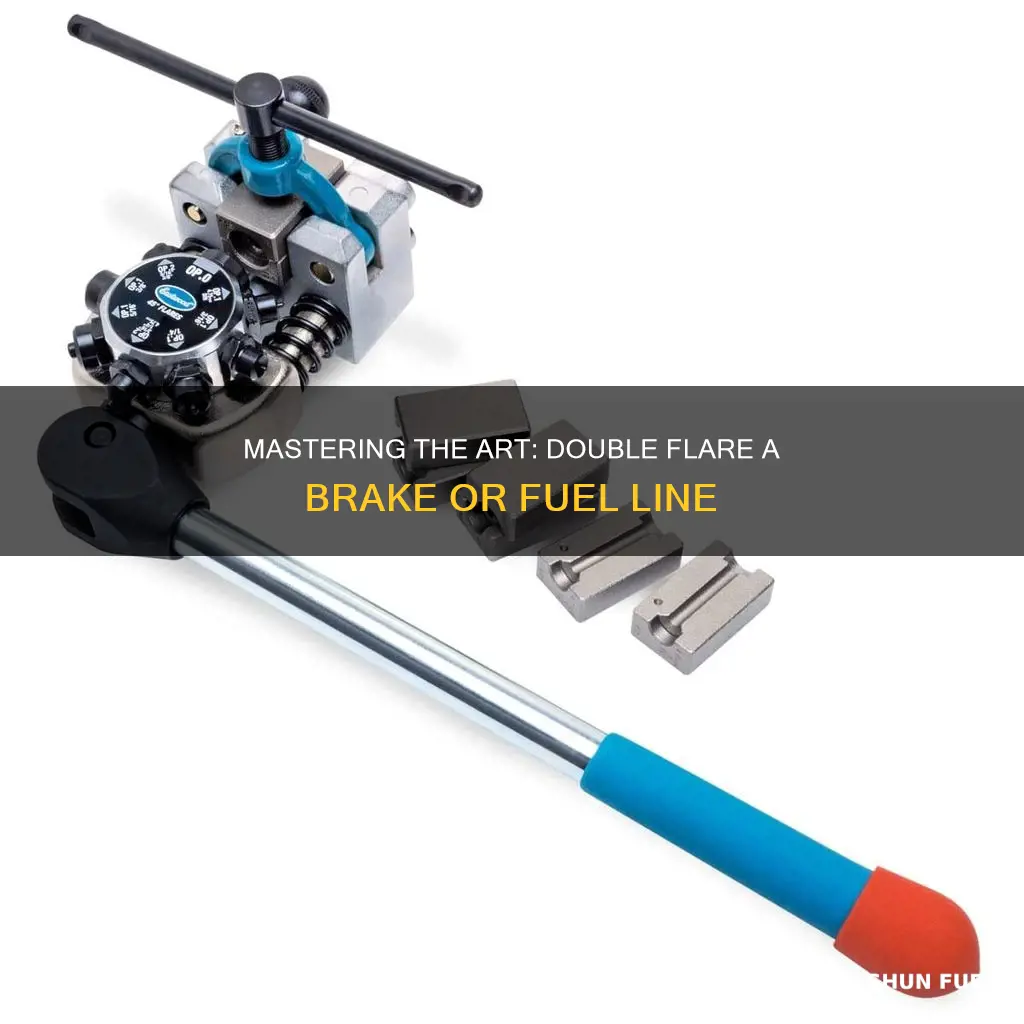
Doubling flare a brake or fuel line is a crucial skill for anyone working on vehicles, as it ensures a secure and reliable connection. This technique involves creating a double flare, which provides a stronger and more durable joint compared to a single flare. By following a series of precise steps, you can achieve a tight and leak-free connection, ensuring the safety and performance of your vehicle's critical systems. This guide will walk you through the process, offering tips and tricks to master the art of double flaring.
What You'll Learn
- Preparation: Ensure you have the right tools and safety gear for the job
- Location: Identify the correct location of the flare fitting on the line
- Angle: Use the correct angle for the flare tool to create a tight seal
- Force: Apply the right amount of force to avoid damaging the line
- Finishing: Tighten the flare nut securely and test for leaks
Preparation: Ensure you have the right tools and safety gear for the job
Before you begin the process of double flaring a brake or fuel line, it's crucial to ensure you have the necessary tools and safety equipment to guarantee a successful and safe outcome. Here's a comprehensive guide to the preparation phase:
Gather the Tools: Start by assembling all the required tools for the job. Double flaring involves creating a secure connection by bending and shaping the pipe or line. You'll need a pipe or line bender, preferably a manual or power bender depending on the size and material of your line. For smaller lines, a manual bender might suffice, but for larger or thicker materials, a power bender could be more efficient. Additionally, a pair of pliers, a wire brush, and a file will be essential for cleaning and shaping the metal. Don't forget a pair of safety gloves and eye protection to shield your hands and eyes from any potential debris or sharp edges.
Safety Gear: Safety should always be a top priority. Wear appropriate clothing that covers your skin, such as long sleeves and pants, to prevent any accidental cuts or burns. Ensure you have a dust mask or respirator to avoid inhaling any hazardous fumes, especially when working with fuel lines. It's also advisable to wear a helmet or hard hat to protect your head from any falling objects or debris. Consider using safety goggles or a face shield to safeguard your eyes from any potential splashes or sparks.
Work Area Preparation: Set up your work area in a well-ventilated space, preferably outdoors, to minimize the risk of fumes accumulation. Ensure the area is clear of any trip hazards and that you have a stable workbench or table to place your tools and materials on. Consider using a non-conductive mat to provide an insulating surface, especially when working with fuel lines to prevent electrical discharges.
Materials and Components: Have all the necessary materials ready, including the brake or fuel line, flare nuts, and any specific adapters or fittings required for your vehicle. Ensure the line is clean and free of any debris or old flares before beginning the process.
By taking the time to prepare and gather the right tools and safety gear, you'll set the foundation for a smooth and safe double-flaring process, ensuring a reliable connection for your brake or fuel line.
Fuel Line Failure: Causes, Symptoms, and Solutions
You may want to see also
Location: Identify the correct location of the flare fitting on the line
When it comes to double flaring a brake or fuel line, identifying the correct location of the flare fitting is crucial. This process involves creating a flare at both ends of the line to ensure a secure and leak-free connection. Here's a step-by-step guide to help you locate the flare fitting accurately:
Start by examining the line and locating the existing flare fitting, if any. This fitting is typically where the line connects to a component such as a caliper, master cylinder, or fuel tank. Mark this point clearly with a piece of tape or a small piece of paint to serve as a reference. Understanding the existing setup will help you determine the correct orientation for the new flare.
Next, measure the length of the line from the existing flare fitting to the end of the line. This measurement will be essential for ensuring the flare fitting is positioned correctly. Use a flexible measuring tape or a ruler to get an accurate reading. Take note of the length, as it will guide you in positioning the new flare fitting.
Now, visualize the path the line takes from the existing flare to the desired connection point. Consider the angles and bends the line undergoes. This step is crucial for ensuring the flare fitting is aligned properly and doesn't interfere with other components. You might need to refer to diagrams or schematics of the braking or fuel system to get a clear understanding of the line's path.
Once you have a clear idea of the line's path, mark the location for the new flare fitting. Use a permanent marker or a small piece of tape to indicate this spot. Ensure that the new flare fitting is positioned at the correct distance from the existing flare, as measured earlier. This step requires precision to avoid any misalignment issues.
Finally, double-check your measurements and markings to ensure accuracy. Verify that the new flare fitting location is aligned with the line's path and that it doesn't interfere with any other components. This meticulous approach will contribute to a successful double flare installation.
Honda Foreman 450 Fuel Line: Size and Compatibility Guide
You may want to see also
Angle: Use the correct angle for the flare tool to create a tight seal
When it comes to double flaring a brake or fuel line, the angle at which you use the flare tool is crucial for achieving a tight and secure seal. The process involves creating a series of folds or flares on the end of the line to ensure a robust connection. Here's a detailed guide on how to get the angle right:
The flare tool should be positioned at a specific angle relative to the line you are working on. This angle is typically measured in degrees and varies depending on the type of flare and the system's requirements. For most double flares, a common angle is around 30 to 45 degrees. This angle allows for a gradual and precise bend, ensuring that the flares are formed evenly and without excessive force. It's important to note that the angle should be consistent throughout the flare process to maintain symmetry and a professional finish.
To achieve the correct angle, start by placing the flare tool's jaw onto the line, ensuring it is centered and aligned with the desired flare point. Then, gently but firmly apply pressure to the tool's handle, guiding it along the line's curve. As you move the tool, maintain a steady and controlled pace to avoid over-bending or creating uneven flares. The goal is to create a smooth, continuous curve without any sharp bends or kinks.
Practice and precision are key to mastering this technique. Take your time and focus on getting the angle right. You can use a caliper or a measuring tool to check the angle periodically, ensuring it remains consistent. Remember, the goal is to create a tight seal, and the correct angle will contribute significantly to the overall quality of the flare.
In summary, achieving the right angle is essential for a successful double flare. It requires a combination of technique, precision, and practice. By following the recommended angle guidelines and taking your time, you can create flares that provide a reliable and secure connection for your brake or fuel lines.
Unraveling the Mystery: What the Fuel Line Connects to
You may want to see also
Force: Apply the right amount of force to avoid damaging the line
When working on double-flaring a brake or fuel line, applying the correct amount of force is crucial to ensure a successful and secure connection. Here's a detailed guide on how to achieve this:
Start by ensuring you have the right tools for the job. You'll need a flare tool, which is specifically designed to create the flare. This tool should be the correct size to match the diameter of your line. It's essential to use the appropriate size to avoid over-flanging, which can damage the line. Place the line securely in the flare tool, ensuring it is centered and aligned with the tool's opening. This initial step sets the foundation for the rest of the process.
Now, it's time to apply force. The key is to use controlled pressure to shape the line without causing any bends or kinks. Begin by gently pushing the flare tool towards the line, creating a slight indentation. This initial force should be light, allowing you to gauge the line's flexibility and the tool's grip. As you feel the line start to conform to the tool's shape, gradually increase the pressure. The goal is to create a smooth, continuous curve without applying excessive force that could lead to damage.
The process requires precision and patience. You should feel the line's resistance as you work, and this feedback will guide your force application. Keep applying pressure evenly, ensuring the line remains straight and true. Avoid any sudden movements or jerky actions, as these can cause the line to twist or bend unnecessarily. Remember, the goal is to create a tight, secure flare without compromising the line's integrity.
As you near the end of the flare, slightly reduce the force to avoid over-flanging. This final adjustment ensures the flare is neat and precise. Once you've achieved the desired shape, release the pressure and carefully remove the flare tool. Inspect the flare to ensure it is smooth and free of any sharp edges. This careful application of force throughout the process is vital to the success of the double flare.
In summary, applying the right amount of force is an art that requires practice and a keen sense of touch. It ensures the line is shaped correctly without suffering damage. Always take your time and listen to the line's feedback to create a professional-grade double flare.
Alcohol-Resistant Fuel Lines: The Ultimate Guide to Compatibility
You may want to see also
Finishing: Tighten the flare nut securely and test for leaks
Once you've successfully created the flare on the brake or fuel line, it's crucial to finish the job properly to ensure a secure and leak-free connection. The final step is tightening the flare nut, which requires careful attention to detail.
Start by placing the flare nut onto the flare, ensuring it is aligned correctly. Use a wrench to tighten the nut by hand, giving it a good grip. This initial tightening is important to set the stage for the final securement. Be cautious not to overtighten at this stage, as it can damage the flare or the nut.
Now, it's time to tighten the nut securely. Use a wrench that fits the nut's size and thread, applying firm pressure. Turn the wrench in a clockwise direction, ensuring you are turning the nut, not the flare. Tighten it until it is snug, but be careful not to overdo it. The goal is to achieve a firm connection without forcing the nut onto the flare, which could lead to damage.
After tightening, it's essential to test for any potential leaks. Locate the flare connection and inspect it for any signs of leakage. You can use a soapy water solution or a specialized leak detection spray to make this process easier. Apply the solution to the connection and observe if any bubbles appear, indicating a leak. If you detect any leaks, it's crucial to address them immediately.
If leaks are found, you may need to adjust the tightening or even re-flare the connection. Ensure you have the necessary tools and knowledge to make these adjustments safely and effectively. Once you've addressed any leaks, re-test the connection to ensure it is secure and leak-free. This final step is critical to guarantee the reliability and safety of your brake or fuel line system.
Fuel Injector Cleaning: Unclogging Fuel Lines for Optimal Performance
You may want to see also
Frequently asked questions
A double flare is a specific type of fitting used in hydraulic systems, particularly for brake and fuel lines. It involves creating a double-threaded section at the end of a tube, which is then inserted into a corresponding double-threaded fitting. This design provides a secure and leak-proof connection, allowing for the transmission of hydraulic pressure or fuel.
Before starting, ensure you have the necessary tools and materials, including the brake or fuel line, a double flare tool, a tube cutter, and a flare gauge. Cut the line to the desired length, ensuring a smooth and clean cut. Use the tube cutter to achieve a precise and square cut, as this will make the flaring process easier.
Begin by inserting the tube into the double flare tool, ensuring it is centered. Use the tool to create the first flare, applying pressure and rotating the tool to form a tight seal. Repeat this process to create the second flare, making sure the first flare is secure before proceeding. Check the flare gauge to ensure the dimensions are correct, and adjust if necessary.
One common issue is an improper fit, which can lead to leaks. Ensure the tube is inserted correctly and the flares are formed at the right angles. Another potential problem is over-tightening, which may damage the tube or tool. Always use the appropriate force and follow the manufacturer's guidelines to avoid such issues. Regularly check the flare gauge to ensure the flares are of the correct size and shape.