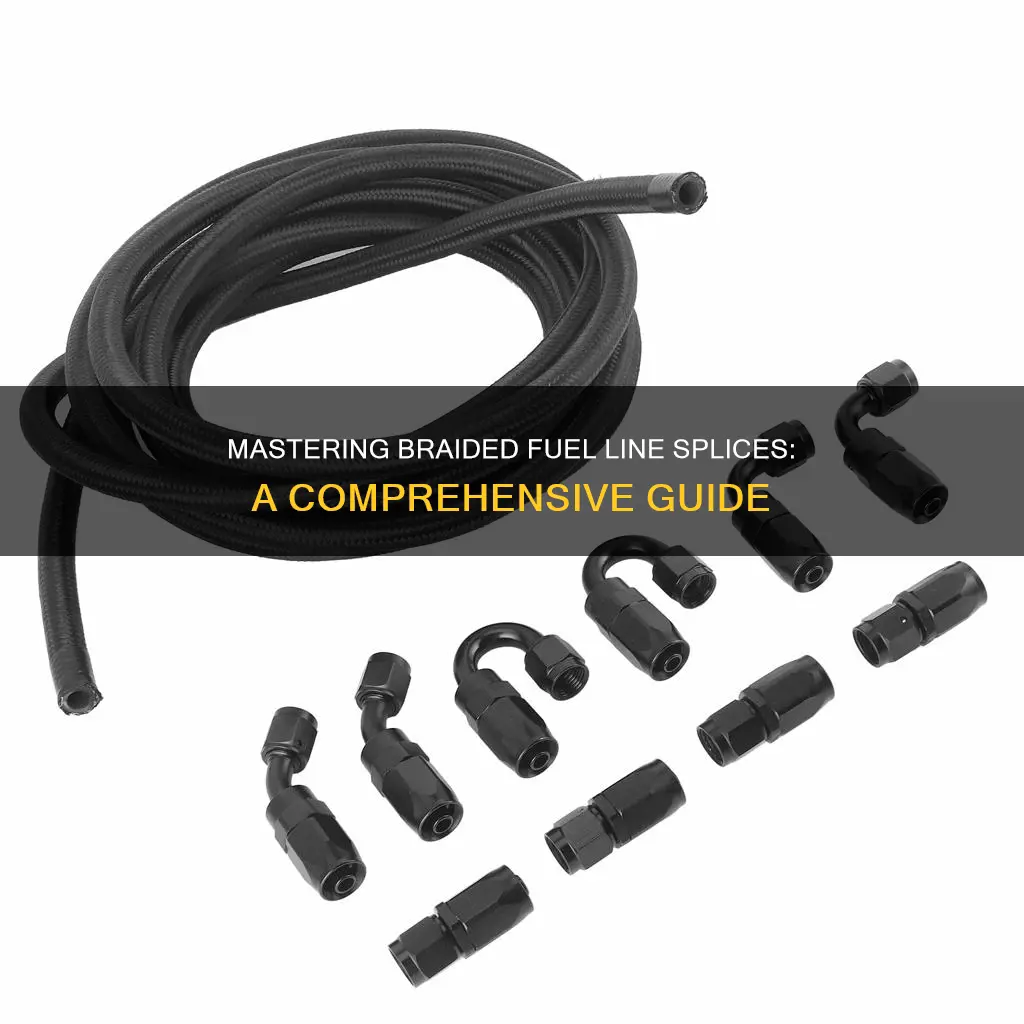
Splicing braided fuel lines is a crucial skill for anyone working on automotive or marine projects that require precise fuel delivery. This process involves joining two braided fuel lines together to create a continuous path for fuel flow. It requires careful preparation, including cleaning the lines and ensuring they are free of debris, and the use of specialized tools and techniques to create a secure and leak-free connection. By following a step-by-step guide, you can master the art of splicing braided fuel lines, ensuring optimal performance and reliability in your fuel system.
Characteristics | Values |
---|---|
Preparation | Clean and prepare the fuel line ends. Remove any dirt, corrosion, or debris. Ensure the ends are smooth and free of damage. |
Tools and Materials | You'll need a fuel line splicer or a heat shrink kit, a fuel line cleaner, a rag, and a heat source (e.g., a heat gun or a soldering iron). |
Process | 1. Cut the braided fuel line to the desired length, leaving a few extra inches for splicing. 2. Use the splicer or heat shrink kit to create a splice. Follow the manufacturer's instructions for the specific tool you're using. 3. Heat the splice area until the material softens. 4. Insert the fuel line into the splice, ensuring a snug fit. 5. Allow the splice to cool and harden. |
Safety | Wear protective gear, including gloves and safety goggles, when working with fuel lines. Ensure proper ventilation in the workspace. |
Testing | After splicing, test the fuel line by applying pressure and checking for leaks. |
Maintenance | Regularly inspect spliced fuel lines for any signs of damage or wear. |
What You'll Learn
- Prepare Tools: Gather necessary tools: fuel line cutter, hose clamp, and cleaning supplies
- Clean Surface: Ensure both ends of the fuel line are clean and free of debris
- Measure and Cut: Measure and cut the braided fuel line to the desired length
- Prepare Connections: Prepare the ends by deburring and ensuring a smooth surface
- Secure and Test: Secure the splice with a hose clamp and test for leaks
Prepare Tools: Gather necessary tools: fuel line cutter, hose clamp, and cleaning supplies
Before you begin the process of splicing a braided fuel line, it's crucial to ensure you have the right tools and materials ready. This will make the task more efficient and help you achieve a professional-looking result. Here's a step-by-step guide on preparing the necessary tools:
Fuel Line Cutter: Start by acquiring a fuel line cutter, which is a specialized tool designed for cutting fuel lines. This tool will allow you to make precise and clean cuts on the braided fuel line. Look for a cutter that can handle the thickness of your fuel line; if you're working with thicker lines, you might need a more robust cutter. A good quality fuel line cutter will ensure a smooth and accurate cut, reducing the risk of damage to the fuel line or the surrounding components.
Hose Clamp: A hose clamp is essential for securing the spliced section of the fuel line. It provides a tight and reliable connection, preventing any potential leaks. Choose a hose clamp that is appropriate for the diameter of your fuel line. Different sizes are available, so select one that fits snugly around the braided fuel line without being too tight or too loose.
Cleaning Supplies: Proper cleaning is an often-overlooked but critical step in splicing a fuel line. Start by gathering cleaning supplies such as a degreaser or fuel line cleaner, a brush or scrubber, and a clean rag. Cleaning the fuel line and the surrounding area is essential to remove any dirt, grease, or contaminants that could interfere with the splicing process. This step ensures a clean and smooth surface for the splice, promoting a secure and leak-free connection.
Having these tools and supplies ready will streamline your splicing process and contribute to a successful and safe fuel line repair or modification. It's always a good practice to double-check the compatibility of the tools with your specific fuel line before proceeding with the splicing procedure.
Outboard Fuel Line Clogs: Causes and Solutions
You may want to see also
Clean Surface: Ensure both ends of the fuel line are clean and free of debris
When splicing a braided fuel line, ensuring a clean and debris-free surface is crucial for a successful and secure connection. Start by carefully removing any existing fuel line from the vehicle, taking note of the length and any unique features. This step is essential to understand the specific requirements of your fuel line and to ensure you have the right amount of new line for the splice. Once the old line is removed, inspect the ends of the fuel line. Over time, debris can accumulate, causing friction and potential issues during the splicing process. Use a soft-bristled brush or a specialized fuel line cleaning tool to gently remove any dirt, corrosion, or old fuel residue. Ensure you clean both the inside and outside of the fuel line, paying extra attention to the threads and any fittings.
For an even more thorough clean, consider using a solvent-based cleaner specifically designed for fuel lines. These cleaners can help dissolve and remove stubborn deposits. Allow the fuel line to dry completely before proceeding with the splicing. Moisture can lead to corrosion and weaken the bond between the new splice and the line. You can use a hairdryer on a low setting to speed up the drying process, ensuring a thorough and safe drying.
Once the fuel line is dry and clean, it's time to prepare the ends for splicing. Debris-free surfaces are critical to ensure a tight and leak-free connection. Any remaining dirt or residue can cause the splice to fail, leading to potential fuel leaks and engine issues. Take your time with this step, as it is essential for the overall success of the project.
Remember, a clean and prepared surface is the foundation for a strong and durable splice. By taking the time to thoroughly clean the fuel line ends, you are setting yourself up for a successful and long-lasting repair. This simple yet crucial step can prevent future problems and ensure the safety and efficiency of your vehicle's fuel system.
Mastering Fuel Line Replacement: A Guide to Poulan PP4218AVX Pro
You may want to see also
Measure and Cut: Measure and cut the braided fuel line to the desired length
Before you begin the splicing process, it's crucial to measure and cut the braided fuel line accurately. This step ensures that the new section seamlessly integrates with the existing line, maintaining the integrity of the fuel system. Here's a step-by-step guide:
- Assess the Length: Start by carefully examining the fuel line and determining the required length. Measure the distance between the two ends of the line that you intend to splice. Take note of any bends or kinks in the line, as these might affect the overall length. It's essential to have a precise measurement to avoid any wastage or potential issues during the splicing process.
- Mark the Cutting Point: Using a permanent marker or a piece of chalk, mark the cutting point on the fuel line. Ensure that the mark is aligned with the desired length you measured. This step helps you stay focused during the cutting process and prevents any mistakes.
- Prepare the Cutting Tools: You can use a sharp utility knife or a dedicated fuel line cutter for this task. If using a knife, ensure it is sharp enough to make a clean cut through the braided material. For a more precise and professional finish, consider using a fuel line cutter, which is designed specifically for this purpose.
- Make the Cut: Position the cutting tool at the marked point and carefully cut through the braided fuel line. Apply steady pressure to ensure a clean and straight cut. Take your time to avoid any accidental damage to the surrounding area. If using a dedicated cutter, follow the manufacturer's instructions for the best results.
- Inspect the Cut: After cutting the line, inspect the edges to ensure they are smooth and free from any debris. If the cut is not clean, you might need to carefully trim the edges with a file or sandpaper to create a precise splice. This step is crucial to ensure a secure connection during the splicing process.
Accurate measurement and cutting are fundamental to a successful splice. By taking the time to measure carefully and cut precisely, you set the foundation for a robust and reliable fuel line repair or modification.
Vacuum Line Fuel Spill: Unraveling the Mystery
You may want to see also
Prepare Connections: Prepare the ends by deburring and ensuring a smooth surface
When splicing a braided fuel line, proper preparation of the connections is crucial to ensure a secure and reliable join. The first step in this process is to carefully deburr the ends of the fuel line. Deburring involves removing any sharp edges or rough surfaces from the line's ends, which can cause friction and damage during the splicing process. You can use a variety of tools for deburring, such as a file, sandpaper, or a specialized deburring tool. The goal is to create a smooth, rounded surface at the end of the fuel line. This step is essential to prevent the line from catching or snagging on other components, ensuring a clean and precise splice.
After deburring, inspect the ends of the fuel line closely. Look for any remaining sharp edges or imperfections that might affect the splice's integrity. If you notice any, use the appropriate tool to carefully remove them. For instance, if there are small burrs, you can use fine-grit sandpaper to smooth them out. Ensuring a completely smooth surface is vital to allow the splice to glide effortlessly without any resistance.
The next step is to consider the type of connection you will make. Common methods include using a ferrule, a crimp, or a clamp. Each method requires specific preparation techniques. For example, if you're using a ferrule, you'll need to ensure the ferrule is clean and free of any debris. If a crimp connection is chosen, the crimping tool should be set to the correct size and position for the desired splice. Taking the time to prepare the connections in this manner will significantly contribute to the overall success of the splice.
Additionally, consider the environment in which the fuel line will be used. If it's in a high-temperature or corrosive environment, you might need to take extra precautions. This could involve using special adhesives or protective coatings to ensure the splice's longevity. Proper preparation at this stage will help prevent future issues and ensure the fuel line's performance meets the required standards.
In summary, preparing the connections by deburring and ensuring a smooth surface is a critical step in splicing a braided fuel line. It requires attention to detail and the right tools to create a clean, precise splice. By following these steps, you can ensure a reliable and long-lasting connection for your fuel line.
Mastering the Art of Return Fuel Line Maintenance
You may want to see also
Secure and Test: Secure the splice with a hose clamp and test for leaks
Once you've prepared the braided fuel line by removing the old section and cleaning the ends, it's crucial to secure the splice effectively. This step ensures the integrity of the connection and prevents any potential fuel leaks. Here's a detailed guide on how to do it:
Start by positioning the new section of the braided fuel line alongside the existing one, ensuring that the splice is aligned properly. The key is to create a smooth and continuous flow of fuel without any kinks or twists. Use a hose clamp to secure the splice tightly. Hose clamps are designed to provide a secure and adjustable grip, allowing you to tighten the connection without damaging the fuel line. Wrap the hose clamp around the splice, making sure it is snug and firmly in place. Take care not to overtighten, as this can cause the fuel line to crimp or distort. A gentle, firm grip is usually sufficient.
After securing the splice with the hose clamp, it's essential to test for any potential leaks. This step is critical to ensure the safety and functionality of your fuel system. Here's how to do it:
- Visual Inspection: Begin by visually inspecting the splice area. Look for any signs of fuel seepage or moisture around the connection. Even a small leak can be a serious issue, so pay close attention to any unusual moisture or fuel residue.
- Soapy Water Test: For a more thorough inspection, use a soapy water solution. Apply a small amount of this solution to the splice area and observe if any bubbles appear. Bubbles indicate the presence of air or fuel leaks, as the soap will create a visible reaction. If bubbles form, it's a clear sign that you need to address the splice further.
- Pressure Test: For a more comprehensive test, you can use a fuel pressure gauge. Connect the gauge to the fuel line, ensuring it is secure, and then start the engine. If the gauge shows any fluctuations or drops in pressure, it could indicate a leak in the splice area. This test is especially important if you're working with a high-pressure fuel system.
If the tests reveal any leaks, you may need to re-secure the splice or consider other repair methods. Ensuring a tight and leak-free connection is vital to maintaining the performance and safety of your vehicle's fuel system. Always take the time to properly secure and test any fuel line connections to avoid potential issues.
Mastering the Art of Fuel Line Sealing: A Comprehensive Guide
You may want to see also
Frequently asked questions
Splicing braided fuel lines is a crucial process to ensure the integrity and safety of the fuel system in vehicles. It involves joining two or more sections of braided fuel lines to create a continuous path for fuel flow, allowing for efficient and reliable fuel delivery to the engine.
You should splice a braided fuel line when you encounter a damaged or worn-out section, a necessary extension to accommodate new engine components, or when replacing an entire fuel line. Regular inspection and maintenance can help identify potential issues early on.
The primary tools needed are a fuel line cutter, a fuel line crimper, a fuel line primer, and a suitable solvent. Materials include the replacement fuel line section, a fuel line ferrule, and the primer. Ensure you have the correct sizes and types of tools and materials for your specific fuel line.
Start by cleaning the ends of the fuel lines using the solvent to remove any dirt or contaminants. Cut the fuel line to the desired length, leaving a few extra inches for the splice. Prepare the ferrule by sliding it onto the fuel line, ensuring it covers the cut end securely.
Begin by inserting the prepared fuel line end into the ferrule until it reaches the crimping area. Use the crimper to apply firm pressure and create a secure crimp, ensuring the fuel line is tightly held in place. Repeat this process for the other end, and allow the splice to dry completely before reassembling the fuel system.