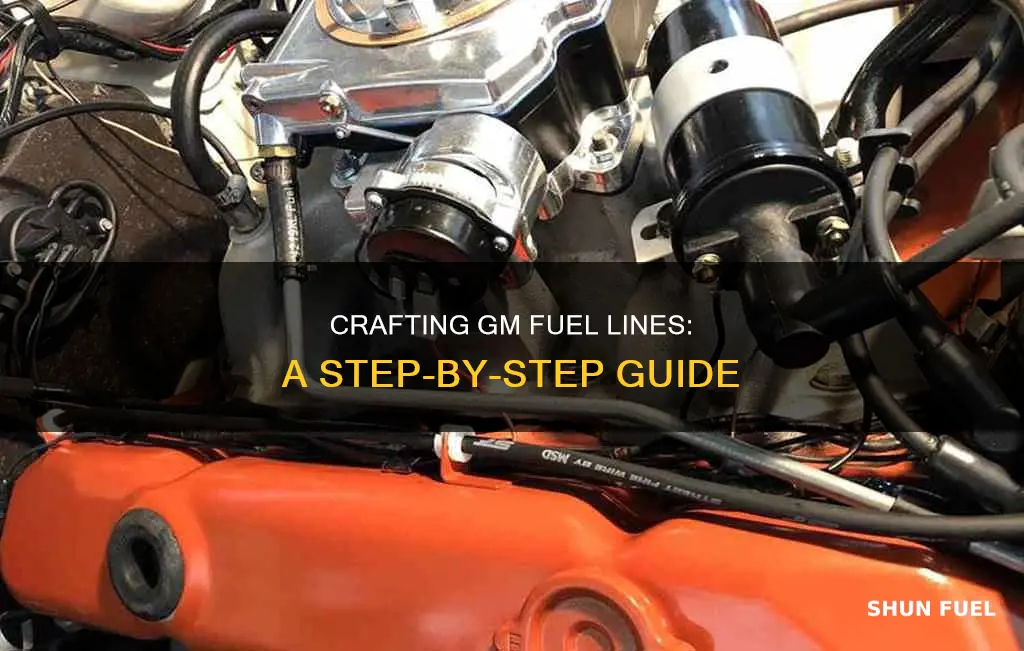
Making your own GM fuel lines can be a rewarding project for car enthusiasts and DIYers. It involves a few key steps: first, you'll need to gather the necessary materials, including fuel line material, fittings, and tools. Next, you'll measure and cut the fuel line to the appropriate length, ensuring it fits your vehicle's specific needs. Then, you'll need to assemble the fittings and securely attach the fuel lines to the engine and fuel tank. This process requires patience and attention to detail to ensure a safe and efficient fuel delivery system. With the right tools and a bit of practice, you can create custom fuel lines that enhance your vehicle's performance and longevity.
What You'll Learn
- Materials and Tools: Gather necessary supplies like GM fuel line, fittings, and crimping tools
- Preparation: Clean and inspect fuel lines for damage before installation
- Fitting Connection: Use crimping tools to secure fittings to fuel lines tightly
- Routing: Route fuel lines away from heat sources and sharp edges
- Testing: Inspect and test fuel lines for leaks after installation
Materials and Tools: Gather necessary supplies like GM fuel line, fittings, and crimping tools
To begin the process of making GM fuel lines, it is crucial to gather the necessary materials and tools. Here's a detailed guide on what you'll need:
Materials:
- GM Fuel Line: The primary material you'll require is the specific type of fuel line designed for General Motors (GM) vehicles. Ensure you obtain the correct diameter and length to match your vehicle's requirements. GM fuel lines are typically made from high-quality rubber or synthetic materials that can withstand the demands of fuel transportation.
- Fittings: You will need various fittings to connect the fuel line to the fuel tank, fuel pump, and other components. Common fittings include quick-connect fittings, barbed fittings, and compression fittings. Make sure to get the appropriate sizes and types for your specific GM vehicle.
- Hose Clamps: These are essential for securing the fuel line and fittings in place. Choose the right size and material (e.g., metal or plastic) based on your application.
- Fuel Line Reinforcement: Depending on the length and route of the fuel line, you might want to add reinforcement materials like steel braiding or protective sleeves to prevent damage.
Tools:
- Crimping Tool: This is a specialized tool used to create secure connections between fuel line fittings and the fuel line itself. Crimping tools come in various designs, such as hand-held or power-driven, so choose one that suits your comfort and the scale of the project.
- Pliers: Regular pliers are useful for gripping and manipulating fittings and fuel line connectors.
- Hose Clamps Tool: If you plan to install hose clamps, you'll need a tool to tighten them securely.
- Measuring Tape or Caliper: Accurate measurement tools are essential to ensure the fuel line is the correct length and diameter.
- Safety Gear: Don't forget to wear safety gloves and goggles to protect yourself during the process.
By gathering these materials and tools, you'll be well-prepared to start the fuel line installation or customization process for your GM vehicle. Remember to follow manufacturer guidelines and safety protocols throughout the project.
Seafoam's Impact: Protecting Fuel Lines from Damage
You may want to see also
Preparation: Clean and inspect fuel lines for damage before installation
Before you begin the process of installing or replacing GM fuel lines, it is crucial to ensure that the preparation phase is thorough to guarantee a successful outcome. The first step in this process is to clean the fuel lines to remove any contaminants that may have accumulated over time. Start by disconnecting the fuel lines from the fuel tank and the engine. Use a fuel line cleaner or a suitable solvent to carefully clean each section of the line, ensuring that you remove any dirt, rust, or debris. This step is essential as it prevents any potential issues caused by contaminants during the installation process.
Once the cleaning process is complete, it's time to inspect the fuel lines for any signs of damage. Visually examine the lines for any cracks, punctures, or leaks. Pay close attention to the connections and bends, as these areas are more susceptible to wear and tear. If you notice any damage, it is critical to replace the affected fuel line section to maintain the integrity of the fuel system. Ensure that you have the necessary replacement parts readily available before proceeding.
When inspecting the fuel lines, also check for any signs of corrosion or deterioration. Over time, fuel lines can develop a layer of corrosion, especially if the fuel contains ethanol or if the lines are not properly maintained. Use a wire brush or a specialized corrosion remover to clean and remove any corrosion from the fuel line surfaces. This step is vital to ensure a proper connection and to prevent any future issues.
After cleaning and inspecting the fuel lines, it is recommended to test the lines for leaks. You can do this by using a soapy water solution and applying it to the connections and bends. If you notice any bubbles forming, it indicates a potential leak. In such cases, tighten the connections or replace the damaged sections to ensure a secure and leak-free installation.
By following these preparation steps, you are ensuring that the fuel lines are in optimal condition before installation. Cleaning and inspecting the lines not only helps in identifying potential issues but also ensures the longevity and reliability of the fuel system in your GM vehicle. This meticulous approach to preparation is a key factor in the success of any automotive project.
Fitech Fuel Injection: Return Line Size Guide
You may want to see also
Fitting Connection: Use crimping tools to secure fittings to fuel lines tightly
When it comes to connecting fuel lines in a General Motors (GM) vehicle, ensuring a secure and leak-free fitting is crucial for optimal performance and safety. One effective method to achieve this is by using crimping tools to tightly secure the fittings to the fuel lines. Here's a step-by-step guide on how to execute this process:
Gather the Materials: Before you begin, ensure you have the necessary components. You'll need the appropriate crimping tool for the specific fitting type you're using, as well as the fuel line fittings themselves. Common types of fittings include quick-connect fittings, pressure fittings, and fuel line adapters. Obtain the correct crimping tool for the fitting's size and thread type.
Prepare the Fuel Line: Start by cleaning the fuel line and the fitting. Remove any dirt, debris, or old fuel residue. Ensure the surface of the fuel line is smooth and free from any contaminants that could interfere with the crimping process. This step is essential for a secure connection.
Position the Fitting: Slide the fitting onto the fuel line, ensuring it is aligned properly. The fitting should have a secure grip on the fuel line, but it might not be tight enough for a long-lasting connection. This is where the crimping tool comes into play.
Crimping Process: Using the crimping tool, apply firm pressure to the fitting, following the manufacturer's instructions. The tool will typically have a specific area or areas where you need to apply pressure. Crimping creates a mechanical lock that holds the fitting securely in place. Be careful not to over-crimp, as it can damage the fuel line. The goal is to achieve a tight, leak-free connection.
Final Inspection: After crimping, inspect the connection thoroughly. Check for any signs of leakage around the fitting. Ensure that the fitting is snugly attached and that there are no gaps or spaces where fuel could leak. If everything looks secure, you've successfully created a reliable fitting for your GM fuel lines.
Remember, crimping is a precise process, and different fittings may require slightly varying techniques. Always refer to the tool's instructions and the specific requirements of your vehicle's fuel line system. Properly secured fittings will contribute to a well-functioning fuel system, ensuring your GM vehicle performs optimally.
Finding the Right Fit: Fuel Line Bolt for Impala 3400 V6
You may want to see also
Routing: Route fuel lines away from heat sources and sharp edges
When it comes to routing fuel lines for a GM vehicle, it's crucial to prioritize safety and performance. One of the most critical aspects of this process is ensuring that the fuel lines are routed away from heat sources and sharp edges to prevent potential damage and ensure optimal fuel delivery. Here's a detailed guide on how to achieve this:
Identify Heat Sources: Begin by thoroughly inspecting your vehicle's engine bay and surrounding areas. Locate all potential heat sources, such as exhaust manifolds, catalytic converters, engine blocks, and any other components that generate significant heat. These areas can cause fuel lines to degrade over time due to the high temperatures they reach. It's essential to keep the fuel lines as far away from these heat sources as possible.
Plan the Route: Carefully plan the path of the fuel lines, ensuring they are positioned away from the identified heat sources. Consider the vehicle's architecture and the available space. Aim to create a route that is as direct as possible while maintaining a safe distance from any potential heat-related hazards. Keep in mind that fuel lines should also be routed away from sharp edges, such as engine mounts, transmission mounts, and other protruding components that could cause damage during vehicle operation or maintenance.
Use Protective Materials: To further protect the fuel lines, consider using protective materials or sleeves. These can be made of heat-resistant materials like rubber or plastic and should be securely attached to the fuel lines. By providing an additional layer of insulation, you create a barrier between the fuel lines and potential heat sources, reducing the risk of damage. Ensure that the protective materials are compatible with the fuel type and vehicle specifications.
Secure the Lines: Properly secure the fuel lines using appropriate clamps or ties. This step is crucial to maintain the desired route and prevent any movement that could lead to damage. Secure the lines at regular intervals, ensuring they are taut and not subjected to excessive tension. Avoid routing the lines through tight spaces or areas where they might come into contact with sharp edges, as this can lead to wear and potential fuel leaks.
Regular Inspection: Implement a regular inspection routine to check the condition of the fuel lines. Over time, even the best-routed lines can experience wear and tear. Inspect for any signs of damage, such as cracks, brittleness, or corrosion. Address any issues promptly to ensure the continued safe operation of your vehicle. Regular maintenance and inspections will help identify potential problems before they become major concerns.
By following these guidelines, you can ensure that your GM fuel lines are properly routed, protected, and maintained, contributing to the overall reliability and performance of your vehicle. Remember, the goal is to create a safe and efficient fuel delivery system by minimizing the risks associated with heat and sharp edges.
Thread Tape: A Safe Bet for Fuel Line Repairs?
You may want to see also
Testing: Inspect and test fuel lines for leaks after installation
After installing the newly fabricated or replaced fuel lines in your General Motors (GM) vehicle, it is crucial to conduct a thorough inspection and testing process to ensure they are leak-free and functioning correctly. This step is essential to prevent potential engine issues and maintain the vehicle's overall performance. Here's a detailed guide on how to inspect and test the fuel lines for leaks:
Initial Inspection: Before starting the testing process, visually inspect the fuel lines for any visible signs of damage or contamination. Look for cracks, punctures, kinks, or any discolored areas along the lines. Ensure that all connections and fittings are secure and properly tightened. Check for any signs of corrosion or rust, especially if the lines have been exposed to harsh environmental conditions. If any issues are found during this initial inspection, address them promptly before proceeding with the tests.
Pressure Testing: This is the most critical step to ensure the integrity of the fuel lines. You will need a fuel pressure gauge and a small amount of compressed air or a pump. Start by disconnecting the fuel lines from the fuel tank and the engine. Apply pressure to the fuel lines using the gauge and observe for any leaks. Hold the pressure for a recommended duration (usually a few minutes) and check for any signs of fuel escaping. Leaks can occur at connections, fittings, or even where the lines are bent or damaged. If a leak is detected, carefully inspect the affected area to identify the source.
Bubble Testing (For Plastic Lines): If your GM vehicle uses plastic fuel lines, you can perform a bubble test to detect leaks. Fill a clear container with water and carefully immerse the fuel lines in it. Look for any bubbles forming on the surface of the water, which could indicate a leak. This method is particularly useful for identifying small leaks that might not be visible during pressure testing.
Starting the Engine: After the initial inspection and pressure testing, start the engine and let it run for a few minutes. Listen carefully for any unusual sounds, such as hissing or roaring, which could indicate a fuel line leak. Check for any fuel odors around the engine bay, as this could also suggest a leak. If the engine runs smoothly without any issues, it is a good sign that the fuel lines are functioning correctly.
Post-Test Inspection: After completing the tests, recheck all connections and fittings to ensure they are tight and secure. Inspect the fuel lines again for any signs of damage or contamination that might have occurred during the testing process. If all tests and inspections pass without any issues, your GM fuel lines are likely ready for use. However, it is always a good practice to monitor the vehicle's performance and fuel consumption over the next few days to ensure there are no unexpected changes.
Fuel Line Removal: A Step-by-Step Guide for Your F-350
You may want to see also
Frequently asked questions
GM fuel lines are typically made from high-quality rubber compounds, such as ethylene propylene rubber (EPR) or natural rubber, which offer excellent flexibility and resistance to fuel chemicals. These materials are chosen for their ability to withstand the harsh conditions of fuel systems, including high temperatures and pressure.
Installation is a critical step to ensure optimal performance and longevity. Start by cleaning the fuel lines and removing any old fuel line material. Use a fuel line cutter to achieve a clean, precise cut. When connecting the new fuel line to the fuel pump and injectors, ensure a tight, secure fit using fuel line connectors or clamps. It's essential to follow the manufacturer's guidelines for torque specifications to avoid over-tightening, which can damage the fuel lines.
Fuel lines can develop issues over time due to aging, corrosion, or physical damage. One common problem is fuel line leaks, which may be caused by cracks, punctures, or improper connections. If you notice any leaks, inspect the fuel lines for visible damage and replace them if necessary. Additionally, ensure that the fuel lines are not pinched or restricted, as this can lead to reduced fuel flow and potential engine performance issues. Regular maintenance and inspection of the fuel system can help prevent these problems.