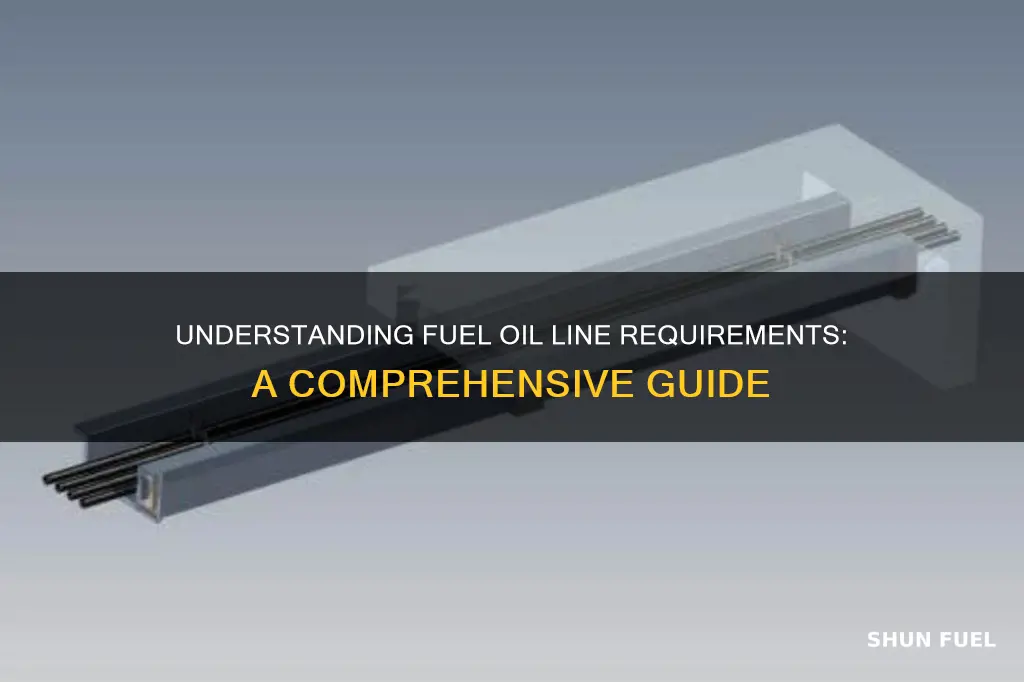
Fuel oil lines are an essential component of any heating system, and ensuring they meet specific requirements is crucial for safety and efficiency. These requirements encompass various aspects, including the type of fuel oil, line diameter, material composition, and installation standards. Understanding and adhering to these standards is vital to prevent potential hazards such as leaks, blockages, or system inefficiencies. This introduction aims to explore the critical factors that define the necessary specifications for fuel oil lines, highlighting their significance in maintaining a reliable and safe heating system.
What You'll Learn
- Line Material: Choose the right material for the fuel oil line, considering factors like temperature resistance and compatibility
- Line Diameter: Ensure the line diameter is adequate for the flow rate and pressure requirements of the fuel oil system
- Line Length: Calculate the required length of the line, considering the distance between the fuel tank and the burner
- Line Slope: Maintain a slight slope to allow for gravity-assisted fuel flow and prevent air locking
- Line Insulation: Insulate the line to prevent heat loss and protect against freezing temperatures
Line Material: Choose the right material for the fuel oil line, considering factors like temperature resistance and compatibility
When it comes to selecting the appropriate material for a fuel oil line, several critical factors come into play, primarily temperature resistance and compatibility. These considerations are essential to ensure the line's longevity, efficiency, and safety in the harsh conditions of a fuel oil system.
Temperature resistance is a key requirement for fuel oil lines. Fuel oil can vary in temperature depending on the climate and the specific fuel type. For instance, low-temperature fuels may require lines that can withstand freezing temperatures, while high-temperature fuels, like those used in industrial applications, need lines that can endure extreme heat. Materials such as high-density polyethylene (HDPE) and polyvinyl chloride (PVC) are often chosen for their excellent temperature resistance, making them suitable for a wide range of fuel oil applications.
Compatibility is another crucial aspect. The chosen material must be compatible with the fuel oil being transported. Different fuels have varying chemical compositions, and some materials may react with the fuel, leading to degradation or contamination. For example, certain types of rubber can be susceptible to dissolution in fuels containing acetone or other solvents. In such cases, materials like stainless steel, brass, or specific types of plastic, such as polypropylene, are preferred for their inertness and ability to withstand the chemical properties of the fuel.
Additionally, the line's material should be resistant to corrosion, especially in environments where fuel oil may contain acidic components. Materials like stainless steel and certain alloys are often used for their inherent corrosion resistance, ensuring the line's integrity over time.
In summary, the choice of material for a fuel oil line is a critical decision that requires careful consideration of temperature resistance and compatibility with the fuel. By selecting the right material, you can ensure the line's durability, efficiency, and safety in the specific conditions of the fuel oil system it serves. This attention to detail is essential for maintaining the overall performance and reliability of the fuel oil infrastructure.
Mastering Carb Fuel Lines: A Comprehensive Guide
You may want to see also
Line Diameter: Ensure the line diameter is adequate for the flow rate and pressure requirements of the fuel oil system
When it comes to fuel oil lines, ensuring the correct line diameter is crucial for the efficient and safe operation of the entire system. The line diameter refers to the size or cross-sectional area of the pipe or conduit that carries the fuel oil. Here's why this aspect is so important:
Flow Rate and Pressure: The primary consideration for line diameter is to accommodate the flow rate and pressure requirements of the fuel oil system. Fuel oil lines need to handle the volume and pressure of the fuel being transported without causing excessive wear and tear or potential system failures. If the line diameter is too small, it may lead to reduced flow rates, which can result in inadequate fuel supply to the engine or heating system. Conversely, a line that is too large can lead to unnecessary pressure drops and inefficiencies.
Engine Performance: Adequate line diameter is essential for maintaining optimal engine performance. Engines require a consistent and precise fuel-air mixture for efficient combustion. If the fuel oil line is too small, it may introduce turbulence or air pockets, leading to poor fuel atomization and incomplete combustion. This can result in reduced engine power, increased emissions, and potential engine damage over time.
System Efficiency: Proper line diameter ensures the overall efficiency of the fuel oil system. It minimizes energy losses due to friction and pressure drops, allowing for better fuel economy and reduced operating costs. Well-designed lines with appropriate diameters contribute to a more reliable and consistent fuel supply, especially in applications where temperature and pressure variations are common.
Safety Considerations: Safety is a critical aspect of fuel oil line design. A line with an incorrect diameter may lead to dangerous situations. For instance, a line that is too small could cause excessive pressure buildup, potentially leading to pipe bursting or leaks. Conversely, an oversized line might result in reduced system response time, making it challenging to control fuel flow during sudden changes in demand.
In summary, the line diameter is a critical factor in fuel oil system design. It directly impacts the system's ability to handle flow rates and pressure, ensuring optimal engine performance and overall efficiency. Engineers and technicians must carefully select the appropriate line diameter based on the specific requirements of the fuel oil system to guarantee safe and reliable operation.
Wedeater Fuel Lines Reversed: A Recipe for Disaster?
You may want to see also
Line Length: Calculate the required length of the line, considering the distance between the fuel tank and the burner
When designing a fuel oil system, one crucial aspect is determining the appropriate length of the fuel oil line to ensure efficient and safe operation. The line length calculation is a critical step that considers the distance between the fuel tank and the burner, as well as other factors that can influence the flow of fuel. Here's a detailed guide on how to approach this calculation:
Understanding the Basics:
The primary goal is to ensure that the fuel oil line has sufficient length to allow for safe and controlled delivery of fuel from the tank to the burner. The line should be long enough to accommodate potential expansion and contraction of the fuel due to temperature changes and to prevent excessive pressure drops. A common rule of thumb is to add a certain percentage of the total distance as a safety margin.
Calculating Line Length:
- Measure the Distance: Start by accurately measuring the straight-line distance between the fuel tank and the burner. This distance will be the baseline for your calculation.
- Consider Slope and Elevation: If the fuel tank and burner are not at the same level, you need to account for the slope and elevation changes. Calculate the vertical and horizontal distances separately and then use the Pythagorean theorem to find the hypotenuse, which represents the total line length.
- Add Safety Margin: To ensure a safe and efficient system, add a percentage of the total distance to the calculated length. A common practice is to add 10-15% of the total distance to account for potential variations and to allow for easy maintenance.
- Consider Line Diameter: The diameter of the fuel oil line also plays a role. Longer lines may require larger diameters to maintain adequate flow rates and minimize pressure drops.
Additional Considerations:
- Material and Insulation: Choose appropriate materials for the line, considering factors like corrosion resistance and temperature tolerance. Insulation may be necessary to prevent heat loss or gain, especially in outdoor applications.
- Bends and Joints: Plan for any necessary bends or joints in the line. Sharp bends can cause pressure drops, so allow for gradual transitions. Joints should be securely sealed to prevent leaks.
- Venting and Air Elimination: Ensure that the line has adequate venting to allow air to escape during startup and to prevent vacuum conditions that could draw contaminants into the system.
By carefully calculating the line length and considering various factors, you can ensure that the fuel oil system meets the requirements for safe and efficient operation, delivering fuel to the burner reliably and with minimal losses. This approach helps prevent issues like fuel starvation, pressure drops, and potential safety hazards associated with improper line sizing.
Understanding Fuel Line Direction: The Switch's Crucial Role
You may want to see also
Line Slope: Maintain a slight slope to allow for gravity-assisted fuel flow and prevent air locking
When designing and installing a fuel oil line system, one crucial aspect to consider is the line slope. Proper slope is essential to ensure efficient and reliable fuel flow while preventing issues such as air locking. Here's a detailed explanation of why and how to maintain a slight slope in your fuel oil lines:
Gravity-Assisted Fuel Flow: Fuel oil lines should be sloped in a way that encourages gravity to assist in the flow of the fuel. This means that the line should have a gentle downward gradient, especially when running from the storage tank to the burner or heating system. By allowing gravity to aid in the movement of the fuel, you ensure that the system can operate efficiently without the need for excessive pumping power. This is particularly important in larger fuel oil systems where the distance between the tank and the burner might be significant.
Preventing Air Locking: A slight slope is critical to preventing air locking, which can cause numerous problems. When the line is horizontal or nearly horizontal, it creates a risk of air entering the system. Air bubbles can lead to inefficient combustion, reduced heat output, and even complete shutdown of the heating system. By maintaining a slight downward slope, you encourage the fuel to flow continuously, displacing any air pockets and ensuring a consistent supply of fuel oil. This is especially crucial in cold weather conditions when the fuel might already be thicker and more prone to settling.
Slope Calculation: The slope of the fuel oil line should be kept to a minimum to avoid unnecessary complications. A general guideline is to maintain a slope of approximately 1/4 inch per foot of horizontal distance. This means that for every 4 feet of horizontal run, the line should drop by 1 inch. This gentle slope is sufficient to allow gravity to assist the fuel flow without causing excessive pressure or flow rate issues. It's important to measure and calculate the slope carefully to ensure it meets the requirements for your specific system.
Installation Considerations: When installing the fuel oil lines, pay close attention to the routing and positioning. The lines should be kept as straight as possible to minimize potential obstructions and ensure a consistent slope. Avoid sharp turns or kinks, as these can disrupt the flow and create areas where air locking is more likely to occur. Proper support and insulation of the lines are also essential to protect them from damage and ensure long-term reliability.
Regular Maintenance: Regular maintenance checks should include inspecting the slope of the fuel oil lines. Over time, lines can become misaligned or damaged, affecting their slope. Any deviations from the recommended slope should be addressed promptly to prevent potential issues. Maintaining the correct slope is a simple yet effective way to keep your fuel oil system operating efficiently and reliably.
FASS Fuel Line: Unlocking the Power of Your Engine
You may want to see also
Line Insulation: Insulate the line to prevent heat loss and protect against freezing temperatures
Insulating the fuel oil line is a critical step in ensuring the efficient and safe operation of your heating system. Proper insulation serves two primary purposes: preventing heat loss and protecting the line from freezing temperatures. Here's a detailed guide on how to approach this task:
Understanding the Importance of Insulation:
The fuel oil line, often referred to as the oil supply line, carries heated oil from the tank to the burner. Without insulation, this line can lose heat to the surrounding environment, especially in colder climates. This heat loss reduces the overall efficiency of your heating system, as more fuel is required to maintain the desired temperature. Additionally, exposed lines are susceptible to freezing, which can lead to blockages, damage, and even system failures during winter.
Materials for Line Insulation:
- Fiberglass Insulation: This is a popular choice for fuel oil lines due to its effectiveness and ease of installation. Fiberglass insulation is lightweight, flexible, and can be easily wrapped around the line. It provides excellent thermal resistance, helping to retain heat and prevent heat loss.
- Mineral Wool Insulation: Another excellent option, mineral wool is fire-resistant and offers superior insulation properties. It is denser than fiberglass, providing better coverage and protection. Mineral wool insulation is available in various forms, including blankets and loose-fill, allowing for versatile installation.
- Insulated Pipe Wrap: Specialized pipe wraps are designed specifically for fuel oil lines. These wraps are typically made of a flexible material with an insulating layer, providing both thermal and physical protection. They are easy to apply and can be cut to fit the length of your line.
Insulation Installation Process:
- Prepare the Line: Ensure the fuel oil line is clean and free of any debris or old insulation. Remove any existing insulation carefully to avoid damaging the line.
- Measure and Cut Insulation: Determine the length of insulation needed, considering the exposed portion of the line. Cut the chosen insulation material to the appropriate size.
- Apply Insulation: Start wrapping the insulation around the line, ensuring complete coverage. Use a utility knife or a specialized insulation cutter to trim the insulation as you go. Secure the insulation in place with tape or a lightweight strap to prevent it from shifting.
- Cover End Connections: Pay special attention to the ends of the line, especially any valves or connections. Use additional insulation or insulated pipe sleeves to cover these areas, ensuring they are adequately protected.
- Secure and Finish: Finish the insulation by sealing any gaps or overlaps with tape or a suitable adhesive. Ensure the insulation is tight and secure, providing a continuous barrier around the line.
Additional Tips:
- Consider using a vapor barrier or a reflective insulation material on the inner side of the insulation to further prevent heat loss.
- In extremely cold climates, you might want to add an extra layer of insulation or use a more robust insulation material.
- Regularly inspect the insulated line for any signs of damage or wear, especially after harsh winters, and re-insulate if necessary.
By properly insulating your fuel oil line, you can improve the efficiency of your heating system, reduce fuel consumption, and ensure reliable operation during the coldest months. This simple yet effective measure is a valuable investment in the long-term performance and longevity of your home's heating infrastructure.
Understanding Hose Fuel Lines: A Comprehensive Guide
You may want to see also
Frequently asked questions
Fuel oil lines must meet specific standards to ensure safe and efficient fuel delivery. The primary requirements include using high-quality, compatible materials such as steel or copper, with a minimum wall thickness to withstand pressure and corrosion. The lines should be properly insulated to prevent heat loss and maintain the fuel's integrity. Additionally, all connections and fittings must be securely sealed to avoid leaks.
The size of the fuel oil line depends on various factors, including the fuel's flow rate, pressure, and temperature. It is crucial to consider the system's design and the specific requirements of the fuel oil pump and heater. A professional can calculate the required diameter based on these factors, ensuring optimal performance and minimizing energy losses.
Yes, there are industry standards and regulations that govern fuel oil line installations. These guidelines ensure safety and compliance with local codes. For example, the American Society of Mechanical Engineers (ASME) Boiler and Pressure Vessel Code provides standards for materials, design, and installation. It is essential to consult these codes and local regulations to ensure your fuel oil line setup meets all necessary requirements.
Regular maintenance is crucial to prevent issues with the fuel oil line. This includes inspecting the line for any signs of damage, corrosion, or leaks. Cleaning the line periodically to remove debris and contaminants is also recommended. Additionally, monitoring the fuel's quality and pressure can help identify potential problems early on. It is advised to consult a professional for maintenance tasks to ensure the line's longevity and safe operation.