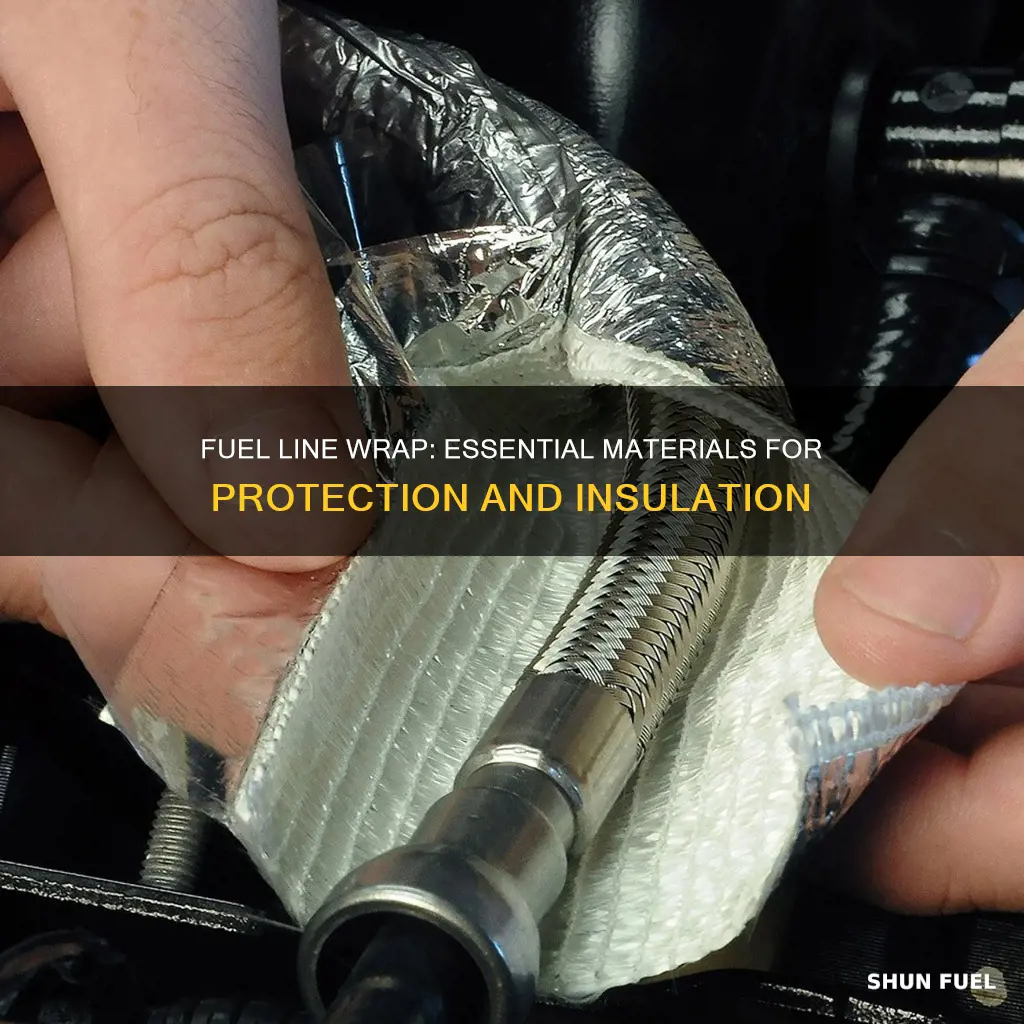
When it comes to wrapping fuel lines, there are several materials and techniques that can be used to ensure optimal performance and safety. The choice of material depends on various factors, including the type of fuel, environmental conditions, and the specific application. Common options include specialized rubber compounds, synthetic materials like Teflon or Kevlar, and even metal braiding for high-temperature or high-pressure applications. Understanding the properties and compatibility of these materials is crucial to selecting the right wrap for fuel lines, ensuring a secure and reliable fuel delivery system.
What You'll Learn
- Insulation Materials: Wrap fuel lines with foam, rubber, or plastic insulation
- Heat Shielding: Use metal or heat-resistant tape to protect against heat sources
- Flexibility: Opt for flexible materials like rubber or silicone for easy movement
- Vibration Resistance: Choose materials that can withstand engine vibrations and movement
- Chemical Resistance: Select materials resistant to fuel chemicals to prevent degradation
Insulation Materials: Wrap fuel lines with foam, rubber, or plastic insulation
When it comes to insulating fuel lines, there are several materials that can be effectively used to ensure optimal performance and longevity. One popular choice is foam insulation, which is lightweight and easy to apply. It provides excellent thermal insulation, helping to maintain the temperature of the fuel and prevent excessive heat or cold from affecting the fuel's quality. Foam insulation is also flexible, allowing it to conform to the shape of the fuel line, ensuring a secure and snug fit. This material is often used in automotive applications due to its durability and resistance to vibration, ensuring that the fuel lines remain insulated even under the most demanding conditions.
Another effective insulation material is rubber. Rubber insulation offers a robust and reliable solution for fuel line protection. It is highly flexible, enabling it to accommodate any bends or twists in the fuel line's route. Additionally, rubber is known for its excellent resistance to heat and chemicals, making it ideal for fuel lines that may be exposed to varying temperatures and fuel types. This insulation material is commonly used in industrial settings where heavy-duty protection is required.
Plastic insulation is also a viable option for wrapping fuel lines. Plastic is lightweight and offers good thermal insulation properties. It is often used in conjunction with other materials, such as foam or rubber, to provide a comprehensive insulation solution. Plastic insulation is particularly useful in areas where moisture or humidity is a concern, as it is resistant to water absorption, ensuring that the fuel lines remain protected.
The choice of insulation material depends on various factors, including the specific application, environmental conditions, and the type of fuel being used. Foam insulation is versatile and cost-effective, making it a popular choice for general automotive applications. Rubber insulation, with its superior heat and chemical resistance, is ideal for high-temperature environments or industrial settings. Plastic insulation, while not as durable as rubber, is lightweight and moisture-resistant, making it suitable for certain specialized applications.
In summary, when insulating fuel lines, consider the properties of foam, rubber, and plastic insulation. Each material offers unique advantages, ensuring that your fuel lines remain protected and efficient. Whether it's the flexibility of rubber, the versatility of foam, or the moisture-resistant nature of plastic, the right insulation material will contribute to the overall performance and longevity of your fuel system.
Stihl BR600 Fuel Line Hose: Unlocking the Secrets
You may want to see also
Heat Shielding: Use metal or heat-resistant tape to protect against heat sources
Heat shielding is an essential step when wrapping fuel lines to ensure the safety and longevity of your vehicle's fuel system. The primary goal is to protect the fuel lines from excessive heat, which can cause damage over time. One effective method is to use metal heat shields or heat-resistant tape, which can provide an extra layer of defense against heat sources.
Metal heat shields are a popular choice for this purpose. These shields are typically made from materials like aluminum or stainless steel, which have excellent heat resistance. They are designed to fit snugly around the fuel lines, creating a barrier between the fuel and the heat source. Metal shields are especially useful in high-temperature environments, such as under the hood of a vehicle, where temperatures can soar. By using metal, you create a robust and durable shield that can withstand extreme conditions, ensuring the fuel lines remain intact.
Heat-resistant tape is another viable option for heat shielding. This type of tape is specifically formulated to endure high temperatures and is often made from materials like fiberglass or ceramic. It can be easily applied to the fuel lines, providing a flexible and customizable solution. Heat-resistant tape is ideal for situations where a more permanent solution is not required, or for those who prefer a temporary fix. It offers good protection against heat and can be a cost-effective alternative to metal shields.
When using either metal heat shields or heat-resistant tape, it is crucial to ensure a proper fit. The material should be securely wrapped around the fuel lines, leaving no gaps or spaces where heat can penetrate. A good fit also helps to prevent the tape or shield from coming loose over time due to vibrations or temperature changes. Consider using adhesive or mechanical fasteners to secure the shielding in place for optimal protection.
In addition to heat shielding, it is recommended to inspect and maintain the fuel lines regularly. Look for any signs of damage, such as cracks or leaks, and address them promptly. Proper maintenance, combined with effective heat shielding, will contribute to the overall reliability and performance of your vehicle's fuel system. Remember, taking these precautions can help prevent costly repairs and ensure a safe and efficient driving experience.
Alcohol Fuel Line Sizing: Expert Guide to Optimal Performance
You may want to see also
Flexibility: Opt for flexible materials like rubber or silicone for easy movement
When it comes to choosing the right material to wrap your fuel lines, flexibility is a crucial factor to consider. Fuel lines are often subject to movement and vibration, especially in high-performance vehicles or those with engine modifications. This is where flexible materials like rubber or silicone come into play, offering a range of benefits that can enhance the performance and longevity of your fuel system.
Rubber and silicone are natural choices for fuel line wrapping due to their inherent flexibility. These materials can easily conform to the shape of the fuel lines, allowing for smooth movement and reducing the risk of damage during engine operation. Unlike rigid materials, which can become brittle over time, rubber and silicone maintain their pliability, ensuring that the fuel lines remain protected even under extreme conditions. This flexibility is particularly important in areas where the fuel lines may need to bend or twist, such as around engine components or through engine compartments.
The use of flexible materials also simplifies the installation process. With their ability to conform to the fuel lines, rubber or silicone wraps can be easily applied without the need for excessive force or complex maneuvering. This makes the wrapping process more accessible to both professionals and DIY enthusiasts, reducing the time and effort required for a successful installation. Additionally, the flexibility of these materials allows for a more secure fit, minimizing the chances of fuel leaks or damage caused by sharp bends.
In high-performance applications, where engine vibrations and acceleration forces are significant, the flexibility of rubber or silicone becomes even more critical. These materials can absorb and dampen vibrations, reducing the stress on the fuel lines and preventing potential damage. By choosing flexible wraps, you create a buffer between the fuel lines and the engine, ensuring that the fuel system remains intact and functional even during aggressive driving conditions.
Furthermore, the durability of rubber and silicone should not be overlooked. Despite their flexibility, these materials are known for their resistance to heat, oil, and fuel, making them ideal for withstanding the harsh environment of an engine bay. This durability ensures that the fuel lines remain protected over the long term, providing peace of mind and reliability for vehicle owners.
Chevy Fuel Tank: Understanding the Lines and Connections
You may want to see also
Vibration Resistance: Choose materials that can withstand engine vibrations and movement
When it comes to choosing the right material to wrap fuel lines, one of the most critical considerations is vibration resistance. Fuel lines are subject to constant movement and vibrations within the engine compartment, which can lead to potential issues over time. To ensure the longevity and reliability of your fuel system, it's essential to select materials that can withstand these harsh conditions.
One effective approach is to use materials with inherent flexibility and durability. Rubber, for instance, is a popular choice due to its natural ability to absorb vibrations and maintain its shape. High-quality rubber fuel line wrappers can provide excellent protection against engine movement, preventing potential leaks and ensuring a secure fit. Look for rubber compounds specifically designed for automotive applications, as they are often reinforced with fibers to enhance strength and flexibility.
Another option to consider is braided materials, such as steel or stainless steel. These materials offer exceptional vibration resistance due to their inherent rigidity and ability to retain shape. Braided fuel line wrappers are commonly used in high-performance applications where extreme vibrations are expected. The tight braiding pattern provides a secure hold, minimizing the risk of fuel line movement and potential damage.
Additionally, some manufacturers offer specialized fuel line wrappers made from composite materials. These materials combine the flexibility of rubber with the strength of synthetic fibers, resulting in a highly durable product. Composite wrappers can withstand intense engine vibrations without compromising their protective properties. They are often used in racing applications or in vehicles with modified engines, where traditional rubber may not provide sufficient protection.
In summary, when wrapping fuel lines, prioritize materials that offer superior vibration resistance. Rubber, braided steel, and composite materials are excellent choices, each providing unique benefits. By selecting the right material, you can ensure that your fuel lines remain secure, protected, and reliable, even in the most demanding engine environments. Remember, investing in high-quality materials will contribute to the overall performance and longevity of your vehicle's fuel system.
Understanding R3 Fuel Line: A Comprehensive Guide
You may want to see also
Chemical Resistance: Select materials resistant to fuel chemicals to prevent degradation
When it comes to choosing the right material to wrap fuel lines, chemical resistance is a critical factor to consider. Fuel lines are exposed to various chemicals that can cause degradation over time, leading to potential leaks and system failures. Therefore, selecting materials that are resistant to these chemicals is essential to ensure the longevity and reliability of your fuel system.
One of the primary chemicals found in fuel is gasoline, which contains a variety of hydrocarbons and additives. These components can dissolve or degrade certain materials, making them unsuitable for fuel line wrapping. For instance, rubber, while commonly used, is not an ideal choice due to its susceptibility to gasoline dissolution. Instead, opt for materials like fluoropolymers or specialized rubber compounds designed to withstand the corrosive effects of gasoline.
Another important consideration is the presence of ethanol in modern fuels. Ethanol is a polar solvent that can attack certain plastics and rubbers, leading to swelling and degradation. Materials such as nylon, polyester, or ethylene-propylene-diene monomer (EPDM) rubber are more resistant to ethanol and can provide better long-term protection for fuel lines in vehicles that use ethanol-blended fuels.
Additionally, diesel fuel contains different chemicals compared to gasoline, including sulfur and aromatic hydrocarbons. Materials that are resistant to these chemicals, such as fluorinated polymers or specific rubber compounds, should be considered for diesel fuel lines. These materials can help prevent degradation and ensure the integrity of the fuel system, even in harsher environments.
In summary, when selecting materials to wrap fuel lines, it is crucial to prioritize chemical resistance. By choosing materials that are resistant to the specific chemicals present in the fuel, you can effectively prevent degradation and ensure the reliability of your fuel system. This includes considering the types of fuels used and selecting materials that can withstand the unique challenges posed by different fuel compositions.
Choosing the Right B Nut for 3/4 Inch Fuel Lines
You may want to see also
Frequently asked questions
The ideal material for wrapping fuel lines is a high-temperature-resistant tape or insulation, such as a silicone-based tape or a specialized fuel line wrap. These materials can withstand the high temperatures and pressures associated with fuel systems and provide excellent protection against fuel leaks.
While regular electrical tape might seem like a quick fix, it is not suitable for fuel line wrapping. Electrical tape is not designed for high-temperature environments and may not adhere well to the fuel line material. It can also degrade over time due to fuel exposure, leading to potential leaks. It's best to use specialized materials for this purpose.
The choice of width and thickness depends on the specific fuel line and application. Thicker wraps provide more insulation and protection but may be more challenging to work with. A standard width of 1/2 inch (12.7 mm) is commonly used for fuel lines, but you can opt for narrower wraps if space is limited. Thinner wraps are more flexible and easier to apply, while thicker ones offer better coverage and security. Always consider the fuel line's diameter and the level of protection required when selecting the wrap dimensions.