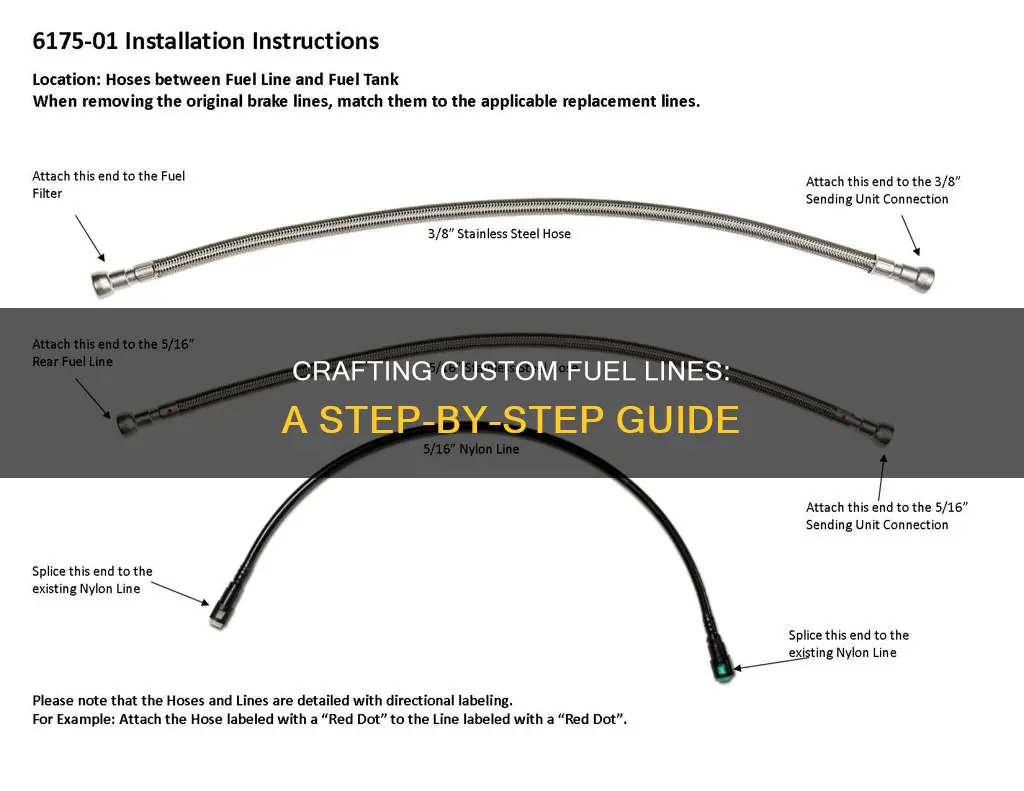
Creating a custom fuel line is a specialized task that requires careful planning and execution. It involves selecting the appropriate materials, ensuring compatibility with the vehicle's engine, and adhering to safety standards. This process begins with understanding the vehicle's fuel system, including the type of fuel it uses and the specific requirements for the fuel line's diameter, length, and material. The next step is to choose the right materials, such as fuel-resistant hoses and fittings, and to ensure they meet the necessary specifications. Proper installation is crucial, involving precise routing and secure connections to prevent leaks and ensure optimal performance. This guide will provide a detailed overview of the process, offering step-by-step instructions and tips to ensure a successful custom fuel line installation.
What You'll Learn
- Materials and Tools: Gather necessary supplies like fuel line material, connectors, and tools
- Cutting and Measuring: Accurately measure and cut the fuel line to desired length
- Assembly: Connect fuel line to engine and other components using appropriate techniques
- Testing: Inspect fuel line for leaks and ensure proper functionality
- Maintenance: Regularly check and replace fuel line as needed to prevent issues
Materials and Tools: Gather necessary supplies like fuel line material, connectors, and tools
To create a custom fuel line, you'll need to gather specific materials and tools to ensure a successful and safe installation. Here's a detailed guide on what you should collect:
Materials:
- Fuel Line Material: The primary material for your custom fuel line is a durable and flexible fuel-resistant hose or tube. You can choose from various options like rubber, PVC, or braided steel, depending on your specific requirements and the environment in which the fuel line will be used. Ensure the material is compatible with the type of fuel you'll be transporting.
- Connectors: You'll require appropriate connectors to join the fuel line segments and ensure a secure and leak-proof connection. Common connectors include quick-release couplings, barbed fittings, or compression fittings, each with its own advantages. Consider the ease of installation and the compatibility of the connectors with your chosen fuel line material.
- Clamps and Straps: These are essential for securing the fuel line in place and preventing any movement or damage. Get a set of adjustable clamps and straps that can accommodate the fuel line's diameter and provide a tight grip.
- Fuel: If you plan to test the fuel line, ensure you have access to the specific type of fuel it will carry. This is crucial for verifying the line's compatibility and performance.
Tools:
- Hose Clamps: Invest in a set of adjustable hose clamps to secure the fuel line to various surfaces or objects. These clamps will provide a tight and customizable hold.
- Pipe Cutter or Scissors: A sharp and precise tool like a pipe cutter or heavy-duty scissors is necessary for cutting the fuel line material to the desired length.
- Crimping Tool: If you're using crimp connectors, a crimping tool is essential for creating a secure and reliable connection.
- Pliers: Pliers will be handy for gripping and manipulating connectors, especially when working with small components.
- Tape Measure: Accurate measurements are critical, so a tape measure will help you determine the length of the fuel line needed.
- Penetrating Oil: Consider using a penetrating oil to ease the installation process, especially when working with connectors that might be stubborn.
- Safety Gear: Don't forget to prioritize safety by wearing protective gloves and goggles to shield your hands and eyes from any potential hazards.
By gathering these materials and tools, you'll be well-prepared to tackle the task of creating a custom fuel line tailored to your specific needs. Remember, having the right supplies and equipment is fundamental to a successful and safe project.
2010 Accord's Return Fuel Line: What You Need to Know
You may want to see also
Cutting and Measuring: Accurately measure and cut the fuel line to desired length
To create a custom fuel line, accurate measurement and cutting are crucial steps. Begin by carefully examining the existing fuel line setup in your vehicle to understand the layout and dimensions. Identify the length required for your custom fuel line, considering the distance between the fuel tank and the engine or the desired location of the fuel pump. It's essential to measure twice to ensure precision.
Using a flexible measuring tape or a ruler, measure the distance from the fuel tank to the intended connection point. Take note of any bends or angles in the path the fuel line will take, as these will impact the overall length needed. Mark the measurement on the fuel line with a permanent marker or a piece of tape to indicate the starting point for cutting.
For the cutting process, ensure you have a sharp utility knife or a fuel line cutter. Carefully cut along the marked line, maintaining a straight and clean cut. It's important to be precise to avoid any damage to the fuel line or nearby components. If you're using a fuel line cutter, follow the manufacturer's instructions to ensure a proper cut.
After cutting, inspect the fuel line for any defects or imperfections. Ensure that the cut ends are smooth and free from any burrs that could cause damage during installation. Consider using a file or sandpaper to refine the edges if necessary. Proper preparation of the cut ends will ensure a secure and leak-free connection.
Remember, accurate measurement and cutting are fundamental to the success of your custom fuel line project. Take your time, double-check your measurements, and use the appropriate tools to achieve a professional finish. This attention to detail will contribute to a reliable and efficient fuel system in your vehicle.
Mastering the Art of Nylon Fuel Line Maintenance
You may want to see also
Assembly: Connect fuel line to engine and other components using appropriate techniques
When connecting a custom fuel line to your engine, it's crucial to follow a meticulous process to ensure a secure and leak-free assembly. Here's a step-by-step guide to help you through this critical phase:
- Preparation: Before you begin, ensure you have all the necessary tools and materials, including the custom fuel line, fittings, clamps, and any specific tools required for your engine model. Clean the engine bay and the areas where the fuel line will be connected to remove any dirt or debris. This step is essential to prevent contamination and ensure a proper seal.
- Fuel Line Inspection: Carefully inspect the custom fuel line for any damage or defects. Look for kinks, tears, or any signs of deterioration. Ensure that the fuel line is the correct size and length for your engine's requirements. If any issues are found, address them immediately by replacing the affected section or the entire line if necessary.
- Fitting Installation: Start by attaching the fittings to the fuel line. Use the appropriate tools to tighten the fittings securely. Ensure that the fittings are aligned correctly and that there is no movement or play in the connections. Tighten the fittings in a clockwise direction, but be careful not to over-tighten, as this can damage the fuel line.
- Engine Connections: Locate the engine's fuel injection system or carburetor, depending on your engine type. Carefully route the fuel line through the engine compartment, following the manufacturer's recommended path. Use appropriate clamps or brackets to secure the fuel line to the engine and other components, such as the firewall or engine mounts. Ensure that the line is not pinched or subjected to excessive stress.
- Hose Clamps and Support: Install hose clamps at regular intervals along the fuel line to provide additional support and prevent sagging. Tighten the hose clamps firmly but avoid over-tightening, as this can restrict fuel flow. Ensure that the clamps are positioned to avoid any interference with moving parts.
- Final Checks: Once the fuel line is connected, perform a thorough inspection to ensure everything is secure. Check for any leaks by applying a small amount of diesel fuel or a suitable sealant to the connections and observing for any seepage. If any leaks are detected, tighten the fittings or clamps and recheck. Ensure that all connections are tight and secure.
Remember, proper assembly is critical to the performance and safety of your vehicle. Take your time, follow the manufacturer's guidelines, and seek professional assistance if needed. A well-connected fuel line will ensure efficient fuel delivery and contribute to the overall reliability of your engine.
Stock Steel Fuel Line Pressure Limits: A Comprehensive Guide
You may want to see also
Testing: Inspect fuel line for leaks and ensure proper functionality
When it comes to testing your custom fuel line, ensuring it is leak-free and functional is crucial for the safety and performance of your vehicle. Here's a step-by-step guide to inspecting the fuel line:
Preparation: Before you begin, ensure you have the necessary tools, including a fuel line inspection kit or a simple set of tools like a wrench and a funnel. It is also advisable to have a helper or a second person to assist with the testing process.
Step 1: Visual Inspection: Start by visually examining the fuel line for any visible signs of damage, cracks, or deterioration. Look for any areas where the line might be pinched, kinked, or damaged during the installation process. Pay close attention to connections, fittings, and bends, as these areas are more susceptible to leaks. Check for any signs of corrosion or oxidation, especially if the fuel line is made of metal.
Step 2: Pressure Test: A pressure test is an essential part of the inspection process. You can use a fuel line pressure tester or a simple pump and gauge system. Start by attaching the tester to the fuel line, ensuring a secure connection. Gradually increase the pressure and observe for any leaks. A small amount of pressure should be sufficient to detect leaks, but you can adjust the pressure as needed. If a leak is detected, identify the source and consider replacing the affected section of the fuel line.
Step 3: Bubble Test: This test is particularly useful for detecting leaks in flexible fuel lines. Fill the fuel line with a small amount of soapy water or a specialized fuel line testing solution. Then, gently shake the vehicle or simulate driving conditions. If there are any leaks, you will see bubbles forming around the leak site due to the air-water mixture. This method is simple yet effective in identifying potential issues.
Step 4: Functionality Check: After ensuring the fuel line is leak-free, it's time to test its functionality. Start the vehicle's engine and monitor for any unusual noises or vibrations. Check for proper fuel flow and ensure that the engine runs smoothly without any stalling or hesitation. Test the fuel pump's operation by listening for its characteristic humming sound and checking the fuel pressure.
Step 5: Documentation: Document your findings and any issues discovered during the testing process. Take notes on the locations of potential problem areas and the results of each test. This documentation will be valuable for future reference and can help you identify patterns or recurring issues.
Remember, thorough testing is essential to guarantee the safety and reliability of your custom fuel line installation. By following these steps, you can ensure that your fuel line is leak-free and functions as intended, providing a seamless and efficient fuel supply to your vehicle's engine.
Flushing Fuel Overflow: A Step-by-Step Guide for 2003 Dakota Owners
You may want to see also
Maintenance: Regularly check and replace fuel line as needed to prevent issues
Regular maintenance of your fuel lines is crucial to ensure optimal performance and prevent potential issues that could lead to costly repairs. Here's a guide on how to approach this task:
Visual Inspection: Begin by regularly inspecting your fuel lines. Look for any signs of damage, such as cracks, leaks, or corrosion. Check for any visible wear and tear, especially at the points where the lines connect to the fuel tank and engine. Pay attention to the hoses and fittings, as these are common areas for deterioration. Over time, fuel lines can become brittle, leading to potential failures.
Pressure Testing: Conduct pressure tests to assess the integrity of the fuel lines. This can be done using a fuel pressure gauge. Connect the gauge to the fuel line and measure the pressure. Compare the reading to the manufacturer's specifications. If the pressure is significantly lower or higher than the recommended range, it may indicate a problem with the fuel line or its connections.
Replacement: Fuel lines should be replaced periodically, especially if they show signs of damage or wear. Here's a step-by-step process:
- Locate the fuel lines and identify their connections.
- Disconnect the lines carefully, ensuring you have the necessary tools and knowledge to avoid any damage to the fuel system.
- Inspect the old fuel lines for any issues. If they are beyond repair or replacement, dispose of them properly.
- Clean the fuel tank and lines to remove any debris or old fuel.
- Install the new fuel lines, ensuring they are securely attached and properly routed. Use the appropriate tools and torque specifications to avoid over-tightening.
- Re-test the fuel system to ensure proper pressure and functionality.
Preventive Measures: To prevent issues, consider the following:
- Use high-quality fuel lines that are compatible with your vehicle's fuel type.
- Regularly check for and address any fuel leaks, as they can lead to engine misfires and reduced performance.
- Keep your fuel tank and lines clean to prevent contamination, which can cause engine issues.
- Follow the manufacturer's recommended maintenance schedule for fuel system inspections and replacements.
By implementing these maintenance practices, you can ensure that your fuel lines remain in optimal condition, providing efficient fuel delivery to your engine and reducing the risk of unexpected breakdowns. Regular checks and timely replacements will contribute to the overall reliability and longevity of your vehicle's fuel system.
Mastering the Art of Fuel Line Connection: A Guide to Auto Gas Tank
You may want to see also
Frequently asked questions
For a custom fuel line, you can use materials like stainless steel, brass, or aluminum. These metals are durable and can withstand high temperatures and pressure, making them ideal for fuel transport.
To achieve a precise fit, measure the required length and diameter of the fuel line carefully. Consider the bends and angles needed to route the line around obstacles. You can use fittings and adapters to connect the line to the fuel source and the engine. Ensure a tight seal using appropriate sealing materials.
Absolutely! Custom fuel lines can be made to any specific length and diameter as per your requirements. You can choose from various sizes and materials to ensure the line fits perfectly in your vehicle's fuel system.
When installing, ensure there are no sharp bends or kinks in the line, as these can restrict fuel flow. Avoid routing the line near heat sources or sharp edges to prevent damage. Properly secure the line to prevent vibration-induced damage, and always use the correct fittings and seals to maintain a safe and efficient fuel system.