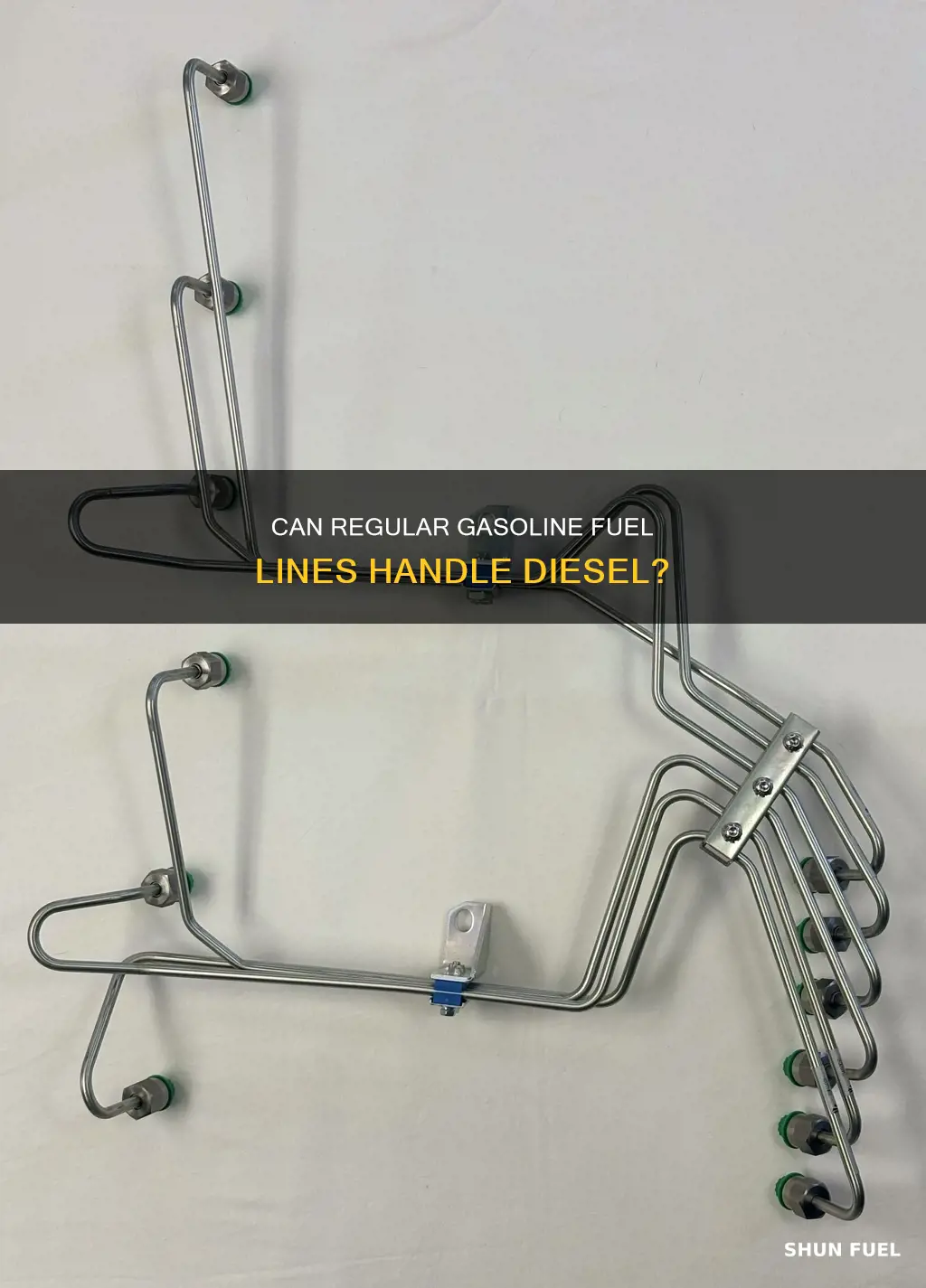
Regular fuel lines are not designed to handle diesel fuel and can lead to performance issues and potential damage to the engine. Diesel fuel has a higher pressure and temperature requirement compared to gasoline, and the fuel lines must be able to withstand these conditions to ensure efficient and safe operation. Therefore, it is crucial to use specialized fuel lines that are specifically designed for diesel engines to avoid any potential problems.
What You'll Learn
- Fuel Compatibility: Regular fuel lines may not withstand diesel's higher pressure and temperature
- Material Selection: Choose fuel lines with high-temperature resistance and durability for diesel
- Pressure Rating: Ensure fuel lines can handle diesel's higher pressure to prevent leaks
- Flexibility: Diesel fuel lines need to be flexible enough to withstand engine vibrations
- Compatibility with Additives: Some diesel fuel additives may affect the performance of regular fuel lines
Fuel Compatibility: Regular fuel lines may not withstand diesel's higher pressure and temperature
When considering the compatibility of fuel lines for diesel engines, it is crucial to understand the specific requirements and challenges associated with diesel fuel. Regular fuel lines, often made from standard materials like rubber or plastic, may not be suitable for the unique characteristics of diesel. One of the primary concerns is the higher pressure and temperature requirements of diesel fuel compared to gasoline. Diesel engines operate at much higher pressures, typically ranging from 30 to 60 psi (pounds per square inch), while gasoline engines usually operate at around 10 to 20 psi. This significant difference in pressure can put immense stress on the fuel lines, especially if they are not designed to handle such forces.
The higher pressure in diesel fuel necessitates fuel lines with enhanced structural integrity and flexibility. Regular fuel lines may not possess the necessary strength to withstand these pressures, leading to potential issues such as cracking, leaking, or even failure. Moreover, diesel fuel often contains additives that can affect the material's performance. Some of these additives can cause rubber fuel lines to become brittle or degrade over time, reducing their overall durability.
Temperature is another critical factor. Diesel fuel typically operates at higher temperatures, and regular fuel lines may not be able to handle these extreme conditions. Rubber, for instance, can become brittle and lose its flexibility when exposed to high temperatures, making it more susceptible to damage. In contrast, diesel fuel lines often require materials that can maintain their integrity over a wide temperature range, from cold starts in winter to high-temperature operation during extended use.
To ensure optimal performance and longevity, it is recommended to use fuel lines specifically designed for diesel applications. These specialized fuel lines are engineered to withstand the higher pressures and temperatures associated with diesel fuel. They are typically made from materials like high-density polyethylene (HDPE) or reinforced rubber compounds, which offer improved strength, flexibility, and resistance to fuel degradation. By investing in compatible fuel lines, diesel engine owners can ensure reliable fuel delivery, maintain engine performance, and avoid potential issues caused by incompatible materials.
In summary, while regular fuel lines may seem adequate for other applications, they may not be suitable for diesel engines due to the higher pressure and temperature requirements of diesel fuel. Using compatible fuel lines designed for diesel is essential to ensure the engine's longevity and optimal performance. Always consult the manufacturer's guidelines or seek professional advice to determine the most appropriate fuel line solution for your specific diesel engine.
Fuel Pump Mystery: Unlocking the Two-Line Secret
You may want to see also
Material Selection: Choose fuel lines with high-temperature resistance and durability for diesel
When it comes to selecting fuel lines for diesel engines, material choice is critical to ensure optimal performance and longevity. Diesel fuel lines must withstand the unique challenges posed by the fuel's higher pressure and temperature compared to gasoline. Regular fuel lines, typically made from rubber or plastic, may not be suitable for diesel applications due to their limited temperature resistance and durability.
For diesel fuel lines, high-temperature-resistant materials are essential. These materials should be able to handle the elevated temperatures generated during diesel combustion without degrading or becoming brittle. Common choices include synthetic rubber compounds, such as neoprene or EPDM (ethylene propylene diene monomer), which offer excellent resistance to heat and chemicals. These materials are designed to maintain their flexibility and structural integrity even under extreme conditions, ensuring the fuel lines can withstand the rigors of diesel operation.
Durability is another critical factor. Diesel fuel lines are exposed to harsh environments, including vibrations, impacts, and chemical corrosion. The chosen material should exhibit superior resistance to abrasion, flexing, and chemical attack. Reinforced construction, such as braided or spiral-wound designs, can enhance the line's strength and flexibility, making it more resistant to damage during installation and operation.
In addition to material properties, the fuel line's construction and design play a vital role in its performance. The inner diameter and wall thickness should be carefully considered to ensure optimal fuel flow and pressure regulation. Thicker walls provide better pressure resistance, while a larger diameter can improve flow efficiency. Properly designed fuel lines should also include protective layers, such as rubber or plastic coatings, to shield against fuel-borne contaminants and environmental factors.
When selecting fuel lines for diesel applications, it is essential to consult manufacturer specifications and guidelines. Different diesel engine manufacturers may have specific requirements or recommendations for fuel line materials and construction. Adhering to these standards ensures compatibility and optimal performance, maximizing the lifespan of the fuel system and the overall reliability of the diesel engine.
Fuel Line Dimensions: Unveiling the Mystery of Mantis Tiller Sizes
You may want to see also
Pressure Rating: Ensure fuel lines can handle diesel's higher pressure to prevent leaks
When considering the use of regular fuel lines for diesel fuel, it's crucial to understand the specific requirements and challenges associated with diesel engines. One of the most critical aspects is the pressure rating of the fuel lines. Diesel fuel operates under higher pressure compared to gasoline, and using regular fuel lines that are not designed for this purpose can lead to several issues, including leaks and potential engine damage.
The higher pressure in diesel fuel systems is necessary to ensure efficient atomization of the fuel during the injection process. This atomization is vital for proper combustion, as it allows the fuel to mix thoroughly with air, resulting in a more complete burn. Regular fuel lines, typically made from materials like rubber or plastic, may not be able to withstand the increased pressure, leading to potential failures. These failures can manifest as small cracks or punctures in the fuel line, causing fuel to leak into the engine compartment or even escape into the atmosphere.
To prevent such issues, it is essential to use fuel lines with a pressure rating suitable for diesel fuel. These specialized fuel lines are often made from more robust materials, such as high-temperature rubber compounds or braided steel, which can handle the higher pressure without compromising integrity. The pressure rating is typically specified in pounds per square inch (psi) or bars, and it's crucial to choose a fuel line that meets or exceeds the engine manufacturer's recommendations.
In addition to the pressure rating, the design and construction of the fuel line should also be considered. Diesel fuel lines often require additional features to ensure reliability, such as reinforced hoses, protective sleeves, or brackets to secure the line in place. These features help prevent damage from engine movement, heat, and other potential sources of stress.
In summary, when adapting a fuel system for diesel use, it is imperative to prioritize the pressure rating of the fuel lines. Regular fuel lines may not be suitable due to their lower pressure ratings, which could lead to leaks and engine performance issues. By selecting fuel lines designed for diesel applications, you ensure that the fuel system can handle the higher pressure, providing a safer and more efficient operation.
Fuel Line Size for Timecutter Z4200: Essential Guide
You may want to see also
Flexibility: Diesel fuel lines need to be flexible enough to withstand engine vibrations
When it comes to diesel fuel lines, flexibility is a critical factor that often gets overlooked. Diesel engines produce a lot of vibrations, and these vibrations can cause stress on the fuel lines, potentially leading to damage over time. Regular fuel lines, which are typically made of rigid materials like steel or brass, are not designed to withstand the intense vibrations generated by diesel engines. This is where the need for flexibility comes into play.
The primary purpose of a fuel line is to deliver fuel from the tank to the engine. However, in the case of diesel engines, the fuel needs to be delivered under high pressure to ensure efficient combustion. This high-pressure fuel is then directed through the fuel lines to the injectors, which spray the fuel into the engine's cylinders. The flexibility of the fuel line becomes crucial here because it needs to accommodate the movement and vibrations of the engine without kinking or breaking.
To achieve this flexibility, diesel fuel lines are often made from materials that offer a balance between durability and suppleness. One common material used is rubber, which is known for its ability to absorb vibrations and flex without compromising its structural integrity. Rubber fuel lines can stretch and move with the engine, reducing the risk of damage from vibrations. Additionally, the inner lining of these fuel lines is often made of a flexible material like a synthetic rubber compound, which further enhances their flexibility.
Another important aspect of flexibility in diesel fuel lines is the design and construction of the fittings. The connections between the fuel lines, the engine, and the fuel tank must be able to move and adjust to the engine's vibrations without causing leaks or damage. This often involves using specialized fittings and clamps that provide a secure yet flexible hold.
In summary, diesel fuel lines require flexibility to withstand the intense vibrations produced by diesel engines. Regular fuel lines, with their rigid construction, are not suitable for this application. By using flexible materials and carefully designed fittings, diesel fuel lines can effectively deliver high-pressure fuel while maintaining their structural integrity and ensuring a reliable fuel supply to the engine. This flexibility is a key consideration in the design and installation of diesel fuel systems to ensure optimal performance and longevity.
Fuel Line Fabrication: Expert Services for Your Vehicle
You may want to see also
Compatibility with Additives: Some diesel fuel additives may affect the performance of regular fuel lines
When considering the use of regular fuel lines for diesel fuel, it's important to understand the potential impact of fuel additives on the system's performance. Diesel fuel often contains additives designed to improve combustion, lubricate engine components, and enhance overall performance. However, these additives can sometimes have unintended consequences on the fuel lines.
One significant concern is the compatibility of these additives with the materials used in regular fuel lines. Many fuel lines are made from rubber or plastic compounds that may not be resistant to the chemicals present in diesel fuel additives. Over time, these additives can degrade the fuel line material, leading to cracks, leaks, or even fuel contamination. For instance, certain additives containing ethanol or methanol can be particularly harmful to rubber fuel lines, causing them to become brittle and fail prematurely.
To ensure optimal performance and longevity, it is recommended to use fuel lines specifically designed for diesel fuel, often referred to as diesel-rated fuel lines. These lines are formulated to withstand the unique properties of diesel fuel, including its higher sulfur content and the presence of additives. Diesel-rated fuel lines are typically made from materials that are more resistant to chemical degradation, ensuring a longer-lasting and more reliable fuel delivery system.
Additionally, when using diesel fuel additives, it is crucial to follow the manufacturer's guidelines and recommendations. Some additives may require specific fuel line materials to function effectively without causing damage. Using the right combination of fuel and fuel line can help maintain the integrity of the fuel system and prevent potential issues.
In summary, while regular fuel lines might seem like a cost-effective solution, the potential compatibility issues with diesel fuel additives could lead to performance problems and premature failure. Investing in diesel-rated fuel lines is a proactive approach to ensure the longevity and reliability of the fuel system, especially when using fuels with added performance enhancers.
Understanding Fuel Lines: A1 vs. B1 Differences Explained
You may want to see also
Frequently asked questions
Yes, you can use a regular fuel line for diesel fuel, but it's important to choose the right type of fuel line for your specific application. Diesel fuel lines are typically made from materials that can withstand the higher pressure and temperature requirements of diesel engines compared to gasoline engines.
Gasoline and diesel fuel lines have some key differences. Diesel fuel lines are generally made from materials like high-density polyethylene (HDPE) or rubber compounds that can handle the higher pressure and temperature ranges associated with diesel fuel. They are also often thicker and more flexible to accommodate the varying flow rates and engine requirements.
Using a regular fuel line for diesel fuel may not cause immediate issues, but it could lead to long-term problems. Regular fuel lines might not be able to handle the higher pressure and temperature of diesel fuel, which can result in fuel leaks, reduced engine performance, and potential damage to the engine over time.
Yes, it is recommended to use fuel lines specifically designed for diesel applications. These fuel lines are engineered to withstand the unique demands of diesel fuel, including higher pressure, temperature, and flow rates. Look for fuel lines made from durable materials like HDPE or rubber compounds, and ensure they meet the standards and specifications for your diesel engine.