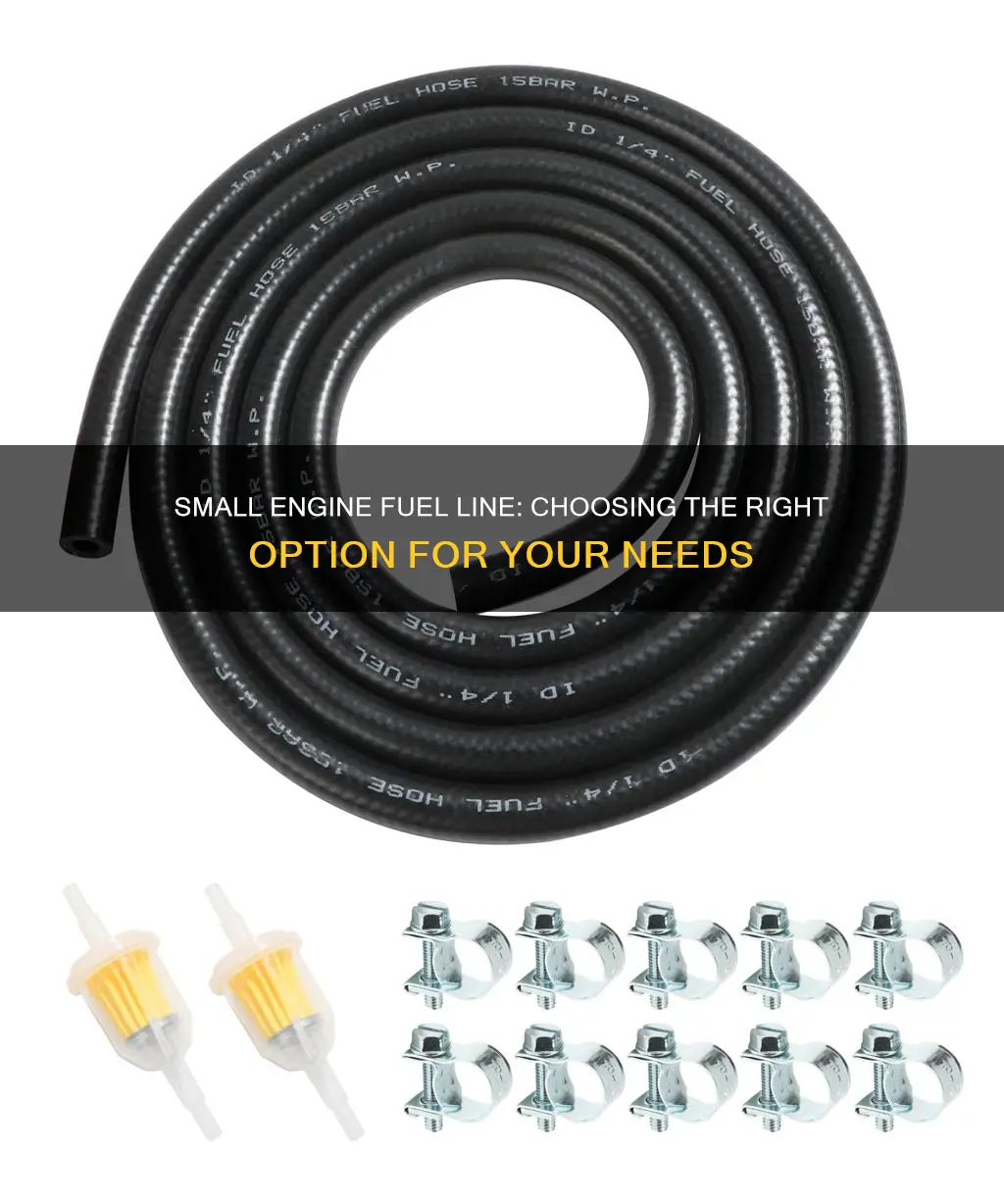
When it comes to small engines, choosing the right fuel line is crucial for optimal performance and longevity. A good small engine fuel line is designed to efficiently deliver fuel from the tank to the carburetor or fuel injection system while withstanding the challenges of small engine environments. These lines are typically made from durable materials like high-density polyethylene (HDPE) or nylon, ensuring flexibility, resistance to fuel degradation, and the ability to handle high pressure without leaking. Additionally, they often feature a braided construction for added strength and protection against damage from engine vibrations and external factors. Understanding the specifications and compatibility of different fuel lines is essential for ensuring your small engine operates smoothly and reliably.
Characteristics | Values |
---|---|
Material | Plastic, rubber, or metal (brass or aluminum) |
Diameter | Typically 5/16" to 3/8" (7.94 mm to 9.53 mm) |
Length | Varies depending on engine and application, but common lengths include 12", 18", 24", 36", or 48" |
Flexibility | Good flexibility to accommodate engine movement |
Durability | Resistant to fuel, oil, and weather conditions |
Temperature Range | Able to withstand engine operating temperatures (-40°F to 250°F or -40°C to 121°C) |
Compatibility | Compatible with gasoline, diesel, and other common engine fuels |
Ease of Installation | Straightforward and relatively easy to install |
Cost | Affordable, especially for small engines |
Availability | Widely available at hardware stores and online retailers |
What You'll Learn
- Materials: Plastic, rubber, or metal lines are common, each with unique properties
- Diameter: Fuel lines come in various diameters, affecting flow rate and pressure
- Length: Consider the engine's layout and the distance between fuel source and carburetor
- Flexibility: Lines must bend without cracking to withstand engine vibrations
- Compatibility: Ensure the fuel line is compatible with the fuel type and engine type
Materials: Plastic, rubber, or metal lines are common, each with unique properties
When it comes to choosing the right fuel line for a small engine, the material is a critical factor to consider. The three primary materials used for fuel lines are plastic, rubber, and metal, each offering distinct advantages and disadvantages. Understanding these properties will help you make an informed decision for your engine's needs.
Plastic fuel lines are lightweight and flexible, making them an excellent choice for small engines where space is limited and maneuverability is essential. They are resistant to corrosion and can withstand a wide range of temperatures, which is crucial for engines operating in various environments. Additionally, plastic lines are often more affordable, making them a cost-effective option. However, they may not be as durable as other materials and can be more susceptible to damage from sharp objects or rough handling.
Rubber fuel lines provide excellent flexibility and durability. They are known for their ability to absorb vibrations, which helps reduce engine noise and protect the fuel line from damage. Rubber is also resistant to most chemicals, ensuring that the fuel remains pure and doesn't degrade over time. This material is often used in high-performance engines where reliability and longevity are essential. Despite its advantages, rubber can be more expensive and may not be as flexible as plastic, making it less ideal for tight spaces.
Metal fuel lines, typically made from materials like steel or aluminum, offer superior strength and durability. They are highly resistant to corrosion and can withstand extreme temperatures, making them suitable for heavy-duty applications. Metal lines are often used in industrial or marine environments where the engine operates under harsh conditions. However, they are much heavier and less flexible than plastic or rubber, which can be a challenge during installation and maintenance. Additionally, metal lines can be more expensive and may require specialized tools for installation.
In summary, the choice of material depends on the specific requirements of your small engine. Plastic lines offer flexibility and cost-effectiveness, rubber provides durability and vibration dampening, while metal lines excel in extreme conditions but may be less practical for some applications. Considering the engine's operating environment, space constraints, and budget will help you select the most suitable fuel line material.
Unleash Your Charm: Understanding the Art of Fuel Pick-Up Lines
You may want to see also
Diameter: Fuel lines come in various diameters, affecting flow rate and pressure
The diameter of a fuel line is a critical factor in determining its performance and suitability for a specific application. Fuel lines are designed to transport gasoline or diesel from the tank to the engine, and the diameter directly influences the flow rate and pressure of the fuel. A larger diameter fuel line allows for a higher flow rate, which means more fuel can be delivered to the engine per unit of time. This is particularly important in high-performance applications where the engine requires a rapid and consistent fuel supply to meet its power demands. For example, in racing or sports cars, a larger diameter fuel line might be used to ensure that the engine receives the necessary fuel to achieve peak performance.
On the other hand, a smaller diameter fuel line can be advantageous in certain scenarios. In applications where fuel efficiency is a priority, a smaller diameter line can help reduce fuel consumption. This is because a smaller line restricts the flow, creating a pressure drop that encourages the engine to use less fuel to maintain the desired power output. This principle is often utilized in economy-focused vehicles or small engines, where optimizing fuel efficiency is a key design consideration.
The choice of diameter also depends on the engine's power output and the overall system design. For instance, a small engine used for lawnmowers or generators might benefit from a slightly larger diameter fuel line to ensure a steady fuel supply, especially during periods of high demand. In contrast, a high-performance engine in a sports bike may require a smaller diameter line to maintain the desired pressure and flow characteristics.
It's important to note that the diameter of the fuel line should be matched with the engine's requirements and the overall fuel system design. Engineers and mechanics must consider factors such as the engine's displacement, compression ratio, and fuel injection system to determine the optimal diameter. This ensures that the fuel line can handle the expected flow rates and pressures without causing issues such as fuel starvation or excessive pressure, which could lead to engine performance problems.
In summary, the diameter of a fuel line is a crucial consideration when selecting the right fuel line for a small engine. It directly impacts the flow rate and pressure of the fuel, and the choice of diameter should be based on the specific engine requirements and the desired performance characteristics. Understanding these factors allows for an informed decision-making process, ensuring the engine operates efficiently and effectively.
Exploring Rubber Fuel Line Hose Sizes: A Comprehensive Guide
You may want to see also
Length: Consider the engine's layout and the distance between fuel source and carburetor
When it comes to small engines, the length of the fuel line is a critical factor to consider, especially when taking into account the engine's layout and the distance between the fuel source and the carburetor. This is a crucial aspect of engine design and performance, as it directly impacts the fuel delivery system's efficiency and reliability.
The primary purpose of a fuel line is to transport gasoline from the fuel tank to the carburetor, where it is mixed with air and then inducted into the engine's cylinders. The length of this line should be optimized to ensure that the fuel reaches the carburetor at the right pressure and flow rate. If the line is too short, it may result in a restriction, causing a decrease in fuel flow and potential performance issues. On the other hand, an overly long fuel line can lead to fuel degradation, especially in small engines where the fuel system is more susceptible to issues.
Engine layout plays a significant role in determining the ideal fuel line length. In-line engines, where the carburetor is positioned directly above the engine block, typically require shorter fuel lines. This design allows for a more direct path from the fuel tank to the carburetor, minimizing the risk of fuel line restrictions. In contrast, V-twin or horizontally opposed engines often have a more complex layout, requiring longer fuel lines to reach the carburetor positioned at the front or rear of the engine.
The distance between the fuel source and the carburetor is another critical factor. For small engines, this distance is usually relatively short, ranging from a few inches to a few feet. When designing the fuel line, it is essential to consider the engine's orientation and the available space. In some cases, the fuel line may need to be routed around obstacles or through tight spaces, requiring careful planning to ensure a straight and unobstructed path.
To optimize fuel line performance, it is recommended to use high-quality fuel lines made from durable materials such as rubber or vinyl. These materials can withstand the pressure and temperature variations encountered in small engines. Additionally, ensuring that the fuel line is properly secured and free from kinks or bends can further enhance its efficiency. Regular maintenance, including checking for leaks and replacing worn-out fuel lines, is essential to keep the engine running smoothly.
Optimizing LS Swap Fuel Lines: A Comprehensive Guide
You may want to see also
Flexibility: Lines must bend without cracking to withstand engine vibrations
When it comes to small engine fuel lines, flexibility is a critical factor that ensures the system can withstand the rigors of the engine's operation. These fuel lines are designed to transmit fuel from the tank to the carburetor or fuel injection system, and they must be able to move and bend without compromising their structural integrity. The constant vibrations and movements of the engine can put significant stress on the fuel lines, so it's essential to choose lines that are flexible enough to handle these demands.
The primary goal of flexibility in fuel lines is to prevent cracking or breaking under the engine's dynamic conditions. Small engines, often found in lawnmowers, generators, and other outdoor equipment, experience rapid acceleration and deceleration, as well as rotational forces. If the fuel lines are too rigid, they may crack or even snap, leading to fuel leaks, reduced performance, or even engine failure. Therefore, selecting fuel lines with a flexible material is crucial.
To achieve this flexibility, manufacturers often use materials like rubber or a synthetic composite that can bend and twist without permanent deformation. These materials are carefully selected to balance flexibility with durability, ensuring the lines can withstand the harsh environment of the engine compartment. The flexibility also allows for easier installation, as the lines can be routed around various engine components without excessive strain.
In addition to the material, the construction of the fuel line also plays a role in its flexibility. Lines with a braided or reinforced design can provide additional flexibility while maintaining structural integrity. Braided lines, for example, use a series of braided strands to create a flexible yet strong line that can handle the engine's vibrations without compromising performance.
When choosing a fuel line for a small engine, it's essential to consider the specific requirements of the application. Factors such as the engine's power output, operating conditions, and the presence of any modifications should be taken into account. By selecting a flexible fuel line that meets these criteria, you can ensure reliable fuel delivery and protect your engine from potential damage caused by rigid or brittle lines.
Fuel Line Clog Symptoms: Engine Issues Revealed
You may want to see also
Compatibility: Ensure the fuel line is compatible with the fuel type and engine type
When it comes to choosing a fuel line for a small engine, compatibility is a critical factor that cannot be overlooked. The fuel line is a vital component that connects the fuel source to the engine, and using the wrong type can lead to performance issues and potential damage. Here's a detailed guide on ensuring compatibility:
Fuel Type Compatibility: Different engines are designed to run on various types of fuel, such as gasoline, diesel, or liquefied petroleum gas (LPG). It's essential to identify the fuel type your engine is designed for. For instance, a gasoline engine requires a fuel line that can handle gasoline's properties, including its volatility and resistance to degradation. On the other hand, diesel engines need a fuel line that can withstand higher pressures and the unique characteristics of diesel fuel. Using a fuel line incompatible with the engine's fuel type can result in fuel leaks, poor performance, and even engine damage.
Engine Type Compatibility: Small engines come in various types, such as four-stroke, two-stroke, or rotary engines. Each engine type has specific requirements for fuel delivery. For example, two-stroke engines often use a smaller diameter fuel line to ensure a precise fuel-air mixture, while four-stroke engines may require a slightly larger line to accommodate the different fuel injection system. The engine's design and fuel system play a crucial role in determining the appropriate fuel line diameter, material, and routing.
To ensure compatibility, it's recommended to consult the engine manufacturer's guidelines or specifications. These resources will provide detailed information on the recommended fuel line type, diameter, and any specific requirements for your engine model. Using the correct fuel line ensures optimal performance, fuel efficiency, and longevity of your small engine.
Additionally, consider the environmental conditions in which the engine will operate. Extreme temperatures or exposure to harsh chemicals can impact the fuel line's performance. Choose a fuel line that can withstand these conditions without compromising its integrity.
In summary, compatibility is the key to a successful fuel line installation. By understanding the engine's fuel type and design, you can select a fuel line that meets the specific requirements, ensuring reliable and efficient operation. Always refer to the manufacturer's recommendations to make informed choices and avoid potential issues.
Quick Fix: Temporary Solutions for Leaky Fuel Lines
You may want to see also
Frequently asked questions
A small engine fuel line is a type of fuel delivery system used in small engines, such as those found in lawn mowers, generators, and other outdoor power equipment. It is designed to deliver gasoline or diesel fuel from the tank to the engine's carburetor or fuel injection system efficiently and reliably.
Selecting the appropriate fuel line depends on several factors, including engine type, fuel requirements, and environmental conditions. Consider the engine's horsepower, fuel consumption rate, and whether it uses a carburetor or fuel injection. Additionally, choose a fuel line made from durable materials like rubber or vinyl, ensuring it can withstand fuel type, temperature variations, and engine vibrations.
Small engine fuel lines can encounter several problems over time. Clogging due to dirt, debris, or fuel contamination is a common issue, leading to poor engine performance. Leaks at the connections or fittings are another potential problem, causing fuel wastage and engine misfires. Regular maintenance, such as cleaning and inspecting the fuel line, can help prevent these issues and ensure optimal engine operation.