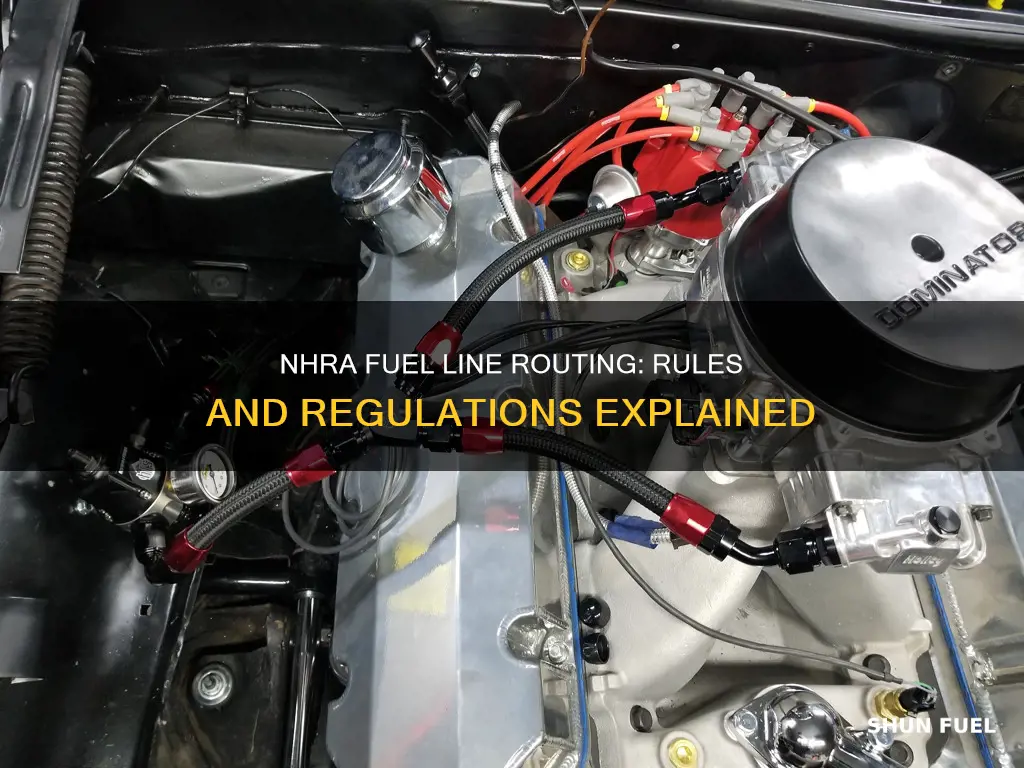
NHRA (National Hot Rod Association) has specific rules and regulations for fuel lines in drag racing vehicles to ensure safety and performance. The fuel line route is a critical aspect of the vehicle's design, as it determines how fuel is delivered to the engine during a race. Understanding the required fuel line route is essential for builders and racers to comply with NHRA rules and optimize their vehicle's performance on the drag strip. This paragraph will explore the specific requirements and considerations for fuel line routing in NHRA-sanctioned events.
Characteristics | Values |
---|---|
Fuel Line Material | High-pressure, flexible fuel lines made of materials like steel or aluminum |
Routing | Specific route to ensure fuel delivery to the engine while maintaining a certain distance from the ground |
Diameter | Typically 3/8" to 1/2" in diameter, depending on the engine and fuel system requirements |
Length | Varies based on the vehicle's layout and engine position |
Connections | Secure and tight connections to the fuel pump, fuel injectors, and other components |
Flexibility | Able to withstand engine vibrations and movement during acceleration and deceleration |
Temperature Resistance | Capable of withstanding high temperatures to prevent fuel degradation |
Compatibility | Compatible with the type of fuel used (e.g., ethanol, methanol) |
Safety Features | May include safety devices like fuel pressure regulators and shut-off valves |
NHRA Regulations | Adherence to NHRA rules and guidelines for fuel system specifications |
What You'll Learn
- Fuel Line Routing Rules: Specific rules dictate the path fuel lines must take to ensure safety and performance
- Length and Diameter Limits: NHRA sets maximum lengths and diameters for fuel lines to prevent leaks and hazards
- Material Requirements: Only approved materials can be used for fuel lines to meet NHRA standards
- Clamping and Support: Proper clamping and support are essential to maintain fuel line integrity during high-speed racing
- Testing and Inspection: Fuel lines undergo rigorous testing and inspection to ensure they meet NHRA specifications
Fuel Line Routing Rules: Specific rules dictate the path fuel lines must take to ensure safety and performance
The National Hot Rod Association (NHRA) has strict guidelines for fuel line routing in drag racing vehicles to ensure optimal performance and safety. These rules are designed to minimize the risk of fuel leaks, which could lead to dangerous situations on the track. The fuel lines must be carefully positioned to avoid interference with other components and to maintain a consistent and efficient fuel supply to the engine.
One of the primary rules is that the fuel lines must be as short as possible to reduce the risk of fuel pressure drop and ensure a steady flow. This means that the lines should be routed directly from the fuel pump to the engine, with minimal bends and twists. Any unnecessary lengthening of the lines can introduce restrictions and potentially cause performance issues. The NHRA specifies that the fuel lines should be no longer than 12 inches from the pump to the engine block, ensuring a direct and efficient path.
Additionally, the routing must avoid any sharp bends or kinks, as these can lead to fuel restriction and potential engine misfires. The lines should be routed in a straight line, with gentle curves where necessary, to maintain a consistent fuel flow. Any sharp turns can cause turbulence in the fuel, leading to air bubbles and reduced performance. The NHRA recommends using flexible fuel lines with a minimum inside diameter of 3/8 inch to accommodate the required straight and smooth routing.
Another critical aspect is the placement of the fuel lines relative to other vehicle components. The lines must be positioned away from hot surfaces, such as exhaust manifolds and headers, to prevent damage from heat. They should also be kept clear of moving parts, like the transmission and driveshaft, to avoid potential damage or interference. Proper insulation and protective sleeves may be required to shield the fuel lines from these sources of heat and potential hazards.
Furthermore, the NHRA has specific rules regarding the use of fuel line connectors and fittings. All connections must be secure and tight to prevent fuel leaks. The use of high-quality, race-approved connectors is mandatory, and any modifications or alterations to the original fittings are strictly prohibited. Regular inspections of the fuel lines and connections are essential to ensure compliance with these rules and to maintain the safety and performance of the vehicle.
Choosing the Right Fuel Line for Your Avenger Carb: A Guide
You may want to see also
Length and Diameter Limits: NHRA sets maximum lengths and diameters for fuel lines to prevent leaks and hazards
The National Hot Rod Association (NHRA) has strict regulations regarding fuel line routing to ensure the safety and performance of racing vehicles. One critical aspect of these rules is the specification of maximum lengths and diameters for fuel lines. These limits are designed to prevent potential hazards and fuel leaks, which could lead to dangerous situations during high-speed racing.
According to NHRA guidelines, fuel lines must adhere to specific dimensions to maintain structural integrity and minimize the risk of failure. The maximum length of a fuel line is typically limited to 6 inches, ensuring that the line is short enough to prevent excessive flexibility and potential damage during acceleration and deceleration. Longer fuel lines could lead to increased stress on the connections and an elevated risk of rupture, especially under the extreme conditions of drag racing.
In addition to length, NHRA also sets maximum diameter requirements for fuel lines. The diameter must be sufficient to handle the expected fuel flow rate while maintaining a safe pressure drop. A smaller diameter than specified could result in reduced fuel capacity and performance, while a larger diameter might increase the risk of fuel line damage or interference with other vehicle components. The optimal diameter ensures efficient fuel delivery while adhering to the safety standards set by the association.
These length and diameter limits are crucial in preventing fuel leaks, which can have severe consequences in a racing environment. Leaks can lead to fuel loss, affecting engine performance and potentially causing dangerous situations on the track. By adhering to the NHRA's specifications, racers can ensure that their fuel lines are robust, reliable, and capable of withstanding the rigorous demands of high-performance racing.
It is essential for racers and mechanics to be well-versed in these regulations to ensure compliance and maintain the safety of their vehicles. Understanding and implementing the correct fuel line dimensions are vital steps in preparing a car for NHRA-sanctioned events, contributing to a safer and more competitive racing experience.
The Strange Sound of Frozen Fuel Lines: A Guide
You may want to see also
Material Requirements: Only approved materials can be used for fuel lines to meet NHRA standards
The NHRA (National Hot Rod Association) has strict regulations and standards for all aspects of vehicle construction, including fuel lines. When it comes to fuel lines, only specific materials are approved to ensure safety and performance. These approved materials are crucial to meeting the NHRA's requirements and must be adhered to by all competitors and enthusiasts.
The primary reason for this material restriction is safety. Fuel lines carry high-pressure fuel, and any compromise in material quality can lead to dangerous situations. Approved materials are designed to withstand the extreme conditions of racing, including high temperatures, vibrations, and fuel compatibility. For instance, the NHRA specifies that fuel lines must be made from materials that are resistant to fuel degradation, such as certain types of rubber or synthetic compounds. This ensures that the fuel lines do not deteriorate over time, leading to potential fuel leaks or system failures.
Additionally, the NHRA's material requirements are designed to maintain the integrity and performance of the fuel system. Approved materials are chosen for their ability to provide a reliable and consistent fuel supply to the engine. This is particularly important in racing, where every millisecond counts, and any disruption in fuel delivery can result in a loss of power or even engine failure. By using only approved materials, competitors can ensure that their fuel lines are built to last and provide the necessary performance characteristics.
It is essential for builders and racers to consult the NHRA's official guidelines and specifications when selecting materials for fuel lines. These guidelines outline the approved materials, their properties, and the manufacturing processes that must be followed. Adhering to these standards ensures that the fuel lines meet the required quality and performance levels, providing peace of mind and confidence in the vehicle's fuel system.
In summary, the NHRA's material requirements for fuel lines are a critical aspect of vehicle construction, emphasizing safety and performance. By using only approved materials, competitors can ensure compliance with NHRA standards, maintain the integrity of their fuel systems, and ultimately enhance their racing experience. It is a fundamental aspect of building a reliable and safe racing machine.
Understanding Fuel Line Flaring: A Comprehensive Guide
You may want to see also
Clamping and Support: Proper clamping and support are essential to maintain fuel line integrity during high-speed racing
In the high-octane world of NHRA (National Hot Rod Association) racing, where speeds can exceed 300 mph, the importance of a well-designed and securely installed fuel system cannot be overstated. One critical aspect of this system is the fuel line route and its secure clamping and support. Proper clamping and support are essential to ensure the fuel lines remain intact and functional under extreme conditions, preventing fuel leaks and potential engine failure.
The fuel lines in NHRA racing cars are typically routed through the engine compartment and along the vehicle's frame, often in close proximity to moving parts. To withstand the intense forces and vibrations experienced during high-speed runs, these lines must be securely fastened. Clamps play a vital role in this process, as they provide the necessary tension and stability to keep the fuel lines in place. The choice of clamp material and design is crucial; stainless steel or aluminum clamps with a robust construction are often preferred for their durability and ability to retain their shape under stress.
When clamping the fuel lines, it is essential to follow a systematic approach. Start by identifying the critical areas where the lines are most susceptible to movement, such as near the engine block and transmission. Here, multiple clamps should be used to ensure a tight and secure fit. The clamps should be tightened evenly to avoid creating uneven pressure points, which could lead to line damage. Additionally, consider the use of flexible clamps in areas where the fuel lines must bend or follow the contours of the vehicle's body, ensuring a smooth and secure installation.
Support structures, such as fuel line brackets and hangers, are another critical component of the fuel system's integrity. These brackets provide additional support and help maintain the fuel lines' position, especially in high-stress areas. They should be securely mounted to the vehicle's frame or other rigid structures, ensuring that the fuel lines are neither pinched nor subjected to excessive strain. Proper support is particularly important for long fuel lines, as it helps prevent sagging and potential damage from road irregularities during high-speed runs.
Furthermore, regular inspection and maintenance of the fuel line clamping and support system are imperative. NHRA teams should conduct routine checks to ensure that all clamps are tight and in good condition, replacing any that show signs of wear or damage. This proactive approach helps identify potential issues before they cause critical failures during races. By maintaining a high level of detail and precision in the clamping and support system, NHRA teams can ensure that their fuel lines remain secure and reliable, contributing to the overall performance and success of their vehicles.
Thawing Frozen Fuel Lines: A Guide to Winter Car Care
You may want to see also
Testing and Inspection: Fuel lines undergo rigorous testing and inspection to ensure they meet NHRA specifications
Fuel lines play a critical role in the performance and safety of high-performance vehicles, especially in the NHRA (National Hot Rod Association) racing world. To ensure the integrity and reliability of these fuel lines, a comprehensive testing and inspection process is mandatory. This process is designed to verify that the fuel lines meet the specific requirements set by the NHRA, which are crucial for maintaining the vehicle's performance and safety during racing events.
The testing and inspection process typically begins with a visual examination of the fuel lines. This initial assessment involves checking for any visible damage, such as cracks, kinks, or signs of corrosion. Technicians use specialized tools and lighting to inspect the lines thoroughly, ensuring that no potential issues are overlooked. The goal is to identify any physical defects that could compromise the fuel line's functionality and safety.
After the visual inspection, fuel lines are subjected to pressure testing. This test is essential to assess the line's ability to withstand the high pressures generated during racing. Technicians use specialized equipment to apply pressure to the fuel lines and measure their response. Any leaks or weaknesses in the line's structure are identified during this stage, ensuring that the fuel lines can handle the extreme conditions of high-speed racing.
Furthermore, the material composition and thickness of the fuel lines are critical factors in NHRA specifications. Technicians analyze the fuel lines to ensure they are made from the correct materials and have the appropriate thickness to withstand the rigors of racing. This includes checking for any deviations from the manufacturer's specifications, ensuring that the fuel lines meet the required standards for durability and performance.
In addition to these tests, fuel lines must also pass dynamic testing, which involves simulating the high-stress conditions of racing. This includes testing the lines under various angles, vibrations, and temperatures to ensure they remain intact and functional. The inspection process is rigorous, leaving no stone unturned to guarantee that the fuel lines are fit for the demanding environment of NHRA racing.
Marine Fuel Line: Choosing the Right Option for Your Boat
You may want to see also
Frequently asked questions
The NHRA (National Hot Rod Association) has specific rules for fuel lines in drag racing to ensure safety and performance. For fuel-injected engines, the fuel line must be routed from the fuel pump to the fuel pressure regulator, then to the fuel injectors. It should be a direct path with minimal bends to prevent fuel pressure loss and ensure efficient fuel delivery.
Yes, the fuel line diameter is regulated by NHRA. The minimum diameter is 3/8 inches, and the maximum is 1/2 inch. This standard ensures that the fuel line can handle the required fuel flow while maintaining a safe pressure drop.
NHRA requires that the fuel line be securely fastened to the vehicle's body or frame using appropriate ties or brackets. The line should be tied down at regular intervals to prevent excessive movement, which could lead to damage or fuel leaks. Proper routing and support are crucial to meet the safety standards.
The length of the fuel line is not a primary concern, but it should be long enough to reach the fuel injectors without causing unnecessary strain or interference with other components. NHRA focuses more on the route and security of the fuel line rather than its length.