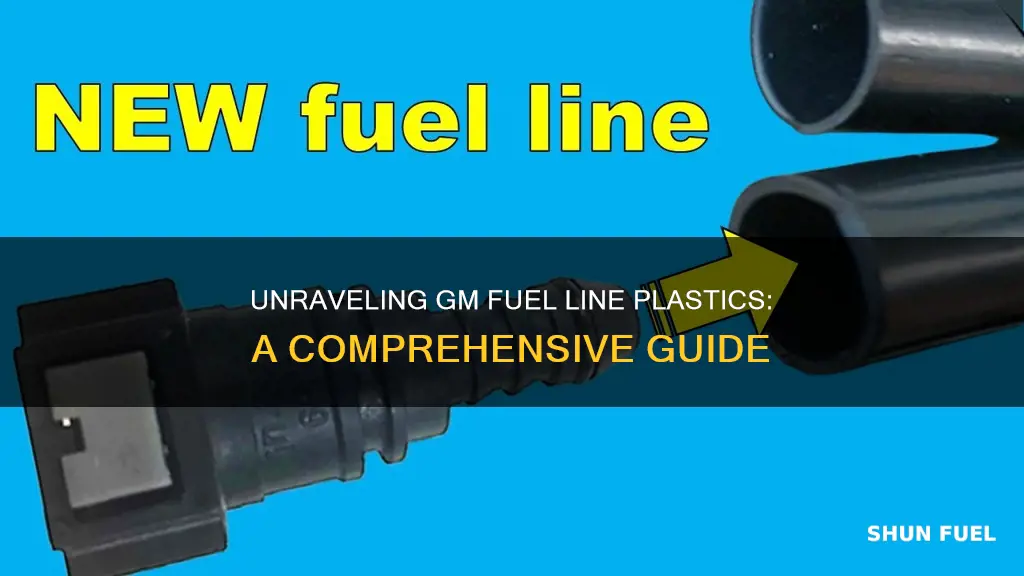
What kind of plastic are GM fuel lines made of? This question is crucial for understanding the durability and compatibility of these components in automotive applications. GM fuel lines are typically constructed from a specific type of plastic, often a high-density polyethylene (HDPE) or a polypropylene (PP) material. These plastics are chosen for their ability to withstand the corrosive effects of fuel, such as gasoline, diesel, and ethanol, while also maintaining flexibility and durability over a wide temperature range. The choice of plastic is essential to ensure the fuel lines remain intact and functional, preventing leaks and potential engine damage. Understanding the specific plastic used can help in selecting appropriate replacement parts and maintaining the vehicle's performance and safety.
What You'll Learn
- Material Composition: GM fuel lines often use polyvinyl chloride (PVC) or ethylene-propylene rubber (EPR) for durability
- Temperature Resistance: These plastics can withstand temperatures ranging from -40°F to 250°F, ensuring fuel line integrity
- Flexibility: The plastic material is flexible to accommodate engine vibrations and movement without cracking or breaking
- Chemical Resistance: GM fuel lines are designed to resist fuel-related chemicals, preventing degradation and leaks
- Installation Guidelines: Proper installation techniques are crucial to ensure a secure and leak-free connection
Material Composition: GM fuel lines often use polyvinyl chloride (PVC) or ethylene-propylene rubber (EPR) for durability
The composition of materials used in GM fuel lines is a critical aspect of their design and performance. One of the primary materials utilized in these fuel lines is polyvinyl chloride (PVC). PVC is a versatile and durable plastic known for its excellent resistance to chemicals, oils, and fuels, making it an ideal choice for automotive applications. Its ability to withstand the harsh conditions of fuel transport and storage ensures the longevity of the fuel system.
In addition to PVC, ethylene-propylene rubber (EPR) is another material commonly employed in GM fuel lines. EPR is a synthetic rubber compound that offers superior flexibility and resilience. This material is particularly useful in fuel lines as it can accommodate temperature variations and provide a reliable seal, preventing fuel leaks. The combination of PVC and EPR in GM fuel lines ensures a robust and reliable system, capable of withstanding the demands of everyday use.
The choice of these specific plastics is strategic, as they possess unique properties that contribute to the overall performance and safety of the vehicle's fuel system. PVC's chemical resistance and EPR's flexibility are key factors in maintaining the integrity of the fuel lines, especially in the presence of various fuel types and environmental conditions. This careful selection of materials highlights GM's commitment to engineering reliable and durable automotive components.
Furthermore, the use of these plastics in fuel lines is a testament to their effectiveness in preventing fuel degradation and maintaining the quality of the fuel delivered to the engine. The materials' ability to resist fuel-related chemicals and maintain their structural integrity over time is crucial for optimal engine performance and longevity.
In summary, GM fuel lines are engineered with a focus on durability and reliability, utilizing PVC and EPR plastics to ensure the system's longevity and performance. These materials' properties make them well-suited for the demanding environment of a vehicle's fuel system, providing a safe and efficient fuel delivery solution.
Honda XR50 Fuel Line: Size and Compatibility Guide
You may want to see also
Temperature Resistance: These plastics can withstand temperatures ranging from -40°F to 250°F, ensuring fuel line integrity
The choice of plastic material for GM fuel lines is a critical aspect of vehicle engineering, ensuring optimal performance and longevity. When it comes to temperature resistance, these fuel lines are designed with specific plastics that can endure a wide range of environmental conditions. The temperature tolerance of these plastics is an essential feature, allowing them to withstand extreme variations without compromising their structural integrity.
The temperature resistance of GM fuel lines is an impressive feat of material science. These plastics are engineered to maintain their flexibility and resilience across a broad temperature spectrum. From as low as -40°F, where many materials would become brittle, these plastics remain pliable and functional. This low-temperature resistance is crucial for vehicles operating in cold climates or during winter months, ensuring that the fuel lines remain operational even in freezing conditions.
As temperatures rise, the plastics used in GM fuel lines continue to excel. They can withstand up to 250°F, a temperature that many other materials would struggle to manage. This high-temperature resistance is vital for vehicles used in high-performance applications or those operating in hot environments, such as racing cars or vehicles in desert regions. By maintaining their structural integrity under extreme heat, these plastics ensure that the fuel lines remain secure and efficient.
The temperature range of -40°F to 250°F is a challenging environment for any material, and the plastics used in GM fuel lines rise to the occasion. This temperature resistance is a key factor in the overall reliability and safety of the vehicle's fuel system. By withstanding such extreme conditions, these plastics contribute to the vehicle's performance, fuel efficiency, and long-term durability.
In summary, the plastics used in GM fuel lines are specifically chosen for their ability to endure a wide range of temperatures, from the harsh cold of winter to the intense heat of summer. This temperature resistance is a testament to the advanced engineering and material science that goes into modern vehicle components, ensuring that GM vehicles can operate reliably and safely in various environments.
Choosing the Right Hose for Your 1.4-Inch Fuel Line
You may want to see also
Flexibility: The plastic material is flexible to accommodate engine vibrations and movement without cracking or breaking
The use of flexible plastic materials in GM fuel lines is a critical design choice, ensuring the system's longevity and reliability in the harsh engine environment. This flexibility is essential to accommodate the various vibrations and movements that occur within an engine's operation.
Engine vibrations can be intense and rapid, causing stress on any rigid material. The plastic used in GM fuel lines is engineered to withstand these vibrations without compromising its structural integrity. This flexibility is achieved through the material's ability to deform and return to its original shape, a property known as elasticity. By allowing for this deformation, the plastic can absorb the energy from vibrations, preventing it from transferring to the fuel line itself.
Furthermore, the engine's movement, especially during acceleration and deceleration, can cause the fuel lines to flex and bend. The plastic material is chosen for its ability to maintain flexibility even under these conditions, ensuring that the fuel lines do not become rigid and brittle. This flexibility is crucial to prevent cracking or breaking, which could lead to fuel leaks and potential engine damage.
The specific type of plastic used in GM fuel lines is carefully selected to balance flexibility with durability. It must be able to withstand the chemical properties of the fuel it carries, as well as the extreme temperatures and pressures found in the engine bay. Materials like polyether ether ketone (PEEK) or polyphenylene sulfide (PPS) are often considered due to their excellent flexibility and resistance to heat and chemicals.
In summary, the flexibility of the plastic material in GM fuel lines is a key feature that enables the system to endure the demanding conditions of an engine's operation. This flexibility ensures that the fuel lines remain intact and functional, contributing to the overall reliability and performance of the vehicle.
E85 Fuel Line: Choosing the Right Option for Your Engine
You may want to see also
Chemical Resistance: GM fuel lines are designed to resist fuel-related chemicals, preventing degradation and leaks
The chemical resistance of GM fuel lines is a critical aspect of their design, ensuring the longevity and reliability of fuel systems in vehicles. These fuel lines are specifically engineered to withstand the harsh conditions of fuel-related chemicals, which can cause degradation and potential leaks over time. The primary goal is to maintain the integrity of the fuel system, preventing any contamination or damage that could lead to performance issues.
GM fuel lines are typically constructed using high-quality plastics that have been carefully selected for their ability to resist various chemicals present in gasoline, diesel, and other fuels. The choice of plastic material is crucial, as it directly impacts the fuel line's durability and performance. Common materials used include polyetheretherketone (PEEK), polyphenylene sulfide (PPS), and certain types of polyolefin blends. These plastics offer excellent resistance to fuel-related chemicals, such as hydrocarbons, alcohols, and aromatic compounds, ensuring that the fuel lines remain stable and functional.
The manufacturing process involves precise engineering to create a seamless and robust structure. The plastic material is carefully processed to form a flexible yet sturdy fuel line that can withstand the constant movement and vibrations within a vehicle's engine compartment. This flexibility is essential to accommodate the various angles and bends in the fuel line routing, ensuring a proper fit without compromising chemical resistance.
In addition to the choice of plastic, the design of GM fuel lines incorporates features that enhance their chemical resistance. These may include specialized coatings or additives that further protect the plastic from fuel-related degradation. For instance, some fuel lines might have a protective layer applied to the inner surface, creating a barrier between the fuel and the plastic material. This additional layer can significantly improve the fuel line's ability to resist chemical attacks and maintain its structural integrity.
By utilizing these advanced materials and design considerations, GM ensures that their fuel lines can withstand the challenges posed by different fuel types and environmental conditions. This chemical resistance is vital for the overall performance and safety of the vehicle, as it directly contributes to preventing fuel leaks, maintaining engine efficiency, and reducing the risk of potential hazards associated with fuel system failures.
Unleash Engine Power: Understanding Fuel Line Cleaner's Magic
You may want to see also
Installation Guidelines: Proper installation techniques are crucial to ensure a secure and leak-free connection
When it comes to installing GM fuel lines, understanding the specific type of plastic used is essential for a successful and secure connection. The fuel lines in General Motors (GM) vehicles are typically made from a particular type of plastic known as High-Density Polyethylene (HDPE). This material is chosen for its excellent chemical resistance, durability, and ability to withstand the harsh conditions of an engine compartment.
Proper installation techniques are crucial to ensure a secure and leak-free connection. Here are some detailed guidelines to follow:
- Preparation: Before beginning the installation, ensure you have the necessary tools and materials, including the HDPE fuel line, fittings, and any required seals or gaskets. Clean the areas where the fuel line will be connected to remove any dirt or debris that could interfere with the installation process.
- Cutting the Fuel Line: Measure and mark the desired length of the fuel line. Use a sharp, clean knife or a dedicated fuel line cutter to make a precise cut. Avoid cutting too close to any existing fittings or connections to prevent damage. Smooth any sharp edges with a file or sandpaper to prevent nicks and cuts during installation.
- Fitting Connections: GM fuel lines often use quick-connect fittings for ease of installation. Ensure you have the correct type of fitting for your specific fuel line diameter. Slide the fitting onto the fuel line, ensuring it is the right size and securely in place. Tighten the fitting using the appropriate tool, being careful not to overtighten, as this can damage the fuel line.
- Sealing and Support: Proper sealing is critical to prevent leaks. Use the provided seals or gaskets and insert them into the fittings before connecting the lines. Ensure a tight fit by applying firm pressure when attaching the fittings. Additionally, consider using fuel line clips or brackets to support the new line, especially in areas with limited space or high vibration.
- Final Checks: After completing the installation, inspect all connections for tightness and proper alignment. Check for any signs of damage or leaks by running the fuel system under pressure. If any issues are found, carefully inspect the connections and make the necessary adjustments or replacements.
By following these installation guidelines, you can ensure that your GM fuel lines are properly connected, secure, and leak-free, contributing to the overall reliability and performance of your vehicle's fuel system. Remember, taking the time to install components correctly can save you from potential issues and costly repairs in the future.
Understanding SAE 307R7 Fuel Line: A Comprehensive Guide
You may want to see also
Frequently asked questions
GM fuel lines are typically made from a specific type of plastic known as High-Density Polyethylene (HDPE). This material is chosen for its durability, flexibility, and resistance to fuel degradation, making it suitable for automotive applications.
No, while HDPE is a common choice, other plastics like Polyethylene Terephthalate (PET) or Polypropylene (PP) might be used in specific GM models or for different components of the fuel system. It's important to check the vehicle's manual or consult a mechanic for precise information.
Identifying the plastic type can be done by examining the fuel line's color, flexibility, and any markings on the line itself. HDPE fuel lines are often black or dark-colored and feel stiff but flexible. Look for any labels or codes on the fuel line, as they might indicate the plastic type.
HDPE is generally considered safe and reliable for fuel lines, but some older GM models might have used HDPE with additives that could degrade over time. If your vehicle is older, it's advisable to inspect the fuel lines for any signs of deterioration or consult a professional for an assessment.
Replacing fuel lines with a different plastic type is possible but should be done with caution. Ensure the replacement plastic is compatible with the fuel type and meets GM specifications. Always consult a qualified mechanic or refer to the vehicle's manual for guidance on choosing the right replacement parts.