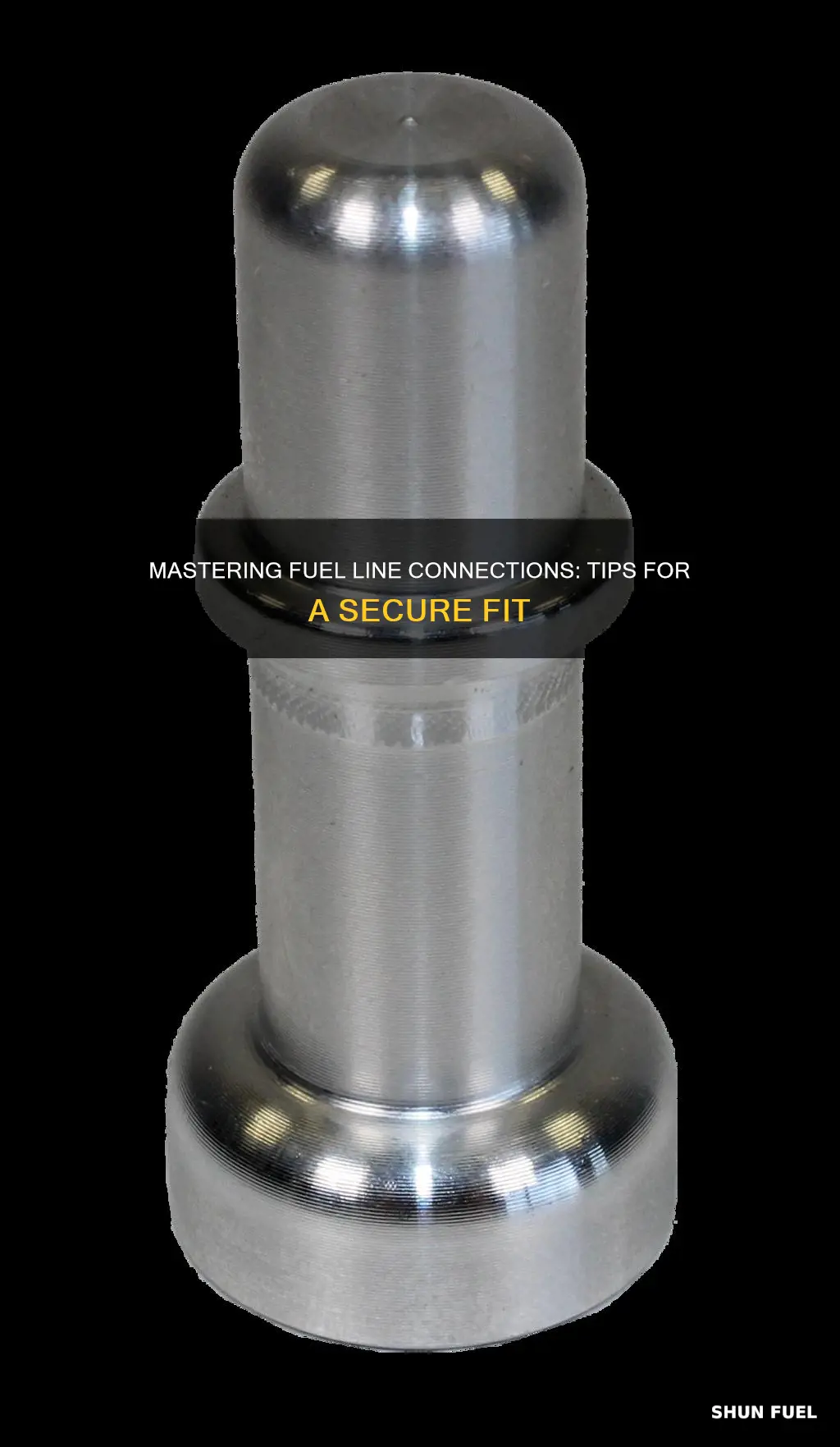
When it comes to plugging a fuel line, there are several methods to consider, each with its own set of advantages and disadvantages. The best approach will depend on the specific situation and the type of fuel line in question. Some common methods include using a fuel line plug, a fuel line clamp, or a fuel line repair kit. Each method has its own set of benefits, such as ease of use, durability, and cost, so it's important to choose the right one for the job. In this paragraph, we will explore these methods in detail, providing a comprehensive guide to help you make an informed decision.
What You'll Learn
- Fuel Line Material: Choose the right material for your fuel line, considering factors like temperature resistance and flexibility
- Fuel Line Routing: Route the fuel line away from heat sources and sharp bends to prevent damage
- Fuel Line Clamps: Use secure, vibration-resistant clamps to fasten the fuel line to the vehicle
- Fuel Line Inspection: Regularly inspect the fuel line for cracks, leaks, and damage
- Fuel Line Disconnect: Learn proper techniques for safely disconnecting and reconnecting fuel lines
Fuel Line Material: Choose the right material for your fuel line, considering factors like temperature resistance and flexibility
When it comes to selecting the appropriate material for your fuel line, several key factors come into play, primarily temperature resistance and flexibility. These characteristics are essential to ensure the fuel line's longevity and performance in various automotive applications.
Temperature resistance is a critical consideration as fuel lines are exposed to varying temperatures, especially in engines. The material must withstand extreme heat without degrading or becoming brittle. For this reason, rubber and synthetic rubber compounds are popular choices. Natural rubber, for instance, offers excellent flexibility and resilience, making it ideal for fuel lines that need to bend and move with the engine's components. However, it's important to note that natural rubber may not be suitable for high-temperature environments, so additional materials or coatings might be required.
Flexibility is another vital aspect, as fuel lines need to accommodate engine movement and vibrations without cracking or breaking. Materials like nylon, polyester, and braided steel are known for their flexibility and ability to withstand repeated bending. Nylon, in particular, is a popular choice due to its lightweight nature and resistance to fuel-related chemicals, making it a durable and reliable option. Braided steel, on the other hand, provides exceptional flexibility and is often used in high-performance applications where extreme flexibility is required.
In addition to temperature and flexibility, the material's compatibility with the fuel type is essential. Different fuels have varying chemical compositions, and the fuel line material should not react with or absorb these chemicals over time. For example, ethanol-blended fuels may require materials that are more resistant to ethanol's corrosive properties.
Lastly, consider the overall design and installation process. Some materials might be easier to work with during the installation process, ensuring a secure and leak-free connection. It's important to choose a material that complements the fuel line's design and allows for a smooth, efficient installation.
Unraveling the Mystery: Why Motorcycles Pop Pinholes in Fuel Lines
You may want to see also
Fuel Line Routing: Route the fuel line away from heat sources and sharp bends to prevent damage
When it comes to fuel line routing, one of the most critical aspects is ensuring the line is protected from potential sources of damage. Heat sources and sharp bends are two common areas of concern that can lead to fuel line issues. Here's a detailed guide on how to route the fuel line to prevent these problems:
Avoid Heat Sources:
Fuel lines should be kept away from any heat sources, such as exhaust systems, engine components, or even hot surfaces in the vehicle's interior. High temperatures can cause the fuel line to expand and contract, leading to potential cracks or leaks. A safe distance is recommended, typically at least a few inches, to ensure the fuel line remains flexible and intact. Consider the placement of the fuel tank and the engine's heat distribution when planning the route. For example, if the fuel tank is located near the engine, ensure the fuel line is routed away from the exhaust manifold and other hot engine components.
Minimize Sharp Bends:
Sharp bends in the fuel line can create stress points, making the line more susceptible to damage over time. It is essential to route the line in a way that minimizes these bends. Aim for gentle curves and avoid sharp angles. One effective technique is to use a 'S' or 'U' shape when routing the line, allowing it to bend gradually. This approach helps distribute the load evenly and reduces the risk of kinking or cracking. Additionally, ensure that any necessary bends are supported by brackets or clips to maintain the line's shape and prevent excessive movement.
Consider the Vehicle's Structure:
The vehicle's structure and available space should be taken into account when routing the fuel line. Look for areas where the line can be tucked away, protected by other components or the vehicle's body. For instance, in some vehicles, the fuel line can be routed behind the firewall, away from the engine's direct heat and movement. Utilize the vehicle's design to your advantage, ensuring the line is not only protected but also easily accessible for maintenance and inspections.
Use Appropriate Materials:
When routing the fuel line, consider using materials that can withstand the environmental conditions and potential hazards. For example, rubber or silicone-coated fuel lines are more flexible and resistant to heat compared to standard rubber. These materials can help absorb expansion and contraction without compromising the line's integrity. Additionally, ensure that any connectors or fittings used are compatible with the fuel line material to prevent leaks or damage.
By following these guidelines, you can effectively route the fuel line, ensuring it is away from heat sources and sharp bends, thus minimizing the risk of damage and potential fuel leaks. Proper routing is a crucial step in maintaining a reliable and safe fuel system in your vehicle.
Understanding Snowmobile Fuel Lines: Inside the Gas Tank
You may want to see also
Fuel Line Clamps: Use secure, vibration-resistant clamps to fasten the fuel line to the vehicle
When it comes to ensuring a secure and reliable fuel line connection, using the right type of clamp is crucial. Fuel lines are susceptible to damage from vibrations, especially in high-performance vehicles or those with rough terrain. Therefore, investing in vibration-resistant clamps is essential to maintain a tight and safe seal. These specialized clamps are designed to withstand the rigors of the automotive environment, providing an extra layer of protection against potential fuel leaks.
The process of installing these clamps is straightforward and can be done by following a few simple steps. First, ensure that the fuel line is clean and free of any debris or contaminants. This is important to guarantee a proper connection. Then, locate the fuel line and identify the point where it needs to be clamped. Carefully slide the clamp over the fuel line, ensuring it covers the entire length of the line where it connects to the vehicle. The clamp should be positioned securely, providing a snug fit without causing any damage to the line.
Vibration-resistant clamps typically feature a robust design with a sturdy metal or durable plastic construction. They often include a rubber or soft material insert to provide a secure grip on the fuel line while minimizing the risk of damage. This design ensures that the clamp remains in place even during sudden stops, sharp turns, or high-speed driving, thus preventing potential fuel leaks and maintaining the vehicle's performance.
It is recommended to use multiple clamps along the length of the fuel line, especially in areas prone to vibration or movement. This additional security measure helps to reinforce the connection and further reduces the chances of fuel line failure. By following this practice, you can ensure that the fuel line remains intact and secure, even under the most demanding driving conditions.
In summary, using secure and vibration-resistant clamps is a critical step in maintaining a reliable fuel system. These clamps provide the necessary protection against vibrations and potential leaks, ensuring the vehicle's performance and safety. With proper installation and regular maintenance, fuel line clamps can significantly contribute to a trouble-free driving experience.
Unraveling the Mystery: Understanding Fuel Pump Line Requirements
You may want to see also
Fuel Line Inspection: Regularly inspect the fuel line for cracks, leaks, and damage
Fuel lines are a critical component of any vehicle's fuel system, and regular inspection is essential to ensure optimal performance and prevent potential issues. Over time, fuel lines can develop cracks, leaks, or other forms of damage, which can lead to fuel leaks, reduced engine performance, and even potential safety hazards. Therefore, it is crucial to establish a routine inspection process to identify and address these issues promptly.
During an inspection, look for any visible signs of deterioration or damage. Cracks, small holes, or splits in the fuel line material are common indicators of wear and tear. These defects can occur due to age, exposure to heat or cold temperatures, or even minor collisions. Inspect the fuel line for any signs of corrosion or rust, especially if the vehicle is stored outdoors or in a humid environment. Corrosion can weaken the fuel line's integrity and lead to leaks.
Pay close attention to the connections and fittings of the fuel line. Over time, these connections can loosen or become damaged, leading to potential fuel leaks. Check for any signs of corrosion or damage around the fittings and ensure they are securely tightened. It is also a good practice to lubricate the fittings with a suitable fuel line compound to ensure a tight seal and prevent leaks.
Regularly inspect the fuel line's routing for any obstructions or damage. The fuel line should be routed away from hot surfaces, sharp edges, and areas prone to vibration or impact. Inspect the line for any kinks or bends that might restrict fuel flow or cause damage over time. Ensure that the fuel line is not pinched or compressed, as this can lead to reduced fuel pressure and engine performance issues.
In addition to visual inspections, it is beneficial to use specialized tools and techniques to identify potential issues. A fuel pressure gauge can help measure the fuel pressure in the system, allowing you to detect leaks or blockages. Visual inspection, combined with these diagnostic tools, provides a comprehensive assessment of the fuel line's condition. Remember, early detection of cracks, leaks, or damage is crucial to maintaining a reliable fuel system and ensuring the longevity of your vehicle.
Fuel Line Faults: Common Issues and Solutions
You may want to see also
Fuel Line Disconnect: Learn proper techniques for safely disconnecting and reconnecting fuel lines
When it comes to working with fuel lines, ensuring a safe and proper disconnection is crucial to avoid any potential hazards. Here's a guide on how to safely disconnect and reconnect fuel lines:
Preparation and Safety Measures: Before attempting any fuel line work, it is essential to prioritize safety. Ensure you are working in a well-ventilated area, preferably outdoors, to minimize the risk of fuel vapor inhalation. Wear appropriate personal protective equipment (PPE), including gloves, safety goggles, and a respirator mask. Familiarize yourself with the location of the fuel tank, fuel lines, and any related components to ensure you have a clear understanding of the system.
Disconnecting the Fuel Line: To disconnect a fuel line, start by locating the specific line you need to remove. Fuel lines are typically made of rubber or flexible materials and are connected to the fuel tank and various engine components. Use a fuel line disconnect tool, often a specialized pliers-like tool, to grip the fuel line securely. Apply firm pressure and twist counterclockwise to loosen the connection. Be cautious not to overtighten, as this can damage the fuel line. Once the connection is loose, carefully pull the fuel line away from the connection point, ensuring you don't kink or damage the line.
Reconnecting the Fuel Line: When reconnecting a fuel line, ensure you have the correct size and type of fuel line for your application. Align the fuel line with the connection port, ensuring it is the right orientation. Secure the fuel line using the disconnect tool again, tightening the connection by turning it clockwise. Apply firm pressure to ensure a snug fit. Check for any leaks by gently pressing on the connection and observing for any fuel seepage. If no leaks are detected, you've successfully reconnected the fuel line.
Important Considerations: It is crucial to follow manufacturer guidelines and recommendations for your specific vehicle or equipment. Different fuel systems may have unique requirements, so always refer to the appropriate manuals. Additionally, when working with fuel, it's essential to be mindful of potential hazards. Fuel is flammable and can pose health risks if inhaled. Always exercise caution, and if you are unsure, consult a professional mechanic.
By following these steps and maintaining a cautious approach, you can safely disconnect and reconnect fuel lines, ensuring the proper functioning of your vehicle's fuel system. Remember, safety should always be the top priority when working with fuel-related components.
Outboard Fuel Confusion: Diesel or Gasoline? Unraveling the Mystery
You may want to see also
Frequently asked questions
A temporary plug can be created using a piece of rubber hose or a rubber fuel line. Simply cut the hose to the appropriate length, slide it over the fuel line, and secure it with a hose clamp. This will prevent fuel from leaking while you work on the engine.
While a regular hose clamp can be used, it's not the most secure or reliable method. Fuel lines are under pressure, and a standard hose clamp might not provide a tight seal. It's recommended to use a fuel line plug or a specialized hose clamp designed for fuel lines to ensure a proper seal.
For a permanent plug, it's best to use a fuel line plug or a fitting specifically designed for fuel lines. These plugs are typically made of durable materials like rubber or plastic and are designed to withstand fuel pressure. You can cut the fuel line to the desired length, insert the plug, and ensure a secure connection using the appropriate tools.
Absolutely. Working with fuel lines requires caution. Always ensure the engine is off and the fuel supply is disconnected before making any modifications. Wear protective gear, such as gloves and safety goggles, to prevent any potential spills or splashes. It's also a good practice to drain the fuel tank if you're making significant changes to the fuel system.