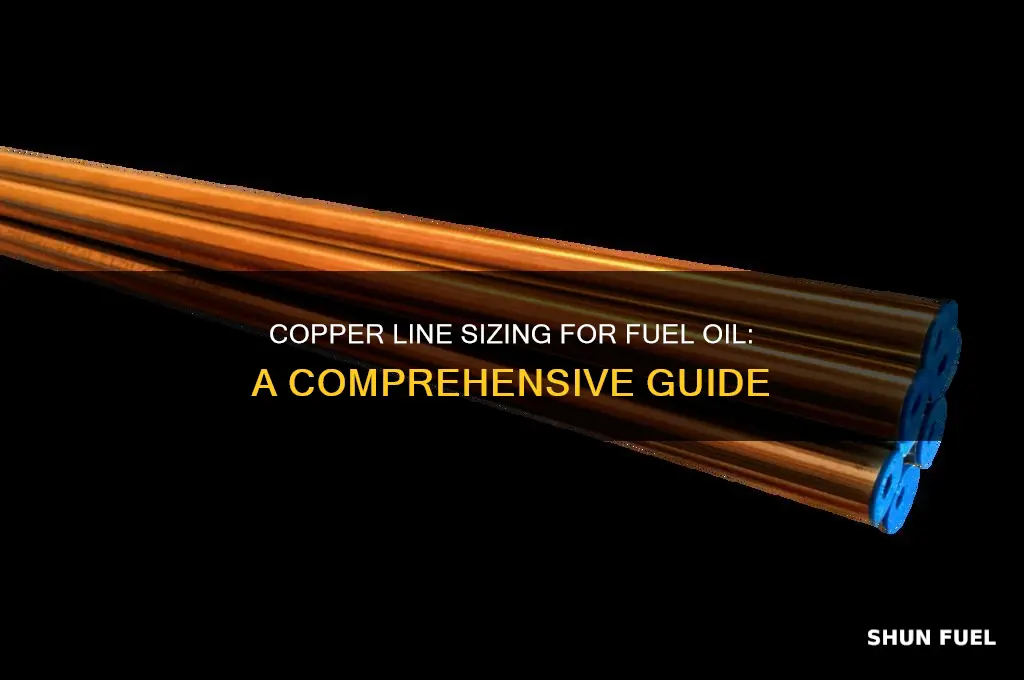
When it comes to fuel oil delivery systems, the size of the copper line used is a critical factor in ensuring efficient and safe operation. The appropriate copper line size depends on various factors, including the length of the line, the flow rate of the fuel oil, and the pressure requirements. In this article, we will explore the considerations and guidelines for selecting the right copper line size to run fuel oil, ensuring optimal performance and reliability in your heating system.
What You'll Learn
- Fuel Oil Line Diameter: Choose diameter based on flow rate and pressure drop
- Copper Line Material: Ensure compatibility with fuel oil and system requirements
- Line Length and Slope: Consider length and slope for optimal performance and safety
- Pressure Drop Calculation: Calculate pressure drop to determine suitable line size
- Local Building Codes: Adhere to local regulations for fuel oil line installation
Fuel Oil Line Diameter: Choose diameter based on flow rate and pressure drop
When it comes to selecting the appropriate diameter for a fuel oil line, two critical factors come into play: flow rate and pressure drop. Understanding these factors is essential to ensure efficient and safe fuel oil distribution.
The flow rate, measured in gallons per minute (GPM) or liters per minute (LPM), represents the volume of fuel oil that needs to be transported through the line per minute. A higher flow rate typically requires a larger diameter pipe to accommodate the increased volume of fuel. For instance, if your fuel oil system needs to supply 100 GPM, you would generally require a larger diameter pipe compared to a system supplying 50 GPM. This is because a larger pipe offers a greater cross-sectional area, allowing more fuel to flow through at any given time without significantly increasing the pressure drop.
Pressure drop is the reduction in pressure that occurs as fuel oil moves through the line. It is influenced by factors such as the length of the pipe, the viscosity of the fuel, and any obstructions or bends in the line. A higher pressure drop can lead to reduced flow efficiency and potential issues with fuel delivery. To minimize pressure drop, it is crucial to choose a pipe diameter that provides an optimal balance between flow rate and resistance. A larger diameter pipe offers less resistance, allowing fuel to flow more easily, while a smaller diameter might increase resistance, leading to higher pressure drop.
To determine the appropriate diameter, consider the specific requirements of your fuel oil system. Start by evaluating the expected flow rate and pressure drop. Consult with fuel oil system experts or refer to manufacturer guidelines for recommended pipe sizes based on these factors. Additionally, consider the material of the pipe. Copper, while not the most common material for fuel oil lines, can be a suitable choice due to its durability and ability to withstand fuel oil temperatures. However, the specific diameter will depend on the unique conditions of your system.
In summary, selecting the right fuel oil line diameter involves a careful consideration of flow rate and pressure drop. A larger diameter pipe generally accommodates higher flow rates and minimizes pressure drop, ensuring efficient fuel oil distribution. By understanding these factors and consulting relevant resources, you can make an informed decision when choosing the diameter for your fuel oil line.
Choosing the Right Fuel Line: Size Matters!
You may want to see also
Copper Line Material: Ensure compatibility with fuel oil and system requirements
When it comes to fuel oil systems, the choice of copper line material is crucial for ensuring optimal performance and longevity. Copper is an excellent choice for fuel oil lines due to its inherent properties and compatibility with the fuel. Firstly, copper is known for its superior corrosion resistance, which is essential when dealing with fuel oil, as it can contain acids and other corrosive substances. This resistance ensures that the copper lines remain intact and do not degrade over time, preventing potential leaks and system failures.
The compatibility of copper with fuel oil is another critical factor. Copper has a low coefficient of expansion, meaning it expands and contracts at a similar rate to the fuel oil, reducing the risk of leaks and cracks. This property is vital, especially in systems where temperature fluctuations are common. Additionally, copper's excellent thermal conductivity helps dissipate heat, which is beneficial in preventing the fuel from becoming too thick or gelling in colder climates.
In terms of system requirements, copper lines offer flexibility and ease of installation. Copper is lightweight and easy to bend, allowing for the creation of custom routes and connections to fit specific system layouts. This flexibility is advantageous when navigating through tight spaces or around obstacles. Moreover, copper's durability ensures that the lines can withstand the rigors of the fuel oil system, including pressure and vibration.
It is essential to choose the appropriate gauge of copper line based on the system's requirements. Thicker gauges provide increased strength and pressure resistance, making them suitable for high-pressure systems or those with longer runs. However, thinner gauges might be preferred for smaller systems or where space is limited. Consulting with a professional or referring to manufacturer guidelines is recommended to determine the right gauge for your specific fuel oil system.
In summary, when selecting copper lines for a fuel oil system, compatibility with the fuel and system requirements should be the primary considerations. Copper's corrosion resistance, low expansion rate, and thermal conductivity make it an ideal choice for fuel oil lines. Its flexibility and durability further enhance its suitability for various system configurations. By carefully choosing the appropriate copper line material and gauge, you can ensure a reliable and efficient fuel oil system.
Tygon Fuel Line: Unlocking the Secrets of High-Performance Fuel Delivery
You may want to see also
Line Length and Slope: Consider length and slope for optimal performance and safety
When it comes to installing a fuel oil system, the size and configuration of the copper lines play a crucial role in ensuring optimal performance and safety. The length and slope of these lines are essential factors to consider, as they directly impact the flow of fuel and the overall efficiency of the system. Here's a detailed guide on why these aspects matter and how to approach them:
Line Length: The length of the copper lines is a critical factor in determining the pressure drop and flow rate of the fuel oil. Longer lines can lead to increased pressure drop, especially if the system has a high elevation change. As a general rule, the longer the line, the more pressure it will lose due to friction and the potential for air pockets. For optimal performance, it is recommended to keep the total length of the fuel oil lines as short as possible. This can be achieved by running the lines in a straight path, avoiding unnecessary turns and bends, and minimizing the number of connections. Properly sizing the lines to handle the required flow rate is essential, as undersized lines can lead to reduced efficiency and potential safety hazards.
Slope and Elevation: The slope of the copper lines is another critical consideration. Fuel oil lines should be designed with a gentle slope to facilitate the flow of the fuel. A slope of 1/4 inch per foot is often recommended as a standard guideline. This means that for every foot of horizontal distance, the line should rise by 1/4 inch. A steeper slope may cause issues with air locking, especially in colder climates, as it can lead to the formation of air bubbles in the lines. Ensuring a consistent and gradual slope throughout the system is vital to prevent air pockets and maintain a steady fuel supply.
To optimize the slope, it is essential to consider the elevation change between the fuel tank and the burner. If there is a significant elevation difference, the lines should be designed with a gradual slope to ensure smooth fuel flow. Proper grading and the use of gravity to assist the flow can help in such cases. Additionally, using a pressure regulator and a fuel pump can help maintain the required pressure and flow rate, especially over longer distances.
Safety Considerations: Proper line length and slope are not just about performance but also about safety. Insufficient line length or improper slope can lead to dangerous situations. For instance, a line that is too short or has an excessive slope might not provide enough pressure to the burner, causing it to malfunction or fail to ignite. On the other hand, a line with a steep slope might cause the fuel to surge, leading to potential safety hazards and system damage. Always ensure that the lines are sized and sloped according to the manufacturer's guidelines and local building codes to maintain a safe and efficient fuel oil system.
In summary, when installing a fuel oil system, paying close attention to line length and slope is essential for both performance and safety. Keeping the lines short and straight, ensuring a gentle slope, and considering elevation changes will contribute to an efficient and reliable fuel supply. It is always advisable to consult with professionals or refer to manufacturer guidelines to ensure the system is installed correctly and meets the required standards.
Unraveling the Mystery: What's the Deal with Fuel Line Sensors?
You may want to see also
Pressure Drop Calculation: Calculate pressure drop to determine suitable line size
When considering the installation of a fuel oil system, understanding the pressure drop calculation is crucial to ensure the right size of copper line is used. This calculation helps determine the pressure loss that occurs as the fuel oil flows through the pipe, allowing you to select an appropriate pipe diameter to maintain optimal system performance. Here's a step-by-step guide to performing this calculation:
- Gather System Information: Begin by collecting data about your fuel oil system. This includes the pump's flow rate (in gallons per minute or liters per minute), the desired pressure at the pump outlet, the system's length, and the type of fuel oil being used. Additionally, note the viscosity of the fuel oil, as this will impact the pressure drop.
- Determine the Friction Factor: The friction factor is a critical component of the calculation. It represents the resistance to flow within the pipe and depends on the pipe's roughness, diameter, and flow conditions. You can find friction factors in engineering tables or use online calculators for various pipe materials and flow regimes.
- Apply the Pressure Drop Formula: Utilize the Darcy-Weisbach equation, a fundamental formula in fluid dynamics, to calculate the pressure drop. The equation is: ΔP = f * L * (v^2) / (2 * g * D), where ΔP is the pressure drop, f is the friction factor, L is the pipe length, v is the fluid velocity, g is the acceleration due to gravity, and D is the pipe diameter. Rearrange this formula to solve for the pipe diameter (D) to find the required line size.
- Consider System Head: In addition to the pressure drop, account for the system head, which is the vertical distance the fuel oil must travel. This is especially important in multi-story buildings or when installing the system above ground level. The system head adds to the overall pressure requirement, influencing the pipe size selection.
- Safety and Code Compliance: Ensure that the calculated pipe size meets or exceeds the safety standards and local building codes. These regulations often provide guidelines for pipe sizing to prevent issues like excessive pressure drops, which can lead to inadequate fuel supply or system inefficiencies.
By following these steps, you can accurately calculate the pressure drop and determine the appropriate copper line size for your fuel oil system. This ensures efficient fuel delivery, optimal system performance, and compliance with safety standards. Remember that proper sizing is essential to avoid issues related to low pressure, excessive noise, or even system failures.
Understanding Feed Fuel Lines: Powering Your Engine's Performance
You may want to see also
Local Building Codes: Adhere to local regulations for fuel oil line installation
When it comes to installing fuel oil lines, adhering to local building codes is of utmost importance to ensure safety and compliance. Each region has its own set of regulations and standards that dictate the installation process, including the size of the copper line required. These codes are in place to protect both the property and its occupants, so it's essential to understand and follow them.
Local building codes often specify the minimum and maximum allowable diameters for fuel oil lines based on factors such as the type of fuel, system pressure, and flow rate. For instance, in some areas, the code might require a minimum of 3/4-inch diameter copper tubing for residential heating systems, while commercial installations may need larger sizes. It is crucial to consult the specific code requirements for your location to ensure you meet the standards.
The installation process must also consider the layout and placement of the fuel oil lines. Building codes often provide guidelines on the minimum distance the lines should be from heat sources, electrical wiring, and other potential hazards. Proper spacing and insulation are essential to prevent fires and ensure the longevity of the system. Additionally, codes may dictate the need for specific fittings, valves, and connectors to maintain safety and efficiency.
Adhering to local regulations is not just about the size of the copper line but also encompasses various aspects of the installation. This includes proper ventilation, the use of approved materials, and the implementation of safety measures such as pressure relief valves and leak detection systems. By following these codes, you can ensure that the fuel oil system is installed correctly, minimizing the risk of accidents and providing efficient heating for your property.
In summary, when dealing with fuel oil line installation, it is imperative to prioritize local building codes. These codes provide the necessary guidelines for proper sizing, installation techniques, and safety measures. By adhering to these regulations, you can create a safe and efficient heating system while also ensuring compliance with legal requirements. Always consult the relevant authorities or professionals to stay informed about the specific codes applicable to your area.
Understanding the Significance of the 3 Lines on Your Fuel Pump
You may want to see also
Frequently asked questions
The size of the copper line for fuel oil delivery depends on various factors, including the volume of oil required, the distance from the tank to the burner, and the specific application. Generally, a 3/4-inch or 1-inch copper line is commonly used for residential heating systems. However, for larger commercial or industrial applications, larger sizes like 1-1/4 inches or even 2 inches might be necessary to handle the higher flow rates.
To determine the right size, consider the oil's flow rate, which is typically measured in gallons per minute (GPM). Consult the specifications of your fuel oil pump and burner to find the recommended flow rate. Then, use a sizing chart or consult with a professional to match the flow rate to the appropriate copper line bore size. Ensure that the line has enough capacity to handle the required volume without causing excessive pressure drops.
It is generally not recommended to use a smaller copper line just to accommodate a potential future upgrade. Fuel oil systems should be designed with the current requirements in mind to ensure optimal performance and safety. Upgrading to a more efficient burner might require additional modifications, but it's best to start with the appropriate line size to handle the current demands. If you anticipate significant changes, it's advisable to consult a professional to ensure your system can handle future upgrades without compromising efficiency or safety.