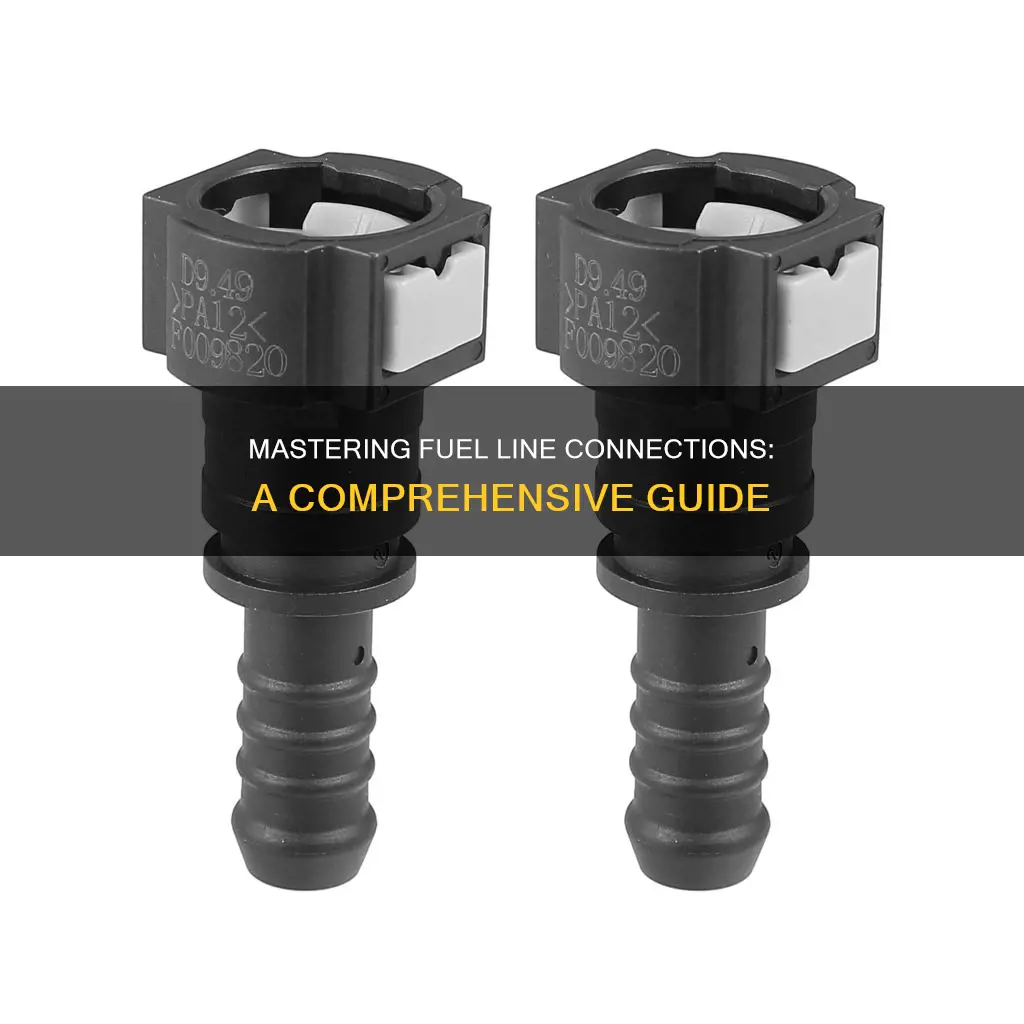
Connecting fuel line fittings requires careful attention to detail and adherence to safety protocols. This process involves ensuring a secure and leak-free connection between the fuel line and the engine's fuel system. It is crucial to use the appropriate tools and materials, such as fuel line connectors, seals, and clamps, to create a tight bond. Proper preparation, including cleaning the surfaces and using the right primer, is essential to ensure a reliable connection. Following manufacturer guidelines and industry best practices will help ensure the fuel line fittings are correctly installed, providing a safe and efficient fuel supply to the engine.
What You'll Learn
- Prepare Tools: Gather necessary tools like wrenches, pliers, and fuel line connectors
- Clean Fittings: Ensure fittings are clean and free of debris for a secure connection
- Align Fittings: Properly align fuel lines and fittings to avoid damage
- Tighten Connections: Securely tighten fittings using appropriate torque settings
- Test for Leaks: Inspect connections for leaks and ensure proper fuel flow
Prepare Tools: Gather necessary tools like wrenches, pliers, and fuel line connectors
Before you begin the process of connecting fuel line fittings, it's crucial to ensure you have the right tools for the job. This preparation step is often overlooked but is essential for a successful and safe fuel line installation. Here's a detailed guide on what you need to gather:
Wrenches and Pliers: These are fundamental tools for any fuel line connection task. You'll typically require a set of adjustable wrenches, which can accommodate various sizes of fittings. The key is to have a range of sizes to fit different fuel line diameters. For example, a 1/4-inch, 3/8-inch, and 1/2-inch adjustable wrench will cover most common fuel line sizes. Additionally, a set of pliers is essential, especially for gripping and turning smaller fittings or connectors. Needle-nose pliers are particularly useful for reaching tight spaces and making precise connections.
Fuel Line Connectors: Depending on your specific application, you might need various types of fuel line connectors. These can include quick-connect fittings, which are commonly used for their ease of installation and removal. They often feature a simple push-to-connect mechanism. You may also encounter fittings with threads, requiring you to have thread seal tape or pipe compound to ensure a tight and leak-free connection. It's important to choose the right connector for your fuel line size and application.
Other Essential Tools: Beyond the basics, there are a few more tools that can make the job easier. A fuel line cutter or a sharp knife can be handy for trimming fuel lines to the correct length. Additionally, having a small wire brush or a cleaning tool can help remove any debris or old fuel line material from the fitting's interior. These tools ensure a clean and precise connection.
By gathering these tools, you'll be well-prepared to tackle the task of connecting fuel line fittings. It's a straightforward process once you have the right equipment, ensuring a secure and reliable fuel supply to your engine. Remember, proper preparation is key to a successful automotive repair or modification project.
Understanding the Lifespan of Fuel Lines in Craftsman Riding Mowers
You may want to see also
Clean Fittings: Ensure fittings are clean and free of debris for a secure connection
When it comes to connecting fuel line fittings, ensuring they are clean and free of debris is an essential step that cannot be overlooked. This process is crucial for a secure and reliable connection, as any dirt or contaminants can lead to leaks, reduced performance, and potential safety hazards. Here's a detailed guide on how to achieve this:
Preparation and Cleaning: Begin by gathering the necessary tools and materials, including the fuel line fittings, a cleaning solvent or brush, and a soft cloth. It is recommended to use a specialized fuel line cleaner or a mild detergent mixed with water. Start by disconnecting the fuel lines from the source and the destination, ensuring you identify the correct fittings and their respective connections. Once disconnected, inspect the fittings for any visible dirt, corrosion, or debris. Use the cleaning solvent or a brush to gently remove any built-up grime, being careful not to damage the fittings. Pay attention to all surfaces, including threads, seals, and O-rings.
Rinsing and Drying: After cleaning, thoroughly rinse the fittings with clean water to remove any remaining cleaning agents. Ensure that no soap residue is left behind, as it can attract dirt. Dry the fittings immediately using a soft cloth to prevent water spots and ensure a dry surface. This step is vital to avoid any moisture-related issues during the connection process.
Debris Removal: Focus on removing any small particles or debris that might have accumulated during the cleaning process. You can use compressed air or a small brush to carefully clear the fittings, ensuring no foreign matter remains. This step is particularly important for hard-to-reach areas and intricate designs of the fittings.
Final Inspection: Before making the connection, perform a final visual inspection to ensure the fittings are entirely clean and free of any contaminants. Check for any signs of damage or wear that might have occurred during the cleaning process. This thorough inspection will help identify any potential issues early on, allowing for prompt resolution.
By following these steps, you can guarantee that the fuel line fittings are clean and ready for a secure connection. This process is a critical aspect of maintaining a fuel system's integrity and performance, ensuring a safe and efficient operation. Remember, proper cleaning is a fundamental practice in automotive maintenance, and it can save you from potential headaches and costly repairs in the long run.
Maximizing Fuel Efficiency: The Role of Return Lines in Pumps
You may want to see also
Align Fittings: Properly align fuel lines and fittings to avoid damage
When connecting fuel line fittings, proper alignment is crucial to ensure a secure and damage-free installation. Misaligned fittings can lead to various issues, including fuel leaks, reduced performance, and even potential engine damage. Here's a step-by-step guide to help you align the fittings correctly:
Start by ensuring you have the right tools and materials, including the fuel lines, fittings, and any necessary connectors or adapters. Check the manufacturer's specifications for the correct sizes and types of fittings required for your specific application. This information will guide you in selecting the appropriate fittings and ensuring compatibility.
Next, carefully inspect the fuel lines and fittings. Look for any signs of damage, such as cracks, tears, or bends in the lines. Also, check for any debris or contaminants that might interfere with the alignment process. Clean the fittings and lines if necessary to ensure a smooth and accurate connection.
Now, begin the alignment process. Position the fittings so that the fuel lines are straight and aligned with the desired flow direction. Ensure that the fittings are not twisted or bent, as this can cause restrictions or damage to the fuel flow. Use a straight edge or a ruler to verify that the lines are aligned properly. Take your time with this step, as precision is key to a successful connection.
Pay close attention to the orientation of the fittings. The male end of the fitting should be aligned with the female port, ensuring a proper mating. Check that the threads or connectors are aligned and not crossed, as this can lead to leaks or damage. If using adapters or connectors, make sure they are securely attached and aligned with the main fittings.
Finally, secure the fittings using the appropriate fasteners or clamps. Tighten them according to the manufacturer's recommendations, being careful not to overtighten, as this can damage the fittings or fuel lines. Double-check your work by testing the connection for leaks and ensuring that the fuel flows smoothly. Proper alignment and secure installation will help prevent fuel leaks, maintain optimal engine performance, and extend the lifespan of your fuel system.
Dirt Bike Fuel Line Attachment: A Comprehensive Guide
You may want to see also
Tighten Connections: Securely tighten fittings using appropriate torque settings
When connecting fuel line fittings, ensuring a secure and tight connection is crucial to prevent fuel leaks and maintain optimal engine performance. The process of tightening these connections requires careful attention to detail and the use of appropriate torque settings. Here's a step-by-step guide to help you achieve a reliable and safe fuel line connection:
Start by gathering the necessary tools, including a torque wrench, which is essential for measuring and applying the correct amount of force during tightening. It is recommended to use a torque wrench with a range suitable for the size of your fittings. Check the manufacturer's specifications or consult a torque chart to determine the appropriate torque value for your specific fitting type. This value is typically measured in pound-force per square inch (psi) or Newton-meters (Nm).
Locate the fitting you want to tighten and ensure it is clean and free of any debris or contaminants. Apply a thin layer of thread sealant or pipe compound to the threads of the fitting and the corresponding pipe or hose. This step is optional but can provide additional security and prevent leaks. Take your time to thread the fitting onto the pipe or hose, ensuring it is aligned properly.
Now, it's time to tighten the fitting using the torque wrench. Place the wrench onto the fitting's threads and apply the specified torque value. Turn the fitting clockwise by hand first to feel the resistance and ensure it is not too tight or too loose. Then, using the torque wrench, tighten it further in a controlled manner. Aim for a consistent and even tightening process to avoid over-tightening, which can damage the fittings or cause fuel leaks.
After tightening, inspect the connection for any signs of leakage. Check for any visible damage or distortion around the fitting and ensure that the threads are not stripped or damaged. If you notice any issues, carefully loosen the fitting and re-tighten it, adjusting the torque as needed. It is better to be cautious and recheck the torque value if you suspect any problems.
Remember, proper torque settings are critical to the longevity and safety of your fuel system. Always refer to the manufacturer's guidelines and torque specifications for your specific fittings. By following these steps, you can ensure that your fuel line connections are secure, leak-free, and ready to provide efficient fuel delivery to your engine.
Unbraided Fuel Line Compatibility: Aero Fittings and Performance
You may want to see also
Test for Leaks: Inspect connections for leaks and ensure proper fuel flow
When working with fuel line fittings, it's crucial to test for leaks to ensure the system's integrity and prevent potential hazards. Here's a step-by-step guide to inspecting connections for leaks and maintaining proper fuel flow:
- Prepare the Tools and Materials: Before beginning the inspection, gather the necessary tools and materials. You'll need a fuel pressure gauge, a soapy water solution, a clean cloth, and a fuel line fitting kit (if needed). Ensure you have the appropriate safety gear, such as gloves and eye protection, to avoid any fuel-related accidents.
- Inspect Connections Visually: Start by visually examining all connections and fittings. Look for any visible signs of damage, cracks, or corrosion. Check for any debris or foreign objects that might have entered the system during installation. Pay close attention to the threads and fittings, ensuring they are tight and secure. If you notice any issues, address them immediately before proceeding.
- Apply Soapy Water Test: This is a common method to detect leaks. Fill the fuel tank with a small amount of fuel, ensuring it's not overfilled. Then, spray a mixture of soapy water onto the connections and fittings. Carefully observe the areas around the fittings for any bubbles or foam. Bubbles indicate the presence of air or fuel escaping, which could be a sign of a leak. If you spot any leaks, tighten the connections or consider replacing the fittings.
- Use a Fuel Pressure Gauge: For a more accurate assessment, utilize a fuel pressure gauge. This tool measures the pressure in the fuel system, helping you identify potential leaks. Start by ensuring the engine is off and the fuel pump is disconnected. Connect the gauge to the fuel line, taking care not to over-tighten. Apply pressure and observe the gauge reading. A significant drop in pressure indicates a possible leak. If leaks are detected, trace the source and address it accordingly.
- Ensure Proper Fuel Flow: After identifying and fixing any leaks, it's essential to verify that fuel is flowing correctly. Check for any blockages or restrictions in the fuel lines. Ensure that the fuel pump is functioning properly and delivering the required pressure. If you suspect an issue with the pump, consider consulting a professional mechanic. Proper fuel flow is vital to prevent engine performance issues and ensure safe operation.
Remember, regular maintenance and testing are key to maintaining a reliable fuel system. By following these steps, you can effectively inspect connections, detect leaks, and ensure optimal fuel flow, ultimately contributing to the overall performance and safety of your vehicle.
Kreem Fuel Tank Liner: A Comprehensive Guide to Installation and Benefits
You may want to see also
Frequently asked questions
To ensure a secure and leak-free connection, you will need a few essential tools. These include a fuel line fitting kit, which typically includes various sizes of fittings, nuts, and washers. Additionally, you'll require a fuel line cutter or a pair of sharp scissors to cut the fuel line to the desired length, a fuel line crimping tool to create a tight seal, and a fuel line clamp or ferrule to secure the fitting.
Proper preparation is crucial to avoid leaks and ensure a long-lasting connection. Start by cleaning the fuel line and removing any dirt, debris, or old fittings. Use a fuel line cleaner or a mild detergent to wash the line, ensuring it is free from contaminants. Then, cut the fuel line to the appropriate length, leaving a few extra inches for the fitting. Smooth out any sharp edges with a file or sandpaper.
The process involves several steps. First, insert the fuel line into the fitting, ensuring it is aligned correctly. Then, using the crimping tool, apply pressure to the fitting's ferrule or clamp, creating a secure grip around the fuel line. Make sure the connection is tight and there are no gaps. Finally, use the appropriate nut and washer to fasten the fitting securely, tightening it with a wrench. Always check for leaks after each step.