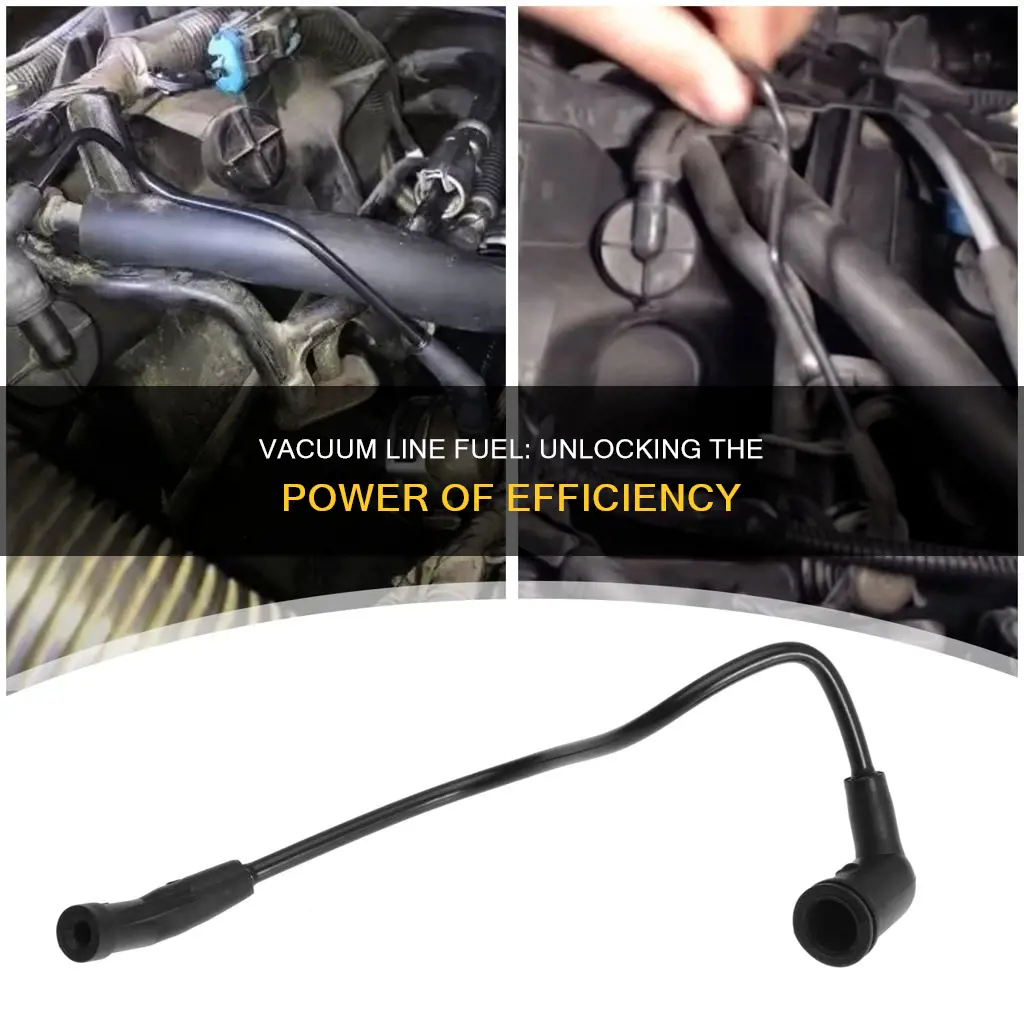
Vacuum line fuel systems have long been a subject of interest in the automotive industry, particularly for their potential to improve fuel efficiency and reduce emissions. This technology involves using a vacuum to draw fuel from the tank to the engine, rather than relying on traditional pumps. The concept is based on the idea that a vacuum can create a more efficient and cleaner fuel delivery process. However, the capabilities and limitations of vacuum line fuel systems have sparked debates among engineers and enthusiasts. This paragraph aims to explore the potential and feasibility of vacuum line fuel systems, examining their advantages, challenges, and the current state of research and development in this area.
What You'll Learn
- Vacuum Line Design: The design of vacuum lines affects fuel flow and pressure
- Fuel Compatibility: Different fuels require specific vacuum line materials and designs
- Performance Impact: Vacuum lines can influence engine performance and fuel efficiency
- Maintenance and Repair: Regular maintenance and repair of vacuum lines are essential
- Safety Considerations: Vacuum lines must be designed and maintained to prevent fuel leaks and explosions
Vacuum Line Design: The design of vacuum lines affects fuel flow and pressure
The design of vacuum lines is a critical aspect of fuel system engineering, especially in high-performance applications where fuel flow and pressure management are essential. Vacuum lines, also known as fuel lines, play a vital role in transporting fuel from the tank to the engine, and their design directly impacts the efficiency and performance of the fuel system. When designing vacuum lines, engineers must consider several factors to ensure optimal fuel flow and pressure regulation.
One key design consideration is the diameter and length of the vacuum lines. The size and shape of the lines determine the resistance to fuel flow, which in turn affects the pressure drop across the system. Generally, a larger diameter vacuum line reduces flow resistance, allowing for smoother and more efficient fuel transport. However, longer lines may introduce additional challenges, such as increased pressure drop due to friction and the potential for fuel vaporization, especially at higher temperatures. Engineers often use calculations and simulations to determine the optimal line dimensions based on the specific fuel requirements and engine specifications.
Another important aspect is the material selection for vacuum lines. Different materials offer varying levels of flexibility, corrosion resistance, and heat tolerance, which can impact fuel flow and pressure stability. For instance, flexible materials like silicone or rubber can accommodate slight movements and vibrations, ensuring a consistent fuel supply. In contrast, rigid materials like steel or aluminum may provide better pressure containment but can be more susceptible to damage from engine components or road vibrations. The choice of material depends on the application's specific needs, balancing factors such as cost, durability, and fuel compatibility.
Additionally, the design should incorporate bends and elbows strategically to minimize turbulence and maintain smooth fuel flow. Sharp bends can create flow restrictions and turbulence, leading to pressure fluctuations and potential fuel atomization issues. By optimizing the line's geometry, engineers can reduce these problems and ensure a consistent fuel-air mixture at the engine's intake.
In summary, the design of vacuum lines is a complex process that requires careful consideration of various factors. Engineers must balance flow resistance, pressure drop, material properties, and geometric constraints to create an efficient and reliable fuel system. Optimizing vacuum line design is crucial for maintaining the performance and longevity of high-performance engines, ensuring that fuel is delivered effectively while managing pressure and flow characteristics.
Flue Liner Sizing Guide: Choosing the Right Fit for Your Multi-Fuel Stove
You may want to see also
Fuel Compatibility: Different fuels require specific vacuum line materials and designs
When it comes to fuel compatibility in vacuum lines, it is crucial to understand the specific requirements of different fuels to ensure optimal performance and safety. Various fuels, such as gasoline, diesel, biofuels, and synthetic fuels, have distinct properties that influence the choice of materials and design considerations for vacuum lines.
Gasoline, a widely used fuel, demands vacuum lines made from materials that can withstand its volatile nature. The lines should be constructed using compatible materials like stainless steel or specialized polymers that resist corrosion and degradation caused by gasoline's aromatic hydrocarbons and oxygenates. These materials ensure the integrity of the vacuum system and prevent fuel leakage or contamination.
Diesel fuel, on the other hand, poses different challenges. Its higher boiling point and sulfur content require vacuum lines with enhanced thermal stability and corrosion resistance. Materials such as 316L stainless steel or specialized alloys are often employed to handle the more aggressive nature of diesel fuel, ensuring the vacuum line's longevity and reliability.
Biofuels, derived from renewable sources, present unique considerations. These fuels may contain varying levels of water and impurities, necessitating vacuum lines with excellent moisture barrier properties. Materials like fluoropolymers or specialized coatings can be used to create a protective barrier, preventing water absorption and potential fuel degradation.
Synthetic fuels, often produced from natural gas, have their own set of requirements. These fuels can be highly corrosive, requiring vacuum lines with advanced corrosion-resistant properties. Materials such as monel or specialized coatings can be utilized to provide the necessary protection against synthetic fuel's corrosive nature.
In summary, fuel compatibility in vacuum lines is a critical aspect of system design. Different fuels demand specific materials and designs to ensure optimal performance and safety. Understanding the unique properties of each fuel type allows engineers to select the appropriate materials, such as stainless steel, specialized polymers, or fluoropolymers, to create vacuum lines that can withstand the challenges posed by various fuels.
Mastering Ford Fuel Line Fitting: A Comprehensive Guide
You may want to see also
Performance Impact: Vacuum lines can influence engine performance and fuel efficiency
The concept of vacuum lines and their impact on engine performance is an intriguing aspect of automotive engineering. When considering the 'Performance Impact: Vacuum lines can influence engine performance and fuel efficiency', it's essential to understand the role of these lines in the fuel system. Vacuum lines, also known as vacuum hoses or intake manifold vacuum lines, are an integral part of the fuel injection system in many modern vehicles. These lines are responsible for carrying the vacuum signal from the engine's intake manifold to the fuel injection system, which then uses this signal to precisely control the fuel-air mixture.
In the context of engine performance, vacuum lines play a critical role in ensuring optimal fuel delivery. The vacuum signal provides information about the engine's intake manifold pressure, which is essential for accurate fuel injection. When the engine is running, the intake manifold creates a partial vacuum, and this vacuum signal is transmitted through the vacuum lines. This signal is then used by the fuel injection system to adjust the fuel spray angle, ensuring that the correct amount of fuel is injected into the combustion chamber. This precise control over fuel delivery directly impacts engine performance, as it allows for efficient combustion and optimal power output.
Moreover, the efficiency of fuel usage is another area where vacuum lines make a significant difference. By accurately measuring the intake manifold pressure, the fuel injection system can optimize the fuel-air mixture, ensuring that the engine operates at its most efficient level. This results in improved fuel economy, as the engine can burn fuel more effectively, reducing waste and improving overall efficiency. In high-performance engines, where precise control over fuel delivery is crucial, vacuum lines become even more critical. They enable the engine to maintain optimal performance, especially during rapid acceleration or high-load conditions, by ensuring that the fuel injection system responds accordingly.
However, it's important to note that the performance impact of vacuum lines can vary depending on several factors. The quality and condition of the vacuum lines themselves are vital. Over time, these lines can become brittle, cracked, or clogged, leading to a loss of vacuum signal. This degradation can result in inaccurate fuel injection, causing the engine to run poorly or even stall. Regular maintenance and inspection of vacuum lines are essential to ensure their longevity and optimal performance. Additionally, the design and layout of the vacuum lines within the engine bay can influence their effectiveness, as proper routing minimizes the risk of damage from heat, vibration, or other mechanical stresses.
In summary, vacuum lines are a crucial component in the fuel injection system, directly impacting engine performance and fuel efficiency. Their ability to transmit the vacuum signal accurately ensures precise fuel delivery, enabling efficient combustion and optimal power output. Understanding the role of vacuum lines and their potential performance impact is essential for maintaining and optimizing engine performance, especially in modern vehicles with sophisticated fuel injection systems. Regular maintenance and attention to the condition of these lines are key to ensuring the engine operates at its best.
Troubleshooting: When Your Fuel Line's Performance is Compromised
You may want to see also
Maintenance and Repair: Regular maintenance and repair of vacuum lines are essential
Vacuum lines are a critical component in the fuel system of many vehicles, and their maintenance and repair are often overlooked but crucial for optimal performance and safety. These lines are responsible for transporting fuel from the tank to the engine, and any issues can lead to reduced power, poor fuel efficiency, and even engine failure. Regular maintenance and timely repairs are essential to ensure the vacuum lines function correctly and prevent potential problems.
Over time, vacuum lines can become susceptible to various issues. One common problem is the development of cracks or leaks, which can occur due to the constant expansion and contraction of the fuel vapor within the lines. These cracks may go unnoticed until they cause a significant loss of pressure, resulting in reduced engine performance. Additionally, the lines can become clogged with debris, such as dirt, rust, or varnish, which can restrict fuel flow and lead to engine misfires or stalling.
To maintain and repair vacuum lines effectively, it is recommended to follow a structured approach. Firstly, regular inspections should be conducted to identify any visible signs of damage, corrosion, or blockages. This can be done by visually examining the lines for cracks, bends, or any foreign objects that might have entered the system. It is also beneficial to check for any signs of fuel leakage, as this could indicate a more serious issue.
When performing repairs, it is crucial to use the right tools and materials. Replacing damaged sections of the vacuum line with new, compatible parts is essential to ensure a proper fit and seal. It is recommended to use high-quality fuel line connectors and seals to prevent future leaks. During the repair process, it is important to follow the manufacturer's guidelines and specifications to avoid any potential complications.
Furthermore, regular maintenance can help prevent issues before they become major problems. This includes checking and replacing the fuel filter regularly to keep the entire fuel system clean. Maintaining a clean and well-maintained engine bay can also reduce the risk of contamination and potential damage to the vacuum lines. By implementing a proactive maintenance routine, vehicle owners can ensure the longevity and reliability of their fuel system.
Understanding Fuel Line Sizes: Gas Tank Capacity Explained
You may want to see also
Safety Considerations: Vacuum lines must be designed and maintained to prevent fuel leaks and explosions
Vacuum lines, an essential component in fuel systems, play a critical role in ensuring the safe and efficient delivery of fuel to an engine. When considering the capability of vacuum lines to handle fuel, it is crucial to prioritize safety as the primary concern. The design and maintenance of these lines are vital to prevent potential hazards such as fuel leaks and explosions, which can have severe consequences.
One of the key safety considerations is the material selection for vacuum lines. These lines should be constructed using materials that are compatible with the fuel being transported. For instance, if the fuel contains corrosive substances, the vacuum lines must be made of materials that can withstand such corrosive effects to prevent degradation and potential failures. Common materials used include stainless steel, aluminum alloys, and specialized polymers designed for fuel transport, ensuring durability and resistance to fuel-related chemicals.
Designing the vacuum lines with appropriate dimensions and wall thickness is another critical aspect. The lines should be designed to handle the expected fuel flow rates and pressures without compromising integrity. Engineers must consider factors such as line diameter, length, and bends to ensure optimal performance and safety. Proper design minimizes the risk of fuel accumulation, which could lead to dangerous situations if not properly managed.
Maintenance is a continuous process that cannot be overlooked. Regular inspections are necessary to identify any signs of wear, corrosion, or damage. Over time, vacuum lines may experience degradation due to fuel exposure, temperature fluctuations, or mechanical stress. Inspecting the lines for cracks, pitting, or any signs of fuel infiltration is essential. Maintenance routines should include pressure testing, leak detection, and replacement of compromised lines to ensure the system's reliability and safety.
Furthermore, proper installation and secure fastening of vacuum lines are vital. Leaks can occur if connections are not tightened correctly, leading to fuel escaping into the engine compartment, which is highly flammable. Regular checks and adjustments during maintenance ensure that all connections remain tight and secure, minimizing the risk of fuel leaks and potential fires.
In summary, the design and maintenance of vacuum lines are critical safety measures in fuel systems. By selecting appropriate materials, considering design specifications, and implementing rigorous maintenance practices, the risk of fuel leaks and explosions can be significantly reduced. Adhering to these safety considerations is essential to ensure the efficient and secure operation of fuel-handling systems.
Maximizing Performance: Understanding the Benefits of Double Lines on Dual Action Fuel Pumps
You may want to see also
Frequently asked questions
Vacuum line fuel, also known as vaporized fuel or fuel vapor, is a mixture of gasoline and air that has been compressed and heated to create a vapor state. This process is typically done in the fuel injectors of modern vehicles to ensure precise fuel delivery to the engine.
Vacuum line fuel is in a gaseous state, while liquid fuel is in a liquid form. The vaporization process in the fuel injectors turns the liquid fuel into a fine mist, which then mixes with air and is injected into the engine's cylinders. This allows for more efficient combustion and better engine performance.
Yes, vacuum line fuel is commonly used in gasoline-powered engines, including those found in cars, trucks, and motorcycles. It is designed to work with the fuel injection systems used in modern vehicles, providing precise control over fuel delivery and combustion.
While vacuum line fuel is primarily used in newer engine designs with fuel injection, some older engines may also utilize this system. However, it's important to note that older engines might require modifications or the use of specialized equipment to handle the vaporized fuel effectively.
Vacuum line fuel offers several advantages, including improved engine performance, better fuel efficiency, and reduced emissions. The precise control over fuel delivery allows for optimal combustion, resulting in a more powerful and environmentally friendly engine.