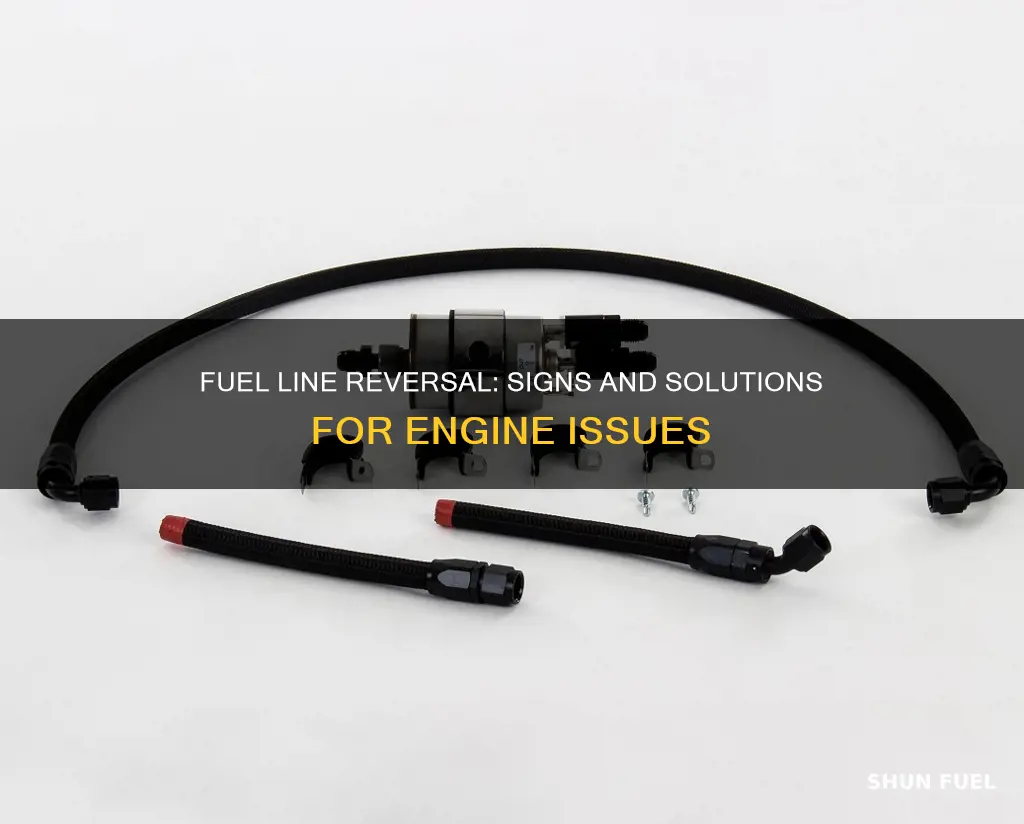
Identifying if fuel lines are installed incorrectly, or backwards, is crucial for maintaining vehicle performance and safety. This issue can lead to fuel delivery problems, causing engines to run poorly or even fail to start. By understanding the signs and following a systematic approach to inspection, you can quickly determine if the fuel lines are installed incorrectly. This guide will outline the key indicators and steps to help you identify and address this common automotive issue.
What You'll Learn
- Visual Inspection: Check for fuel leaks, blockages, and proper connections
- Pressure Test: Measure fuel pressure to ensure correct flow direction
- Engine Performance: Monitor engine idling, acceleration, and power output
- Fuel Gauge: Verify fuel level accuracy and gauge sensitivity
- Fuel Filter: Inspect for clogs and debris, ensuring clean fuel flow
Visual Inspection: Check for fuel leaks, blockages, and proper connections
A visual inspection is a crucial step in determining if your fuel lines are installed correctly and identifying any potential issues. This method allows you to assess the system's integrity and ensure it functions optimally. Here's a detailed guide on how to perform this inspection:
Start by locating the fuel lines, which are typically made of rubber or plastic and run from the fuel tank to the engine. These lines can be found under the vehicle, often along the frame or behind the engine compartment. Inspect the lines for any visible signs of damage, cracks, or deterioration. Look for any areas where the rubber or plastic may be worn, torn, or showing signs of aging. Even minor damage can lead to fuel leaks, so it's essential to be thorough. Check for any blockages or clogs that might obstruct the fuel flow. This could be caused by dirt, debris, or even small stones that might have entered the system. Ensure that the fuel lines are not kinked or twisted, as this can restrict fuel flow and potentially cause engine performance issues.
Now, let's focus on the connections. Fuel lines are connected to the fuel tank and the engine using various fittings and clamps. Inspect these connections for tightness and proper alignment. Ensure that all fittings are secure and tight, as loose connections can lead to fuel leaks. Look for any signs of corrosion or damage around the connection points, as this could compromise the seal. It's also important to check for any signs of fuel leaks at these connections. Even a small leak can cause significant issues over time. If you notice any fuel dripping or a sweet odor, it's a clear indication of a potential problem.
Additionally, pay attention to the direction of the fuel lines. If the lines are installed incorrectly, they might be running in the wrong direction, which can lead to fuel delivery issues. Properly oriented fuel lines ensure that the fuel flows efficiently to the engine. If you suspect that the lines might be backwards, carefully examine the connections and the overall layout to identify any discrepancies.
During this visual inspection, it's also a good idea to check for any signs of fuel contamination. Look for any visible debris or sediment in the fuel lines, especially if your vehicle has been used in dirty or dusty conditions. Contaminated fuel can cause engine problems, so it's essential to address this issue promptly.
Remember, a thorough visual inspection can help you identify potential issues with your fuel lines before they become major problems. If you notice any leaks, blockages, or improper connections, it's best to consult a professional mechanic for further assistance.
Honda XR50 Fuel Line: Understanding the OD and OEM Specs
You may want to see also
Pressure Test: Measure fuel pressure to ensure correct flow direction
When it comes to diagnosing potential issues with your fuel system, a pressure test is a crucial step to ensure the correct flow direction of fuel lines. This test is particularly important as it helps identify if the fuel lines are installed backwards, which can lead to a variety of performance problems. By measuring the fuel pressure, you can verify the integrity of the fuel system and ensure that the fuel is being delivered to the engine efficiently.
To perform a pressure test, you'll need a fuel pressure gauge, which is a specialized tool designed for this purpose. Start by disconnecting the fuel lines from the fuel tank and the engine. It's essential to work on a clean, level surface to get accurate readings. Attach the fuel pressure gauge to the fuel line, ensuring a secure connection. The gauge should have a clear display to read the pressure value.
Next, start the engine and allow it to idle. With the engine running, the fuel pressure should be stable and within the manufacturer's specified range. If the pressure is too low, it could indicate a restriction or a problem with the fuel pump. Conversely, if the pressure is abnormally high, it might suggest a blocked fuel filter or a faulty pressure regulator. In both cases, further investigation is required to identify the root cause.
The key to this test is comparing the fuel pressure with and without the engine running. When the engine is off, the fuel pressure should be significantly lower, indicating that the fuel pump is not actively supplying fuel. However, when the engine is running, the fuel pressure should rise to the required level, ensuring a steady supply of fuel to the engine. Any significant deviation from these expected pressure values could indicate that the fuel lines are indeed backwards or that there are other underlying issues.
By conducting a pressure test, you can quickly narrow down the potential causes of fuel system problems. If the fuel pressure is incorrect, it's a strong indicator that the fuel lines need to be reconfigured or replaced. This simple yet effective test empowers vehicle owners and mechanics to diagnose fuel system issues efficiently, ensuring optimal engine performance and reliability. Remember, proper fuel flow direction is critical for efficient combustion and engine operation.
Mastering Fuel Line Sleeving: A Concrete Guide
You may want to see also
Engine Performance: Monitor engine idling, acceleration, and power output
When it comes to diagnosing potential issues with your fuel lines, monitoring engine performance is a crucial step. Here's how you can identify if the fuel lines might be installed incorrectly, affecting your engine's behavior:
Idling Performance: Start by observing your engine's idling speed and stability. If the fuel lines are backwards, it can lead to an improper fuel-air mixture, causing the engine to run rich (with excess fuel). This might result in a noticeable increase in idle speed, engine vibration, or even stalling. On the other hand, a lean mixture (too little fuel) can also occur, leading to a rough idle, decreased performance, and potential engine damage. Keep an eye on these symptoms, as they could indicate a reversed fuel line configuration.
Acceleration and Power: Monitoring acceleration and power output is essential. When the fuel lines are correctly positioned, the engine should deliver smooth and consistent power during acceleration. However, if the lines are backwards, you might experience a decrease in power, especially when the engine is under load. This is because the fuel is not being delivered efficiently to the combustion chambers, resulting in a less powerful performance. Pay attention to any changes in acceleration, as it could be an early indicator of fuel line issues.
Engine Misfires: Engine misfires, where the engine rattles or loses power, can also be a sign of improper fuel line installation. When the fuel lines are reversed, it can cause an uneven fuel distribution, leading to misfires and potential engine damage over time. Listen for any unusual sounds and feel for vibrations, as these could be early warning signs of fuel line problems.
In summary, monitoring engine idling, acceleration, and power output is a practical way to detect if your fuel lines are installed incorrectly. Any deviations from the normal engine behavior mentioned above could indicate a reversed fuel line configuration, prompting further investigation and potential repairs. Regularly checking these performance metrics can help you identify and address fuel line issues promptly.
Volvo S80 Fuel Line Cover Removal: A Step-by-Step Guide
You may want to see also
Fuel Gauge: Verify fuel level accuracy and gauge sensitivity
The fuel gauge in your vehicle is a critical component for monitoring fuel levels, and ensuring its accuracy is essential for safe and efficient driving. Here's a guide on how to verify the fuel level accuracy and gauge sensitivity:
Understanding the Fuel Gauge: Familiarize yourself with your car's fuel gauge system. It typically consists of a fuel sender unit, a gauge, and a set of sensors. The sender unit is usually located in the fuel tank and sends electrical signals to the gauge based on the fuel level. Understanding the gauge's scale and markings is crucial for accurate interpretation.
Checking Fuel Level Accuracy: To verify the accuracy of the fuel gauge, you can follow these steps. Firstly, fill your fuel tank completely and note the initial fuel level reading. Then, drive the vehicle until the fuel light comes on, indicating that the tank is almost empty. Stop and check the fuel level again, ensuring it matches the gauge reading. This test helps confirm that the gauge provides an accurate representation of the fuel remaining.
Calibrating the Gauge: Over time, fuel gauges may require calibration to maintain accuracy. This process involves adjusting the gauge's sensitivity to match the actual fuel level. You can typically find calibration procedures in your vehicle's owner's manual. It may involve using a fuel pump or a specialized tool to adjust the gauge's sensitivity until it aligns with the actual fuel volume.
Testing Gauge Sensitivity: Gauge sensitivity refers to how responsive the gauge is to changes in fuel level. You can test this by adding a small amount of fuel to the tank while monitoring the gauge's response. The gauge should reflect the added fuel accurately and promptly. If the gauge is slow to respond or shows inconsistent readings, it may indicate a sensitivity issue that requires attention.
Addressing Issues: If you notice discrepancies between the fuel gauge reading and the actual fuel level, or if the gauge becomes unresponsive, it's essential to address the issue promptly. This could be due to sensor malfunctions, electrical problems, or even fuel line issues, as mentioned in your initial research. Consulting a professional mechanic is advisable to diagnose and resolve any underlying problems with the fuel gauge system.
By following these steps, you can ensure that your fuel gauge provides reliable information, helping you manage your vehicle's fuel efficiency and safety effectively. Regular maintenance and calibration can contribute to accurate fuel level monitoring, giving you peace of mind while on the road.
Unraveling the Mystery: Suction Fuel Line for Your Poulan Wild Thing Chainsaw
You may want to see also
Fuel Filter: Inspect for clogs and debris, ensuring clean fuel flow
The fuel filter is a critical component in your vehicle's fuel system, responsible for ensuring that only clean fuel reaches the engine. Over time, this filter can become clogged with debris, contaminants, and even water, leading to reduced engine performance and potential damage. Regular inspection and maintenance of the fuel filter are essential to keep your vehicle running smoothly. Here's a step-by-step guide on how to inspect the fuel filter for clogs and debris:
- Locate the Fuel Filter: Start by locating the fuel filter in your vehicle. The position of the filter can vary depending on the make and model of your car. It is typically found along the fuel line, often near the engine or under the vehicle. Refer to your vehicle's manual if you're unsure of its exact location.
- Inspect for Visual Clues: Carefully examine the fuel filter for any visible signs of damage or contamination. Look for cracks, leaks, or excessive moisture. If you notice any issues, it may indicate that the filter needs to be replaced. Additionally, check for the presence of debris or dirt accumulation around the filter housing.
- Remove and Inspect: To get a more thorough inspection, you may need to remove the fuel filter. This process can vary, so consult your vehicle's manual for specific instructions. When removing the filter, be cautious of any fuel that may spill, and ensure you have a suitable container to catch it. Once removed, examine the filter element for clogs. You should see a clear, clean surface if the filter is functioning correctly. If you notice any blockages or a dirty appearance, it's a sign that the filter needs attention.
- Check for Fuel Flow: After inspecting the filter, it's essential to ensure that the fuel is flowing correctly. Start the vehicle's engine and listen for any unusual noises or vibrations. If the engine runs smoothly and quietly, it's a good sign that the fuel filter is clean and functioning properly. However, if you notice any changes in engine performance, such as reduced power or rough idling, it could indicate a clogged filter.
- Maintenance and Replacement: Regular maintenance of the fuel filter is crucial. If you find any clogs or debris during your inspection, consider replacing the filter to ensure optimal fuel flow. It is generally recommended to replace the fuel filter at regular service intervals or whenever you notice any issues with engine performance. Keeping the fuel filter clean and debris-free will help maintain the overall health of your vehicle's engine.
Briggs & Stratton Fuel Line: Top Sources & Tips
You may want to see also
Frequently asked questions
One way to check is by examining the fuel pump's location and the fuel filter. If the fuel pump is positioned to the right of the engine and the fuel filter is on the left, it's likely that the lines are installed correctly. However, if the fuel filter is on the right and the pump is on the left, the lines might be backwards.
Yes, you can look for signs of excessive fuel pressure or leaks. If the lines are backwards, the fuel pressure might be too high, causing the fuel pump to overheat or the lines to burst. Additionally, you may notice fuel leaking around the connections or under the vehicle, indicating a potential issue with the installation.
Absolutely. By connecting a fuel pressure gauge to the fuel lines, you can measure the pressure at different points. If the gauge reads consistently high pressure, it could suggest that the lines are backwards, as the pump would be working against the natural flow of fuel.
Fuel lines installed incorrectly can lead to poor engine performance, such as reduced power and fuel efficiency. It may also cause the engine to stall or misfire. In some cases, the incorrect installation can damage the fuel pump or other engine components, resulting in costly repairs.