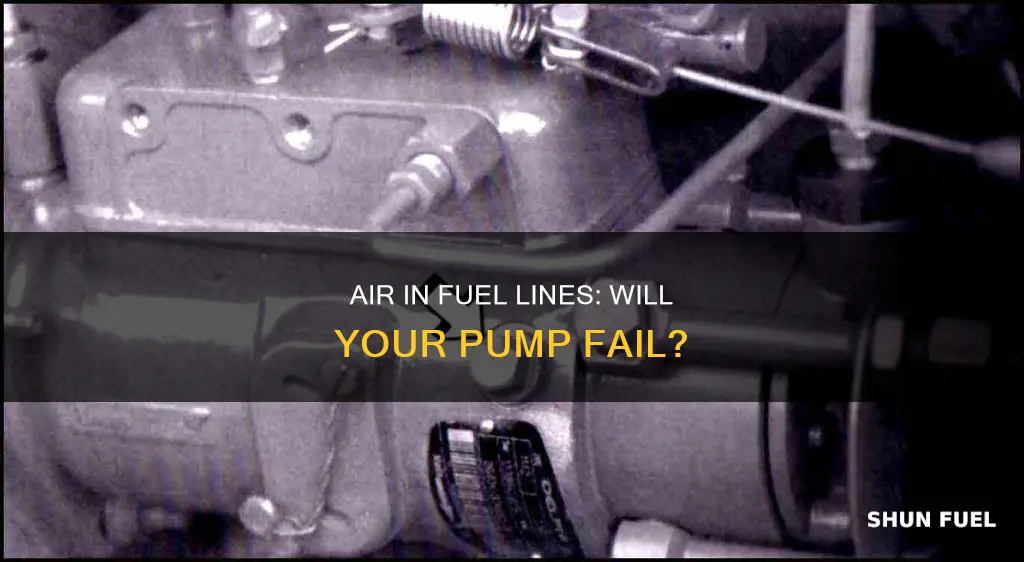
Fuel pumps are essential components in vehicle engines, responsible for delivering fuel from the tank to the engine. However, they can encounter issues if air enters the fuel lines. When air is present in the fuel lines, it can cause the fuel pump to stop working, leading to a lack of fuel supply to the engine. This problem often arises due to issues with the fuel tank or fuel system, such as a damaged fuel filter or a cracked fuel line. Understanding the causes and effects of air in the fuel lines is crucial for maintaining a vehicle's performance and preventing potential breakdowns.
Characteristics | Values |
---|---|
Fuel Pump Operation | Air in the fuel lines can cause the fuel pump to stop working. This is because air bubbles can restrict the flow of fuel, leading to a lack of pressure and power to the engine. |
Engine Performance | When the fuel pump fails due to air, the engine may stall or have reduced performance. This is a common issue in vehicles with fuel injection systems. |
Symptoms | Symptoms include difficulty starting the engine, poor acceleration, and reduced power. In some cases, the engine may not start at all. |
Causes | Air in the fuel lines can be caused by various factors such as a faulty fuel filter, a leaking fuel tank, or a problem with the fuel pump itself. |
Solution | To fix this issue, one should bleed the fuel lines to remove air bubbles. This can often be done by running the engine and then turning it off while the fuel is still running. |
What You'll Learn
- Air in Fuel Lines: Air bubbles can cause fuel pump issues, leading to engine problems
- Pump Sensitivity: Fuel pumps are sensitive to air, which can disrupt their operation
- Air Lock: Air locks in the fuel system can cause the pump to fail
- Pressure Drop: Air reduces fuel pressure, potentially causing the pump to stop
- Maintenance: Regular checks can prevent air-related pump failures
Air in Fuel Lines: Air bubbles can cause fuel pump issues, leading to engine problems
The presence of air bubbles in fuel lines can indeed lead to significant engine problems, and it's a common issue that many vehicle owners face. When air enters the fuel system, it can cause a range of symptoms, from poor engine performance to complete engine failure. This phenomenon is often referred to as 'airlock' or 'air in the fuel.'
The primary reason for this problem is the air's inability to mix properly with the fuel. Fuel pumps are designed to deliver a precise mixture of fuel and air to the engine's combustion chambers. However, when air bubbles are introduced into the fuel lines, they can disrupt this delicate balance. As a result, the engine may not receive the correct amount of fuel, leading to a condition known as 'fuel starvation.' This can cause the engine to misfire, stall, or even shut down completely, especially during acceleration or when the engine is under load.
One of the most common ways air bubbles can enter the fuel system is through the fuel tank. Over time, small amounts of air can accumulate in the tank, especially if the fuel level is low or the tank is not sealed properly. When the engine is started, this air can be drawn into the fuel lines, causing the aforementioned issues. Additionally, if the fuel pump is located in the tank, it can draw in air if the pump is not functioning correctly or if there is a blockage in the line.
To address this problem, it is essential to ensure that the fuel system is free of air bubbles. One method is to bleed the fuel lines by starting the engine and then turning it off while the fuel pump is running. This allows the air to be pushed out of the system. Another solution is to use a fuel system cleaner, which can help remove any existing air bubbles and prevent new ones from forming. Regular maintenance, such as checking the fuel tank for leaks and ensuring the fuel pump is functioning correctly, can also help prevent air-related issues.
In summary, air bubbles in fuel lines can cause significant engine problems due to the disruption of the fuel-air mixture. By understanding the causes and implementing preventive measures, vehicle owners can avoid costly repairs and ensure their engines run smoothly. It is always advisable to consult a professional mechanic if you suspect any issues with your fuel system to ensure proper diagnosis and resolution.
The Ultimate Guide to Choosing Lubricant for Rubber Fuel Lines
You may want to see also
Pump Sensitivity: Fuel pumps are sensitive to air, which can disrupt their operation
Fuel pumps are intricate components of an engine's fuel system, and their sensitivity to air is a critical aspect of their functionality. When air enters the fuel lines, it can have detrimental effects on the pump's performance and overall engine operation. This issue is often overlooked but can lead to significant problems.
The primary concern with air in the fuel lines is its impact on the pump's ability to deliver fuel efficiently. Fuel pumps are designed to operate under specific conditions, and the presence of air can disrupt this delicate balance. As air bubbles enter the pump, they can cause a decrease in pressure, leading to an inconsistent fuel flow. This inconsistency may result in a reduced fuel supply to the engine, causing it to run poorly or even stall.
One of the key reasons for this sensitivity is the pump's design. Fuel pumps are typically small and compact, with intricate internal mechanisms. These mechanisms are finely tuned to handle the pressure and flow rate of fuel. When air is introduced, it can interfere with the pump's ability to maintain a consistent pressure, leading to erratic behavior. Over time, this can cause wear and tear on the pump's components, reducing its overall lifespan.
To address this issue, it is essential to ensure that the fuel system is free from air bubbles. One common method is to use a fuel filter that can trap air and other contaminants. Regular maintenance, including checking and replacing filters, is crucial. Additionally, keeping the fuel tank full can help prevent air from entering the system, as it leaves less room for air bubbles to form.
In summary, fuel pumps' sensitivity to air is a critical factor in their operation. Air bubbles in the fuel lines can disrupt the pump's performance, leading to engine issues. Understanding and addressing this sensitivity through proper maintenance and design considerations are essential to ensure the longevity and efficient operation of the fuel pump system.
Nylon Fuel Line Cleaning: Effective Methods and Tools
You may want to see also
Air Lock: Air locks in the fuel system can cause the pump to fail
Air locks are a common issue that can occur in fuel systems, and they can indeed lead to the failure of the fuel pump. This problem is often overlooked but can be a significant cause of pump malfunction. When air enters the fuel lines, it creates a bubble or lock of air that can restrict the flow of fuel, leading to various performance issues.
The primary reason air locks are problematic is that they disrupt the pressure required to pump fuel efficiently. Fuel pumps rely on a consistent and sufficient pressure to deliver fuel to the engine. When air is introduced into the system, it reduces the overall pressure, making it challenging for the pump to function optimally. As a result, the engine may experience reduced power, poor performance, or even stall.
Identifying an air lock can be done through several signs. One common indicator is a sudden drop in engine performance, such as hesitation, stalling, or a loss of power during acceleration. If you notice these symptoms, it's essential to inspect the fuel system for any signs of air bubbles. You might also hear a distinctive 'squealing' or 'whooshing' sound coming from the fuel tank or lines, which could be an indication of air movement.
To address this issue, the first step is to locate the air bleeder valve, typically found near the fuel pump or in the fuel tank. This valve allows you to release any trapped air from the system. By opening the bleeder valve, you can expel the air lock, restoring the proper pressure and allowing the fuel pump to function correctly. It is recommended to consult the vehicle's manual to locate the specific bleeder valve for your make and model.
Regular maintenance and inspections can help prevent air locks. Ensuring that the fuel system is clean and free of debris is crucial. Over time, dirt, rust, or other contaminants can accumulate, increasing the likelihood of air bubbles. Therefore, keeping the fuel system in good condition and regularly checking for any signs of air locks can help avoid unexpected pump failures.
Rubber Hose Fuel Line Lubrication: Essential Tips for Smooth Operation
You may want to see also
Pressure Drop: Air reduces fuel pressure, potentially causing the pump to stop
The presence of air in the fuel lines can have a significant impact on the performance of a fuel pump, potentially leading to a complete cessation of its operation. This phenomenon is primarily attributed to the pressure drop that occurs when air is introduced into the fuel system. When air enters the fuel lines, it creates a less dense medium compared to the fuel, resulting in a decrease in overall system pressure. This pressure drop is particularly critical for fuel pumps, as they rely on a consistent and sufficient pressure to deliver fuel to the engine.
As the fuel pump operates, it draws fuel from the tank and pushes it through the lines to the engine. However, when air is present, the pump encounters a reduced pressure environment. This can cause the pump to struggle to maintain the necessary force to push the fuel through the system, especially against the back pressure generated by the engine's fuel injection system. Over time, this struggle can lead to an inefficient pumping action, where the pump may not be able to provide the required fuel volume or pressure.
The consequences of this pressure drop can be severe. If the fuel pressure drops significantly, the pump might not be able to overcome the back pressure, resulting in a complete shutdown. This situation can occur when the air in the lines is not properly addressed, leading to a potential loss of power and performance in the engine. In extreme cases, the pump may even fail prematurely due to the excessive strain caused by the air-fuel mixture.
To prevent such issues, it is crucial to ensure that the fuel system is free from air bubbles. This can be achieved through proper fueling techniques, such as priming the fuel pump or using a fuel vacuum pump to remove air from the system. Additionally, regular maintenance and inspection of the fuel lines can help identify and rectify any air-related problems, ensuring optimal fuel delivery and pump performance.
In summary, the introduction of air into the fuel lines can lead to a pressure drop, which directly affects the fuel pump's ability to function effectively. This issue highlights the importance of maintaining a clean and air-free fuel system to ensure the pump's longevity and the overall performance of the engine. By understanding and addressing this problem, vehicle owners can avoid potential breakdowns and maintain a reliable fuel supply.
Unveiling the Mystery: The Essential Metal Tool for Fuel Line Disconnects
You may want to see also
Maintenance: Regular checks can prevent air-related pump failures
Regular maintenance and inspections are crucial to preventing air-related fuel pump failures, which can be a costly and inconvenient issue for vehicle owners. The fuel pump, responsible for delivering fuel from the tank to the engine, is a critical component that can be susceptible to air-related problems. When air enters the fuel lines, it can lead to a range of issues, ultimately causing the pump to fail.
One of the primary reasons for this is the potential for air bubbles to form in the fuel lines. As fuel is pumped through the system, it can become aerated, especially if the lines are not properly sealed or if there are leaks. Over time, these air bubbles can accumulate, leading to a condition known as 'air lock'. This occurs when the air bubbles become trapped in the lines, preventing the fuel from flowing efficiently. As a result, the pump may struggle to deliver the required amount of fuel, leading to reduced engine performance and, in some cases, complete pump failure.
To prevent this, regular checks and maintenance are essential. Vehicle owners should inspect the fuel lines for any signs of damage, cracks, or leaks. Ensuring that the fuel tank is properly sealed and that there are no sources of air intrusion, such as damaged fuel caps or faulty fuel pumps, is vital. A simple yet effective practice is to check for any visible condensation in the fuel lines, as this could indicate the presence of air. Condensation forms when air enters the system, and it can be easily spotted as a milky or cloudy substance in the lines.
Additionally, keeping the fuel system clean is crucial. Over time, dirt, debris, and contaminants can accumulate in the fuel lines, especially if the fuel is not of high quality or if the vehicle is used in harsh conditions. These particles can restrict fuel flow and contribute to air-related issues. Regular fuel filter changes and the use of fuel system cleaners can help maintain the system's integrity and prevent the buildup of contaminants.
In summary, regular maintenance and inspections are key to avoiding air-related fuel pump failures. By checking for air bubbles, inspecting the fuel lines, ensuring proper sealing, and keeping the system clean, vehicle owners can significantly reduce the risk of pump failure. This proactive approach to maintenance not only saves costs but also ensures the reliable operation of the vehicle's fuel system.
The Ultimate Guide to Threading Fuel Lines: Materials and Techniques
You may want to see also
Frequently asked questions
Yes, air in the fuel lines can cause the fuel pump to stop working. When air enters the system, it can create a condition known as "air lock," which prevents the fuel from flowing properly. This can lead to a lack of fuel pressure, causing the engine to stall or not start at all.
Air bubbles in the fuel lines can disrupt the smooth flow of fuel to the engine. The pump may struggle to deliver the required fuel volume, resulting in reduced power and performance. Over time, this can also cause damage to the pump and other fuel system components.
Common symptoms include engine misfires, reduced power, and difficulty starting the vehicle. You might also notice a sputtering or hesitating sound when accelerating. If left unattended, the engine may eventually shut off completely.
Ensuring that the fuel tank is properly sealed and that there are no leaks in the fuel system is crucial. Regularly checking for and replacing old or damaged fuel lines, as well as using a fuel stabilizer, can help prevent air bubbles. Additionally, maintaining a clean fuel filter is essential to keep the system free from contaminants.