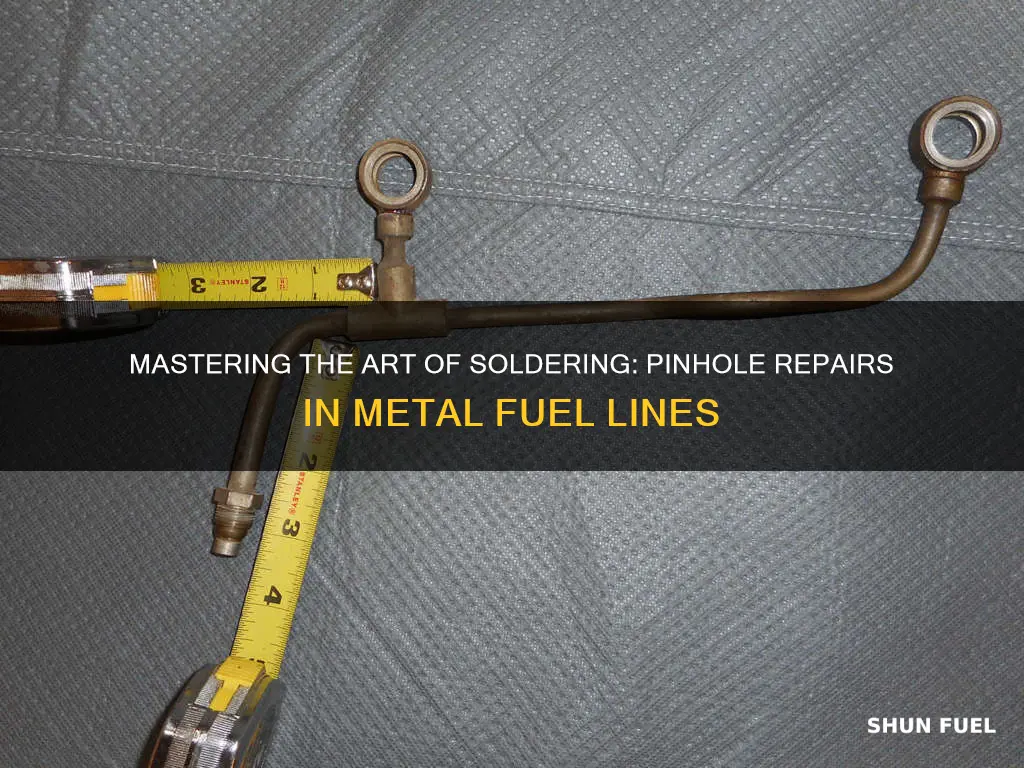
Soldering a pinhole in a metal fuel line requires precision and care to ensure a secure and leak-free repair. This guide will provide a step-by-step process for effectively soldering the pinhole, including preparing the necessary materials, cleaning the metal surface, applying flux for better solder adhesion, and heating the joint to create a strong bond. By following these instructions, you can restore the integrity of the fuel line and prevent further leaks.
What You'll Learn
- Prepare Tools: Gather soldering iron, flux, wire brush, and safety gear
- Clean Line: Use wire brush to remove oxidation and ensure a clean surface
- Apply Flux: Coat the line and joint with flux to enhance conductivity
- Heat and Melt: Heat the joint, melting the solder, and apply gentle pressure
- Inspect Joint: Check for leaks, ensure a strong bond, and test the connection
Prepare Tools: Gather soldering iron, flux, wire brush, and safety gear
Before you begin the soldering process, it's crucial to ensure you have the right tools and equipment to work with. Here's a step-by-step guide on preparing the necessary tools for soldering a pinhole in a metal fuel line:
Soldering Iron: Start by acquiring a high-quality soldering iron suitable for metalwork. Look for one with a temperature-controlled setting, allowing you to adjust the heat to the specific requirements of your project. A soldering iron with a fine, thin tip is ideal for working in tight spaces and ensuring precise heat application.
Flux: Flux is a crucial component in the soldering process, especially when dealing with metal fuel lines. It helps to clean the metal surface, remove oxidation, and create a strong bond between the metal and the solder. Choose a flux suitable for the type of metal you are working with, and ensure it is compatible with the solder you plan to use.
Wire Brush: A wire brush is essential for cleaning the metal surface and removing any dirt, rust, or debris that could interfere with the soldering process. Opt for a brush with fine wire bristles to ensure effective cleaning without damaging the metal. This step is vital to ensure a strong and reliable solder joint.
Safety Gear: Prioritize your safety by wearing appropriate gear. Heat-resistant gloves will protect your hands from the soldering iron's heat, and safety goggles are essential to shield your eyes from any potential splashes or sparks. Additionally, consider wearing a respirator mask to avoid inhaling any harmful fumes that may be produced during the soldering process.
Having these tools ready will ensure a smooth and efficient soldering process, allowing you to effectively repair or modify your metal fuel line. It's always a good practice to double-check your equipment before starting any soldering project to avoid any potential hazards.
F250 Superduty Fuel Line Dimensions: 1999 Model Year Specs
You may want to see also
Clean Line: Use wire brush to remove oxidation and ensure a clean surface
When dealing with a pinhole in a metal fuel line, ensuring a clean and prepared surface is crucial for a successful repair. One effective method to achieve this is by using a wire brush. Here's a step-by-step guide on how to utilize a wire brush to remove oxidation and ensure a clean surface:
Step 1: Prepare the Wire Brush
Start by selecting a wire brush with a stiff bristle composition suitable for metal surfaces. The brush should have a sturdy handle for a comfortable grip during the cleaning process. Ensure the bristles are not too soft, as they may not effectively remove oxidation.
Step 2: Apply the Wire Brush
Gently apply the wire brush to the affected area of the metal fuel line. Apply moderate pressure to create friction and initiate the cleaning process. Move the brush in a circular motion, ensuring you cover the entire pinhole and the surrounding area. The goal is to remove any loose oxidation, rust, or debris that might hinder the soldering process.
Step 3: Remove Oxidation
As you brush, you will notice the bristles collecting small particles of oxidation and debris. This is a good sign, indicating that the oxidation is being effectively removed. Continue the brushing process until the surface appears clean and free of any visible oxidation. Be thorough but gentle to avoid damaging the metal.
Step 4: Inspect and Repeat
After brushing, inspect the area closely. If oxidation or debris is still present, repeat the brushing process until the surface is consistently clean. This step is essential to ensure a strong bond between the solder and the metal during the repair.
Step 5: Consider Safety Precautions
While using a wire brush, it's important to work in a well-ventilated area or outdoors to avoid inhaling any potential fumes or particles. Additionally, wear safety gear, such as gloves and eye protection, to safeguard yourself during the process.
By following these steps and using a wire brush effectively, you can create a clean and prepared surface for soldering the pinhole in the metal fuel line, increasing the likelihood of a successful and long-lasting repair.
Nylon Fuel Line Repair: Quick Tips for a Successful Fix
You may want to see also
Apply Flux: Coat the line and joint with flux to enhance conductivity
When dealing with a pinhole in a metal fuel line, applying flux is a crucial step to ensure a successful repair. Flux is a substance that is used to clean and prepare the surfaces of the metal, creating a better bond for the solder. This process is essential as it helps to remove any oxidation or corrosion that may have occurred around the pinhole, allowing the solder to flow more easily and form a strong, durable joint.
To begin, ensure you have the right type of flux for the job. There are various types available, such as rosin-based fluxes, which are commonly used for general-purpose soldering, and acid-core fluxes, which are more aggressive and suitable for thicker or more oxidized surfaces. Choose a flux that is compatible with the metal of your fuel line and the type of solder you will be using.
Next, carefully clean the area around the pinhole. Use a wire brush or a small scrubber to remove any dirt, grease, or old solder residue. This step is vital to ensure the flux adheres properly and doesn't interfere with the soldering process. Once the area is clean, apply a thin, even layer of flux to the metal surfaces, including the pinhole itself and the surrounding area where the solder will be applied. Make sure to cover the entire joint, as this will help to create a strong, reliable connection.
When applying the flux, take your time and be thorough. You want to ensure that the flux is distributed evenly, as an uneven application might lead to inconsistent results. Allow the flux to act for a few minutes, following the manufacturer's instructions for optimal results. This waiting period allows the flux to activate and prepare the metal surfaces for soldering.
Remember, the goal of applying flux is to improve the conductivity between the metal and the solder, ensuring a strong and reliable joint. By properly preparing the surfaces with flux, you set the stage for a successful repair, minimizing the risk of future leaks or damage. This step is a critical part of the soldering process and should not be overlooked.
Mastering Fuel Line Repairs: A Guide to Fixing 1.4-Inch Rubber Fuel Lines
You may want to see also
Heat and Melt: Heat the joint, melting the solder, and apply gentle pressure
When dealing with a pinhole in a metal fuel line, soldering is a crucial technique to ensure a secure and leak-free repair. The process begins with careful preparation and the right tools. You'll need a soldering iron with a fine tip, a suitable flux, and a high-quality solder that is compatible with the metal of your fuel line. It's essential to clean the joint area to remove any dirt or corrosion, ensuring a strong bond.
The key step in this process is the 'heat and melt' technique. Start by heating the joint of the fuel line where the pinhole is located. Use the soldering iron to apply heat directly to the metal, being careful not to overheat the surrounding areas. The heat should be sufficient to bring the metal just below its melting point. As you heat the joint, you'll observe the solder melting and becoming liquid. This is the critical moment where the magic happens.
Once the solder is melted, quickly but gently apply pressure to the joint. Apply steady pressure with a pair of pliers or your fingers (if you have a steady hand) to ensure the solder flows into the pinhole and forms a strong bond with the metal. The pressure should be firm but controlled to avoid distorting the metal or causing damage. This step requires precision and a steady hand to avoid any excess solder or uneven distribution.
Hold the pressure for a few seconds, allowing the solder to cool and solidify. This initial bond will provide the foundation for a strong, leak-free repair. After a short while, you can release the pressure and assess the quality of the joint. If the solder has flowed correctly and filled the pinhole, you've successfully repaired the fuel line.
Remember, practice makes perfect when it comes to soldering. Take your time, be patient, and ensure you have the right tools and materials for the job. With a little patience and the right technique, you can effectively repair a pinhole in a metal fuel line using soldering.
Optimizing Performance: Choosing the Right Fuel Line for Your 50 HP Outboard
You may want to see also
Inspect Joint: Check for leaks, ensure a strong bond, and test the connection
When dealing with a pinhole in a metal fuel line, the inspection and repair process is crucial to ensure the safety and efficiency of your vehicle's fuel system. The first step is to carefully examine the joint where the pinhole is located. Start by cleaning the area around the hole to remove any dirt, debris, or old solder residue. Use a wire brush or a small wire brush tool to gently scrub the surface, ensuring it is free from any contaminants. This step is essential as it provides a clean and smooth surface for the new solder to adhere to.
Next, inspect the joint for any signs of damage or weakness. Look for any cracks, corrosion, or signs of previous repairs. If you notice any issues, it's important to address them before proceeding. In some cases, you might need to cut out the damaged section and replace it with a new piece of metal pipe. Ensure that the joint is free from any sharp edges or rough surfaces that could compromise the soldering process.
To check for leaks, you can use a simple bubble test. Soak the joint in a mixture of water and dish soap, ensuring the pinhole is covered. If there are any leaks, bubbles will form around the joint, indicating the presence of air or fuel escaping. This test is a quick way to identify potential issues and ensure the integrity of the repair. If leaks are detected, you may need to re-solder the joint or consider more permanent solutions like welding, depending on the severity of the damage.
Ensuring a strong bond is crucial for the long-term success of the repair. Prepare the metal surfaces by cleaning them again and applying a flux to the joint. Flux helps to remove any oxidation and provides a protective layer for the solder, allowing it to flow more easily. Follow the instructions on the flux product for the best results. Then, heat the joint and apply the solder, ensuring it melts and forms a solid connection. Practice the proper soldering technique to avoid any air bubbles, which can weaken the bond.
Finally, test the connection by applying pressure to the joint and checking for any leaks. You can also run the fuel system under pressure to ensure the repair holds up. If no leaks are detected, your pinhole repair should be secure. However, it's essential to remember that soldering is a temporary fix, and regular inspections are recommended to ensure the safety of your vehicle's fuel system.
Small Engine Fuel Line: Choosing the Right Option for Your Needs
You may want to see also
Frequently asked questions
Soldering a pinhole in a metal fuel line is a temporary fix to repair a small hole or crack. It helps to prevent fuel leaks and maintain the structural integrity of the fuel system.
While temporary solutions like clamps or tape can provide some level of containment, they are not as effective as soldering. Clamps may not create a strong bond, and tape can lose its adhesive properties over time, leading to potential fuel leaks. Soldering offers a more permanent and reliable repair.
You will need a soldering iron with a fine tip, a suitable solder (lead-free or traditional), flux to clean the metal surface, a pair of tweezers or pliers for handling small components, and a heat source to apply heat to the joint. It's also recommended to have a small container of solvent cleaner to remove any oxidation from the metal surface.
Start by cleaning the area around the pinhole with the solvent cleaner to ensure a good bond. Then, use the flux to coat the metal surfaces, which will help the solder adhere better. Be careful not to apply too much flux, as it can cause issues with the soldering process.
Apply a small amount of solder to the tip of the soldering iron, then touch the hot tip to the pinhole, ensuring the solder melts and fills the gap. Keep the heat applied for a few seconds, then remove the iron. The solder should form a strong bond, creating a seamless repair. Allow the joint to cool down before handling the fuel line.