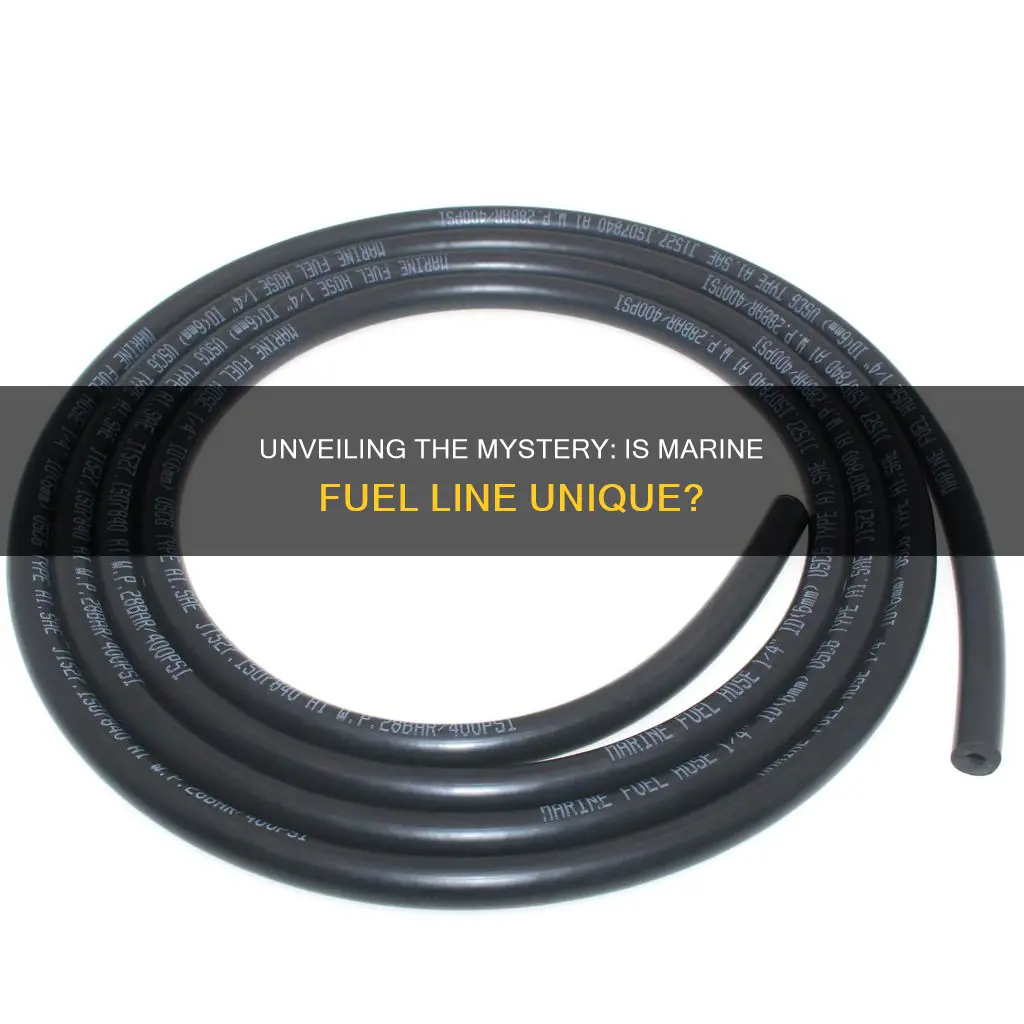
The world of marine fuel lines is a specialized and often overlooked aspect of the maritime industry. While the primary focus is on the engines and propulsion systems, the fuel lines play a crucial role in ensuring the safe and efficient operation of vessels. The question of whether marine fuel lines are different from those used in other industries is a valid one, as these lines are designed to withstand the unique challenges of marine environments. This paragraph aims to explore the distinct characteristics and considerations of marine fuel lines, shedding light on their importance and the specialized nature of their design.
What You'll Learn
- Composition: Marine fuel lines are made from materials resistant to saltwater corrosion and extreme temperatures
- Design: These lines often feature double-walled construction for safety and are designed to withstand dynamic sea conditions
- Pressure Rating: They are rated for higher pressure to handle fuel injection systems and varying engine demands
- Flexibility: Marine fuel lines are flexible to accommodate engine movement and provide a smooth flow of fuel
- Compatibility: Compatibility with different fuel types, such as diesel or gasoline, is a key consideration
Composition: Marine fuel lines are made from materials resistant to saltwater corrosion and extreme temperatures
Marine fuel lines are an essential component of any vessel's fuel system, and their design and composition are crucial to ensure optimal performance and longevity. These fuel lines are specifically engineered to withstand the harsh marine environment, which is characterized by saltwater exposure and extreme temperature fluctuations. The primary challenge in creating these lines is to develop materials that can resist the corrosive effects of saltwater while also maintaining flexibility and durability over a wide temperature range.
One of the key materials used in the construction of marine fuel lines is high-density polyethylene (HDPE). HDPE is a type of plastic that offers excellent resistance to saltwater corrosion. It has a low permeability to water, which means it can effectively prevent the intrusion of saltwater into the fuel system. This is particularly important because saltwater can cause rapid degradation of other materials, leading to cracks, leaks, and potential engine damage. HDPE's inherent resistance to corrosion ensures that the fuel lines remain intact and functional even in the most demanding marine conditions.
Additionally, the composition of marine fuel lines often includes additives that enhance their performance. These additives can include UV stabilizers, which protect the lines from the damaging effects of ultraviolet radiation, and antioxidants to prevent oxidation and degradation over time. The lines may also be reinforced with fibers, such as glass or Kevlar, to increase their strength and flexibility, ensuring they can withstand the stresses of fuel transfer and engine operation.
Furthermore, the design of these fuel lines takes into account the temperature variations experienced in marine environments. Materials are chosen for their ability to remain flexible in cold temperatures and resistant to brittleness in hot conditions. This ensures that the lines can withstand the expansion and contraction caused by temperature changes without compromising their structural integrity.
In summary, marine fuel lines are engineered with specialized materials that provide superior resistance to saltwater corrosion and extreme temperatures. The use of HDPE, along with carefully selected additives and reinforcements, ensures that these fuel lines can withstand the unique challenges of marine environments, providing reliable and safe fuel delivery to vessels' engines. This composition is a critical aspect of marine engineering, contributing to the overall performance and longevity of marine vehicles.
Fuel Line Sources for 2000 Mercury Mountaineer: Quick and Easy Access
You may want to see also
Design: These lines often feature double-walled construction for safety and are designed to withstand dynamic sea conditions
When it comes to marine fuel lines, the design plays a crucial role in ensuring safety and performance. One of the key features that sets these lines apart is their double-walled construction. This design element is a significant departure from standard fuel lines used in other applications, such as those found in automobiles or light vehicles.
The double-walled construction is a safety measure that provides an extra layer of protection. By having two walls, the fuel line can better withstand the pressures and forces encountered in the marine environment. This is particularly important when considering the dynamic nature of sea conditions. Waves, currents, and the overall movement of the vessel can exert significant stress on the fuel lines, and a double-walled design helps to mitigate these effects.
In addition to the double-walled structure, marine fuel lines are engineered to be highly durable. They are typically made from materials that can resist corrosion, abrasion, and the overall harshness of saltwater. This ensures that the fuel lines remain intact and functional even in the most challenging marine conditions. The design also incorporates flexible sections to accommodate the vessel's movement and provide a secure connection between the fuel tank and the engine.
Furthermore, the design of these fuel lines often includes specialized fittings and connectors. These components are designed to be robust and resistant to saltwater corrosion, ensuring a reliable and safe connection. The overall construction and design of marine fuel lines are tailored to meet the unique demands of the marine industry, providing a level of safety and performance that is essential for vessel operations.
In summary, the design of marine fuel lines is a critical aspect that sets them apart from standard fuel lines. The double-walled construction, combined with durable materials and specialized fittings, ensures safety and reliability in the demanding marine environment. This design approach is essential to maintaining the integrity of the fuel system and the overall performance of the vessel.
Boat Fuel Line Vent Hose: Size Guide for Optimal Performance
You may want to see also
Pressure Rating: They are rated for higher pressure to handle fuel injection systems and varying engine demands
When it comes to marine fuel lines, one of the key considerations is their pressure rating. These lines are specifically designed to handle the unique demands of marine engines, which often require higher pressure to operate efficiently and effectively. The pressure rating of a fuel line is a critical factor in ensuring the safe and reliable delivery of fuel to the engine.
Marine fuel injection systems are complex and require precise fuel delivery to optimize performance. The pressure rating of the fuel line is directly related to its ability to withstand the pressure generated by the fuel injection system. Higher pressure ratings are essential to accommodate the varying engine demands, such as acceleration, cruising, and idling. By being rated for higher pressure, the fuel line can ensure a consistent and controlled fuel flow, even in demanding operating conditions.
The pressure rating is typically measured in pounds per square inch (PSI) or bars, and it indicates the maximum pressure the fuel line can handle without compromising its structural integrity. Marine fuel lines are engineered to meet or exceed the pressure requirements specified by the engine manufacturer. This ensures that the fuel system operates within safe limits and reduces the risk of fuel leaks, engine damage, or performance issues.
In addition to handling higher pressure, marine fuel lines are also designed to resist corrosion and abrasion, which are common challenges in marine environments. The materials used in their construction, such as high-density polyethylene (HDPE) or specialized rubber compounds, provide excellent resistance to saltwater, UV radiation, and other corrosive elements. This ensures the longevity and reliability of the fuel line, even in harsh marine conditions.
By selecting fuel lines with an appropriate pressure rating, marine engine owners and operators can ensure optimal performance, fuel efficiency, and longevity of their engines. It is crucial to consult the manufacturer's specifications and guidelines to determine the correct pressure rating for a specific marine engine and fuel system setup. Properly rated fuel lines contribute to a well-functioning marine propulsion system, providing a seamless and efficient power source for vessels.
Ford Fuel Line Removal: A Step-by-Step Guide for 1990 Models
You may want to see also
Flexibility: Marine fuel lines are flexible to accommodate engine movement and provide a smooth flow of fuel
Marine fuel lines play a crucial role in the efficient and safe operation of vessels, and their flexibility is an essential aspect that sets them apart from other fuel lines. This unique characteristic is designed to address the specific challenges posed by the marine environment and the movement of the vessel itself.
The flexibility of marine fuel lines is a direct response to the fact that marine engines are often subjected to various types of motion. As the vessel moves through the water, the engine experiences vibrations, shocks, and changes in orientation. To ensure a consistent and uninterrupted supply of fuel, the fuel lines must be able to adapt to these movements without compromising the flow. This flexibility is achieved through the use of specialized materials and construction techniques.
One key factor contributing to flexibility is the choice of materials. Marine fuel lines are typically made from high-quality, durable polymers that possess inherent flexibility. These materials are carefully selected to withstand the harsh marine environment, including exposure to saltwater, UV radiation, and temperature fluctuations. The flexibility of the fuel lines allows them to bend and move with the engine, ensuring that the fuel remains in a consistent flow path.
Additionally, the design and construction of marine fuel lines incorporate features that enhance flexibility. This includes the use of flexible hoses with reinforced layers to provide strength and durability while maintaining a high degree of flexibility. The hoses are often constructed with multiple layers, including an inner layer that resists fuel permeation and an outer layer that provides protection against abrasion and environmental factors.
The flexibility of marine fuel lines is not just about accommodating engine movement but also about providing a smooth and consistent fuel flow. This is crucial for maintaining optimal engine performance and preventing issues such as fuel starvation or uneven combustion. By allowing the fuel lines to move with the engine, the risk of fuel accumulation or air bubbles is minimized, ensuring a clean and efficient fuel supply. This flexibility is a critical design consideration, especially in larger vessels where engine movement can be more pronounced.
Fixing a Leaky Fuel Line: A Step-by-Step Guide for 1993 Ford Rangers
You may want to see also
Compatibility: Compatibility with different fuel types, such as diesel or gasoline, is a key consideration
When it comes to marine fuel lines, compatibility with different fuel types is a critical aspect that cannot be overlooked. Marine environments often involve a variety of fuel sources, and ensuring the right fuel lines are used is essential for optimal performance and safety. The primary consideration here is the chemical composition and properties of the fuel being used. Diesel and gasoline, for instance, have distinct characteristics that require specific fuel lines to handle their unique challenges.
Diesel fuel is known for its higher energy content and thicker consistency compared to gasoline. This thicker nature can lead to increased pressure and potential issues if the fuel lines are not designed to accommodate this. Therefore, marine fuel lines for diesel engines need to be robust and capable of withstanding the higher pressure and thicker fuel flow. The materials used in these lines should be resistant to the corrosive effects of diesel, ensuring longevity and reliability.
On the other hand, gasoline fuel lines require a different set of considerations. Gasoline is generally less viscous and has a lower flash point compared to diesel. This means that gasoline fuel lines need to be more flexible to accommodate the varying fuel flow rates and temperatures. Additionally, gasoline fuel lines should be designed to prevent fuel evaporation and ensure a tight seal to avoid any leaks, which could be dangerous in a marine setting.
The compatibility of fuel lines with different fuels is not just about the physical properties but also the chemical compatibility. Marine fuel lines should be made from materials that are resistant to the chemicals present in both diesel and gasoline. This ensures that the fuel lines do not degrade over time, leading to potential performance issues or even failures. For instance, certain types of rubber or synthetic materials might not be suitable for long-term exposure to gasoline due to its solvent properties.
In summary, when selecting marine fuel lines, it is crucial to consider the specific fuel types in use. Each fuel type presents unique challenges, and the fuel lines must be designed to handle these challenges effectively. By ensuring compatibility with different fuels, marine operators can maintain optimal performance, safety, and the overall longevity of their fuel systems. This consideration is a fundamental part of the overall design and maintenance strategy for any marine vessel or engine.
Camaro Fuel Line: The Perfect Diameter for Power and Performance
You may want to see also
Frequently asked questions
No, marine fuel lines are specifically designed for the unique demands of marine environments. They are typically made from materials that are more resistant to saltwater corrosion, UV radiation, and temperature fluctuations, ensuring durability and longevity in harsh marine conditions.
Marine fuel lines are engineered to handle the higher pressure and temperature variations often encountered in marine applications. They are also designed to be more flexible to accommodate the movement of a vessel, and they may have different sizing and material specifications to meet the specific requirements of marine engines.
While it is technically possible to use regular fuel lines in a marine environment, it is not recommended due to the potential risks. Regular fuel lines may not withstand the corrosive effects of saltwater and the extreme conditions of marine use, leading to premature failure and potential safety hazards.
Yes, marine fuel lines often utilize materials like stainless steel, brass, or specialized polymers that are resistant to corrosion and degradation. These materials ensure the fuel lines can withstand the harsh marine environment and provide reliable performance over extended periods.