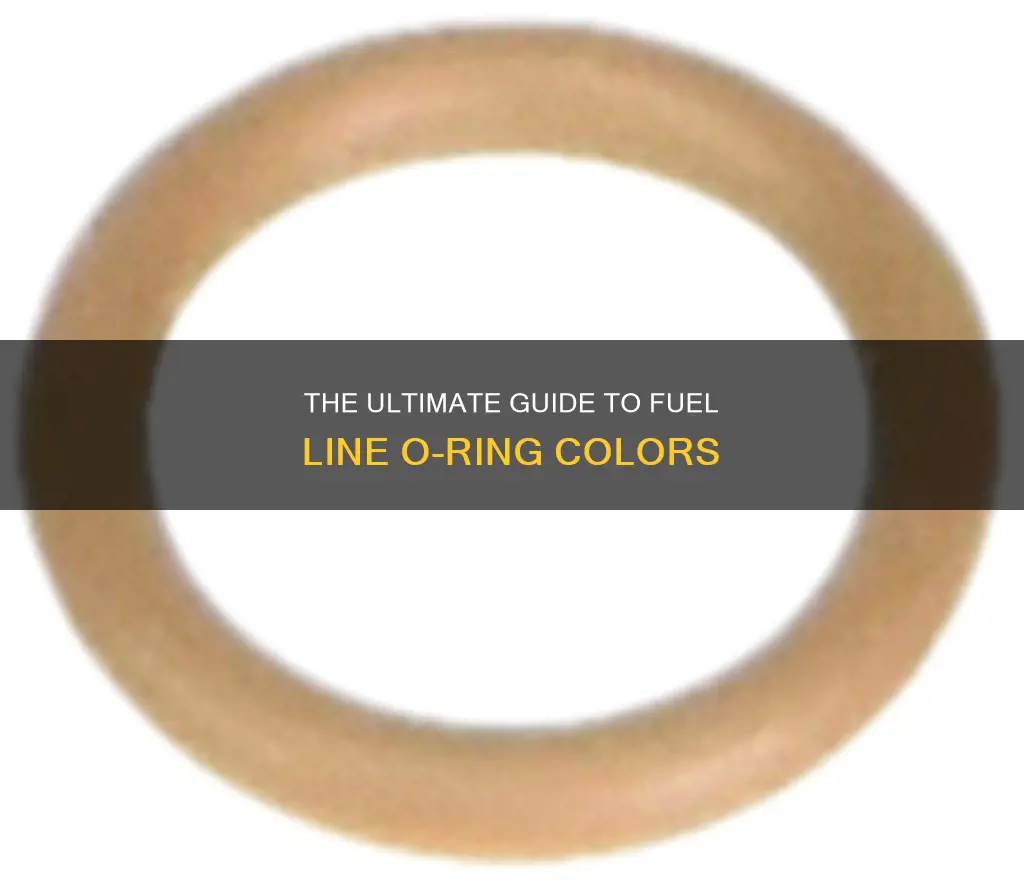
When it comes to vehicle maintenance, one crucial aspect often overlooked is the condition of the fuel lines. These lines are responsible for transporting fuel from the tank to the engine, and over time, they can develop leaks or become damaged. To prevent fuel leaks and ensure optimal engine performance, it is essential to use the correct color O-ring for the fuel line. The color of the O-ring is a simple yet effective way to identify the correct type and size for a specific application, ensuring a proper seal and preventing fuel from escaping. Understanding the significance of this small but vital component can help vehicle owners and mechanics make informed decisions during repairs and replacements.
What You'll Learn
- Material Compatibility: O-rings for fuel lines must be compatible with the fuel type to prevent degradation
- Temperature Tolerance: O-rings should withstand fuel temperature fluctuations without hardening or melting
- Pressure Resistance: Fuel lines require O-rings that can handle pressure without leaking or failing
- Vibration Resistance: O-rings must remain intact and functional despite engine vibrations and movement
- Color Coding: Manufacturers often use color-coded O-rings for easy identification and proper installation
Material Compatibility: O-rings for fuel lines must be compatible with the fuel type to prevent degradation
When it comes to fuel lines, the choice of O-ring material is critical to ensure the safe and efficient operation of the system. Material compatibility is a key consideration, as it directly impacts the performance and longevity of the fuel line assembly. O-rings are an essential component in fuel lines, providing a seal to prevent fuel leakage and maintain system integrity. However, the compatibility of these O-rings with the fuel type is a crucial factor that cannot be overlooked.
The primary concern with material compatibility is the potential for degradation. Different fuels have varying chemical compositions and properties, and some can be detrimental to certain O-ring materials. For instance, gasoline, with its higher volatility and potential for containing ethanol, can be particularly challenging. Ethanol, a common additive in modern gasoline, can dissolve certain O-ring materials, leading to swelling, softening, or even disintegration over time. This degradation can result in fuel leaks, engine misfires, and potential safety hazards.
To address this issue, engineers and manufacturers carefully select O-ring materials that are resistant to the specific fuel types used. For gasoline applications, O-rings made from materials like nitrile rubber (NBR) or fluorinated elastomers (such as Viton®) are commonly used. These materials offer excellent resistance to gasoline's volatile nature and the presence of ethanol. NBR, for example, provides good flexibility and chemical resistance, making it suitable for a wide range of fuel applications.
In the case of diesel fuel, the choice of O-ring material may differ. Diesel fuel, being less volatile and containing no ethanol, can be compatible with a broader range of materials. However, it is still essential to consider the specific properties of the diesel fuel, including its sulfur content and other additives. Materials like neoprene or butyl rubber can be suitable for diesel applications due to their resistance to fuel degradation.
In summary, material compatibility is a critical aspect of designing and maintaining fuel lines. O-rings must be chosen based on their ability to withstand the chemical properties of the fuel they will encounter. By selecting the right O-ring material, engineers can ensure that fuel lines remain leak-free, maintain engine performance, and provide a safe and reliable fuel delivery system. It is always advisable to consult manufacturer guidelines and industry standards to determine the most appropriate O-ring materials for specific fuel types.
Outboard Fuel Confusion: Diesel or Gasoline? Unraveling the Mystery
You may want to see also
Temperature Tolerance: O-rings should withstand fuel temperature fluctuations without hardening or melting
O-rings play a critical role in ensuring the integrity and safety of fuel systems in various applications, including automotive, aviation, and industrial settings. When it comes to fuel lines, the choice of O-ring material is crucial, especially regarding temperature tolerance. Fuel temperatures can vary significantly, from extremely cold in winter to hot during engine operation, and these temperature fluctuations can have a direct impact on the O-ring's performance.
The primary concern with temperature variations is the potential for O-rings to harden or melt. Hardening occurs when the O-ring material becomes brittle due to cold temperatures, losing its flexibility and sealing properties. This can lead to leaks or reduced performance, as the O-ring may not effectively seal the fuel line, allowing fuel to escape or contaminate other components. On the other hand, melting happens when the O-ring material is exposed to excessive heat, causing it to deform or lose its shape. This can result in a failure to seal properly, leading to fuel leaks and potential engine damage.
To address these challenges, O-rings designed for fuel lines are typically made from materials with excellent temperature resistance. These materials are carefully selected to maintain their flexibility and sealing capabilities across a wide temperature range. For instance, synthetic rubbers like nitrile or fluorocarbon rubbers are commonly used due to their ability to withstand both extreme cold and high temperatures without hardening or melting. These materials have a high resistance to fuel degradation, ensuring that the O-ring remains effective over an extended period.
In addition to material selection, the design and manufacturing process of O-rings also contribute to their temperature tolerance. Engineers consider the specific fuel system requirements and operating conditions to choose the appropriate O-ring dimensions and cross-sectional shapes. This ensures that the O-ring can effectively seal the fuel line while accommodating temperature-induced changes without compromising its performance.
In summary, temperature tolerance is a critical aspect of O-rings used in fuel lines. These O-rings must withstand significant temperature fluctuations without hardening or melting to ensure the safe and efficient operation of fuel systems. By utilizing materials with excellent temperature resistance and carefully designing the O-rings, engineers can provide reliable sealing solutions that meet the demanding requirements of fuel line applications.
Unraveling the Mystery: Lines Attached to the Fuel Pump
You may want to see also
Pressure Resistance: Fuel lines require O-rings that can handle pressure without leaking or failing
When it comes to fuel lines, the choice of O-ring color is not merely a cosmetic decision but a critical factor in ensuring the system's reliability and performance. The primary concern here is the O-ring's ability to withstand the pressure within the fuel system without compromising its integrity. This is especially crucial in automotive applications, where fuel lines are exposed to varying pressure levels, from the pump to the engine.
The pressure resistance of an O-ring is determined by its material composition and design. For fuel lines, synthetic rubber O-rings are commonly used due to their superior resistance to fuel chemicals and their ability to maintain flexibility over a wide temperature range. Among the various synthetic rubbers, nitrile rubber (NBR) and fluorocarbon rubber (FPM) are popular choices. NBR offers excellent resistance to fuels and oils, making it ideal for fuel lines, while FPM provides even higher resistance to fuel chemicals, ensuring long-term reliability.
The design of the O-ring also plays a significant role in pressure resistance. The cross-sectional shape and the number of grooves (or lips) on the O-ring can affect its ability to seal under pressure. For fuel lines, a standard O-ring with a single groove is often sufficient, but in some high-pressure applications, a double-lip O-ring may be necessary to provide a more secure seal. The O-ring's dimensions should also be carefully selected to ensure a proper fit within the fuel line and the mating component, allowing for a tight seal without excessive force that could lead to premature failure.
In addition to material and design considerations, the installation process is vital to achieving optimal pressure resistance. Proper alignment and insertion of the O-ring into the fuel line are essential to ensure a uniform seal. Any misalignment or improper installation can lead to uneven pressure distribution, potentially causing the O-ring to fail prematurely.
In summary, the O-ring used in fuel lines must possess exceptional pressure resistance to prevent leaks and ensure the safe operation of the vehicle. The choice of material, design, and installation technique all contribute to the overall performance and longevity of the fuel system. By selecting the right O-ring and following best practices, engineers and mechanics can ensure that fuel lines remain reliable and efficient, even under demanding conditions.
Emergency Fuel Line Fixes: Quick Solutions for Leaks & Clogs
You may want to see also
Vibration Resistance: O-rings must remain intact and functional despite engine vibrations and movement
O-rings play a critical role in ensuring the integrity and performance of fuel lines in engines, and their ability to withstand vibrations is a key aspect of this function. Engine vibrations can be intense and constant, especially during operation, and these vibrations can cause significant stress on the components within the engine, including the O-rings. These rubber seals are designed to maintain a tight, leak-free connection between various parts, and their resistance to vibration is essential for the overall reliability and safety of the engine system.
The primary challenge with vibrations is that they can cause the O-rings to degrade or fail over time. O-rings are typically made from synthetic rubbers that are chosen for their flexibility and sealing properties. However, these materials can be susceptible to wear and tear when subjected to repetitive motion and impact. As the engine operates, the constant vibrations can lead to the O-rings losing their shape, becoming brittle, or even breaking apart. This failure can result in fuel leaks, which not only cause performance issues but also pose a potential fire hazard due to the volatile nature of fuel.
To address this issue, engineers have developed O-rings with specific properties to enhance their vibration resistance. One approach is to use compounds that are more resilient to mechanical stress. These compounds often include additives that improve the material's ability to absorb and distribute the energy from vibrations, preventing the O-rings from deforming or breaking. For instance, some O-rings are made with a higher durometer (a measure of hardness) to provide increased resistance to distortion under pressure and movement.
Additionally, the design and installation of the O-rings are crucial factors in ensuring vibration resistance. Engineers often specify unique designs, such as double-gland systems or O-rings with flanged ends, to provide additional support and stability. These designs help to anchor the O-rings in place, preventing them from being dislodged or damaged by the engine's vibrations. Proper installation techniques, including the use of appropriate lubricants and ensuring a secure fit, are also essential to maintain the O-rings' integrity.
In summary, vibration resistance is a critical requirement for O-rings used in fuel lines, as it ensures the long-term functionality and safety of the engine. By utilizing specialized materials and designs, engineers can create O-rings that can withstand the harsh conditions of an operating engine, providing a reliable seal that prevents fuel leaks and potential hazards. Understanding and addressing the impact of vibrations on O-rings is essential for maintaining the performance and longevity of fuel line systems.
Outboard Fuel Line Clogs: Causes and Solutions
You may want to see also
Color Coding: Manufacturers often use color-coded O-rings for easy identification and proper installation
Color coding is a crucial practice in the manufacturing and installation of O-rings, especially in critical applications like fuel lines. Manufacturers often employ this technique to ensure that the right O-ring is used in the correct position, preventing potential leaks and system failures. The color-coded system provides a simple yet effective method for identification, making it easier for technicians and engineers to select the appropriate O-ring for a specific application.
In the context of fuel lines, O-rings are typically designed with a specific color to indicate their compatibility and function. For instance, a bright red O-ring might be used for high-pressure fuel lines, while a green one could be designated for low-pressure applications. This color-coding system allows for quick visual identification, reducing the chances of human error during installation. When a fuel line is assembled, the corresponding color of the O-ring should match the color of the fuel line connector to ensure a proper seal.
The benefits of color coding extend beyond the initial installation process. In maintenance and repair scenarios, color-coded O-rings enable technicians to quickly identify the correct replacement part, ensuring that the system is restored to its original specifications. This is particularly important in industries where downtime due to equipment failure can be costly and potentially dangerous. By using color-coded O-rings, manufacturers provide a clear and consistent method for identifying the right components, streamlining the maintenance process.
Furthermore, color coding can also include additional information beyond just the application. Some manufacturers might use a two-color system, where the first color indicates the primary function and the second color represents a specific size or material. For example, a blue-green O-ring could signify a low-pressure, medium-sized, and temperature-resistant seal. This level of detail ensures that the O-ring is not only compatible with the system but also meets the specific requirements of the application.
In summary, color coding is an essential practice in O-ring manufacturing and installation, particularly for fuel lines and other critical systems. It simplifies the identification process, reduces installation errors, and facilitates efficient maintenance. By adhering to color-coded standards, manufacturers and technicians can ensure the reliability and safety of their systems, making it a valuable tool in the industry.
Chevy Fuel Tank: Understanding the Lines and Connections
You may want to see also
Frequently asked questions
The color of the O-ring used for fuel lines can vary depending on the manufacturer and the specific application. However, a common color for these O-rings is blue or black. These colors are often chosen for their visibility and to distinguish them from other components in the fuel system.
The color-coding of O-rings is a standard practice in the automotive and mechanical industries to ensure proper identification and installation. Different colors may indicate specific materials, durometers, or compatibility with certain substances, ensuring the right O-ring is used for the intended purpose.
It is generally not recommended to use an O-ring of a different color unless it is specifically designed for the fuel line application. Different colors may indicate different materials or properties, and using the wrong O-ring can lead to leaks, reduced performance, or even safety hazards.
Consult the vehicle's service manual or the manufacturer's specifications to identify the correct O-ring size and color. If you are unsure, it is best to consult a professional mechanic or contact the manufacturer's support team for guidance.
While there are some universal O-rings available, it is crucial to choose the correct size and material for your specific fuel line application. Universal O-rings may not always provide the best seal or compatibility, so it's essential to match the O-ring to the fuel line's requirements.