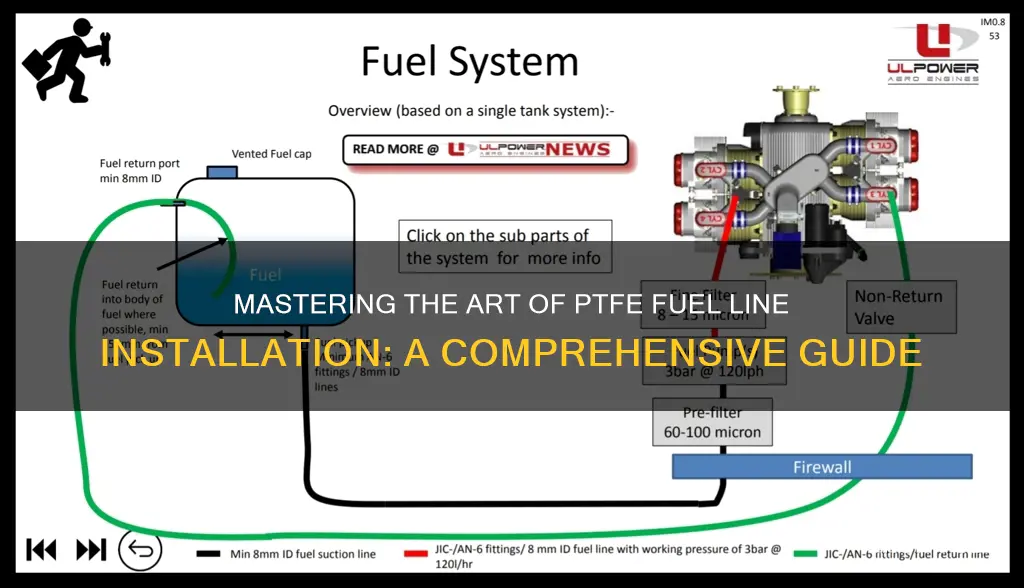
Installing a polytetrafluoroethylene (PTFE) fuel line is a great way to ensure a reliable and efficient fuel supply for your vehicle. This type of fuel line is known for its durability and resistance to heat and chemicals, making it an excellent choice for high-performance engines. The process involves carefully cutting and fitting the PTFE line to your vehicle's fuel system, ensuring a tight seal to prevent any leaks. This guide will provide a step-by-step approach to help you successfully install a PTFE fuel line, ensuring your vehicle's performance and longevity.
What You'll Learn
- Preparation: Gather tools and materials, ensure workspace is clean and organized
- Fuel Line Inspection: Check for damage, ensure proper length and compatibility
- Clamping: Secure fuel line with appropriate clamps, follow manufacturer's instructions
- Routing: Route fuel line away from heat sources and sharp edges
- Testing: Verify fuel flow, pressure, and leaks after installation
Preparation: Gather tools and materials, ensure workspace is clean and organized
Before you begin the installation process, it's crucial to prepare your workspace and gather the necessary tools and materials. Start by ensuring that your work area is clean, well-lit, and free from any potential hazards. A cluttered workspace can lead to mistakes and accidents, so take the time to organize your tools and materials. Lay out all the components you'll need, including the PTFE fuel line, connectors, and any specialized tools required for the installation. Having everything within reach will make the process more efficient and less time-consuming.
Gather the appropriate tools such as a hose cutter, crimping tool, and a utility knife. These tools are essential for cutting the fuel line to the correct length, creating a secure connection, and making any necessary adjustments. Additionally, ensure you have a supply of replacement gaskets or seals, as these are often required for a proper installation. It's a good idea to have a few extra connectors on hand in case any are damaged during the process.
Check your workspace for any potential hazards. Ensure that the area is clear of tripping hazards, sharp objects, or any items that could interfere with the installation. Consider wearing protective gear, such as gloves and safety goggles, to safeguard yourself from any potential spills or debris. A well-prepared workspace will not only make the installation process smoother but also ensure your safety throughout the project.
Once you have everything ready, double-check the compatibility of the PTFE fuel line with your vehicle's system. Refer to the manufacturer's guidelines or consult a professional if you're unsure about any specific requirements. This step is crucial to ensure a successful and safe installation. With a well-prepared workspace and the right tools, you'll be ready to proceed with the installation process, confident that you have everything you need to complete the task efficiently.
Unraveling the Mystery: Husqvarna Tractor Fuel Line Sizes Demystified
You may want to see also
Fuel Line Inspection: Check for damage, ensure proper length and compatibility
Fuel lines are an essential component of your vehicle's fuel system, and proper inspection and maintenance are crucial to ensure optimal performance and safety. When it comes to installing a PTFE (Polytetrafluoroethylene) fuel line, a thorough inspection is a must to guarantee a successful and reliable setup. Here's a step-by-step guide to inspecting and ensuring the compatibility and integrity of your fuel line:
Damage Inspection: Begin by visually examining the fuel line for any signs of damage. Look for cracks, punctures, or any visible tears along the length of the line. PTFE fuel lines are known for their durability, but they can still be susceptible to wear and tear over time. Check for any signs of deterioration, especially in areas where the line connects to the fuel tank, pump, or engine. Inspect the fittings and connectors as well; ensure they are intact and securely attached to prevent any potential leaks.
Length and Routing: Verify that the fuel line is the correct length for your vehicle's specific model. Measure the existing line (if any) or refer to the vehicle's manual to determine the required length. Proper length is crucial to ensure the line reaches the fuel pump and engine without excessive tension or strain. Additionally, check the routing of the line. It should follow the recommended path, avoiding sharp bends or kinks that could restrict fuel flow or cause damage over time.
Compatibility Check: Ensure that the PTFE fuel line is compatible with your vehicle's fuel type and system. Different vehicles may require specific fuel line materials to withstand the pressure and temperature variations of the fuel they carry. Check the manufacturer's specifications and guidelines for your car's fuel system. Incompatible fuel lines can lead to performance issues and potential safety hazards.
Pressure Testing (Optional): For added assurance, consider performing a pressure test on the fuel system. This step is especially important if you're replacing an existing line. Connect a pressure gauge to the fuel line and pump the fuel system to a specified pressure. Observe for any leaks or abnormalities. This test will help identify any potential issues with the fuel line's integrity and sealing capabilities.
By following these inspection steps, you can ensure that your PTFE fuel line installation is not only correct but also safe and efficient. Regular maintenance and inspections are key to maintaining a reliable fuel system in your vehicle.
Mastering the Art of Fuel Line Flare: A Comprehensive Guide
You may want to see also
Clamping: Secure fuel line with appropriate clamps, follow manufacturer's instructions
When installing a PTFE (Polytetrafluoroethylene) fuel line, clamping is a crucial step to ensure a secure and reliable connection. The process involves using specialized clamps designed to fit the specific fuel line and provide a tight, leak-free seal. Here's a detailed guide on how to properly clamp the fuel line:
Choose the Right Clamps: Begin by selecting the appropriate clamps for your PTFE fuel line. Different manufacturers may offer various types of clamps, such as compression or quick-release clamps. It is essential to use the clamps recommended by the manufacturer to ensure compatibility and optimal performance. Check the fuel line's specifications and the clamp's manufacturer guidelines to identify the correct size and type.
Prepare the Fuel Line: Before clamping, ensure the fuel line is clean and free of any debris or contaminants. Use a soft cloth or a brush to wipe down the surface, removing any dirt or old adhesive residue. This step is crucial for a proper clamp-to-fuel-line bond.
Follow the Manufacturer's Instructions: Clamping techniques may vary depending on the manufacturer's recommendations. Typically, you will need to position the clamp around the fuel line, ensuring it covers the entire length of the connection. Tighten the clamp securely, but be careful not to overtighten, as this can damage the fuel line. Refer to the manufacturer's diagram or instructions provided with the fuel line to ensure you are clamping it correctly.
Secure the Clamp: Once the clamp is in place, double-check that it is secure and firmly attached. You should feel a slight resistance when tightening the clamp further. Ensure that the clamp is snug against the fuel line, creating a tight seal. Avoid using excessive force, as this can lead to fuel line damage.
Test for Leaks: After clamping, it is essential to test the connection for any leaks. Turn on the fuel supply and inspect the clamp area for any signs of fuel escaping. If a leak is detected, carefully adjust the clamp and retest until a secure, leak-free connection is achieved.
Remember, proper clamping is vital to maintain the integrity of the fuel line installation. Always refer to the manufacturer's guidelines and instructions specific to your PTFE fuel line to ensure a successful and safe installation.
Mastering the Art of Hard Fuel Line Cutting: A Comprehensive Guide
You may want to see also
Routing: Route fuel line away from heat sources and sharp edges
When installing a PTFE (polytetrafluoroethylene) fuel line, proper routing is crucial to ensure the system's longevity and performance. One essential aspect of this process is to route the fuel line away from potential heat sources and sharp edges to prevent damage and potential leaks. Here's a detailed guide on how to achieve this:
Identify Heat Sources and Hazards: Begin by thoroughly inspecting your vehicle's engine bay and surrounding areas. Identify any heat sources, such as exhaust manifolds, catalytic converters, or engine components that generate significant heat. Also, look for sharp edges, like engine mounts, body panels, or other metal structures that could pose a risk during installation. Understanding these potential hazards is the first step in effective routing.
Plan the Route: Design a path for the fuel line that avoids these identified risks. The goal is to create a route that is as straight and direct as possible while maintaining a safe distance from heat sources and sharp objects. Consider the natural flow of the engine bay and the layout of other components. Aim for a route that is easy to follow and access during maintenance or repairs.
Use Protective Materials: To further protect the fuel line, consider using protective sleeves or insulation made from heat-resistant materials. These sleeves can be wrapped around the fuel line where it comes into contact with potential heat sources. Ensure that the insulation is secure and does not restrict the line's flexibility or movement. This additional layer of protection adds an extra margin of safety.
Secure the Line: As you route the fuel line, ensure it is securely fastened using appropriate clamps or ties. Avoid tight bends or kinks that could compromise the line's integrity. Keep the line taut and away from any sharp edges or protruding components. Proper securing prevents damage and ensures a clean, professional installation.
Test and Inspect: After completing the installation, start the engine and listen for any unusual noises. Check for any signs of fuel leakage around the connections and joints. Inspect the fuel line for any visible damage or wear. This testing phase is crucial to ensure the system's reliability and identify any potential issues early on.
Replacing Fuel Lines: A Step-by-Step Guide for Your 2007 Cadillac CTS
You may want to see also
Testing: Verify fuel flow, pressure, and leaks after installation
After installing the PTFE fuel line, it's crucial to conduct a thorough testing procedure to ensure the system's functionality and reliability. Here's a step-by-step guide on how to verify fuel flow, pressure, and leaks:
Fuel Flow Testing: Start by checking the fuel flow rate to ensure it meets the required specifications. You can use a fuel flow meter or a calibrated orifice to measure the volume of fuel passing through the line per unit of time. Compare the measured flow rate with the expected value based on the engine's requirements. If the flow rate is inconsistent or below the specified limit, it may indicate a restriction or blockage in the fuel line, requiring further investigation and potential adjustments.
Pressure Testing: Verify the fuel pressure to ensure it is within the optimal range for your engine. Use a fuel pressure gauge to measure the pressure at the fuel rail or injection pump. The pressure should be consistent and stable, typically within a specified range recommended by the manufacturer. Low pressure might suggest a clogged filter or a faulty pump, while excessive pressure could indicate a potential safety hazard. Adjustments to the fuel pump or pressure regulator may be necessary if the pressure is out of the desired range.
Leak Detection: Inspect the entire fuel system for any leaks. Start by checking all connections, fittings, and joints for any signs of fuel seepage. Use a soapy water solution or a specialized fuel leak detector to identify potential leak points. Ensure that all components are securely tightened and sealed. Leaks can lead to fuel wastage, reduced engine performance, and potential safety risks. Address any leaks promptly by tightening connections or replacing damaged parts.
Additionally, consider running the engine and monitoring its performance during this testing phase. Listen for any unusual noises and observe the engine's behavior. Proper fuel flow, pressure, and leak-free installation should result in smooth operation and optimal engine performance. If any issues are identified, carefully troubleshoot and resolve them before finalizing the installation.
Fuel Line Functionality: Unlocking the Secrets of Your Engine's Lifeblood
You may want to see also
Frequently asked questions
PTFE fuel lines are an excellent choice for fuel systems due to their exceptional chemical resistance, flexibility, and low-friction properties. They are commonly used in high-performance engines and racing applications where traditional rubber or plastic fuel lines may not withstand the demands of extreme conditions.
Before installation, ensure you have the necessary tools such as fuel line cutters, crimping tools, and soapy water for cleaning. Prepare the fuel lines by cutting them to the desired length and ensuring a clean, smooth surface at the ends. It's crucial to follow the manufacturer's guidelines for the specific fuel line type you are using.
While it is possible to install PTFE fuel lines without prior experience, it is recommended to have some knowledge of fuel system basics. Familiarize yourself with the specific fuel line type, its installation process, and any unique requirements. If you are unsure, consulting a professional mechanic or referring to detailed online tutorials can provide valuable guidance.
One common issue is ensuring a secure and leak-free connection. Use the appropriate crimping tool and follow the manufacturer's instructions for a tight, reliable bond. Additionally, be mindful of sharp bends or kinks in the fuel lines, as these can cause damage. Regularly inspect the installed lines for any signs of wear or damage, especially in areas with high vibration or temperature fluctuations.