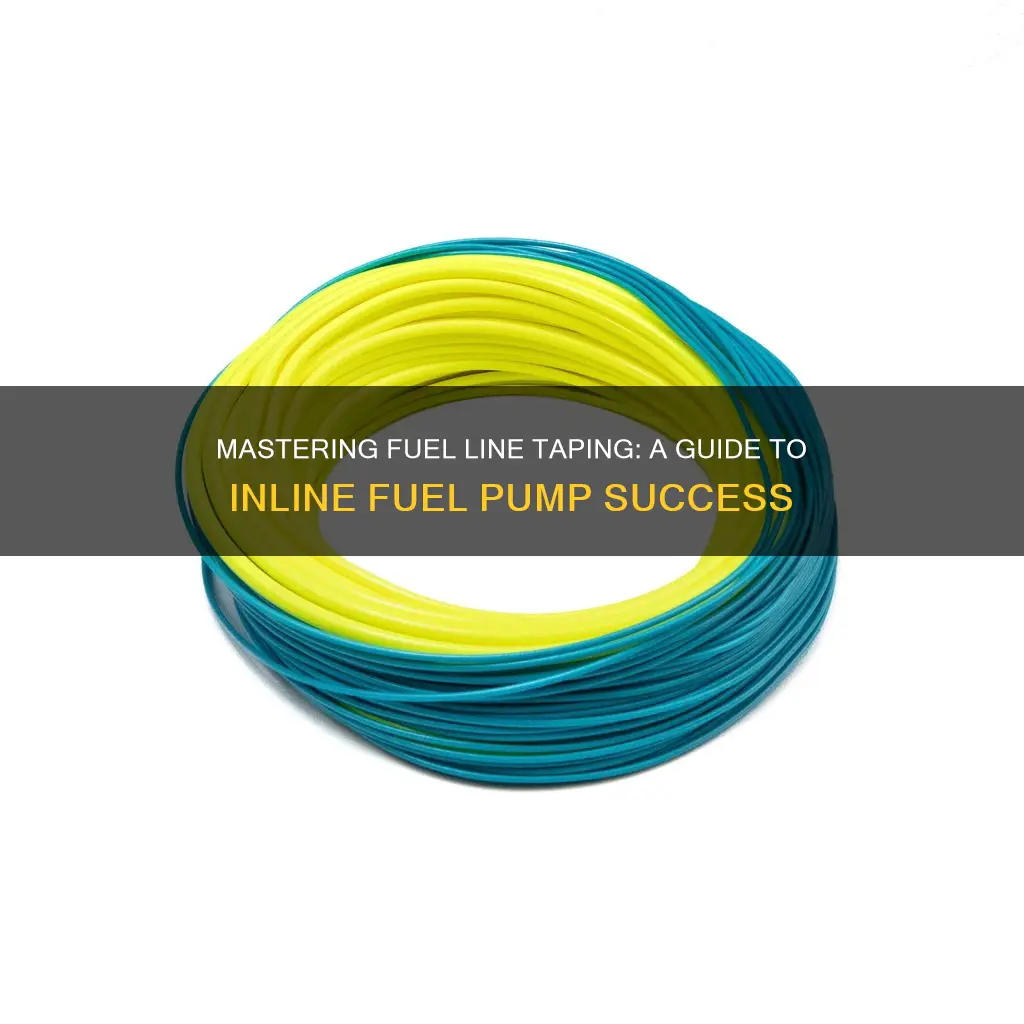
Tapered fuel lines are an essential component for in-line fuel pumps, ensuring efficient and reliable fuel delivery to the engine. This guide will provide a step-by-step process for tapering fuel lines, including the necessary tools and techniques to achieve a precise and secure fit. By following these instructions, you can ensure optimal performance and longevity for your fuel system.
What You'll Learn
- Fuel Line Material: Choose the right material for the fuel line, considering flexibility, durability, and compatibility with fuel
- Line Routing: Route the fuel line away from heat sources and vibrations to prevent damage and ensure proper flow
- Bends and Angles: Maintain smooth, gradual bends and angles to avoid stress points and potential leaks
- Clamps and Fittings: Use appropriate clamps and fittings to secure the fuel line and ensure a tight, leak-free connection
- Testing and Inspection: Test the fuel line for leaks and ensure proper flow rate and pressure before installation
Fuel Line Material: Choose the right material for the fuel line, considering flexibility, durability, and compatibility with fuel
When it comes to choosing the right material for your fuel line, especially when modifying for an in-line fuel pump, several factors come into play. The primary considerations are flexibility, durability, and compatibility with the fuel type. These factors are crucial to ensure the fuel line functions optimally and safely.
Flexibility is essential to accommodate the various movements and vibrations the fuel line will experience during vehicle operation. Rubber is a common choice for fuel lines due to its inherent flexibility. Natural rubber, in particular, offers a good balance of flexibility and strength. However, it's important to note that rubber can degrade over time when exposed to certain fuels, especially those with high ethanol content. For this reason, some enthusiasts opt for synthetic rubber compounds that are more resistant to fuel degradation.
Durability is another critical aspect. Fuel lines must withstand the harsh conditions inside the engine bay, including heat, vibration, and chemical exposure from the fuel. Materials like nylon, stainless steel, and braided steel are often used for their superior durability. Nylon is lightweight and flexible, making it a popular choice for fuel lines. It also has good resistance to fuel degradation. Stainless steel offers excellent resistance to corrosion and heat, ensuring the fuel line can handle the demanding environment of the engine bay. Braided steel provides a flexible yet strong solution, often used in high-performance applications.
Compatibility with the fuel type is perhaps the most overlooked aspect. Different fuels have varying properties that can affect the material of the fuel line. For instance, ethanol-blended fuels can be more corrosive to certain materials. Always check the fuel specifications and consult the manufacturer's guidelines to ensure the chosen material is compatible. Some materials, like certain types of rubber, may not be suitable for fuels with high alcohol content.
In summary, selecting the right material for your fuel line involves a careful consideration of flexibility, durability, and compatibility with the fuel. Natural rubber offers flexibility, while synthetic rubber provides improved resistance to fuel degradation. Nylon, stainless steel, and braided steel are excellent choices for durability. Always ensure the chosen material is compatible with the fuel type to avoid potential issues.
Understanding Flaring: A Fuel Line Emergency
You may want to see also
Line Routing: Route the fuel line away from heat sources and vibrations to prevent damage and ensure proper flow
When installing or modifying an in-line fuel pump system, proper fuel line routing is crucial to ensure optimal performance and longevity. One of the key considerations is to route the fuel line away from heat sources and vibrations to prevent potential damage and maintain a consistent fuel flow.
Heat sources, such as exhaust manifolds, headers, or even the engine block itself, can cause the fuel to degrade over time. This degradation can lead to reduced performance and potential engine issues. To mitigate this, it is essential to keep the fuel line as far as possible from these heat-generating components. A common practice is to route the line along the bottom of the engine bay, where temperatures are generally lower, and it is less likely to come into contact with hot surfaces.
Additionally, vibrations from the engine can also impact the fuel line's performance and durability. Vibrations can cause the line to become loose or even damage the fuel pump itself. To address this, it is recommended to secure the fuel line with appropriate clamps or ties, ensuring it is tightly routed and away from areas prone to engine vibrations. A good practice is to run the line through a rubber or flexible hose to absorb some of the vibrations, providing a buffer between the line and the engine.
When planning the route, consider the fuel line's length and the available space within the engine bay. Longer lines may require additional support or shielding to maintain their shape and prevent kinking. Proper routing should also consider the fuel pump's location, ensuring the line is not too long, which could lead to unnecessary pressure drops and potential flow issues.
By carefully routing the fuel line away from heat sources and vibrations, you can significantly contribute to the overall reliability and efficiency of your in-line fuel pump system. This simple yet crucial step ensures that the fuel flows optimally, delivering the required amount to the engine without compromising performance or longevity.
KTM 640 Fuel Line Size: Ultimate Guide
You may want to see also
Bends and Angles: Maintain smooth, gradual bends and angles to avoid stress points and potential leaks
When working with fuel lines for an in-line fuel pump, ensuring smooth and gradual bends is crucial to prevent stress points and potential leaks. The goal is to create a path that allows the fuel line to follow the natural contours of the engine bay without putting excessive strain on the material. Start by carefully measuring and marking the desired bend radius on the fuel line. This radius should be consistent and gradual, avoiding sharp corners that could lead to stress concentrations. Use a flexible ruler or a similar tool to ensure accuracy.
As you begin bending the fuel line, apply gentle and even pressure to maintain the desired shape. Avoid forcing the line, as this can cause kinks and permanent bends that may restrict fuel flow. Instead, work the line slowly and methodically, ensuring that each bend is smooth and continuous. The key is to create a fluid path that mirrors the engine's natural layout.
Pay close attention to the angles formed during the bending process. Aim for gentle, 90-degree angles whenever possible. Sharp angles can create stress points and increase the risk of fuel line failure. If you encounter a situation where a 90-degree bend is unavoidable, consider using a bend radius that is larger than the standard recommended value to minimize stress.
In areas where the fuel line must navigate around obstacles or follow the engine's contours, maintain a consistent and gradual bend. This approach helps to distribute the load evenly along the length of the line, reducing the likelihood of leaks or damage. Remember, the goal is to create a seamless and stress-free path for the fuel line.
By following these guidelines and paying close attention to bends and angles, you can ensure that the fuel lines are properly tapered and installed, providing a reliable and efficient fuel supply to the in-line fuel pump. This attention to detail will contribute to the overall performance and longevity of the fuel system.
Fuel Line Repair: Revive Your Impala's Performance with These Steps
You may want to see also
Clamps and Fittings: Use appropriate clamps and fittings to secure the fuel line and ensure a tight, leak-free connection
When working with fuel lines for an in-line fuel pump, using the right clamps and fittings is crucial to ensure a secure and leak-free connection. The process of tapering the fuel lines involves creating a precise reduction in diameter to accommodate the pump's requirements, and this must be complemented by an equally careful approach to clamping. Here's a detailed guide on how to achieve this:
Selecting the Right Clamps: Choose clamps that are specifically designed for fuel line applications. These clamps should be made from durable materials such as stainless steel or high-quality alloys to withstand the corrosive nature of fuel. The clamp should have a smooth, non-marring interior to protect the fuel line's outer coating. Look for clamps with a generous inside diameter to ensure a snug fit around the tapered section of the fuel line.
Fitting Selection: Fittings play a vital role in maintaining the integrity of the fuel system. Opt for fittings that are compatible with the fuel line material and the pump's requirements. For example, if you're working with a steel fuel line, consider using brass or stainless steel fittings to ensure compatibility and corrosion resistance. The fittings should be securely tightened to prevent any fuel leakage.
Clamping Technique: When clamping the fuel line, ensure that the clamp is positioned correctly, covering the tapered section. Tighten the clamp by hand first to achieve a good initial grip, then use a wrench to secure it further. The goal is to apply enough force to create a tight seal without causing damage to the fuel line or fittings. Over-tightening can lead to cracking or distortion, so be cautious.
Leak-Free Connection: The key to a successful installation is ensuring that the connection is leak-free. After clamping, inspect the area for any signs of fuel leakage. If you notice any, carefully check the clamp and fitting connections, making sure they are properly tightened. It's essential to double-check these connections, especially at bends or where multiple components are joined.
Testing and Inspection: Once the fuel lines are clamped and fitted, it's crucial to test the system. Start the engine and monitor for any fuel-related issues. Check for unusual noises, vibrations, or signs of fuel leakage. If everything is functioning correctly, you've successfully secured the fuel lines with appropriate clamps and fittings, ensuring a reliable and safe fuel supply to the in-line fuel pump.
Finding the Right Fit: Fuel Line Bolt for Impala 3400 V6
You may want to see also
Testing and Inspection: Test the fuel line for leaks and ensure proper flow rate and pressure before installation
Before installing the tapered fuel lines for your in-line fuel pump, it's crucial to thoroughly test and inspect the lines to ensure they are leak-free and functioning correctly. This process involves a series of checks and measurements to guarantee optimal performance and prevent potential issues.
Start by applying a small amount of fuel-safe sealant or tape at the connections where the fuel lines will be joined. This initial step is essential to identify any potential leaks early on. After sealing, run the fuel line from the pump to the engine and back, ensuring it is securely attached to the pump and the fuel tank. Use a fuel-safe pressure gauge to measure the pressure at the pump and along the line. The pressure should be consistent and within the recommended range for your specific engine and fuel system. If the pressure varies or drops significantly, it indicates a potential issue with the line's integrity or the pump's performance.
Next, perform a visual inspection for any signs of damage or contamination. Look for cracks, punctures, or any foreign matter that might affect the line's functionality. Ensure that the fuel line is free from kinks and has adequate clearance from hot engine components to prevent damage.
To test for leaks, remove the fuel line from the pump and temporarily block the return line to prevent fuel from flowing back. Apply a small amount of fuel to the open end of the line and observe for any leaks. If a leak is detected, carefully inspect the connection points and the line itself for damage or contamination. Ensure that all connections are tight and secure, and consider using a different type of sealant or tape if necessary.
Finally, check the flow rate and pressure at various points along the fuel line. You can use a flow meter to measure the volume of fuel passing through the line per unit of time. Compare the measured flow rate with the expected value for your engine and fuel system. Proper flow rate ensures that your engine receives the required fuel volume for efficient operation. Additionally, verify that the pressure remains consistent and within the specified range throughout the entire length of the fuel line.
By following these testing and inspection procedures, you can ensure that the tapered fuel lines are in optimal condition, ready for installation, and will provide reliable fuel delivery to your engine.
FASS Fuel Line: Unlocking the Power of Your Engine
You may want to see also
Frequently asked questions
Tapered fuel lines are used to ensure a precise and controlled flow of fuel from the tank to the engine. The tapering process involves gradually reducing the diameter of the line, which helps to maintain a consistent pressure and minimizes fuel pulsations, ensuring a steady supply of fuel to the engine.
Before tapering, it's essential to clean and inspect the fuel lines. Remove any debris or old fuel residue using a fuel line cleaner or a mild solvent. Ensure the lines are free from kinks and damage. Measure the length of the line and mark the tapering points accordingly, usually a few inches from the pump and the fuel filter.
You will need a fuel line taper tool, which is a specialized device with a tapered end to shape the fuel line. A set of fuel line connectors and fittings is also necessary to ensure a secure connection. It's recommended to use fuel line tape or adhesive to reinforce the joints and provide insulation.
Tapering fuel lines is a task that requires precision and knowledge of fuel system components. While it is possible to taper the lines yourself using the right tools, it is often recommended to seek professional assistance, especially if you are unsure about the process. A mechanic can ensure the work is done correctly and safely, preventing any potential fuel leaks or engine issues.