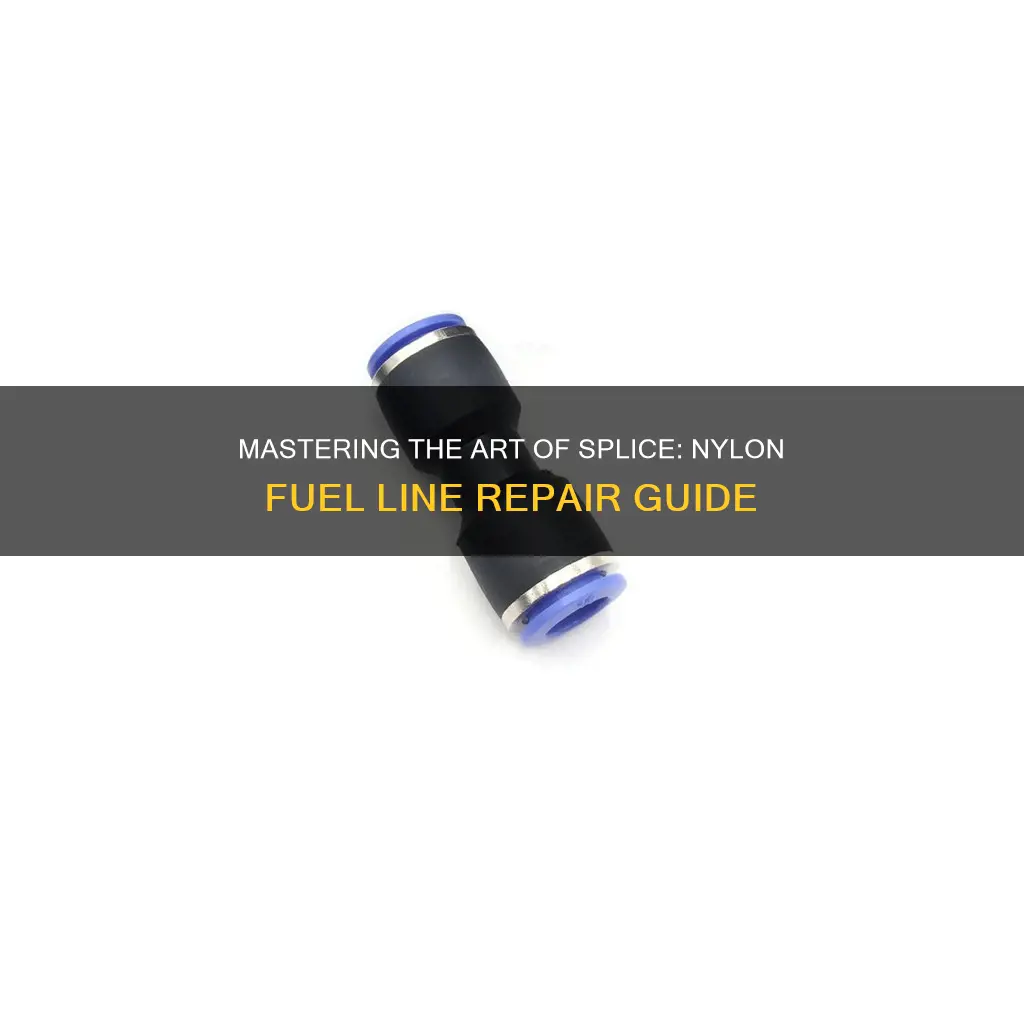
Splicing a nylon fuel line is a crucial skill for anyone working on vehicles or machinery that relies on fuel. This process involves joining two damaged or torn sections of the fuel line to ensure a continuous and secure flow of fuel. By following a few simple steps, you can effectively splice the nylon fuel line, restoring its integrity and preventing potential fuel leaks. This guide will provide a step-by-step approach to help you master the art of splicing, ensuring your vehicle's fuel system remains reliable and efficient.
What You'll Learn
- Preparation: Gather tools and materials, ensure a clean workspace, and wear protective gear
- Cutting: Use a sharp blade to cut the line, measure accurately, and make a clean cut
- Clamping: Secure the ends with clamps, apply heat shrink, and ensure a tight seal
- Splicing: Strip insulation, align lines, and use a splice kit for a strong bond
- Testing: Inspect the splice, perform pressure tests, and ensure no leaks
Preparation: Gather tools and materials, ensure a clean workspace, and wear protective gear
Before you begin the process of splicing a nylon fuel line, it's crucial to prepare and ensure you have everything you need to complete the task safely and effectively. Here's a detailed guide on the preparation steps:
Gather the Necessary Tools and Materials: Start by collecting all the required tools and supplies. For splicing a nylon fuel line, you will typically need a pair of sharp scissors or a specialized fuel line cutter, a length of replacement nylon fuel line that matches the original, a fuel line clamp or a suitable adhesive, and some cleaning supplies. Ensure you have the right sizes and lengths to fit your specific application. Having all these items ready will streamline the splicing process and prevent any unnecessary delays.
Create a Clean and Organized Workspace: Set up your work area in a well-ventilated area, preferably outdoors or in a well-ventilated garage. Cleanliness is essential to avoid any contamination that could affect the splice's quality. Clear any clutter and ensure there are no potential hazards nearby. A tidy workspace will also make it easier to access the necessary tools and materials when you need them.
Protective Gear: Safety should always be a priority. Before you begin, put on appropriate personal protective equipment (PPE). This includes safety goggles to protect your eyes from any potential splashes or debris, and gloves to safeguard your hands. Consider wearing a dust mask if there might be any dust or debris in the air during the splicing process. Taking these precautions will help prevent injuries and ensure a safe working environment.
Additionally, make sure you have a steady hand and a good understanding of the task at hand. Take your time to read through the entire process and gather all the necessary information before you start. This preparation will contribute to a more efficient and successful splicing of the nylon fuel line.
Mastering Ford Fuel Line Connector Removal: A Step-by-Step Guide
You may want to see also
Cutting: Use a sharp blade to cut the line, measure accurately, and make a clean cut
When splicing a nylon fuel line, precision and care are essential to ensure a secure and reliable connection. Here's a step-by-step guide focusing on the cutting process:
Prepare Your Tools and Materials: Before you begin, gather the necessary tools and materials. You'll need a sharp blade, preferably a utility knife or a dedicated fuel line cutter. Ensure the blade is in good condition to make clean cuts. Additionally, have a measuring tape or ruler ready for accurate measurements.
Measure and Mark: Accurate measurement is crucial. Carefully measure the length of the nylon fuel line you need to splice. Mark this length on the line itself using a permanent marker or a piece of tape. This step ensures you cut the exact amount required, preventing wastage and potential issues with the splice.
Position the Blade: Hold the nylon fuel line firmly with one hand, ensuring it is taut and straight. Position the sharp blade at the marked cut point. A clean cut is essential to avoid damaging the line's internal structure. Apply gentle pressure to guide the blade through the line, making a straight and precise cut.
Make the Cut: With steady hands, guide the blade along the marked line, cutting through the nylon fuel line. A sharp blade will make a clean, smooth cut, minimizing the risk of fraying or damaging the line. Take your time and apply consistent pressure to achieve the best results.
Final Inspection: After cutting, inspect the edges of the line. Ensure they are smooth and free from any debris or damage. If necessary, use a file or sandpaper to gently smooth the cut edges, creating a clean and professional finish. This attention to detail will contribute to a strong and reliable splice.
Fuel Lines for 2005 Yukon: Expert Sources Revealed
You may want to see also
Clamping: Secure the ends with clamps, apply heat shrink, and ensure a tight seal
When splicing a nylon fuel line, clamping is a crucial step to ensure a secure and reliable connection. Here's a detailed guide on how to achieve a tight seal:
Start by preparing the ends of the fuel line. Cut the line to the desired length, ensuring a clean and precise cut. Remove any excess material or debris from the cut ends. This step is essential to create a smooth surface for the clamp to grip.
Next, select the appropriate clamp for your application. Nylon fuel lines often use specialized clamps designed for fuel-resistant materials. These clamps typically feature a sturdy construction with a tight grip. Ensure the clamp is the right size to accommodate the fuel line's diameter.
Now, it's time to secure the ends. Place the clamp over one end of the fuel line, positioning it so that the clamp's opening aligns with the cut end. Gently but firmly tighten the clamp by hand. This initial tightening ensures a good initial grip. For an even more secure connection, consider using a tool to tighten the clamp further, but be careful not to overtighten, as it may damage the fuel line.
After clamping, inspect the connection. Ensure the clamp is snug and there are no gaps or loose areas. A tight seal is crucial to prevent any potential leaks. If the clamp feels loose, carefully adjust it and tighten it again.
Finally, consider applying heat shrink tubing over the clamped area. Heat shrink provides an additional layer of protection and insulation. Slide the heat shrink onto the fuel line, ensuring it covers the entire clamped section. Then, apply heat using a heat gun or a similar tool, following the manufacturer's instructions for the specific heat shrink material. The heat will cause the shrink tubing to contract, creating a tight, sealed connection. This step is especially useful in high-temperature environments or when exposed to direct sunlight.
By following these clamping techniques, you can ensure a secure and reliable splice for your nylon fuel line, minimizing the risk of leaks and ensuring optimal performance.
Mastering Fuel Line Replacement: A Guide to Poulan PP4218AVX Pro
You may want to see also
Splicing: Strip insulation, align lines, and use a splice kit for a strong bond
Splicing a nylon fuel line is a process that requires careful attention to detail to ensure a strong and reliable connection. Here's a step-by-step guide to help you through the process:
Step 1: Prepare the Materials
Before you begin, gather all the necessary tools and materials. You'll need a splice kit specifically designed for nylon fuel lines, which typically includes a splice sleeve, a ferrule, and a crimping tool. Ensure you have the correct size of the splice kit for your fuel line diameter. Additionally, have a sharp utility knife or a dedicated insulation stripper for removing the protective covering.
Step 2: Strip Insulation
Locate the damaged or worn-out section of the nylon fuel line where you plan to make the splice. Carefully strip the insulation from both the primary and secondary lines. Start by cutting the insulation with the utility knife, ensuring you remove enough material to expose the nylon fibers but not damage the inner strength members. Take your time with this step to avoid any mistakes.
Step 3: Align the Lines
With the insulation removed, carefully align the primary and secondary fuel lines. Ensure they are in perfect alignment, with the fibers running parallel to each other. Any misalignment can lead to a weak bond and potential failure of the splice. Use a straight edge or a ruler to verify the alignment.
Step 4: Insert the Splice Sleeve
Take the splice sleeve from your kit and carefully slide it over the aligned sections of the fuel lines. Ensure the sleeve is positioned correctly, with the opening facing the correct direction. The sleeve should be snugly fitted around the lines, providing a secure base for the splice.
Step 5: Apply the Ferrule
Next, insert the ferrule from the splice kit onto the splice sleeve. The ferrule will create a mechanical and chemical bond with the nylon fuel line. Ensure the ferrule is fully seated onto the sleeve and that there are no gaps or misalignments.
Step 6: Crimp and Bond
Using the crimping tool provided in the kit, apply the specified amount of force to the ferrule. Follow the manufacturer's instructions for the correct crimping technique. This process will create a secure bond between the ferrule and the fuel line. Repeat the crimping process for any additional ferrules required for the splice.
Step 7: Test and Inspect
Once the splicing process is complete, thoroughly inspect the splice to ensure there are no visible gaps or imperfections. Test the splice by applying pressure and checking for any leaks. If everything is secure, your splice should now be ready for use, providing a strong and reliable connection for your fuel line.
Carburetor Fuel Line Connection: Unlocking Engine Power
You may want to see also
Testing: Inspect the splice, perform pressure tests, and ensure no leaks
Once you've carefully spliced the nylon fuel line, it's crucial to thoroughly test the connection to ensure its integrity and prevent any potential leaks. Here's a step-by-step guide to the testing process:
Inspection: Begin by visually inspecting the splice. Check for any visible signs of damage, such as cracks, tears, or debris caught between the splice and the original line. Ensure that the splice is smooth and free of any sharp edges that could cause damage to the fuel system. Pay close attention to the connection area, making sure that the splice is properly aligned and securely attached.
Pressure Testing: This is a critical step to verify the splice's effectiveness. You can use a simple pressure test by attaching a pressure gauge to the fuel line, ensuring it is connected to the splice. Gradually increase the pressure in the system and monitor the gauge. The pressure should hold steady without any drops, indicating a successful splice. If you notice any pressure loss, it suggests a potential leak or an improperly executed splice.
Leak Detection: After the pressure test, perform a leak detection procedure. This can be done by applying a small amount of soapy water or a specialized fuel line sealant around the splice area. Observe the fuel line for any bubbles or foam, which would indicate a leak. Alternatively, you can use a smoke machine to detect leaks by introducing a small amount of smoke into the fuel system and observing if any smoke escapes from the splice area.
Final Inspection: Finally, inspect the splice once more to ensure all connections are secure and free from any contaminants. Make sure that the splice is not kinked or twisted, as this could compromise its integrity over time. If everything appears satisfactory, your splice is ready for use, and you can proceed with fueling your vehicle or equipment.
Remember, proper testing is essential to guarantee the safety and reliability of your fuel system. By following these steps, you can confidently rely on your spliced nylon fuel line, knowing that it has been thoroughly evaluated for performance and leak prevention.
Stock Fuel Line Dimensions for Honda Civic EK
You may want to see also
Frequently asked questions
Splicing a nylon fuel line is a crucial repair technique used to reconnect a damaged or torn section of the line, ensuring the fuel delivery system remains intact and functional.
Before splicing, clean the line thoroughly to remove any dirt, debris, or old adhesive. Ensure the line is dry and free of contaminants. Then, cut the line to the desired length, allowing for a few extra inches on each side for the splice.
You will need a nylon fuel line splice kit, which typically includes a splice sleeve, adhesive, and a heat source (such as a heat gun or iron). Additionally, have a pair of sharp scissors or a knife for cutting the line.
No, it is not recommended to use standard adhesive tape for splicing nylon fuel lines. Specialized splice kits are designed to provide a strong and durable bond specifically for nylon materials, ensuring the line's integrity.
Start by inserting the splice sleeve over the damaged section of the line. Ensure it is centered and aligned properly. Apply the adhesive according to the kit's instructions, heating the splice area to facilitate bonding. Allow the splice to cool and cure as per the manufacturer's guidelines before reinstalling the line.