time, these materials may break down, releasing volatile organic compounds (VOCs) and other chemicals that contribute to the distinctive smell. Factors such as heat, sunlight, and chemical exposure can accelerate this degradation process, making the fuel lines stink. Understanding the causes of this odor is crucial for vehicle owners to address potential issues and ensure optimal performance.
What You'll Learn
Braided Fuel Lines: A Review of Their Durability and Longevity
Braided fuel lines are an essential component in the fuel delivery system of many vehicles, particularly those with high-performance engines. These lines are designed to withstand the rigors of the automotive environment, including extreme temperatures, vibrations, and exposure to fuel contaminants. One of the key advantages of braided fuel lines is their durability and longevity, which make them a preferred choice for many automotive enthusiasts and professionals.
The construction of braided fuel lines involves a unique process. A high-strength synthetic fiber core is surrounded by multiple layers of braided material, typically made from materials like steel, stainless steel, or Kevlar. This braided design provides excellent flexibility while maintaining structural integrity. The braided layers create a robust and flexible structure that can withstand the constant movement and pressure within the fuel system. This flexibility is crucial as it allows the fuel lines to navigate around engine components and other obstacles without compromising performance or durability.
In terms of durability, braided fuel lines offer several advantages. The braided construction provides superior resistance to abrasion, ensuring that the lines can withstand the harsh conditions of the engine bay. This is particularly important in high-performance applications where fuel lines may be subjected to increased stress and heat. Additionally, the use of high-strength materials in the braiding process makes these lines highly resistant to corrosion, ensuring their longevity even in the presence of fuel contaminants and engine moisture.
The longevity of braided fuel lines is further enhanced by their ability to maintain a consistent fuel flow under varying conditions. The braided design allows for efficient fuel delivery, ensuring that the engine receives the required amount of fuel without any loss or restriction. This is especially critical in high-performance vehicles where precise fuel management is essential for optimal power output and engine efficiency. Moreover, the flexibility of braided fuel lines reduces the risk of damage from engine movement, vibrations, and temperature fluctuations, which can be detrimental to the performance and longevity of traditional rubber fuel lines.
In conclusion, braided fuel lines offer a superior alternative to traditional fuel lines due to their exceptional durability and longevity. The braided construction, combined with high-strength materials, provides excellent resistance to abrasion, corrosion, and temperature extremes. This ensures that the fuel lines can withstand the demanding conditions of the automotive environment, resulting in improved engine performance and reliability. When considering fuel line upgrades, braided fuel lines are a reliable and long-lasting solution for vehicle owners seeking enhanced fuel system efficiency and durability.
Street Avenger Fuel Line: Unleash the Power with the Right Choice
You may want to see also
Braided Fuel Lines: The Impact of Temperature on Performance
Braided fuel lines are an essential component in the fuel delivery system of many vehicles, especially high-performance cars and motorcycles. These lines are designed to withstand the rigors of the automotive environment, including varying temperatures, fuel pressure, and vibration. One of the critical factors affecting the performance and longevity of braided fuel lines is temperature.
Braided fuel lines are typically made from a combination of materials, including synthetic fibers, such as Kevlar or polyester, and a protective outer layer. The braiding process creates a flexible yet sturdy structure that can handle the constant flexing and movement within the engine bay. However, this flexibility also means that the lines can expand and contract with changes in temperature, which can have several implications for their performance.
In cold temperatures, braided fuel lines can become stiff and less flexible. This stiffness can lead to increased pressure on the fuel pump and injectors, potentially causing fuel delivery issues. As a result, the engine may struggle to start, or the performance might be reduced during cold weather. To mitigate this, some vehicles are equipped with electric fuel pumps that can maintain a steady fuel flow even when temperatures drop.
On the other hand, high temperatures can also take a toll on braided fuel lines. Prolonged exposure to heat can cause the synthetic fibers to degrade, leading to a loss of flexibility and potential cracking. This can result in fuel leaks, which are not only dangerous but can also cause damage to the engine over time. To prevent this, manufacturers often use specialized materials and coatings to protect the braided fuel lines from excessive heat.
The impact of temperature on braided fuel lines is a critical consideration for vehicle owners and mechanics. Proper maintenance, such as regular inspections and the use of appropriate fuel additives, can help ensure that the fuel lines remain in optimal condition. Additionally, understanding the effects of temperature can guide the selection of the right braided fuel lines for specific vehicle applications, ensuring reliable and efficient fuel delivery in all weather conditions.
Understanding the Perfect Fuel Line Size for Snapper Lawb Mowers
You may want to see also
Braided Fuel Lines: Maintenance and Cleaning Techniques
Braided fuel lines, while durable and flexible, can sometimes emit an unpleasant odor, which can be a cause for concern for vehicle owners. This issue often arises due to the materials used in the construction of these fuel lines, particularly the rubber or synthetic compounds that can absorb and retain odors over time. The smell is often described as musty, sweet, or even slightly chemical, and it can be a result of several factors, including the type of fuel used, the age of the vehicle, and the overall condition of the fuel system. Understanding the causes and implementing proper maintenance techniques can help mitigate this problem.
One of the primary reasons braided fuel lines may stink is the absorption of fuel-related compounds. When fuel is stored in the tank, it can evaporate, leaving behind volatile organic compounds (VOCs) that can permeate the fuel lines. Over time, these VOCs can mix with the rubber or synthetic materials of the braided fuel lines, causing a persistent odor. This is especially common in older vehicles or those that have been stored for extended periods.
To address this issue, regular maintenance and cleaning of the fuel system are essential. Here are some techniques to keep in mind:
- Fuel System Flush: A professional fuel system flush can effectively remove accumulated contaminants and odors. This process involves using a specialized cleaner that is injected into the fuel tank and circulates through the entire system, dissolving and removing any deposits, varnish, and odors. It is recommended to perform this flush every few years or as advised by the vehicle manufacturer.
- Air Bleed and Venting: Ensuring proper ventilation in the fuel system can help prevent odor buildup. After refueling, slightly open the fuel filler cap to allow air to enter the tank, which helps disperse the fuel and any associated odors. Additionally, checking and cleaning the fuel tank breathers regularly can prevent the accumulation of contaminants.
- Regular Fuel Changes: Changing the fuel type or using a different brand of fuel can sometimes eliminate the smell. Some fuel additives are designed to clean and protect the fuel system, reducing the likelihood of odor absorption. However, it is crucial to choose additives that are compatible with the vehicle's fuel system to avoid any potential damage.
- Inspect and Replace: Regularly inspect the braided fuel lines for any signs of damage, cracks, or deterioration. If the lines are old or show signs of wear, replacement may be necessary. Modern vehicles often have fuel lines that are more resistant to odor absorption due to improved materials and construction techniques.
By implementing these maintenance and cleaning techniques, vehicle owners can effectively manage and reduce the unpleasant odors associated with braided fuel lines. It is essential to stay proactive in the care of the fuel system to ensure optimal performance and a pleasant driving experience.
Understanding the Role of Fuel Vapor Lines in Your Vehicle
You may want to see also
Braided Fuel Lines: Common Issues and Troubleshooting Tips
Braided fuel lines are a common component in many vehicles, designed to carry fuel from the tank to the engine. While they are known for their durability and flexibility, they can sometimes develop issues that may lead to unpleasant odors. One of the most common problems associated with braided fuel lines is the development of a strong, often unpleasant smell. This issue can be caused by several factors, and understanding these causes is crucial for effective troubleshooting.
One primary reason for the stench of braided fuel lines is the degradation of the rubber material over time. Braided fuel lines are typically made of rubber or a rubber-like compound, which can break down due to exposure to fuel, heat, and UV radiation. As the rubber ages, it may become brittle and crack, allowing fuel to permeate the line and come into contact with the inner walls of the line, potentially causing a chemical reaction that produces an odor. This is especially common in older vehicles or those with high mileage.
Another contributing factor is contamination. Fuel lines can become contaminated with various substances, such as water, fuel vapor, or even engine oil. When water enters the fuel line, it can create a breeding ground for bacteria, leading to a foul smell. Similarly, fuel vapor can condense inside the line, especially in colder climates, and this condensation can emit an unpleasant odor. Engine oil contamination is less common but can occur if there is a breach in the fuel line, allowing oil to mix with the fuel.
Troubleshooting a stinky braided fuel line involves a systematic approach. Firstly, inspect the fuel line for any visible damage, cracks, or signs of contamination. If you notice any issues, it's best to replace the fuel line to prevent further problems. Next, check for any signs of water accumulation. If water is present, it needs to be drained and the line flushed to remove any potential contaminants. Using a fuel line cleaner can help eliminate odors and ensure the line is free from debris.
In some cases, the issue might be related to the fuel pump or injectors. If the smell persists after addressing the fuel line, it's advisable to inspect these components. Clogged or faulty fuel injectors can cause fuel to spray improperly, leading to a strong odor. Similarly, a failing fuel pump may cause fuel to flow unevenly, resulting in a similar smell. These issues often require professional diagnosis and repair.
Remember, regular maintenance and inspection of braided fuel lines can help prevent such problems. Keeping an eye out for any changes in smell or performance can lead to early detection and resolution of potential issues.
Heat Shield for Fuel Line: Top Sources Revealed
You may want to see also
Braided Fuel Lines: Environmental Factors and Their Effects
Braided fuel lines, an essential component in many vehicle and machinery systems, are designed to withstand the rigors of fuel transport. However, their durability and performance can be significantly influenced by environmental factors. Understanding these factors is crucial for maintaining the integrity of the fuel system and ensuring optimal performance. Here's an in-depth look at the environmental considerations related to braided fuel lines:
Temperature Extremes: One of the most critical environmental factors affecting braided fuel lines is temperature. Extreme heat or cold can cause the fuel lines to expand or contract, respectively. This thermal expansion and contraction can lead to stress on the braided structure, potentially causing damage over time. In regions with varying temperatures, it is essential to choose braided fuel lines with materials that offer flexibility and resistance to temperature fluctuations. Some manufacturers use specialized rubbers or synthetic materials that can handle a wide temperature range, ensuring the fuel lines remain intact and functional.
UV Radiation and Sun Exposure: Prolonged exposure to sunlight and ultraviolet (UV) radiation can degrade the materials used in braided fuel lines. UV rays can cause the rubber or synthetic fibers to become brittle and crack, leading to potential fuel leaks. This is particularly relevant for vehicles or equipment that operate in outdoor environments for extended periods. To combat this, manufacturers often incorporate UV-resistant additives or use materials with inherent UV stability. Additionally, regular inspections and replacements of fuel lines in exposed areas can help prevent damage.
Chemical Exposure: Braided fuel lines are in direct contact with fuel, which may contain various chemicals, including ethanol and other additives. Over time, these chemicals can permeate the fuel line material, leading to degradation and potential performance issues. For example, ethanol can attract moisture, causing corrosion in metal components and swelling in rubber fuel lines. To mitigate this, using fuel lines with materials resistant to chemical degradation is essential. Some braided fuel lines are designed with compounds that repel moisture and resist the effects of ethanol, ensuring long-term reliability.
Moisture and Humidity: Moisture and high humidity can be detrimental to braided fuel lines, especially in enclosed or poorly ventilated systems. Condensation within the fuel lines can lead to corrosion, especially in metal components, and may also cause the fuel to become contaminated. To address this, manufacturers often include desiccant-filled containers or moisture-absorbing materials within the fuel line assembly. Regularly checking for signs of moisture and ensuring proper ventilation can also help prevent moisture-related issues.
Vibration and Mechanical Stress: Braided fuel lines are subjected to various mechanical stresses, including vibration and movement. Over time, this can cause the braided structure to loosen or the protective covering to wear down, leading to potential fuel leaks. Regular maintenance and inspections are vital to identify and rectify any issues. Using high-quality braided fuel lines with robust construction and proper installation techniques can minimize the risk of mechanical damage.
Airdog Fuel Line Routing: A Comprehensive Guide
You may want to see also
Frequently asked questions
The odor is primarily due to the materials used in the construction of the braided fuel lines. These lines are often made from rubber compounds, which can contain volatile organic compounds (VOCs). When exposed to air, these VOCs evaporate and release a distinct smell, often described as a strong, pungent odor.
While the smell can be unpleasant, it is usually not harmful. The odor is a result of the fuel lines' interaction with the fuel and the environment. However, if the smell becomes extremely strong or persistent, it could indicate a potential issue with the fuel system, such as a leak or contamination, which may require professional inspection and repair.
Yes, there are a few methods to mitigate the smell. One approach is to ensure proper ventilation in the vehicle's interior. Opening windows and using air conditioning or ventilation systems can help disperse the odor. Additionally, using fuel line treatments or sealants specifically designed to reduce odors can be beneficial. Regular maintenance and inspection of the fuel system can also help prevent any potential issues that might cause the unpleasant smell.