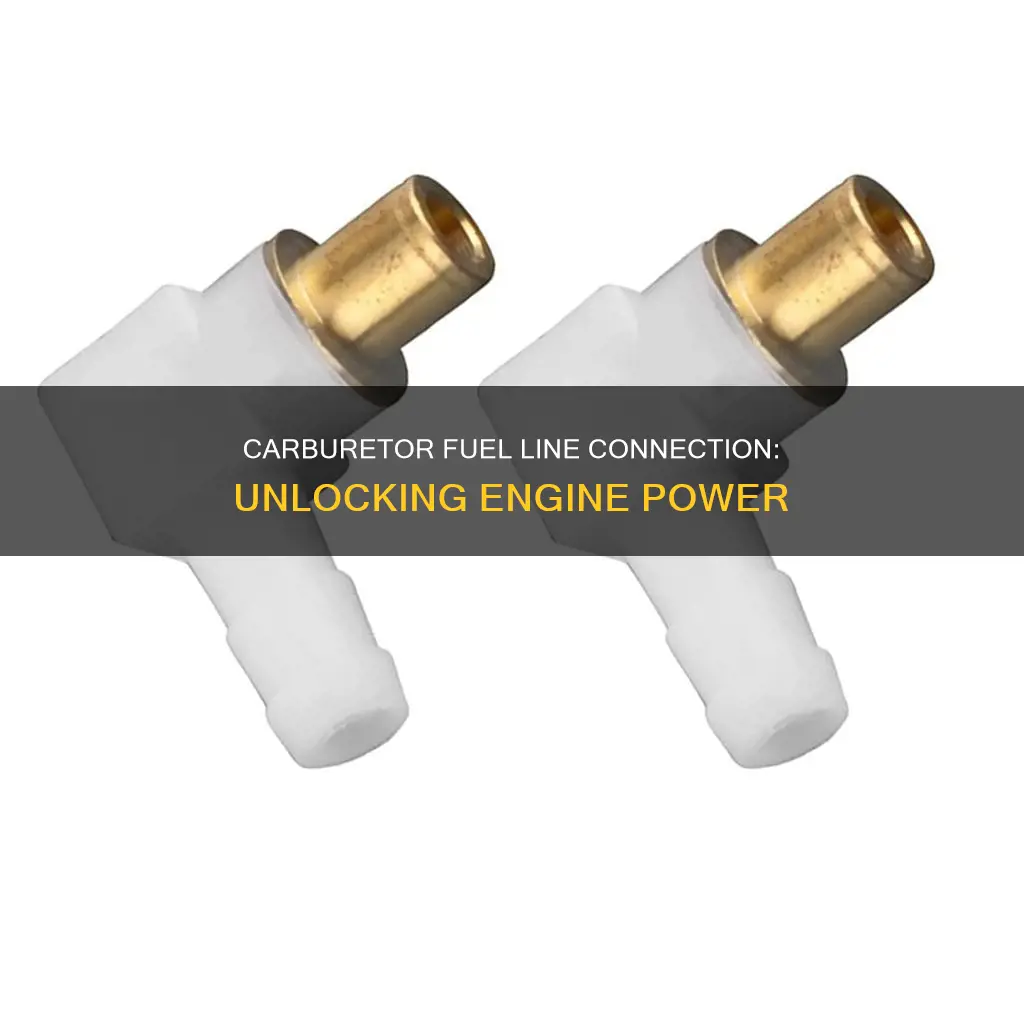
The intricate network of components within a vehicle's engine system is a fascinating interplay of precision engineering. One crucial juncture in this network is where the carburetor and fuel line connect, a point of convergence that is both essential and complex. This connection is vital for the efficient delivery of fuel to the engine, ensuring optimal performance and power output. Understanding the mechanics and design of this interface is key to appreciating the intricate dance of components that keeps a vehicle running smoothly.
What You'll Learn
- Carburetor Design: The carburetor's design influences fuel-air mixing and performance
- Fuel Line Material: Different materials affect fuel flow, pressure, and durability
- Connection Type: Various connection types ensure secure fuel delivery and prevent leaks
- Vacuum Effects: Engine vacuum impacts fuel-air ratio and carburetor operation
- Airflow Considerations: Airflow around the carburetor affects fuel atomization and engine performance
Carburetor Design: The carburetor's design influences fuel-air mixing and performance
The design of a carburetor is a critical aspect of engine performance, especially in older vehicles that rely on this technology for fuel delivery. Carburetors are responsible for mixing air and fuel in the correct ratio to create a combustible mixture for the engine. This process is intricate and highly dependent on the carburetor's design, which includes various components and mechanisms.
One key design element is the carburetor's float bowl, a reservoir that stores fuel. The bowl's capacity and design influence the amount of fuel available for the engine. A larger bowl can hold more fuel, which is beneficial for high-performance applications or when the engine operates at varying speeds. The bowl's shape and surface area also affect how fuel is distributed, ensuring a consistent supply to the carburetor's jets and passages.
The carburetor's jets are another crucial design feature. These small orifices regulate the fuel flow into the engine. The design and placement of these jets determine the fuel-air mixture's quality. For instance, a carburetor with multiple jets can provide different fuel-air ratios for various engine speeds, allowing for better performance and efficiency. The jet design also considers the engine's power requirements, ensuring the correct amount of fuel is delivered to meet the demands of different operating conditions.
The carburetor's design also includes the mixing chamber, where air and fuel are combined. This chamber's geometry and volume impact the mixing process. A well-designed mixing chamber ensures a homogeneous fuel-air mixture, which is essential for optimal combustion. The design may incorporate baffles or other structures to guide the airflow and fuel, promoting efficient mixing and reducing the chances of fuel accumulation or air turbulence.
Furthermore, the carburetor's design influences the engine's performance characteristics. The fuel-air mixture's quality directly affects power output, throttle response, and overall engine behavior. A well-designed carburetor can provide a smooth power delivery, excellent low-end torque, and responsive acceleration. It also plays a role in engine stability, ensuring consistent performance across different operating ranges. The design's precision in fuel-air mixing contributes to the engine's efficiency and longevity.
The Ultimate Guide to Thread Sealants for Fuel Lines
You may want to see also
Fuel Line Material: Different materials affect fuel flow, pressure, and durability
The choice of material for the fuel line is a critical aspect of engine performance and longevity, especially when considering the connection to the carburetor. Different materials have distinct properties that can significantly impact fuel flow, pressure regulation, and overall durability. Here's an in-depth look at how various materials influence these factors:
- Rubber: Rubber fuel lines are a common choice due to their flexibility and cost-effectiveness. This material is ideal for routes that require some give, especially in areas with potential vibration or movement. Rubber's natural elasticity helps absorb minor shocks, ensuring a consistent fuel supply. However, rubber's performance can vary; some types may degrade over time, leading to cracks or leaks. High-temperature environments can accelerate this degradation, making rubber less suitable for long-term use in certain applications.
- Vinyl: Vinyl fuel lines offer a balance between cost and durability. They are more flexible than metal but less so than rubber, providing a good compromise for many vehicles. Vinyl is generally resistant to fuel degradation and can handle moderate temperatures. Its flexibility makes it suitable for routing around various engine components. However, like rubber, it may not be the best choice for high-performance applications where fuel pressure stability is crucial.
- Braided Steel: Braided steel fuel lines are known for their exceptional strength and pressure-bearing capacity. The braided design provides flexibility while maintaining rigidity when needed. This material is ideal for high-performance engines that require precise fuel pressure control. Braided steel can handle extreme temperatures and is less susceptible to corrosion, ensuring long-lasting performance. However, its rigidity might make it less suitable for certain engine layouts with limited space.
- Stainless Steel: For the most demanding applications, stainless steel fuel lines are an excellent option. This material offers superior corrosion resistance, ensuring longevity even in harsh environments. Stainless steel's strength and ability to withstand high temperatures make it ideal for racing or high-performance vehicles. It provides excellent pressure regulation and fuel flow consistency. While it may be more expensive, the investment is justified for those seeking the highest level of durability and performance.
In summary, the material of the fuel line plays a pivotal role in the overall health and performance of the engine, particularly when connected to the carburetor. Each material offers unique advantages, and the choice depends on the specific requirements of the vehicle, including performance needs, environmental conditions, and budget constraints. Understanding these material properties ensures that the fuel system is optimized for efficient and reliable operation.
Optimal Fuel Line Size for Efficient Beckett Oil Furnace Performance
You may want to see also
Connection Type: Various connection types ensure secure fuel delivery and prevent leaks
The connection between the carburetor and fuel line is a critical component of an engine's fuel system, and the type of connection used can significantly impact performance and reliability. Various connection types are employed to ensure a secure and leak-free fuel delivery system, which is essential for optimal engine operation.
One common connection type is the rubber hose with a clamp. This design utilizes a flexible rubber hose that connects the carburetor to the fuel line. The hose is secured in place using a metal or plastic clamp, which provides a tight seal. This method is simple and cost-effective, allowing for easy installation and replacement. The clamp's grip ensures that the hose remains firmly attached, preventing any potential leaks that could lead to engine misfires or performance issues.
Another approach is the use of a fuel line with a quick-connect fitting. These fittings are designed with a male and female end, allowing for a snap-on connection. This type of connection is often found on modern vehicles and offers a secure and reliable way to join the fuel line to the carburetor. Quick-connect fittings typically feature a locking mechanism to ensure the connection is tight and won't come loose during operation. This design also makes it easier for mechanics to service the fuel system without specialized tools.
In some cases, a metal fuel line with a threaded connection is used. This method involves threading the fuel line onto a corresponding port on the carburetor. The threads provide a mechanical lock, ensuring a secure connection. While this connection type may require more precise installation, it offers excellent durability and resistance to fuel-related degradation. Threaded connections are often found in high-performance applications where fuel efficiency and power are critical.
Additionally, some engines may use a combination of these connection types. For instance, a rubber hose with a quick-connect fitting can be employed to provide a flexible and easily replaceable connection. This hybrid approach allows for customization based on the engine's specific requirements and the manufacturer's preferences.
In summary, the connection type between the carburetor and fuel line is a crucial aspect of engine design, and various connection methods are employed to ensure secure fuel delivery. Each connection type offers unique advantages, catering to different engine needs and performance expectations. Whether it's a simple clamp-style connection or a more complex threaded design, these connections play a vital role in maintaining a reliable and efficient fuel system.
Perfect Fuel Line Size for Harley-Davidson Crossover: Expert Guide
You may want to see also
Vacuum Effects: Engine vacuum impacts fuel-air ratio and carburetor operation
The engine's vacuum plays a crucial role in the intricate dance of fuel-air mixture management, especially when it comes to the interaction between the carburetor and the fuel system. When an engine is running, it creates a vacuum, which is essentially a region of low pressure. This vacuum has a significant impact on the carburetor's performance, particularly in the delicate process of mixing fuel and air.
At the heart of this process is the carburetor, a component responsible for precisely metering and mixing the air-fuel mixture. The carburetor's primary function is to ensure that the engine receives the correct ratio of fuel and air for optimal combustion. This ratio is critical, as too much or too little fuel can lead to poor engine performance, reduced power, and even potential damage. The vacuum created by the engine's operation directly influences this delicate balance.
As the engine runs, the vacuum pulls air through the carburetor's float bowl and into the carburetor's body. This air is then mixed with the fuel, creating the air-fuel mixture. The strength of this vacuum is essential because it determines the amount of air that can be drawn into the carburetor. A stronger vacuum allows for a more significant air intake, which, in turn, affects the fuel-air ratio. When the vacuum is at its peak, it pulls more air into the system, diluting the fuel and creating a leaner mixture. Conversely, a weaker vacuum results in a richer mixture as less air is available for the fuel.
The carburetor's design incorporates a series of jets and passages that regulate the fuel flow based on the engine's vacuum. These components ensure that the fuel-air mixture is delivered at the correct rate and in the right proportion. For instance, a carburetor might have a main jet that controls the overall fuel flow and a series of smaller jets that adjust the mixture based on engine speed and load. The vacuum's influence on these jets is vital, as it modulates their opening and closing, thus fine-tuning the fuel-air ratio.
Understanding the vacuum's impact on the carburetor and fuel-air mixture is essential for engine tuning and troubleshooting. Mechanics and enthusiasts often adjust the carburetor's settings, such as jet sizes and vacuum advance, to optimize performance. By manipulating these factors, they can ensure that the engine operates efficiently across various speeds and loads. This process highlights the intricate relationship between engine vacuum, carburetor design, and the ultimate goal of delivering a balanced fuel-air mixture for efficient combustion.
Fuel Line Dimensions for 2004 VW Beetle
You may want to see also
Airflow Considerations: Airflow around the carburetor affects fuel atomization and engine performance
The carburetor is a critical component in an internal combustion engine's fuel system, and its placement and orientation significantly impact engine performance. One crucial aspect often overlooked is the airflow around the carburetor itself. The carburetor's primary function is to mix air and fuel in the correct ratio for combustion, and this process is highly dependent on the surrounding airflow.
When considering the airflow around the carburetor, it's essential to understand the concept of 'airflow velocity'. This refers to the speed at which air moves past the carburetor. A higher airflow velocity can lead to better fuel atomization, which is the process of breaking down fuel into tiny droplets. This is crucial because smaller fuel droplets provide a larger surface area, allowing for more efficient combustion. As a result, the engine can burn fuel more effectively, leading to improved performance and power output.
The design of the carburetor and its location within the engine bay play a vital role in achieving optimal airflow. A well-designed carburetor should have an efficient air intake system that directs air smoothly and at an optimal velocity towards the carburetor's jetting. This ensures that the air passing through the carburetor is clean and free of contaminants, which is essential for proper fuel-air mixture formation. Additionally, the carburetor's orientation should be such that it doesn't create excessive turbulence, as this can disrupt the airflow and lead to uneven fuel atomization.
In practice, engineers often use a technique called 'airflow shaping' to optimize the airflow around the carburetor. This involves carefully designing the engine bay and carburetor housing to guide the airflow in a specific direction. By controlling the airflow, engineers can ensure that the air passing through the carburetor is at the right velocity and angle, promoting efficient fuel atomization. This is particularly important in high-performance engines where precise fuel-air mixture control is critical for optimal power delivery.
In summary, the airflow around the carburetor is a critical factor in engine performance. Proper airflow velocity and design considerations ensure that the air passing through the carburetor facilitates efficient fuel atomization. By understanding and optimizing these airflow aspects, engineers can enhance engine performance, improve fuel efficiency, and deliver a more responsive and powerful driving experience.
Silverado 1500 Fuel Lines: Location and Maintenance Tips
You may want to see also
Frequently asked questions
The carburetor is typically located near the front of the engine, often just in front of the cylinder head. It is a crucial component in older engines, responsible for mixing air and fuel for combustion.
The fuel lines are usually made of rubber or plastic and are connected to the carburetor's float bowl. The lines draw fuel from the tank and deliver it to the carburetor, where it is then distributed to the engine's cylinders.
Replacing a carburetor can be a complex task and is often best left to professionals. It requires a good understanding of engine mechanics and the specific make and model of the vehicle. It's recommended to consult a mechanic or refer to the vehicle's manual for guidance on this process.