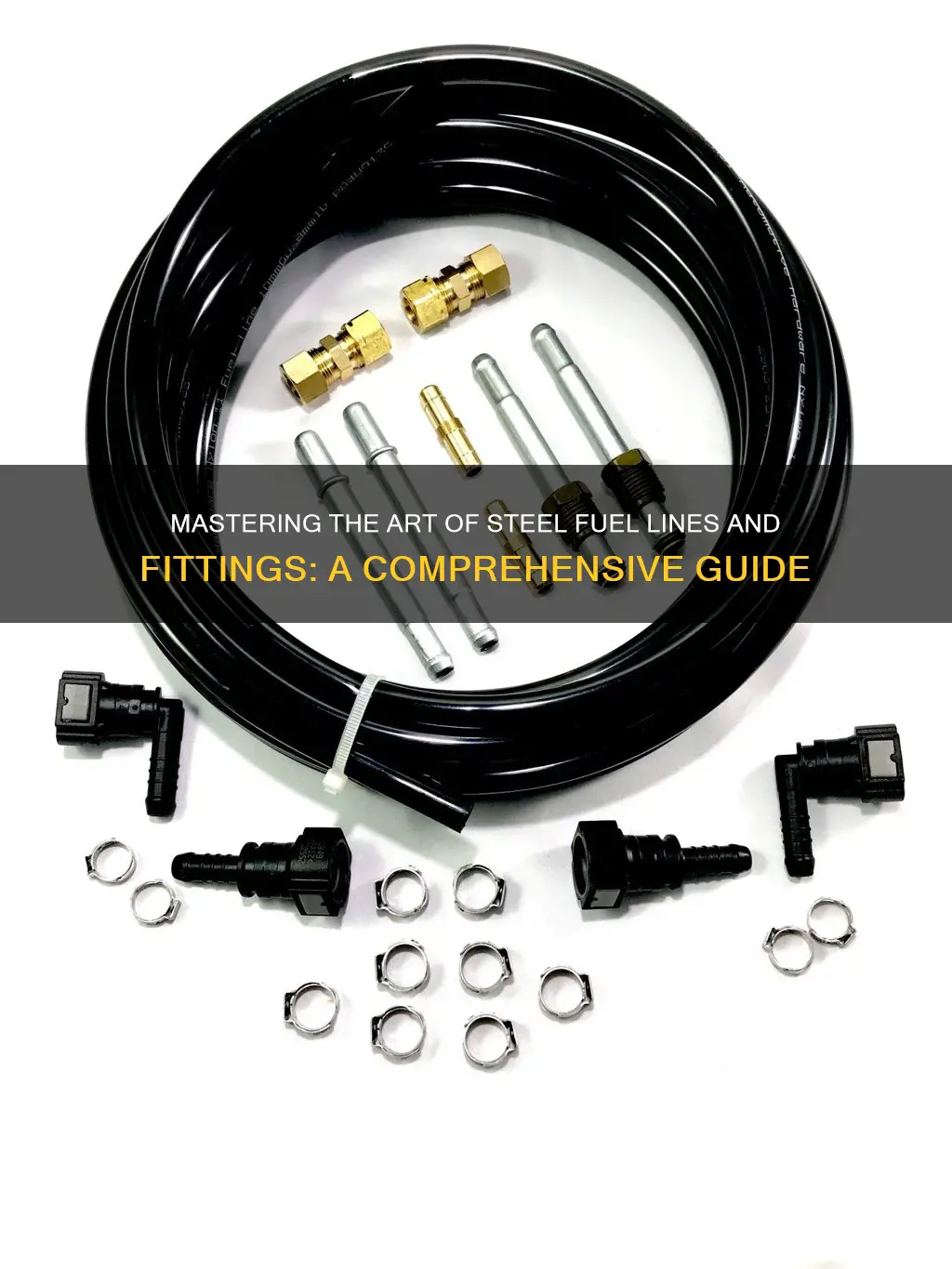
Creating steel fuel lines and fittings is a specialized process that requires precision and expertise. It involves selecting the appropriate steel grade, such as 304 or 316 stainless steel, which offers excellent corrosion resistance for fuel applications. The manufacturing process typically includes bending, welding, and fitting fabrication to ensure a secure and leak-proof connection. Proper preparation of the steel surface, such as cleaning and etching, is crucial for achieving a strong bond during the welding process. This introduction sets the stage for a detailed guide on the technical aspects of fabricating steel fuel lines and fittings, ensuring a reliable and safe fuel system for vehicles or industrial equipment.
What You'll Learn
- Material Selection: Choose appropriate steel alloys for fuel lines and fittings based on temperature and pressure requirements
- Fabrication Techniques: Employ methods like bending, welding, and threading to create custom fuel lines and fittings
- Pipe Bending: Use specialized tools to bend steel pipes to desired angles and shapes for fuel lines
- Fitting Installation: Securely attach fittings to fuel lines using welding, threading, or compression methods
- Testing and Inspection: Perform pressure tests and visual inspections to ensure the integrity and safety of the steel fuel system
Material Selection: Choose appropriate steel alloys for fuel lines and fittings based on temperature and pressure requirements
When designing steel fuel lines and fittings, material selection is a critical aspect to ensure the system's reliability and performance. The choice of steel alloy must consider the operating conditions, including temperature and pressure, to guarantee the safety and efficiency of the fuel delivery system. Here's a detailed guide on how to select the appropriate steel alloys for this application:
Temperature Considerations:
Fuel lines and fittings are exposed to varying temperatures, especially in automotive or industrial settings. For low-temperature applications, such as cold climates or fuel systems with liquid fuels, stainless steel alloys like 304 or 316 are excellent choices. These alloys offer excellent corrosion resistance and can withstand freezing temperatures without becoming brittle. In contrast, for high-temperature environments, such as racing cars or industrial machinery, consider using alloys like 4130 or 4340 steel. These alloys provide superior strength and heat resistance, ensuring the fuel lines can handle elevated temperatures without compromising structural integrity.
Pressure and Mechanical Stress:
Fuel lines and fittings must also be designed to manage the pressure and mechanical stress associated with fuel delivery. For low-pressure systems, standard carbon steel alloys, such as 1018 or 1020, can be used, providing adequate strength and durability. However, for high-pressure applications, it is crucial to select alloys with enhanced mechanical properties. Alloys like 4340 or 4130 steel offer improved tensile strength and hardness, making them ideal for fuel lines that operate under significant pressure. These alloys can withstand the forces exerted by high-pressure fuel pumps and injectors.
Corrosion Resistance:
Corrosion is a significant concern in fuel systems, as it can lead to fuel degradation and system failure. To combat this, consider using stainless steel alloys with higher chromium content, such as 304L or 316L. These alloys provide excellent corrosion resistance, especially in environments with high humidity or exposure to fuel contaminants. For applications where corrosion resistance is critical, such as marine or off-road vehicles, the use of stainless steel is highly recommended.
Flexibility and Ductility:
Fuel lines often require flexibility to accommodate engine movement and vibrations. Alloys like 304 stainless steel or 1018 carbon steel offer a good balance of strength and ductility, allowing for some flexibility without compromising structural integrity. This flexibility is essential to prevent cracking or damage to the fuel lines during engine operation.
In summary, the selection of steel alloys for fuel lines and fittings should be a meticulous process, considering the specific temperature and pressure requirements of the application. By choosing the right alloys, engineers can ensure the fuel system's longevity, safety, and performance, contributing to a reliable and efficient fuel delivery mechanism. This approach to material selection is fundamental in the manufacturing process of high-quality steel fuel lines and fittings.
2003 Trailblazer Fuel Line Location: A Comprehensive Guide
You may want to see also
Fabrication Techniques: Employ methods like bending, welding, and threading to create custom fuel lines and fittings
To create custom steel fuel lines and fittings, you'll need to employ various fabrication techniques that ensure the final product is both functional and durable. Here's a detailed guide on the methods you can use:
Bending: This is a fundamental process in fabricating steel components. To bend steel into the desired shape for fuel lines, you'll require a metal bending machine or a brake press. Start by marking the steel sheet with the intended bend radius and line. Then, position the steel correctly on the machine, ensuring the marked line aligns with the machine's bending axis. Apply force gradually, following the machine's instructions, to achieve the desired bend. For tight bends, consider using a mandrel to prevent the steel from kinking. Practice and precision are key to achieving clean, professional-looking bends.
Welding: Welding is essential for joining steel components and creating a seamless fuel line. Begin by preparing the steel surfaces, ensuring they are clean, free of oil, and slightly oxidized. Use a flux to prevent oxidation and promote a strong bond. Select an appropriate welding electrode and current for the job. Practice on a test piece to get a feel for the process. When welding, maintain a consistent arc length and speed. For complex fittings, consider using a TIG (Tungsten Inert Gas) welding technique, which offers precise control over the heat input, resulting in a cleaner, more refined weld.
Threading: Threading steel for fuel fittings requires a threading machine or a hand-held tool. Start by marking the steel with the desired thread depth and pitch. Secure the steel in the threading machine and feed it slowly, following the machine's instructions. For hand-threading, use a die and a tap. Insert the tap into the steel, creating the female thread, and then use the die to cut the male thread. Ensure the threads are accurate and consistent to guarantee a tight, leak-proof connection.
Additionally, consider using a mandrel or a core for complex fittings, especially when dealing with tight bends and small diameters. This technique involves inserting a mandrel into the steel tube and then bending it around the mandrel, ensuring a consistent radius. After fabrication, always inspect the work for any defects or imperfections and make necessary adjustments or repairs.
Mastering these fabrication techniques will enable you to create custom steel fuel lines and fittings tailored to specific vehicle requirements, ensuring optimal performance and longevity.
Mastering Fuel Line Disconnect Pliers: A Comprehensive Guide
You may want to see also
Pipe Bending: Use specialized tools to bend steel pipes to desired angles and shapes for fuel lines
Pipe bending is a crucial step in creating custom steel fuel lines and fittings, ensuring a precise and secure fit within the vehicle's engine bay. This process requires specialized tools and a methodical approach to achieve the desired angles and shapes. Here's a detailed guide on how to bend steel pipes for fuel lines:
Tools and Materials:
Before beginning, ensure you have the necessary tools and materials. You'll need a pipe bender, which can be a manual or hydraulic model, depending on the complexity of the bends. The bender should be suitable for the thickness of the steel pipe you are working with. Additionally, have the steel pipe, fuel fittings, and any necessary cutting tools ready. It's essential to use high-quality steel to ensure durability and compatibility with fuel systems.
Preparation:
Start by measuring and marking the pipe at the desired bend points. Use a straight edge or a ruler to ensure accurate measurements. Mark the pipe with a pencil or a marker to indicate the bend radius and the desired angle. This step is critical to achieving the correct shape and fit. Consider the vehicle's engine layout and the position of the fuel tank and engine to plan the bends accordingly.
Bending Process:
- Position the pipe bender: Place the pipe securely in the bender, ensuring it is centered and aligned with the bending axis.
- Apply force: Depending on the bender type, apply the required force to create the bend. For manual benders, this might involve using a mallet or a mechanical lever. Hydraulic benders will have a control mechanism to adjust the pressure.
- Control the bend: As you bend the pipe, maintain a consistent pressure and control the angle. The goal is to create a smooth, continuous bend without kinks or sharp bends that could compromise the pipe's integrity.
- Repeat for multiple bends: If your fuel line requires multiple bends, repeat the process at the marked points, ensuring each bend aligns with the previous one.
Safety and Precision:
Pipe bending requires precision and attention to detail. Always wear appropriate safety gear, such as gloves and eye protection, to avoid injuries. Take your time and work carefully to avoid damaging the pipe or fittings. It's essential to get the bends right, as incorrect angles can lead to fuel leaks or reduced flow. Consider using a mandrel or a bending die to create more complex shapes and ensure a clean, precise bend.
Finishing and Testing:
Once the bending is complete, inspect the fuel lines for any defects or imperfections. Ensure the bends are smooth and free from sharp edges. Test the fittings and connections to guarantee a tight and secure seal. Consider using a fuel line inspection tool to verify the integrity of the bends and connections.
Understanding the Three Fuel Lines in an Engine: A Comprehensive Guide
You may want to see also
Fitting Installation: Securely attach fittings to fuel lines using welding, threading, or compression methods
When it comes to installing fuel fittings onto steel fuel lines, there are several methods to ensure a secure and reliable connection. The choice of method depends on factors such as the type of fitting, the fuel line material, and the specific application. Here's a detailed guide on how to securely attach fittings using welding, threading, and compression methods:
Welding Method:
Welding is a strong and permanent method for attaching fittings to fuel lines. This process involves heating the fuel line and fitting until they reach a molten state and then joining them together. Here's a step-by-step process:
- Prepare the Materials: Ensure you have the appropriate welding equipment, including a welding torch, shielding gas, and a suitable welding rod for steel. Clean the fuel line and fitting surfaces to remove any dirt or contaminants.
- Positioning: Position the fitting onto the fuel line, ensuring proper alignment and orientation. Use clamps or temporary fixtures to hold the fitting in place temporarily.
- Welding Process: Apply the welding torch to the joint, heating the fuel line and fitting until they become soft and malleable. Maintain a consistent heat source and ensure the temperature is suitable for welding steel. Then, melt the welding rod and carefully fuse it into the joint, creating a strong bond.
- Post-Welding: After welding, inspect the joint for any defects or imperfections. Remove any excess welding material and grind the joint to ensure a smooth finish. Test the weld's strength and integrity using non-destructive testing methods if necessary.
Threading Method:
Threading is a common technique for attaching fittings, especially in fuel systems where flexibility is required. This method involves creating a male or female thread on the fuel line and fitting.
- Threading Preparation: Use a thread-cutting tool or die to cut threads onto the fuel line and fitting. Ensure the threads are of the correct pitch and diameter for a secure fit.
- Assembly: Insert the fitting onto the fuel line, aligning the threads. Apply thread sealing tape or compound to the threads to prevent leaks. Hand-tighten the fitting, then use a wrench to tighten it further, ensuring the threads are engaged properly.
- Final Check: Inspect the threaded connection for any signs of leakage. Spin the fitting by hand to ensure it rotates freely without backing off. If everything is secure, the fitting is ready for use.
Compression Method:
Compression fittings are commonly used for fuel lines due to their ease of installation and leak-resistant properties.
- Fitting Installation: Slide the compression fitting over the fuel line, ensuring it covers the entire diameter of the line. The fitting should have a compression nut and a ferrule (a metal or composite ring) that grips the fuel line.
- Tightening: Tighten the compression nut by hand, then use a wrench to apply additional force. The goal is to compress the ferrule onto the fuel line, creating a secure seal. Ensure the nut is tightened evenly to avoid damaging the fuel line.
- Final Steps: After tightening, inspect the fitting for any leaks. Spin the fitting to ensure it doesn't back off. If all checks pass, the compression fitting is installed correctly.
Each of these methods offers a reliable way to connect fuel fittings to steel fuel lines, ensuring a secure and leak-free system. It's important to follow manufacturer guidelines and best practices for each fitting type to guarantee the longevity and safety of the fuel system.
Mastering Braided Fuel Line Splices: A Comprehensive Guide
You may want to see also
Testing and Inspection: Perform pressure tests and visual inspections to ensure the integrity and safety of the steel fuel system
When it comes to ensuring the safety and reliability of a steel fuel system, testing and inspection are crucial steps that should not be overlooked. These processes help identify potential issues and ensure that the fuel lines and fittings are capable of withstanding the pressures and demands of the fuel system. Here's a detailed guide on how to approach these tests and inspections:
Pressure Testing:
Pressure testing is an essential method to evaluate the integrity of the steel fuel lines and fittings. This test involves applying pressure to the system and monitoring for any leaks or failures. Start by filling the fuel lines with a suitable test fluid, such as water or a specialized fuel system test fluid, to a specific pressure recommended by the manufacturer. Use a calibrated pressure gauge to measure and maintain the desired pressure. Then, observe the system for any signs of leakage, such as bubbles or moisture appearing in the test fluid. If any leaks are detected, it indicates a potential issue with the fittings or the quality of the steel used. Ensure that the test pressure is sufficient to simulate real-world conditions, providing a comprehensive assessment.
Visual Inspection:
In addition to pressure testing, visual inspections play a vital role in identifying any visible defects or potential failure points. Begin by thoroughly examining the steel fuel lines for any signs of corrosion, rust, or damage. Look for bends, kinks, or any visible imperfections that could compromise the structural integrity of the lines. Pay close attention to the fittings as well; check for any cracks, warping, or signs of excessive wear. Ensure that all connections are secure and tight, as loose fittings can lead to fuel leaks. It is also important to inspect the system for any signs of contamination, such as fuel residue or debris, which can affect the performance and safety of the fuel system.
During the visual inspection, make detailed notes of any issues found, including their locations and severity. This documentation will be valuable for further analysis and any necessary repairs or replacements. It is recommended to perform these inspections at regular intervals, especially after any modifications or repairs to the fuel system, to ensure ongoing safety and compliance.
By combining pressure testing and visual inspections, you can effectively assess the overall health and safety of the steel fuel system. These methods help identify potential problems early on, allowing for timely repairs or replacements, thus ensuring the system's longevity and reliability. Remember, proper testing and inspection are critical to maintaining a safe and efficient fuel system.
Toyota Fuel Line Removal: A Step-by-Step Guide for Injector Access
You may want to see also
Frequently asked questions
Manufacturing steel fuel lines and fittings involves several steps. It begins with the selection of high-quality steel alloys, which are then melted and refined to ensure purity. The molten steel is poured into molds to create the desired shape and size of the fuel lines and fittings. After cooling, the steel components are cut, bent, and formed using precision machinery to achieve the required specifications. Heat treatment processes such as annealing or hardening may be applied to enhance the material's strength and durability. Finally, the steel parts undergo thorough inspections and quality control checks to meet industry standards.
Installing steel fuel lines and fittings requires careful planning and adherence to safety guidelines. Start by disconnecting the fuel supply at the tank and ensuring the engine is off. Clean the mounting surfaces and apply a suitable primer to prevent corrosion. Slide the fuel line into the fitting, ensuring a secure connection. Use fuel line clips or brackets to secure the line in place, maintaining the required tension. Repeat this process for all connections, ensuring proper alignment and tightness. Finally, double-check all connections for leaks and re-connect the fuel supply, allowing the system to prime before starting the engine.
Yes, steel fuel lines and fittings are generally compatible with various fuel types, including gasoline, diesel, and even biofuels. However, it's essential to consider the specific fuel properties and compatibility with the chosen steel alloy. Some fuels, like ethanol-blended gasoline, may require additional precautions due to their corrosive nature. Always refer to the manufacturer's guidelines and recommendations for the specific fuel you are using. Proper installation, regular maintenance, and the use of compatible materials can ensure the longevity and reliability of steel fuel systems across different fuel types.