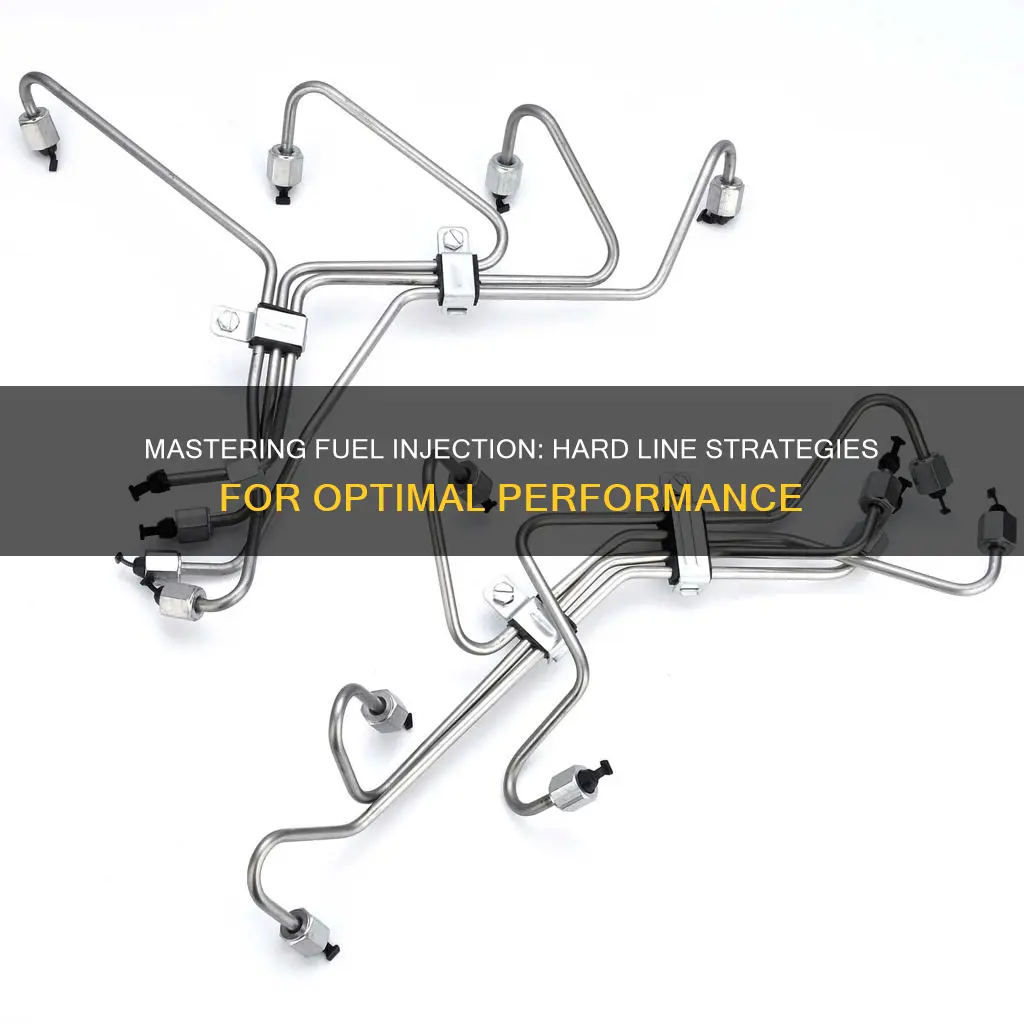
When it comes to fuel injection, a hard line is a crucial component that ensures optimal performance and efficiency. This paragraph will delve into the importance of using a hard line with fuel injection systems, exploring how it contributes to the precise delivery of fuel, improved engine performance, and enhanced overall reliability. By understanding the role of a hard line, readers can appreciate the significance of this often-overlooked component in modern vehicle engineering.
What You'll Learn
- Fuel Injection Basics: Understanding the principles of fuel injection systems and their components
- Hard Line Design: Exploring the design considerations for hard lines in fuel injection systems
- Pressure Regulation: Techniques for maintaining optimal fuel pressure and flow in hard lines
- Material Selection: Choosing appropriate materials for hard lines to ensure durability and performance
- Troubleshooting Hard Lines: Common issues and solutions for diagnosing and repairing hard line problems
Fuel Injection Basics: Understanding the principles of fuel injection systems and their components
Fuel injection is a sophisticated technology that has revolutionized the automotive industry, offering improved engine performance, efficiency, and control. At its core, fuel injection is a process that precisely delivers fuel to an engine's cylinders, replacing the traditional carburetor system. This system operates on the principle of injecting fuel directly into the combustion chamber, ensuring optimal air-fuel mixture for combustion.
The fuel injection system consists of several key components, each playing a vital role in the overall functionality. Firstly, the fuel pump is responsible for supplying fuel from the tank to the high-pressure fuel rail. This pump ensures a consistent and controlled flow of fuel, which is crucial for accurate injection. The high-pressure fuel rail stores the fuel at elevated pressure, ready for injection.
One of the most critical components is the fuel injectors. These are small, precise valves that spray fuel into the engine's intake manifold or directly into the cylinders. Each cylinder typically has its own dedicated injector, allowing for individual control of fuel delivery. The injectors are designed to open and close rapidly, ensuring the right amount of fuel is injected at the correct time. This precision is achieved through the use of solenoids, which are electromagnetic valves that control the injector's operation.
The electronic control unit (ECU) is the brain of the fuel injection system. It receives input from various sensors, such as the engine's temperature, speed, and load, and uses this data to calculate the optimal fuel injection timing and amount. The ECU then sends commands to the fuel injectors and other system components to ensure the engine operates efficiently and within specified parameters.
Understanding the principles of fuel injection is essential for mechanics and enthusiasts alike. It involves recognizing the importance of each component's role, from the fuel pump's initial supply to the ECU's precise control. By grasping these basics, one can appreciate the complexity and benefits of fuel injection systems, ensuring proper maintenance and optimization of engine performance.
Understanding Fuel Lines: The Vital Link in Your Engine's Fuel Supply
You may want to see also
Hard Line Design: Exploring the design considerations for hard lines in fuel injection systems
The design of hard lines in fuel injection systems is a critical aspect of engine performance and reliability. These lines, also known as high-pressure fuel lines, play a vital role in delivering fuel from the fuel pump to the injectors with precision and efficiency. When designing hard lines, several key considerations come into play to ensure optimal performance and longevity.
One of the primary design considerations is the material selection. Hard lines must be constructed from materials that can withstand the high-pressure environment and the corrosive effects of fuel. Common materials used include high-strength steel, stainless steel, or specialized fuel-resistant polymers. The chosen material should offer excellent durability, flexibility, and resistance to fuel degradation to ensure long-term reliability.
Another crucial factor is the line's diameter and length. The diameter should be carefully calculated to handle the required fuel flow rate while minimizing pressure drop. Longer lines may be necessary to route fuel from the pump to the injectors, especially in complex engine layouts. Designers must balance the line's length and diameter to optimize fuel delivery without introducing unnecessary restrictions or pressure losses.
Additionally, the design should incorporate features to prevent fuel leakage and ensure a tight seal. This includes using appropriate fittings, gaskets, and seals that can withstand high pressure. Proper sealing is essential to maintain the integrity of the fuel system and prevent fuel wastage or potential safety hazards.
Furthermore, the design should consider the flexibility of the hard lines to accommodate engine movement during operation. Engines experience vibrations and thermal expansion, so the lines must be flexible enough to absorb these movements without compromising fuel delivery. This can be achieved through the use of flexible hoses, braids, or specialized flexible tubing.
In summary, hard line design in fuel injection systems requires careful consideration of material selection, line dimensions, sealing mechanisms, and flexibility. By addressing these design considerations, engineers can create robust and efficient fuel lines that contribute to the overall performance and longevity of the engine.
Street Avenger Fuel Line: Unleash the Power with the Right Choice
You may want to see also
Pressure Regulation: Techniques for maintaining optimal fuel pressure and flow in hard lines
When it comes to fuel injection systems, maintaining optimal fuel pressure and flow is crucial for efficient engine performance. Hard lines, also known as high-pressure fuel lines, play a vital role in this process. These lines are responsible for transporting fuel from the fuel pump to the engine, ensuring a steady and precise supply of fuel to the injectors. However, hard lines can be susceptible to pressure drops and flow restrictions, which can negatively impact engine performance. To address this, several techniques can be employed to regulate pressure and maintain optimal fuel flow.
One effective method is the use of pressure regulators. These devices are installed in the hard lines and are designed to control the fuel pressure at a specific level. Pressure regulators typically consist of a precision-engineered valve that opens and closes based on the fuel pressure. When the pressure exceeds a predetermined threshold, the valve opens, allowing fuel to flow through. Conversely, when the pressure drops, the valve closes, preventing excessive fuel flow. By regulating the pressure, these devices ensure that the fuel injectors receive the correct amount of fuel at the desired pressure, promoting efficient combustion and engine performance.
Another technique for pressure regulation is the implementation of pressure-reducing nozzles. These nozzles are strategically placed along the hard lines and are designed to reduce the fuel pressure as it travels towards the engine. By gradually decreasing the pressure, these nozzles help to maintain a consistent fuel flow rate throughout the system. This is particularly important in high-pressure fuel lines, where sudden pressure drops can lead to inefficient fuel distribution. Pressure-reducing nozzles ensure that the fuel injectors receive a steady supply of fuel, optimizing engine performance and responsiveness.
Additionally, the use of fuel filters can contribute to pressure regulation and overall fuel system health. Filters are installed at various points in the hard lines to remove contaminants and ensure clean fuel delivery. Over time, fuel can accumulate impurities, including water, sediment, and varnish, which can restrict flow and cause pressure drops. Regularly replacing fuel filters helps to maintain optimal fuel pressure and flow, ensuring that the engine receives the necessary amount of fuel for efficient operation.
In summary, maintaining optimal fuel pressure and flow in hard lines is essential for the performance of fuel injection systems. Techniques such as pressure regulators, pressure-reducing nozzles, and regular fuel filter maintenance play a crucial role in achieving this. By implementing these strategies, engine enthusiasts and mechanics can ensure that their fuel injection systems operate at their peak, delivering clean and precise fuel to the injectors for optimal combustion and engine performance.
Clogged Fuel Return Line: Engine Performance and Safety Risks
You may want to see also
Material Selection: Choosing appropriate materials for hard lines to ensure durability and performance
When it comes to hard lines for fuel injection systems, material selection is a critical aspect that directly impacts the overall performance and longevity of the system. The primary goal is to choose materials that can withstand the harsh conditions within the engine bay, including high temperatures, fuel pressures, and chemical exposure. Here's an in-depth look at the key considerations for material selection:
- Temperature Resistance: Engine compartments can reach extremely high temperatures, especially during prolonged operation. Materials used for hard lines should have a high melting point and excellent thermal stability. For instance, stainless steel is a popular choice due to its ability to resist corrosion and maintain structural integrity at elevated temperatures. It is commonly used for fuel lines and hoses in high-performance applications. Alternatively, silicone-based materials offer flexibility and can handle a wide temperature range, making them suitable for various engine bay environments.
- Chemical Compatibility: Fuel injection systems operate in a corrosive environment, with fuel containing various additives and potentially harmful substances. The chosen material must be chemically inert and resistant to degradation when exposed to these substances. For example, nylon or polyether block (PEB) materials are often used for their excellent chemical resistance, ensuring the hard lines remain intact over time. These materials can withstand the presence of fuels, oils, and other engine fluids without deteriorating.
- Flexibility and Durability: Hard lines need to be flexible enough to navigate through tight engine spaces and engine mounts while also being durable to resist kinking, crushing, or damage during installation and operation. Materials like braided stainless steel or high-temperature rubber compounds are often employed. Braided stainless steel offers excellent flexibility and durability, making it ideal for high-pressure fuel lines. It can withstand the rigors of engine operation without compromising performance.
- Pressure Rating: Fuel injection systems operate under significant pressure, so the chosen material must be able to handle these forces without failure. Materials like PEB or nylon can provide the necessary pressure resistance, ensuring a reliable fuel supply to the injectors. These materials are engineered to maintain their structural integrity under pressure, preventing leaks or system failures.
- Cost and Availability: Practical considerations include the cost and availability of materials. While high-performance materials offer superior performance, they may also be more expensive. Finding a balance between performance and cost is essential for many applications. For instance, some manufacturers might opt for standard stainless steel or PEB, which are widely available and offer good performance at a lower cost.
In summary, material selection for hard lines in fuel injection systems requires a careful consideration of temperature resistance, chemical compatibility, flexibility, pressure rating, and cost. By choosing the right materials, engineers can ensure that the fuel injection system operates efficiently and reliably, even in the most demanding conditions. This attention to detail is crucial for maintaining engine performance and longevity.
Unveiling Ford's Fuel Supply Line Color: A Quick Guide
You may want to see also
Troubleshooting Hard Lines: Common issues and solutions for diagnosing and repairing hard line problems
When dealing with fuel injection systems, the 'hard line' typically refers to the high-pressure fuel lines that connect the fuel pump to the engine. These lines are crucial for delivering fuel at the precise pressure required for efficient combustion. However, they can be prone to various issues that may affect performance and engine operation. Here's a guide to troubleshooting and repairing hard line problems:
Leaks and Cracks: One of the most common issues with hard lines is leaks or cracks. Over time, these lines can develop small punctures or leaks due to wear, corrosion, or damage from road debris. Inspect the lines regularly for any signs of leakage, especially at connections and bends. If you notice a leak, it's essential to act promptly. Start by identifying the source of the leak; it could be a damaged section of the line, a faulty fitting, or a worn-out gasket. Replace the affected line segment or fitting with a new one, ensuring a tight and secure connection. For minor cracks, temporary solutions like sealing compounds or tape can be used, but a permanent fix is necessary for long-term reliability.
Clogged Lines: Hard lines can also become clogged, leading to reduced fuel flow and potential engine performance issues. Clogs can be caused by various factors, including contamination from fuel additives, water accumulation, or the formation of deposits over time. To troubleshoot clogged lines, start by checking for any visible blockages, such as debris or sediment. If you find a blockage, carefully remove it using a fuel filter or line cleaning tool. In some cases, the line may need to be replaced if the clog is extensive or recurring. Regularly replacing fuel filters can also help prevent clogs and maintain optimal fuel flow.
Pressure Issues: Hard lines are responsible for maintaining the required fuel pressure for the engine. If these lines fail to deliver the correct pressure, it can result in poor engine performance, misfires, or starting difficulties. To address pressure-related problems, first check the fuel pump's operation and ensure it is delivering the correct pressure. If the pump is functioning correctly, inspect the hard lines for any restrictions or damage that might affect pressure. Consider using a fuel pressure gauge to measure the pressure at different points in the system, helping to pinpoint the exact location of the issue.
Diagnosis and Testing: Diagnosing hard line problems often requires a systematic approach. Start by checking the fuel pressure at the engine's fuel rail or injectors using a suitable gauge. Compare the measured pressure with the manufacturer's specifications to determine if the line is functioning correctly. Visual inspections are also crucial; look for any signs of damage, corrosion, or debris buildup. In some cases, a professional diagnostic tool can be connected to the engine's computer to retrieve error codes, which may provide valuable insights into the issue.
Maintenance and Prevention: Regular maintenance can help prevent hard line issues. Keep the fuel system clean by regularly replacing fuel filters and using fuel system cleaner to remove contaminants. Inspect the hard lines during routine engine maintenance checks to identify potential problems early. Additionally, ensure that the fuel pump and injectors are properly lubricated to reduce wear and tear on the fuel lines. By following these troubleshooting steps and implementing preventive measures, you can effectively manage and repair hard line problems, ensuring optimal performance from your fuel injection system.
Understanding In-Line Fuel Filters: Benefits and Maintenance Tips
You may want to see also
Frequently asked questions
In the automotive world, a "hard line" refers to a fuel line made of rigid materials like steel or brass. These lines are designed to withstand high pressure and are often used in high-performance applications where flexibility is not a priority.
Hard lines offer several advantages. They provide a more consistent fuel flow due to their rigid structure, ensuring that the fuel pressure remains stable. This is crucial for precise engine control, especially in racing or high-performance vehicles. Additionally, hard lines are less susceptible to damage from engine movement or external factors.
While hard lines offer benefits in terms of stability and durability, they can be more challenging to install due to their rigidity. They may require more careful routing to avoid sharp bends or kinks, which could restrict fuel flow. Furthermore, the cost of hard lines can be higher compared to flexible alternatives.
The decision to use a hard line depends on your specific application and requirements. If you're building a high-performance engine or racing car, where fuel pressure stability and consistency are critical, a hard line might be the better choice. However, for everyday use or low-power applications, flexible lines are often sufficient and easier to work with. It's essential to consider factors like engine power, fuel pressure, and the overall design of your fuel injection system when making this decision.