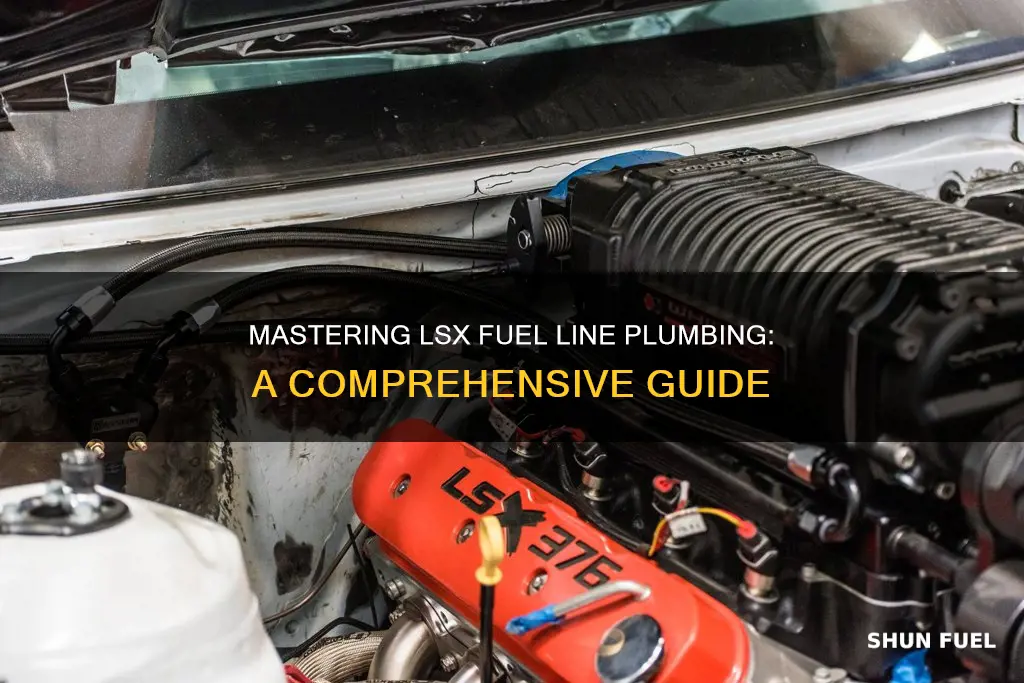
Plumbing fuel lines on LSX engines requires careful planning and execution to ensure optimal performance and reliability. This guide will provide a step-by-step approach to effectively route and secure fuel lines, covering essential considerations such as material selection, line sizing, and proper installation techniques. By following these instructions, you can create a robust fuel system that delivers fuel efficiently to the engine while minimizing the risk of leaks and ensuring a smooth running vehicle.
What You'll Learn
- Fuel Tank Installation: Secure the tank, ensuring proper alignment and mounting
- Line Routing: Plan a safe path, avoiding sharp bends and potential damage
- Fittings and Connections: Use appropriate fittings for a tight, leak-free seal
- Fuel Pump Placement: Position the pump to ensure optimal fuel flow
- Testing and Inspection: Verify functionality and pressure before final assembly
Fuel Tank Installation: Secure the tank, ensuring proper alignment and mounting
When installing a fuel tank on an LSX engine, proper alignment and secure mounting are crucial to ensure optimal performance and safety. Here's a step-by-step guide to achieving this:
- Preparation: Begin by laying out all the necessary components, including the fuel tank, mounting brackets, and any additional hardware required. Ensure you have a clear understanding of the tank's specifications, such as its capacity and dimensions, to ensure compatibility with your LSX setup.
- Tank Placement: Position the fuel tank in the designated location, typically behind the driver's side of the engine bay. Ensure the tank is aligned correctly, with its opening facing the appropriate direction for fuel line connections. Check for any obstructions or interference with other engine components during this step.
- Secure Mounting: Utilize the provided mounting brackets or custom-made brackets designed for your LSX engine. Secure the tank to the brackets using the appropriate fasteners, such as bolts or screws. Ensure that the tank is firmly attached and cannot shift or move during engine operation. Consider using vibration-damping materials or rubber mounts to reduce noise and vibrations.
- Alignment Verification: Double-check the tank's alignment to ensure it is level and properly positioned. Adjust the mounting brackets if necessary to achieve the correct orientation. Proper alignment is essential to prevent fuel sloshing and potential leaks.
- Fuel Line Connections: With the tank securely mounted, proceed with connecting the fuel lines. Refer to the LSX's fuel system diagram for guidance on the correct routing and connections. Ensure all fuel lines are properly secured with clamps or ties to prevent movement and potential damage.
Remember, each LSX engine setup may vary, so it's essential to consult the specific instructions and diagrams provided for your engine. Properly securing the fuel tank will contribute to a reliable and efficient fuel system, ensuring your LSX engine operates optimally.
Is Your 3/8 Fuel Line Up to the Task?
You may want to see also
Line Routing: Plan a safe path, avoiding sharp bends and potential damage
When plumbing fuel lines on an LSX engine, proper line routing is crucial to ensure optimal performance and longevity. The goal is to create a smooth, efficient path for the fuel to travel from the tank to the engine, minimizing potential issues like leaks, restrictions, and damage. Here's a detailed guide on planning a safe route for your fuel lines:
- Understand the Layout: Begin by studying the engine bay and the available space. Identify the locations of the fuel tank, fuel pump, and the engine's fuel injectors or carburetor. Visualize the path the fuel needs to take and consider the natural flow of the engine bay. Understanding the layout will help you anticipate potential challenges and make informed decisions about line placement.
- Avoid Sharp Bends: One of the most critical aspects of line routing is avoiding sharp bends. Fuel lines should be routed in a way that minimizes sharp turns, as these can lead to restrictions, reduced fuel flow, and potential damage to the lines. Aim for gentle curves and straight runs whenever possible. Use flexible fuel line material that can accommodate some bending without kinking or cracking.
- Plan for Accessibility: Ensure that the fuel lines are easily accessible for maintenance and repairs. Avoid routing lines in areas where they might be accidentally damaged or obstructed by other components. Keep lines away from hot engine components, exhaust systems, and moving parts. Proper accessibility also allows for easier inspection and identification of potential issues.
- Consider Flexibility and Routing Material: Choose the appropriate fuel line material based on your specific application. Rubber or silicone-based fuel lines offer flexibility and resistance to heat and chemicals. Ensure the lines are long enough to allow for some slack and easy installation. When routing, use bends that are gradual and consistent, avoiding sharp angles that could lead to kinking.
- Securement: Properly secure the fuel lines to prevent movement and potential damage. Use fuel-resistant clips, ties, or brackets to attach the lines to the engine bay and other components. Avoid tight bends or sharp turns that could cause the lines to rub against each other or other surfaces. Securement also helps maintain the integrity of the fuel lines and prevents leaks.
By carefully planning the route, considering the engine's layout, and avoiding sharp bends, you can ensure that your fuel lines are properly plumbed, providing efficient and reliable fuel delivery to the LSX engine. Remember, proper routing is essential for the overall performance and longevity of your fuel system.
Towing's Impact: Fuel Line Damage Risks Explained
You may want to see also
Fittings and Connections: Use appropriate fittings for a tight, leak-free seal
When plumbing fuel lines on an LSX engine, ensuring a tight and leak-free seal is crucial for optimal performance and safety. The right fittings and connections are essential to achieving this. Here's a detailed guide on the process:
Fitting Selection: Choose fittings that are compatible with the fuel lines and engine components. Common materials for fuel lines include steel, aluminum, and rubber. Select fittings made from similar materials to ensure a secure connection. For example, use steel fittings for steel fuel lines and aluminum fittings for aluminum lines. This compatibility ensures that the fittings won't corrode or degrade over time due to fuel exposure.
Threaded Fittings: Threaded fittings are commonly used for fuel lines. Ensure that the threads are clean and free of debris before assembly. Apply a thin layer of thread sealant or pipe compound to the threads to enhance the seal. Tighten the fittings securely, but be careful not to over-tighten, as this can damage the fuel lines. A good rule of thumb is to use a torque wrench to achieve the manufacturer's recommended torque specifications.
Clamped Fittings: Clamped fittings provide a secure connection using a clamp around the fuel line. These are useful for quick connections and adjustments. Ensure the clamp is made from a compatible material and apply it firmly, ensuring it doesn't pinch the fuel line. Check the clamp's tightness periodically, especially if the vehicle is subjected to vibration or extreme conditions.
Bungs and Caps: Use bungs or caps to temporarily seal openings in the fuel lines during installation. These should be made from compatible materials and tightened securely to prevent fuel leakage. When sealing openings, ensure the bungs or caps are tight enough to prevent fuel from seeping out but not so tight that they damage the fuel line.
Leak-Proof Assembly: Pay close attention to each connection to ensure a leak-free assembly. Inspect the fittings for any signs of damage or deformation. Check for any gaps or spaces between the fittings and the fuel lines, and ensure they are properly sealed. Use thread seal tape or pipe dope on threaded fittings to provide an additional layer of protection against leaks.
Honda Motorcycle Fuel Line: Size Guide for Optimal Performance
You may want to see also
Fuel Pump Placement: Position the pump to ensure optimal fuel flow
When plumbing fuel lines for an LSX engine, the placement of the fuel pump is critical to ensuring optimal fuel flow and performance. The goal is to position the pump in a way that minimizes pressure drop and maximizes efficiency. Here's a detailed guide on how to achieve this:
- Consider the Engine Bay Layout: Begin by understanding the available space in your engine bay. The LSX engine family offers various configurations, and the pump's placement will depend on the specific model and year. For example, some LSX engines may have limited space near the front of the engine bay, while others might have more room towards the rear. Identify the best location that allows for easy access and proper clearance.
- Height and Proximity to the Fuel Tank: The fuel pump should be positioned as close as possible to the fuel tank to reduce the height difference, which can cause pressure issues. Aim for a height difference of no more than 12 inches (30 cm) between the pump and the tank. Additionally, ensure the pump is not too high or too low; an ideal height would be around 18-24 inches (45-60 cm) above the ground to allow for easy maintenance and access.
- Orientation and Mounting: Proper orientation is key to efficient fuel flow. Typically, the pump should be mounted vertically, with the inlet and outlet ports aligned with the fuel lines. This orientation ensures that the fuel flows smoothly through the lines without unnecessary bends or twists, which can create pressure losses. Secure the pump using appropriate mounting brackets to ensure it remains stable and vibration-free during operation.
- Consideration of Heat and Noise: Fuel pumps generate heat, so it's essential to choose a location that provides adequate cooling. Avoid placing the pump near heat-sensitive components or areas where it might overheat. Additionally, consider the noise level; some pumps can be noisy, so positioning them away from the driver's compartment or passenger area can be beneficial.
- Testing and Adjustments: After installing the fuel pump, it's crucial to test the system to ensure optimal performance. Start the engine and monitor the fuel pressure using a gauge. Adjust the pump's position or angle if necessary to fine-tune the fuel flow. Proper placement will result in consistent and stable fuel pressure, ensuring your LSX engine runs efficiently and reliably.
Flare for Aluminum Fuel Lines: Unlocking the Secrets of a Perfect Fit
You may want to see also
Testing and Inspection: Verify functionality and pressure before final assembly
Before finalizing the assembly of the fuel system on your LSX engine, it is crucial to conduct thorough testing and inspection to ensure its functionality and reliability. This step is often overlooked, but it plays a vital role in preventing potential issues and ensuring optimal performance. Here's a detailed guide on how to approach this process:
Fuel Line Testing: Start by checking each fuel line for any visible damage, such as cracks, leaks, or signs of deterioration. Inspect the lines for any bends or kinks that might have occurred during installation. Ensure that all connections are secure and free from any debris or contaminants. Use a fuel pressure gauge to measure the pressure at different points along the lines. The pressure should be consistent and within the recommended range specified by the engine manufacturer. If any discrepancies are found, identify the source of the issue and address it accordingly.
Pressure Testing: Set up a pressure test to simulate the engine's operating conditions. Connect the fuel pump to a pressure gauge and ensure it delivers the required pressure to the injectors or carburetor. Check for any leaks or pressure drops along the fuel lines. If any issues are detected, consider replacing the affected lines or fittings to maintain a robust fuel supply. It is essential to verify that the fuel system can handle the pressure requirements of the engine to prevent potential failures.
Functionality Verification: With the fuel system pressurized, inspect the engine's response. Start the engine and monitor its performance. Check for any unusual noises, such as hissing or roaring sounds, which could indicate fuel leaks. Ensure that the engine starts and runs smoothly, with no erratic behavior. Verify that the fuel pump engages and disengages as it should, providing a consistent fuel supply. This step is critical to identifying any potential issues with the plumbing or fuel delivery system.
Final Assembly Inspection: Before closing the engine bay, double-check all connections and fittings. Ensure that all fuel lines are securely attached and free from any obstructions. Inspect the engine compartment for any signs of fuel leakage or spills. Clean the area if necessary to prevent contamination. Properly secure all components to maintain a professional and safe assembly.
By following these testing and inspection procedures, you can ensure that your LSX engine's fuel system is reliable and ready for optimal performance. It is an essential step that should not be overlooked, as it directly contributes to the overall efficiency and longevity of the engine.
Makita Blower Fuel Line: Unlocking the Mystery of the Perfect Fit
You may want to see also
Frequently asked questions
For optimal performance and longevity, it is recommended to use high-quality fuel lines specifically designed for high-pressure fuel systems. Braided stainless steel fuel lines are a popular choice due to their durability, flexibility, and resistance to fuel degradation. These lines can handle the high pressures associated with LSX engines and provide a reliable fuel delivery system.
Before installing the fuel lines, ensure that the engine bay is clean and free of any debris. Inspect the fuel lines for any bends or kinks and straighten them if necessary. It is crucial to route the lines away from moving parts and heat sources to prevent damage. Consider using fuel line clips or ties to secure the lines and maintain a neat appearance.
Reusing original fuel lines is generally not recommended for an LSX engine. LSX engines often require modifications to the fuel system to accommodate the new engine's requirements. The original lines may not be compatible with the higher fuel pressures and flow rates of the LSX. It is best to invest in new, high-quality fuel lines designed for the specific LSX application.
Plumbing fuel lines on an LSX engine requires several essential tools. These include fuel line cutters or shears for trimming the lines to the desired length, fuel line connectors or fittings to join the lines, a fuel line crimping tool for secure connections, and a fuel line cleaner to ensure a proper seal. Additionally, have a fuel pressure gauge and a fuel pump primer to test the system's functionality.