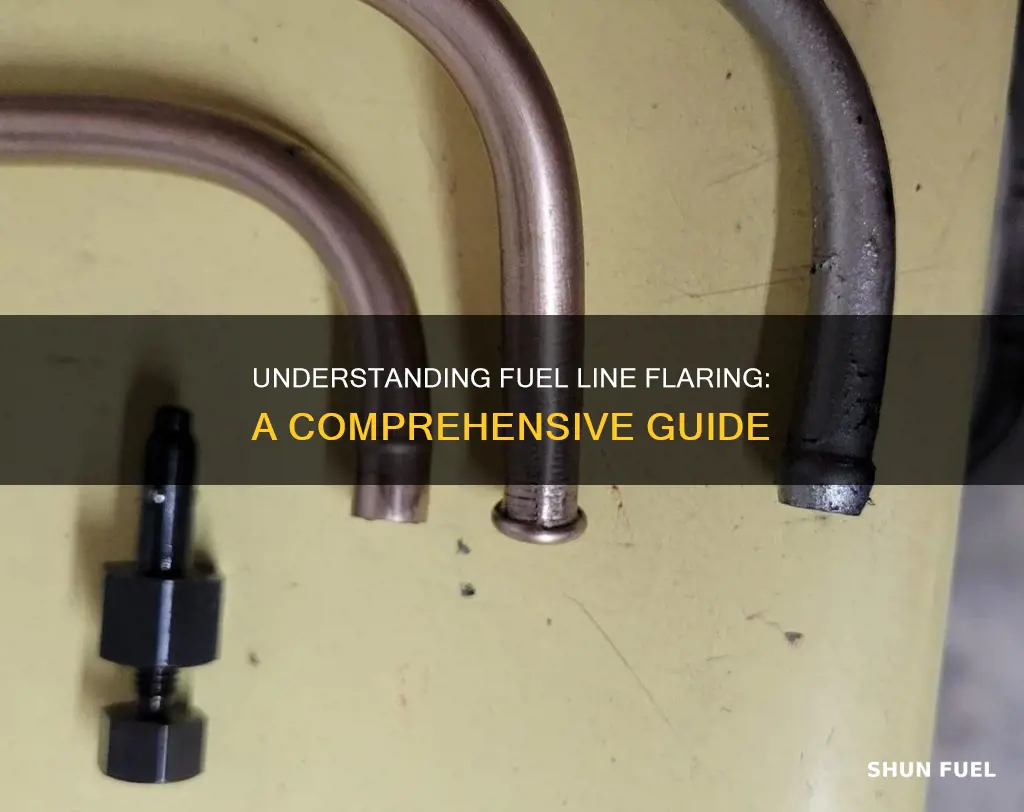
What degree is fuel line flared? This question delves into the technical specifications of fuel lines, particularly the angle at which they are bent or flared. Understanding the degree of flaring is crucial in various industries, such as automotive and aviation, where precise fuel delivery systems are essential for optimal performance and safety. The flaring angle affects the flow rate, pressure, and overall efficiency of the fuel system, making it a critical consideration in design and maintenance. This paragraph sets the stage for a detailed exploration of the factors influencing flaring degrees and their implications in different applications.
What You'll Learn
- Fuel Line Material: Different materials (metal, plastic) offer varying durability and corrosion resistance for fuel lines
- Flaring Techniques: Various methods (crimping, swaging) are used to create a secure and leak-free connection at the fuel line flare
- Flared Size Compatibility: Ensuring the flare size matches the fuel line diameter is crucial for proper fuel flow and pressure
- Fuel Line Routing: Proper routing minimizes stress and potential damage to the fuel line flare connection
- Maintenance and Inspection: Regular checks for leaks, corrosion, and damage are essential to maintain the integrity of the fuel line flare
Fuel Line Material: Different materials (metal, plastic) offer varying durability and corrosion resistance for fuel lines
When it comes to fuel lines, the choice of material is a critical factor that can significantly impact the overall performance and longevity of the system. Fuel lines are responsible for transporting fuel from the tank to the engine, and the material used can determine the durability and reliability of this vital component. Two common materials used for fuel lines are metal and plastic, each offering distinct advantages and considerations.
Metal fuel lines, typically made from materials like steel or aluminum, are renowned for their exceptional durability. These lines are known to withstand high pressure and temperature variations, making them ideal for high-performance vehicles or those operating in extreme conditions. Metal's inherent strength provides excellent resistance to kinking and crushing, ensuring a reliable fuel supply even in challenging environments. Additionally, metal fuel lines often feature a protective coating or plating to enhance corrosion resistance, further extending their lifespan. However, metal lines can be heavier and more rigid, which might impact the overall flexibility of the fuel system.
On the other hand, plastic fuel lines have gained popularity due to their lightweight and flexibility. Materials such as high-density polyethylene (HDPE) or polyvinyl chloride (PVC) offer excellent resistance to corrosion, making them suitable for vehicles with fuel tanks located in areas prone to moisture or corrosive elements. Plastic lines are generally more flexible, allowing for easier installation and routing around engine components. This flexibility also reduces the risk of damage during vehicle movement or maintenance. Moreover, plastic fuel lines are often more cost-effective compared to metal alternatives, making them an attractive option for budget-conscious consumers.
The choice between metal and plastic fuel lines depends on various factors, including the specific vehicle requirements, environmental conditions, and personal preferences. For high-performance or off-road vehicles, metal lines might be preferred for their superior strength and durability. In contrast, plastic lines could be the ideal choice for everyday vehicles, offering a balance between performance and cost. It is essential to consider the potential trade-offs, such as weight and flexibility, when deciding on the most suitable material for fuel lines.
In summary, the material of fuel lines plays a crucial role in determining their performance and longevity. Metal lines provide exceptional durability and corrosion resistance, making them suitable for demanding conditions, while plastic lines offer flexibility, lightweight design, and cost-effectiveness. Understanding the characteristics of each material allows vehicle owners and mechanics to make informed decisions, ensuring a reliable and efficient fuel system.
Air in Diesel Fuel Lines: Causes and Solutions
You may want to see also
Flaring Techniques: Various methods (crimping, swaging) are used to create a secure and leak-free connection at the fuel line flare
Flaring is a crucial process in creating a secure and leak-free connection for fuel lines, ensuring optimal performance and safety in automotive and industrial applications. This technique involves shaping the end of a fuel line to form a precise, conical shape, which then mates with a corresponding flare fitting. The flare fitting is designed to provide a tight seal, preventing fuel leaks and ensuring efficient fuel delivery. The process of flaring is an art that requires precision and skill, and various methods are employed to achieve the desired results.
One common method is crimping, which involves applying pressure to the flare fitting using specialized tools. The fuel line is inserted into the fitting, and the crimping process compresses the material, creating a secure and leak-resistant seal. Crimping ensures that the flare is tightly held in place, providing a robust connection. This technique is often used in high-pressure applications where a strong, reliable seal is essential.
Swaging is another flaring technique that offers a different approach to achieving a secure connection. This method involves the use of a swaging tool, which deforms the flare fitting by applying force in a controlled manner. The fuel line is inserted, and the swaging process creates a series of folds or swages along the flare, forming a tight, continuous seal. Swaging provides excellent pressure distribution and is particularly useful for creating a secure connection in larger diameter fuel lines.
Both crimping and swaging techniques require precision and skill to ensure the flare is properly formed and aligned. The goal is to create a uniform, consistent flare that mates perfectly with the corresponding fitting. This ensures a tight seal, preventing fuel from escaping and minimizing the risk of contamination or system failure. Proper flaring techniques are essential for maintaining the integrity of the fuel system and overall vehicle or equipment performance.
In summary, flaring techniques, including crimping and swaging, are vital processes in creating secure and leak-free connections for fuel lines. These methods ensure that fuel lines are properly sealed, preventing potential hazards and maintaining the efficiency of fuel delivery systems. Skilled technicians use these techniques to ensure the highest standards of quality and safety in various industries.
Understanding Fuel Lines: The Vital Link in Your Engine's Fuel Supply
You may want to see also
Flared Size Compatibility: Ensuring the flare size matches the fuel line diameter is crucial for proper fuel flow and pressure
When it comes to ensuring optimal performance in fuel systems, understanding the importance of flared size compatibility is essential. This concept revolves around the precise matching of flare sizes to the corresponding fuel line diameters. By doing so, you create an efficient pathway for fuel to travel from the source to the engine, ensuring a steady and controlled supply.
The process begins with identifying the fuel line's internal diameter, a critical measurement that determines the size of the flare required. This diameter is typically measured in inches or millimeters, and it directly influences the flow rate and pressure of the fuel. For instance, a larger fuel line diameter will necessitate a larger flare to accommodate the increased volume and maintain optimal performance.
Flared sizes are often categorized using a specific degree measurement, commonly referred to as the 'flare angle.' This angle is crucial because it dictates the shape and size of the flare. A higher flare angle results in a more compact and precise flare, which is ideal for applications where space is limited. Conversely, a lower angle provides a larger flare, allowing for better flow characteristics and pressure regulation.
Ensuring compatibility between the flare size and fuel line diameter is a delicate balance. If the flare is too small, it may restrict fuel flow, leading to reduced performance and potential engine issues. On the other hand, an oversized flare can cause unnecessary pressure drops and inefficiencies. Therefore, precise measurements and careful selection of flare sizes are imperative.
In summary, achieving proper fuel flow and pressure requires a meticulous approach to flare size compatibility. By matching the flare angle to the fuel line's internal diameter, engineers and mechanics can optimize the fuel system's performance. This attention to detail ensures that the fuel delivery process is efficient, reliable, and tailored to the specific requirements of the engine.
Fuel Line for Your 96 Civic: A Guide to Finding the Right Fit
You may want to see also
Fuel Line Routing: Proper routing minimizes stress and potential damage to the fuel line flare connection
The proper routing of fuel lines is a critical aspect of vehicle maintenance, especially when it comes to minimizing stress and potential damage to the fuel line flare connection. This connection is a crucial component in the fuel system, responsible for securely attaching the fuel line to the engine or fuel tank. When this connection is compromised due to improper routing, it can lead to fuel leaks, reduced engine performance, and even safety hazards.
When routing fuel lines, the primary goal is to ensure that the lines are not subjected to unnecessary tension or stress. Fuel lines should be routed in a way that allows for flexibility and easy movement, especially in areas where the vehicle's components may shift during operation. One common practice is to use a loop or a slight bend in the fuel line near the flare connection. This loop provides a natural point of flexibility, reducing the likelihood of the line being pulled taut and causing strain on the connection.
Additionally, it is essential to avoid sharp bends or kinks in the fuel line, as these can create localized stress points. The fuel line should be routed away from high-stress areas, such as suspension components, exhaust systems, and moving parts. By maintaining a consistent and smooth path, you can ensure that the fuel line flare connection remains intact and secure.
In some cases, the use of protective sleeves or conduits may be necessary to shield the fuel line from potential damage. These protective measures are especially important when routing the line near heat sources, sharp edges, or other potential hazards. By providing an additional layer of protection, you can further minimize the risk of damage to the fuel line flare connection.
In summary, proper fuel line routing is a vital practice that directly contributes to the longevity and reliability of a vehicle's fuel system. By minimizing stress and potential damage to the fuel line flare connection, you can ensure that the vehicle operates efficiently and safely. Regular inspection and maintenance of fuel lines are also recommended to identify and address any issues promptly.
Fuel Injector Line Maintenance: Is Cleaning Necessary?
You may want to see also
Maintenance and Inspection: Regular checks for leaks, corrosion, and damage are essential to maintain the integrity of the fuel line flare
The fuel line flare is a critical component in any vehicle's fuel system, and its maintenance and inspection are often overlooked but essential tasks. Regular checks are vital to ensure the system's integrity and prevent potential issues that could lead to costly repairs. Here's a detailed guide on why and how to maintain and inspect this crucial part.
Firstly, it is important to understand the purpose of a fuel line flare. This component is designed to connect the fuel tank to the engine, allowing the fuel to flow efficiently while ensuring a secure and tight seal. Over time, however, this flare can be susceptible to various issues. Leaks, for instance, can occur due to worn-out gaskets or seals, which may go unnoticed until significant fuel loss is observed. Corrosion is another common problem, especially in older vehicles or those exposed to harsh weather conditions. This corrosion can lead to a deterioration of the flare's internal components, reducing its effectiveness.
Regular maintenance and inspection are key to preventing these issues. A simple yet effective practice is to check for any signs of leaks regularly. This can be done by applying a small amount of diesel or fuel-based lubricant around the flare and observing if any fuel appears. Even a small leak can lead to engine performance issues and potential safety hazards. Additionally, inspecting the flare for corrosion is crucial. Look for any signs of rust or oxidation, especially in areas where the flare connects to the fuel tank and engine. Corrosion can weaken the flare's structure and compromise its ability to seal properly.
During inspections, it is also important to check for physical damage. Over time, the flare may be subjected to vibrations and impacts, leading to potential cracks or bends. These issues can go unnoticed until the flare fails, causing fuel starvation to the engine. Inspecting the flare for any visible damage, such as cracks, bends, or kinks, is essential. It is recommended to use a borescope or a small camera to inspect the internal components of the flare for any blockages or debris.
In summary, maintaining and inspecting the fuel line flare is a critical aspect of vehicle care. By regularly checking for leaks, corrosion, and physical damage, you can ensure the flare's integrity and prevent potential engine issues. This simple maintenance practice can save vehicle owners from costly repairs and ensure their engines run efficiently and safely. Remember, a well-maintained fuel system is a key component in overall vehicle performance and longevity.
Fuel Injector Linearity: A Matter of Efficiency and Precision
You may want to see also
Frequently asked questions
Fuel line flaring is a process used in the construction and maintenance of fuel systems, particularly in the automotive and aviation industries. It involves the use of specialized tools to create a flared or expanded end on a fuel line, which helps to ensure a secure and leak-tight connection.
Flaring is essential to prevent fuel leaks and ensure the integrity of the fuel system. It provides a reliable seal, allowing fuel to flow efficiently without the risk of spills or contamination. This process is critical in aviation, where fuel lines are exposed to extreme conditions and vibrations.
Flaring tools come in various types, including manual and powered options. Manual flaring tools are commonly used for smaller fuel lines and require the operator to apply force and precision. Powered flaring machines, on the other hand, are more efficient and can handle larger diameters, making them suitable for aviation fuel systems.
While some basic flaring techniques can be learned and performed by individuals, professional-grade flaring is best left to experienced technicians and engineers. The process requires precision, specialized tools, and knowledge of fuel system design to ensure safety and proper functionality.
Yes, flaring techniques can vary depending on the material of the fuel line. For example, stainless steel fuel lines may require a different flaring process compared to aluminum or brass lines. Each material has unique properties that influence the flaring method, ensuring a proper seal and compatibility.