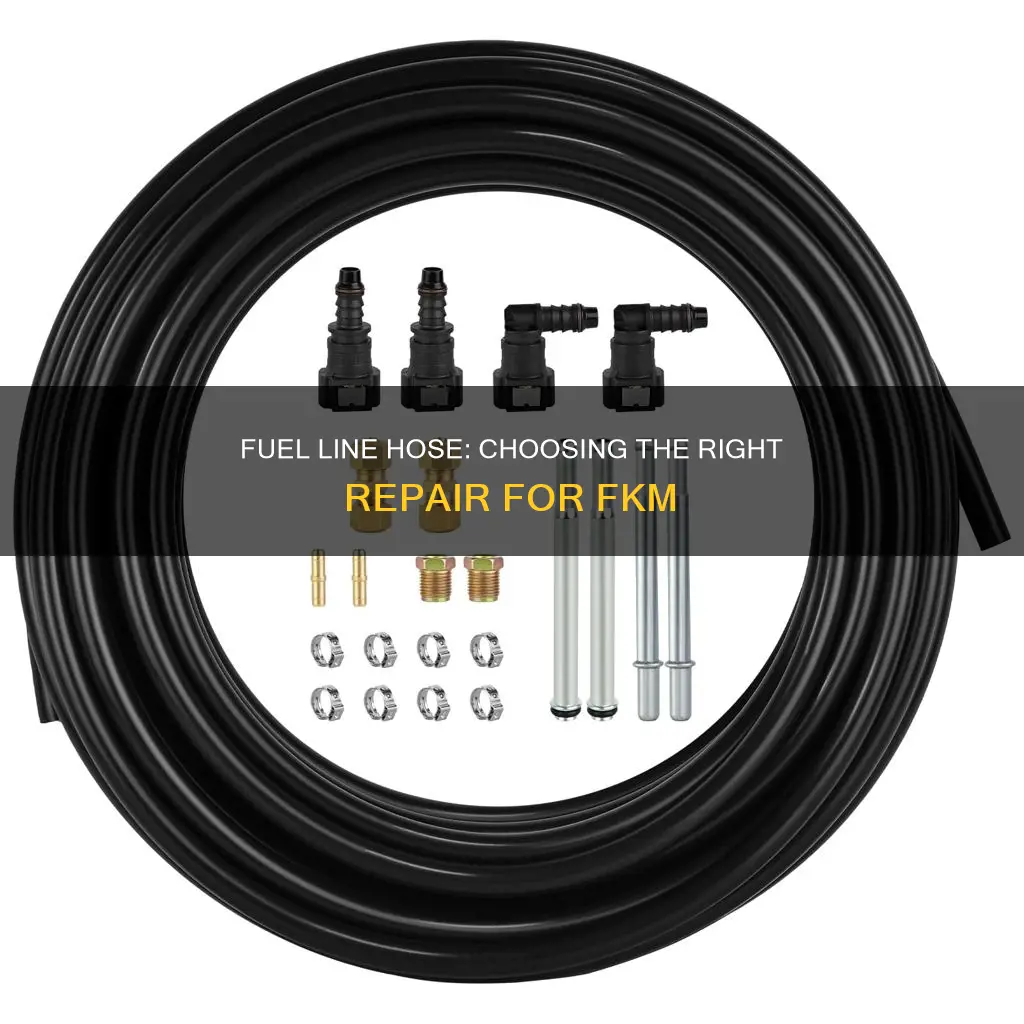
When it comes to repairing a fuel line, choosing the right hose is crucial for a successful and safe fix. The type of hose you select depends on the specific requirements of your vehicle's fuel system. For instance, if you're dealing with a fuel line repair using FKM (Fluororubber), a material known for its excellent resistance to fuel and temperature variations, you'll need a hose that can withstand these conditions. This introduction sets the stage for discussing the various hose options available and their suitability for different fuel line repair scenarios.
What You'll Learn
- Hose Material: Choose from rubber, vinyl, or synthetic options for durability
- Hose Diameter: Select the appropriate size based on fuel flow rate
- Temperature Range: Ensure the hose can withstand engine temperatures
- Flexibility: Opt for a flexible hose for easy installation and movement
- Compatibility: Verify hose compatibility with fuel type and vehicle model
Hose Material: Choose from rubber, vinyl, or synthetic options for durability
When it comes to choosing the right hose material for a fuel line repair, you have several options to ensure durability and reliability. The material you select will depend on various factors, including the specific application, environmental conditions, and the type of fuel being used. Here's an overview of the common hose materials and their advantages:
Rubber Hose: Rubber hoses have been traditionally used for fuel lines due to their flexibility and resilience. Natural rubber hoses are known for their ability to withstand fuel's corrosive nature over time. They offer excellent resistance to abrasion, making them suitable for applications where the hose might come into contact with rough surfaces. Additionally, rubber hoses can handle moderate temperatures, which is crucial for fuel lines that may experience varying climate conditions. However, one drawback is that rubber hoses can become brittle over time, especially in the presence of certain fuels, so it's essential to choose a high-quality, fuel-resistant rubber material.
Vinyl Hose: Vinyl hoses are a more cost-effective option and offer good flexibility. They are less resistant to abrasion compared to rubber but can still provide adequate performance for fuel line applications. Vinyl hoses are generally suitable for low-pressure fuel systems and are less prone to cracking. This material is often used in temporary or non-critical fuel line repairs. It's important to note that vinyl hoses may not be as durable as rubber hoses, especially in harsh environments, so they might not be the best choice for long-term fuel line solutions.
Synthetic Hose: Synthetic hoses, such as those made from polyurethane or fluoropolymers, offer superior durability and resistance to fuel degradation. These hoses are highly flexible and can withstand extreme temperatures, making them ideal for fuel line repairs in various automotive and industrial settings. Synthetic hoses often provide excellent chemical resistance, ensuring they can handle different fuel types without deterioration. While they might be more expensive, the increased longevity and performance make them a reliable choice for critical fuel line applications.
In summary, the choice of hose material depends on the specific requirements of your fuel line repair. Rubber hoses offer flexibility and moderate temperature resistance, vinyl hoses provide cost-effectiveness, and synthetic hoses excel in durability and temperature tolerance. Consider the fuel type, environmental factors, and the overall lifespan needed for your application to make an informed decision.
Understanding CPE Fuel Line: A Comprehensive Guide
You may want to see also
Hose Diameter: Select the appropriate size based on fuel flow rate
When it comes to repairing a fuel line, selecting the right hose diameter is crucial for ensuring optimal performance and safety. The hose diameter directly impacts the fuel flow rate, which is a critical factor in maintaining the engine's efficiency and preventing potential issues. Here's a detailed guide on how to choose the appropriate hose diameter for your fuel line repair:
Understanding Fuel Flow Rate: The fuel flow rate refers to the volume of fuel that passes through the fuel line per unit of time. It is typically measured in liters per minute (L/min) or gallons per minute (GPM). The flow rate is influenced by various factors, including the engine's power output, fuel pressure, and the overall design of the fuel system. It's essential to determine the required fuel flow rate for your specific application to select the correct hose diameter.
Factors Affecting Hose Diameter Selection: The diameter of the hose should be chosen based on the expected fuel flow rate to ensure efficient and reliable fuel delivery. Here are some key considerations:
- Engine Requirements: Consult the vehicle's manual or manufacturer specifications to identify the recommended fuel flow rate for your engine. Different engines may have varying fuel requirements, and using the correct diameter hose is essential to meet these needs.
- Fuel Pressure: Higher fuel pressure can impact the required hose diameter. If your fuel system operates at elevated pressure, you might need a larger hose to accommodate the increased flow without compromising performance.
- Hose Material and Flexibility: Consider the material and flexibility of the hose. Some materials may offer better flow characteristics than others. For instance, hoses with a higher flexibility rating can handle more significant bends and twists, which is beneficial for fuel lines with complex routes.
Calculating Hose Diameter: To select the appropriate hose diameter, you can use the following formula:
Flow Rate (L/min) = (Fuel Pressure (bar) x Cross-Sectional Area) / (Density of Fuel (kg/L) x Gravity (m/s²))
Once you have the flow rate, you can refer to hose sizing charts or tables, which provide a range of diameters for different flow rates. These charts typically offer standard hose sizes, such as 3/8", 1/2", or 3/4" ID (inside diameter) for fuel lines. Choose the diameter that closely matches or slightly exceeds your calculated flow rate to ensure optimal performance.
Remember, using a hose with an inappropriate diameter can lead to fuel restrictions, reduced engine power, or even fuel pump damage. Always refer to the manufacturer's guidelines and consult experts if needed to make an informed decision when selecting the hose diameter for your fuel line repair.
Fuel Line Clog Symptoms: Engine Issues Revealed
You may want to see also
Temperature Range: Ensure the hose can withstand engine temperatures
When it comes to fuel line repair, one of the critical factors to consider is the temperature range that the hose will need to withstand. Engine temperatures can vary significantly, and using the wrong hose can lead to performance issues, leaks, or even safety hazards. Here's a detailed guide on how to ensure the hose can handle the heat:
Understanding Engine Temperatures: Engines generate a considerable amount of heat, especially during operation. The temperature inside an engine bay can reach extremely high levels, often exceeding 200°C (400°F). These temperatures are not only hot but also fluctuate rapidly, especially during acceleration or when the engine is under load. It's essential to consider both the maximum and minimum temperatures the hose will encounter.
Material Selection: The choice of hose material is crucial for withstanding engine temperatures. Rubber hoses, for example, have a limited temperature range and can become brittle or melt at high temperatures. For fuel line repairs, it's recommended to use hoses made from materials like silicone or fluoropolymer. Silicone hoses offer excellent heat resistance, maintaining their flexibility and structural integrity over a wide temperature range, typically from -60°C to 250°C (-76°F to 482°F). Fluoropolymer hoses, such as those made from PTFE (polytetrafluoroethylene), can handle even higher temperatures, making them suitable for extreme engine conditions.
Flexibility and Durability: In addition to temperature resistance, the hose should be flexible enough to navigate the engine bay's contours and withstand the vibrations and movements associated with engine operation. Look for hoses with a braided or reinforced construction to ensure they can handle the mechanical stress without compromising their temperature-resistant properties.
Testing and Certification: To ensure the hose meets the required temperature standards, it should be tested rigorously. Manufacturers often provide temperature ratings based on standardized tests, such as those conducted by the Society of Automotive Engineers (SAE). Look for hoses that are certified to meet or exceed the temperature requirements of your specific engine and application.
Installation and Maintenance: Proper installation is vital to ensure the hose's performance. Follow the manufacturer's guidelines for routing, securing, and connecting the hose. Regular maintenance, including checking for cracks, brittleness, or signs of degradation, will also help ensure the hose's longevity and performance over time.
Unveiling the Mystery: Small Lines Behind Fuel Filter in Cadillac SRX
You may want to see also
Flexibility: Opt for a flexible hose for easy installation and movement
When it comes to repairing a fuel line, one of the most important considerations is flexibility. Opting for a flexible hose is a wise choice for several reasons, and it can significantly impact the ease and success of your repair. This type of hose is designed to bend and move, which is crucial when dealing with the intricate network of fuel lines in a vehicle.
The primary advantage of using a flexible hose is the ease of installation. Fuel lines can be routed through tight spaces and challenging angles, especially in older vehicles or those with compact engine compartments. A flexible hose allows you to navigate these obstacles effortlessly. You can easily maneuver the hose into place, ensuring a proper fit and secure connection without causing damage to the surrounding components. This flexibility also reduces the risk of kinking or bending the hose beyond its limits, which could lead to premature failure.
Furthermore, the flexibility of the hose is beneficial during the repair process. When working on a fuel line, you may need to adjust the hose's position to access different areas of the engine or to align it with other components. A flexible hose accommodates these movements, making the repair job more manageable and efficient. This is particularly useful when dealing with complex fuel system layouts, where multiple lines and components are closely spaced.
In addition to installation and repair, flexibility also plays a role in long-term maintenance. Over time, fuel lines can experience movement due to engine vibrations or changes in temperature. A flexible hose can better withstand these movements, reducing the likelihood of cracks, leaks, or damage. This ensures that your fuel line repair remains reliable and durable, providing peace of mind during your vehicle's operation.
When choosing a flexible hose for fuel line repair, consider the material and construction. Look for hoses made from high-quality rubber or synthetic materials that offer excellent flexibility without compromising strength. Ensure the hose has a suitable inner diameter to handle the fuel flow required by your vehicle. Properly selecting the hose will ensure a successful and long-lasting repair.
Essential Components: Building a Robust Fuel Line System
You may want to see also
Compatibility: Verify hose compatibility with fuel type and vehicle model
When it comes to fuel line repairs, ensuring compatibility is crucial to prevent potential issues and ensure optimal performance. The first step in choosing the right hose for your fuel line repair is to identify the specific fuel type and vehicle model you are working with. Different fuels, such as gasoline, diesel, or aviation fuel, have varying properties and require hoses with specific characteristics to handle their unique challenges. For instance, gasoline hoses need to be resistant to fuel evaporation and degradation, while diesel hoses should withstand higher pressure and temperature.
Researching the vehicle's fuel system and understanding the specifications is essential. Each vehicle model has its own set of requirements, and using the correct hose ensures a proper fit and prevents potential leaks. You can often find this information in the vehicle's manual or by consulting the manufacturer's guidelines. It is important to note that using an incompatible hose can lead to fuel leaks, engine performance issues, and even safety hazards.
For example, if you are working on a gasoline-powered vehicle, you should look for hoses specifically designed for gasoline applications. These hoses typically have a rubber or synthetic material that can withstand the corrosive nature of gasoline over time. Similarly, diesel vehicles require hoses with a more robust construction to handle the higher pressure and temperature of diesel fuel.
Additionally, consider the vehicle's model and year, as older models might have different hose requirements. Modern vehicles often incorporate advanced fuel systems, and using the correct hose ensures compatibility with these systems. It is always a good practice to consult the vehicle's service manual or seek advice from automotive experts to confirm the specific hose requirements for your make and model.
In summary, compatibility is key when selecting a hose for fuel line repairs. By verifying the hose's compatibility with the fuel type and vehicle model, you can ensure a successful repair, maintain engine performance, and avoid potential risks associated with improper hose selection. Taking the time to research and choose the right hose will contribute to a reliable and safe fuel system.
Sugar's Sweet Secret: Uncovering Its Impact on Fuel Lines
You may want to see also
Frequently asked questions
For fuel line repairs using FKM, a suitable hose would be a high-temperature, fuel-resistant hose made from this material. FKM hoses are known for their excellent resistance to fuels, oils, and chemicals, making them ideal for automotive applications.
The hose size should match the diameter of the original fuel line to ensure a proper fit. Measure the old line or consult the vehicle's manual for the correct specifications. FKM hoses are available in various diameters to accommodate different repair needs.
Yes, FKM hoses are designed to handle a wide range of fuels, including gasoline, diesel, and aviation fuels. They provide excellent chemical resistance, ensuring compatibility with various fuel types commonly used in vehicles.
FKM hoses offer several benefits, such as superior temperature resistance, flexibility, and durability. They can withstand extreme temperatures, making them suitable for both hot and cold environments. Additionally, FKM's resistance to fuel degradation ensures a longer-lasting repair.
Absolutely! FKM hoses are versatile and can be used for both temporary fixes and long-term solutions. For temporary repairs, you can use a hose with a suitable clamp, while for permanent installations, you can solder or weld the hose to the fuel line, ensuring a secure and reliable connection.