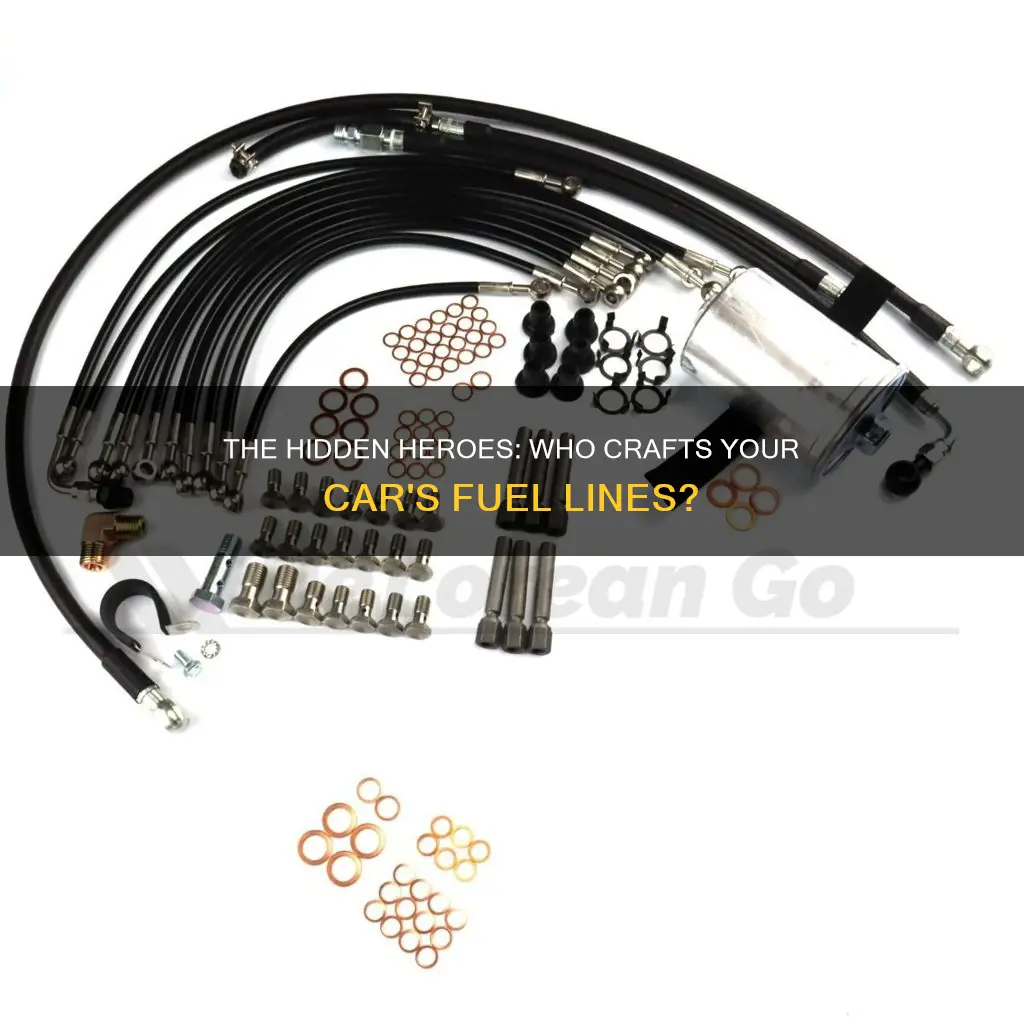
Fuel lines are an essential component of any vehicle's fuel system, and their production involves specialized manufacturing processes. These lines are typically made from materials such as steel, aluminum, or high-density polyethylene (HDPE), chosen for their durability and resistance to fuel degradation. The manufacturing process often includes extrusion, where the material is forced through a die to create the desired shape and thickness. Specialized companies and manufacturers focus on producing high-quality fuel lines, ensuring they meet or exceed industry standards and vehicle specifications. These fuel lines are crucial for delivering fuel from the tank to the engine, and their quality directly impacts the vehicle's performance and reliability.
What You'll Learn
- Fuel Line Manufacturers: Companies like Bosch, Denso, and Valeo produce fuel lines for automotive applications
- Materials and Design: Engineers choose materials like steel, aluminum, or plastic based on durability and performance
- Fuel Line Types: Different types include rubber, braided, and steel fuel lines, each with unique properties
- Fuel Line Standards: Industry standards ensure fuel lines meet safety and performance requirements for various vehicle models
- Fuel Line Testing: Rigorous testing methods include pressure testing, leak testing, and durability testing to ensure quality
Fuel Line Manufacturers: Companies like Bosch, Denso, and Valeo produce fuel lines for automotive applications
The automotive industry relies heavily on fuel lines, which are an essential component of any vehicle's fuel system. These lines are responsible for transporting fuel from the tank to the engine, ensuring a steady and efficient supply of gasoline or diesel. When it comes to manufacturing these critical components, several reputable companies have established themselves as key players in the market.
One of the most well-known fuel line manufacturers is Bosch. With a rich history dating back to the late 19th century, Bosch has become synonymous with quality and innovation in the automotive sector. Their fuel lines are designed with precision and are known for their durability, ensuring a reliable fuel supply to the engine. Bosch's extensive research and development efforts have led to the creation of advanced fuel line systems that meet or exceed industry standards. These systems are engineered to withstand various environmental conditions and provide long-lasting performance.
Denso, another prominent player in the automotive industry, is also a leading fuel line manufacturer. Denso's expertise lies in their ability to combine cutting-edge technology with a deep understanding of vehicle systems. Their fuel lines are designed to offer superior performance and reliability, ensuring optimal fuel delivery to the engine. Denso's commitment to quality has earned them a strong reputation among vehicle manufacturers and aftermarket suppliers.
Valeo, a global automotive supplier, is yet another significant player in the fuel line manufacturing space. With a focus on innovation and sustainability, Valeo offers a comprehensive range of fuel line solutions. Their products are designed to meet the specific requirements of different vehicle models, ensuring a perfect fit and seamless integration. Valeo's fuel lines are known for their high-quality materials and construction, providing excellent resistance to fuel degradation and environmental factors.
These manufacturers play a crucial role in the automotive supply chain, ensuring that vehicles are equipped with reliable and efficient fuel lines. Their expertise and commitment to quality have made them trusted partners for original equipment manufacturers (OEMs) and aftermarket suppliers alike. With their advanced technologies and deep understanding of vehicle systems, these companies continue to drive innovation in fuel line design and manufacturing, contributing to the overall performance and reliability of modern vehicles.
Perfect Fuel Line Fit: 2001 VL800 Guide
You may want to see also
Materials and Design: Engineers choose materials like steel, aluminum, or plastic based on durability and performance
Engineers play a crucial role in selecting the right materials for fuel lines, ensuring optimal performance and safety in various applications. When it comes to choosing materials, engineers consider several factors, primarily focusing on durability and performance. These factors are essential to guarantee the reliability and longevity of fuel lines in different environments and conditions.
One of the most commonly used materials for fuel lines is steel. Engineers prefer steel due to its exceptional strength and durability. It can withstand high pressures and temperatures, making it ideal for fuel lines in vehicles, aircraft, and industrial machinery. Steel's resistance to corrosion and its ability to maintain structural integrity over time make it a preferred choice for critical applications. For instance, high-strength steel alloys are often utilized in racing cars and aircraft, where fuel lines need to handle rapid acceleration and extreme conditions.
Aluminum is another material that engineers consider for fuel lines, especially in applications where weight reduction is essential. Aluminum offers excellent corrosion resistance and a lightweight profile, making it a popular choice for aircraft and high-performance vehicles. Its ability to withstand temperature changes and its low density contribute to improved fuel efficiency and overall vehicle performance. However, aluminum fuel lines may require additional protective measures to ensure long-term durability.
Plastic, particularly polyether ether ketone (PEEK) and polyimide, has gained popularity in fuel line manufacturing. These plastics offer superior chemical resistance, making them suitable for fuel lines in various environments. PEEK, in particular, is known for its high-temperature stability and resistance to fuel degradation, ensuring the longevity of the fuel lines. Plastic fuel lines are often used in racing applications and high-performance vehicles where lightweight and corrosion-resistant materials are advantageous.
The choice of material also depends on the specific operating conditions. Engineers might opt for materials with enhanced flexibility for fuel lines in vehicles with tight spaces or those subjected to frequent vibrations. Additionally, environmental factors, such as exposure to sunlight or extreme temperatures, influence material selection to ensure the fuel lines' performance and safety.
In summary, engineers carefully select materials like steel, aluminum, or plastic for fuel lines based on their unique properties and performance characteristics. The decision-making process involves considering factors such as strength, durability, temperature resistance, and environmental conditions to ensure the fuel lines meet the required standards and provide reliable performance in various applications.
Toyota Tundra '08 Fuel Line Location: A Comprehensive Guide
You may want to see also
Fuel Line Types: Different types include rubber, braided, and steel fuel lines, each with unique properties
Fuel lines are an essential component of any vehicle's fuel system, responsible for transporting fuel from the tank to the engine. The choice of material for these lines is crucial, as it directly impacts performance, durability, and safety. Here's an overview of the different types of fuel lines and their unique characteristics:
Rubber Fuel Lines:
Rubber fuel lines have been a traditional choice for many years due to their flexibility and cost-effectiveness. These lines are typically made from natural or synthetic rubber compounds, which provide excellent resistance to fuel chemicals. Rubber is known for its ability to absorb vibrations, making it less prone to breaking or cracking over time. This type of fuel line is often used in classic car restoration projects and older vehicles where a more classic look is desired. However, rubber lines may not be as durable as other options and can become brittle in extreme temperatures.
Braided Fuel Lines:
Braided fuel lines offer a more modern and robust solution. These lines are constructed by braiding multiple layers of rubber or synthetic material around a steel or copper core. The braiding process provides exceptional flexibility while maintaining structural integrity. Braided lines are highly resistant to fuel leaks and can withstand higher pressure levels, making them ideal for high-performance vehicles. They are also less susceptible to expansion and contraction due to temperature changes, ensuring a longer lifespan.
Steel Fuel Lines:
Steel fuel lines are the strongest and most rigid type available. These lines are made from high-quality steel, offering superior durability and resistance to corrosion. Steel lines are often used in high-performance racing cars and heavy-duty applications where extreme conditions are expected. While they provide excellent protection against leaks, they can be less flexible and more prone to kinking or bending. Proper installation and regular inspection are crucial to ensure the safety and longevity of steel fuel lines.
Each type of fuel line has its own advantages and is chosen based on the specific requirements of the vehicle and its intended use. Rubber lines offer a classic look and flexibility, braided lines provide modern performance and durability, while steel lines are the ultimate choice for heavy-duty applications. When selecting fuel lines, it's essential to consider factors such as temperature range, fuel type, and the overall performance needs of the vehicle to ensure optimal functionality and safety.
Permatex on Fuel Lines: A Carburetor Repair Hack or a No-Go?
You may want to see also
Fuel Line Standards: Industry standards ensure fuel lines meet safety and performance requirements for various vehicle models
The automotive industry has established rigorous standards for fuel lines to ensure the safety and reliability of fuel systems in various vehicle models. These standards are crucial as they directly impact the performance and safety of vehicles, especially in preventing fuel leaks and potential hazards. Industry standards dictate the materials, construction, and performance criteria that fuel lines must adhere to, ensuring they can withstand the rigors of the automotive environment.
One of the primary focuses of these standards is the material composition of fuel lines. Industry guidelines specify the use of high-quality materials such as reinforced rubber or synthetic compounds that offer excellent resistance to fuel degradation and environmental factors. These materials are chosen for their ability to maintain flexibility over a wide temperature range, ensuring the fuel lines remain pliable and functional in extreme conditions. Additionally, the standards may require the use of specific types of reinforcements, such as braided or spiral-wound designs, to enhance the structural integrity of the fuel lines and prevent damage from fuel pressure and vibration.
Construction techniques are another critical aspect of fuel line standards. Manufacturers must adhere to precise methods to ensure the fuel lines are free from defects and can withstand the internal fuel pressure. This includes specifications for crimping, splicing, and bonding techniques to ensure a secure and leak-free connection. Industry standards also dictate the use of appropriate fittings and connectors that meet specific torque and sealing requirements, further enhancing the overall safety and performance of the fuel system.
Performance requirements are also an essential part of fuel line standards. These standards define the pressure ratings, burst strength, and flexibility of the fuel lines to ensure they can handle the demands of the vehicle's fuel system. For instance, fuel lines must be able to withstand the pressure generated by the fuel pump and the expansion and contraction caused by temperature changes. Industry-approved testing methods are employed to verify that fuel lines meet these performance criteria, ensuring they can effectively transport fuel while maintaining a secure connection.
Furthermore, industry standards take into account the compatibility of fuel lines with different vehicle models and fuel types. Manufacturers must ensure that their fuel lines are designed to work seamlessly with the specific fuel requirements of various vehicles, including those with different fuel pump configurations and fuel tank designs. This compatibility ensures that the fuel lines can efficiently deliver fuel to the engine without compromising performance or safety.
In summary, industry standards play a vital role in ensuring that fuel lines meet the necessary safety and performance criteria for various vehicle models. By adhering to these standards, manufacturers can provide reliable and durable fuel systems, reducing the risk of fuel-related issues and enhancing overall vehicle safety. These standards are regularly updated to reflect advancements in technology and materials, ensuring that fuel lines continue to meet the evolving demands of the automotive industry.
2008 Cobalt Fuel Line: Size and Compatibility Guide
You may want to see also
Fuel Line Testing: Rigorous testing methods include pressure testing, leak testing, and durability testing to ensure quality
Fuel lines are an essential component of any vehicle's fuel system, responsible for transporting fuel from the tank to the engine. The quality and reliability of these lines are critical to ensure optimal engine performance and prevent potential hazards. To guarantee the highest standards, manufacturers employ rigorous testing methods that simulate real-world conditions.
One of the primary testing procedures is pressure testing. This process involves subjecting the fuel lines to elevated pressure to assess their ability to withstand potential stress. By applying pressure, engineers can identify any weaknesses or defects in the lines, such as cracks or leaks, which could compromise their integrity. Pressure testing is crucial, especially for high-performance vehicles or those operating in extreme environments, as it ensures the lines can handle the demands of the engine.
Leak testing is another critical aspect of fuel line quality assurance. This method involves systematically checking for any leaks along the length of the fuel lines. It is typically done using specialized equipment that can detect even the smallest amount of fuel escaping. By identifying and locating leaks, manufacturers can address potential issues and ensure that the fuel lines are free from defects. This testing is vital to prevent fuel loss, which could lead to engine misfires, reduced performance, or even dangerous situations if the fuel comes into contact with a hot surface.
Durability testing is also an integral part of the fuel line manufacturing process. This test evaluates the lines' resistance to wear and tear over an extended period. It involves exposing the fuel lines to various environmental conditions, such as extreme temperatures, UV radiation, and vibration, to mimic the rigors of everyday use. By doing so, manufacturers can assess the lines' long-term performance and ensure they can withstand the challenges of different driving conditions. Durability testing helps identify potential failure points and allows for the necessary improvements to enhance the overall reliability of the fuel lines.
In summary, fuel line testing is a comprehensive process that ensures the highest quality and safety standards. Through pressure testing, leak detection, and durability assessments, manufacturers can identify and rectify any issues, ensuring that the fuel lines meet or exceed industry requirements. These rigorous testing methods are essential to provide vehicle owners with reliable and safe fuel systems, contributing to overall engine performance and peace of mind.
Expertise in Fuel Line Repair: Who Can Fix Your 1998 F150?
You may want to see also
Frequently asked questions
Fuel lines are typically produced by automotive suppliers and manufacturers, often as part of an engine system assembly. These companies design and engineer the lines to ensure compatibility and performance with specific vehicle models.
While some DIY enthusiasts might attempt to replace fuel lines, it is generally recommended to have this task performed by qualified mechanics. Fuel lines require precise installation to avoid leaks and ensure safety, so professional expertise is advisable.
Fuel lines are often made from materials like steel, stainless steel, or rubber compounds. The choice of material depends on factors such as temperature resistance, flexibility, and compatibility with the fuel type. For example, rubber lines are common in gasoline applications, while steel lines are used in diesel systems.
Regular maintenance and inspection of fuel lines are essential. It is recommended to check for any signs of damage, corrosion, or leaks during routine vehicle inspections. The frequency of replacement depends on the vehicle's age, usage, and maintenance history, but generally, fuel lines should be replaced every 10-15 years or as advised by the manufacturer.
Yes, several reputable brands and manufacturers supply high-quality fuel lines. These include well-known automotive suppliers like Bosch, Denso, and Delphi, as well as specialized fuel system manufacturers such as Fuel Injection Technology (FIT) and Fuel Systems International (FSI). These companies often provide lines that meet or exceed original equipment specifications.