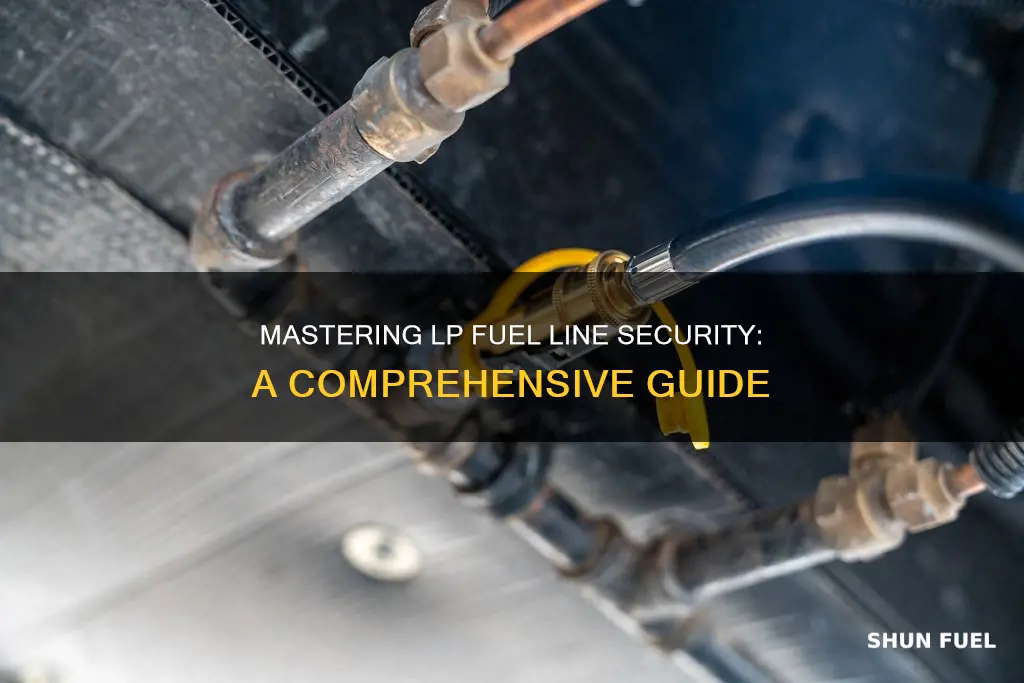
Securing an LP (liquid petroleum) fuel line is a crucial step in ensuring the safety and efficiency of your vehicle's fuel system. Properly securing the fuel line helps prevent leaks, reduces the risk of damage from vibrations, and maintains a tight connection to optimize fuel flow. This guide will provide a step-by-step process to secure an LP fuel line, covering essential techniques and tools to ensure a reliable and safe setup.
What You'll Learn
- Materials: Choose the right materials for the fuel line and fittings to ensure compatibility and durability
- Clamps: Use secure, adjustable clamps to fasten the line to the engine, preventing leaks
- Routing: Route the line away from heat sources and sharp edges to avoid damage
- Filters: Install fuel filters to prevent contaminants from entering the engine
- Testing: Regularly inspect and test the fuel line for leaks and damage
Materials: Choose the right materials for the fuel line and fittings to ensure compatibility and durability
When it comes to securing an LP (liquid petroleum) fuel line, choosing the right materials is crucial for ensuring compatibility, durability, and long-term performance. The fuel line and fittings must be able to withstand the corrosive nature of LP gas, as well as the high temperatures and pressures involved. Here's a detailed guide on selecting the appropriate materials:
- Hose Material: The primary component of your fuel line is the hose, which should be made from a material specifically designed to handle LP gas. Natural rubber or synthetic rubber compounds are commonly used for this purpose. Look for hoses that are reinforced with braided steel or fiber to enhance their strength and flexibility. These reinforced hoses can better withstand the pressure and movement associated with fuel delivery systems. Ensure the hose has a suitable inner diameter to accommodate the fuel flow rate and maintain adequate pressure.
- Fittings and Connections: Fittings play a critical role in maintaining a secure and leak-free connection. Opt for fittings made from materials such as brass, stainless steel, or aluminum alloys. These materials offer excellent corrosion resistance and can handle the harsh conditions of LP gas. Look for fittings with a smooth interior surface to minimize friction and potential fuel degradation. Threaded connections should be tight and secure, using high-quality seals to prevent gas leaks. Consider using fittings with a female thread on the inside and a male thread on the outside to ensure a tight seal.
- Compatibility and Temperature Range: It is essential to choose materials that are compatible with LP gas and can withstand the expected temperature variations. Some materials may degrade or become brittle when exposed to the corrosive effects of LP gas over time. Research and select materials that have a proven track record of compatibility and longevity in LP gas applications. Additionally, ensure that the chosen materials can handle the temperature range of your fuel system, including both the cold start and hot operating temperatures.
- Flexibility and Movement: LP fuel lines need to accommodate movement and vibration, especially in mobile applications. Choose materials that offer a good balance of flexibility and rigidity. This ensures that the fuel line can bend and flex without kinking or damaging the internal components. Consider the routing of the fuel line and select materials that can withstand the physical stresses of that particular installation.
- Industry Standards and Regulations: Adhere to industry standards and regulations when selecting materials. Many regions have specific guidelines for LP gas systems to ensure safety and performance. For example, the American Society of Mechanical Engineers (ASME) provides codes and standards for pressure vessels and piping systems, which can be relevant to LP fuel line installations. Following these standards ensures that your fuel line setup meets the required quality and safety standards.
2003 Xterra Fuel Line Location: A Quick Guide
You may want to see also
Clamps: Use secure, adjustable clamps to fasten the line to the engine, preventing leaks
When securing an LP (liquid petroleum) fuel line to your engine, using the right type of clamp is crucial to ensure a tight and reliable connection. The primary purpose of these clamps is to prevent any potential leaks, which could lead to dangerous situations and costly repairs. Here's a detailed guide on how to use secure, adjustable clamps for this task:
Start by ensuring you have the appropriate clamp for the specific application. LP fuel lines often require specialized clamps designed to withstand the unique challenges of fuel transport, including pressure and temperature variations. These clamps are typically made from durable materials like stainless steel or high-strength plastics. Look for clamps with a smooth, non-marring interior to protect the fuel line's surface.
Proper installation is key to the clamp's effectiveness. Begin by cleaning the engine's mounting surface and the clamp's contact area to ensure a solid bond. Then, position the clamp around the fuel line, ensuring it is centered and aligned with the engine's mounting points. The clamp should be tight enough to eliminate any slack but not so tight that it causes damage to the fuel line or the engine. Adjust the clamp's position if necessary to achieve a secure fit.
Adjustability is a critical feature of these clamps. You should be able to fine-tune the clamp's grip to ensure a snug fit. This adjustability allows for minor variations in fuel line diameter or engine mounting configurations. To adjust, locate the clamp's release mechanism, often a screw or lever, and carefully manipulate it to tighten or loosen the clamp's grip as needed.
Finally, ensure that the clamps are securely fastened to the engine. Use the appropriate fasteners, such as screws or bolts, to attach the clamps in place. Tighten these fasteners by hand first, then use a wrench to ensure a secure hold. Regularly check the clamp's condition and retighten the fasteners as necessary to maintain the integrity of the connection.
By following these steps and using secure, adjustable clamps, you can effectively secure your LP fuel line, minimizing the risk of leaks and ensuring the safe and efficient operation of your engine. Remember, proper installation and regular maintenance are essential to the long-term success of any fuel line system.
Upgrading Your 2001 Silverado's Fuel Pump: A Step-by-Step Guide to Line Replacement
You may want to see also
Routing: Route the line away from heat sources and sharp edges to avoid damage
When securing an LP (liquefied petroleum) fuel line, proper routing is crucial to ensure the safety and longevity of the system. One essential aspect of this process is to route the fuel line away from potential heat sources and sharp edges. Heat sources, such as engines, exhaust systems, or even nearby hot surfaces, can cause the LP fuel to vaporize, leading to potential safety hazards and system inefficiencies. Similarly, sharp edges or protruding objects can physically damage the fuel line, causing leaks or even complete rupture.
To achieve this, it is recommended to follow a few guidelines. Firstly, plan the route of the fuel line carefully, taking into account the layout of the vehicle or equipment it is being installed on. Identify any potential heat sources or sharp edges in the vicinity and plan the path of the line to avoid these areas. For example, if the fuel tank is located near the engine, ensure that the line is routed away from the engine block and any hot exhaust pipes.
When routing the LP fuel line, it is essential to use flexible hoses or tubes that can accommodate bends and turns without kinking or putting excessive strain on the material. These hoses should be made of durable materials that can withstand the temperature and pressure of the LP fuel. Additionally, consider using protective sleeves or covers to shield the fuel line from potential impacts or abrasion, especially in areas where it might come into contact with moving parts or sharp objects.
It is also important to secure the fuel line at regular intervals to prevent it from becoming loose or damaged. Use appropriate fasteners, such as clips, ties, or brackets, to keep the line in place. Ensure that these fasteners are not tight enough to cause damage to the fuel line but firm enough to hold the line securely in its intended position. Regularly inspect the routing and fasteners to identify any signs of wear or damage and make the necessary adjustments or replacements.
By following these routing practices, you can significantly reduce the risk of damage to the LP fuel line, ensuring a safer and more efficient fuel system. Proper routing away from heat sources and sharp edges is a fundamental step in the overall process of securing an LP fuel line, contributing to the overall reliability and safety of the system.
Understanding the Choke Fuel Line: A Car's Essential Component
You may want to see also
Filters: Install fuel filters to prevent contaminants from entering the engine
Securing an LP (liquid petroleum) fuel line is a crucial step in ensuring the safe and efficient operation of your engine. One of the most effective ways to achieve this is by installing fuel filters. These filters act as a barrier, trapping contaminants and impurities that could potentially damage the engine over time. Here's a step-by-step guide on how to properly install fuel filters to protect your engine:
- Choose the Right Filter: Start by selecting a fuel filter that is compatible with your engine and the type of fuel it uses. Different engines may require specific filter sizes and types, so it's essential to consult your vehicle's manual or seek advice from a mechanic. Common types of fuel filters include in-line filters, which are installed along the fuel line, and suction-type filters, which are mounted closer to the engine.
- Locate the Fuel Line: Identify the LP fuel line, which typically runs from the fuel tank to the engine. This line is responsible for delivering fuel to the engine's carburetor or fuel injection system. Locate any existing filters along this line and note their positions. Understanding the layout will make the installation process smoother.
- Remove Contaminated Filters (if applicable): If your vehicle already has filters, it's a good practice to inspect and replace them regularly. Over time, filters can become clogged or damaged, allowing contaminants to pass through. If you encounter a filter that is heavily contaminated or shows signs of wear, replace it immediately to maintain optimal engine performance.
- Install the New Filter: Now, you can proceed with installing the new fuel filter. Start by turning off the engine and allowing it to cool down, as working on a hot engine can be dangerous. Locate the filter mounting position, which is usually near the fuel line. Carefully remove any existing screws or brackets securing the old filter. Clean the mounting surface to ensure a proper seal. Take your new filter and align it with the mounting position, ensuring it fits snugly. Secure the filter using the appropriate screws or brackets.
- Test and Verify: After installing the filter, it's crucial to test the system to ensure proper functionality. Start the engine and check for any leaks or unusual noises. Verify that the fuel flow is smooth and consistent. Regularly replacing fuel filters will help maintain the engine's performance and longevity, especially in LP fuel systems where contaminants can be more prevalent.
By following these steps, you can effectively secure your LP fuel line and protect your engine from potential harm caused by contaminants. Remember, regular maintenance and filter replacements are key to keeping your vehicle running smoothly and reliably.
Fuel Filter Lines: Understanding the Connections and Their Roles
You may want to see also
Testing: Regularly inspect and test the fuel line for leaks and damage
When it comes to securing an LP (liquid petroleum) fuel line, regular testing and inspection are crucial to ensure the safety and efficiency of your system. This process involves a series of checks to identify any potential issues before they become major problems. Here's a step-by-step guide on how to effectively test and inspect your LP fuel line:
Start by visually examining the fuel line for any visible signs of damage or deterioration. Look for cracks, punctures, or any discolouration that might indicate wear and tear. Pay close attention to the connections and fittings, as these areas are more susceptible to damage. Inspect the entire length of the line, including where it passes through walls, floors, or ceilings, as these points may require additional protection. If you notice any damage, it's essential to address it promptly to prevent further issues.
The next step is to perform a leak test. This is a critical aspect of ensuring the safety of your LP fuel system. You can use a soapy water solution or a specialized fuel line leak detector to identify leaks. Start by applying the solution or detector to the fuel line, ensuring it covers all connections and fittings. Then, observe the line for any bubbles or foam, which indicate the presence of a leak. If you find any leaks, it's important to locate the source and repair or replace the affected section of the fuel line.
Additionally, consider using a pressure gauge to test the fuel line's integrity. Connect the gauge to the fuel line and measure the pressure at different points along the line. Compare the readings to the manufacturer's specifications to ensure the line is functioning correctly. Low pressure might indicate a restriction or leak, while high pressure could suggest a potential failure in the system.
Regular testing should be conducted at intervals recommended by the manufacturer or industry standards. For instance, you might perform a visual inspection monthly and a comprehensive leak test and pressure check every six months. This proactive approach will help you identify and rectify issues before they lead to costly repairs or safety hazards.
Remember, proper maintenance and testing are essential to the longevity and safety of your LP fuel system. By following these steps, you can ensure that your fuel line remains secure and reliable, providing efficient operation and peace of mind.
Clear Tubing: A Viable Fuel Line Solution?
You may want to see also
Frequently asked questions
Securing an LP fuel line is crucial for safety and performance. Start by identifying the specific type of fuel line and the appropriate securing method. Typically, a combination of clamps, ties, and brackets is used. Clamps should be tightened securely but not excessively, and they should be positioned at regular intervals along the line. Ties can be used to further secure the line, especially in areas with vibrations. Brackets can be attached to the vehicle's frame or other sturdy structures to provide additional support. Always refer to the manufacturer's guidelines for the specific fuel line and vehicle model.
Selecting the appropriate clamp is essential for a secure and leak-free connection. Consider the diameter and material of your fuel line. Clamps are available in various sizes and materials, such as steel, stainless steel, or aluminum. For LP fuel lines, a common choice is a stainless steel clamp due to its durability and resistance to corrosion. Ensure the clamp has a good grip and is the correct size to fit the fuel line snugly. It's important to follow the manufacturer's recommendations or consult an expert to choose the right clamp for your specific application.
Yes, there are a few pitfalls to be aware of. Firstly, avoid overtightening clamps, as this can damage the fuel line and create leaks. Always use the appropriate tools to tighten them properly. Secondly, ensure the fuel line is not twisted or kinked, as this can restrict flow and cause potential issues. Keep the line straight and secure it at regular intervals. Additionally, never use electrical tape or duct tape as a long-term solution, as they can lose their adhesive properties over time and may not provide a reliable seal.